1018 steel and 4140 alloy steel are both common steel alloys, but they have differences in their composition and properties that make one better suited for certain applications over the other. However, 4140 steel loses toughness with increased hardness levels. For applications requiring a low-cost material, 1018 steel is sufficient. But where high strength is paramount, 4140 alloy steel – despite its increased cost – is a superior choice and is commonly used in drivetrain components, shafts, gears, and other stressed parts.
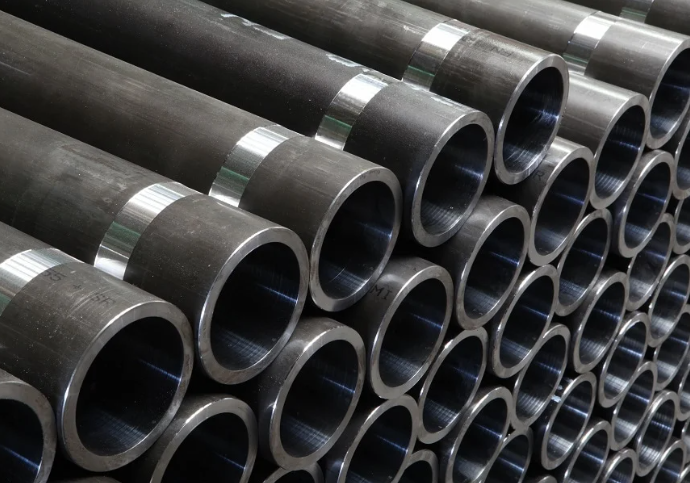
About 1018 Steel
1018 steel is a low-carbon steel that is among the industry’s most commonly used carbon steel. It is well known for its good balance of strength, ductility, and ease of machining, making it a popular choice for a variety of applications.
Uses of 1018 Steel
1018 steel is highly versatile and finds application across various industries due to its favorable properties such as good machinability, formability, and strength.
1. Automotive Industry
– Shafts and Rods: Used in the manufacture of non-critical parts like tie rods in the steering system.
– Mounting Brackets: Often used for mounting systems under the hood or in the chassis of vehicles.
2. Manufacturing Equipment
– Tool Handles: Due to its good machinability and strength, 1018 steel is used in the manufacture of handles for various tools.
– Jigs and Fixtures: The steel’s good formability and strength make it ideal for creating jigs and fixtures in manufacturing settings.
3. Construction
– Structural Frames: For light frames where high strength is not critical.
– Base Plates: Used in the construction of machinery bases and other structural components that require welding.
4. Consumer Goods
– Furniture Parts: Particularly in metal frameworks for office furniture or shelving units.
– Home Appliances: Small internal components that require mild steel for formability and are not subjected to high stress.
5. Metal Fabrication
– Chains and Gears: Used in applications where the material is not subjected to extreme stresses.
– Bolts, Nuts, and Screws: Especially those that do not require high tensile strength but benefit from the ease of machining.
Properties of 1018 Steel
1. Chemical Composition
Element | Percentage |
Carbon (C) | 0.15 – 0.20% |
Manganese (Mn) | 0.60 – 1.00% |
Phosphorus (P) | ≤ 0.040% |
Sulfur (S) | ≤ 0.050% |
Silicon (Si) | ≤ 0.040% |
Iron (Fe) | Balance |
2. Physical Properties
Property | Value | Units |
Density | 7.85 | g/cm³ |
Melting Point | Approx. 2750 | °F (1510 °C) |
Electrical Resistivity | 0.000013 | ohm-cm |
Thermal Conductivity | 48.5 | BTU-in/hr-ft²-°F |
Specific Heat | 0.11 | BTU/lb-°F |
Thermal Expansion | 6.5 × 10⁻⁶ | in/in-°F |
3. Mechanical Properties
Property | Value | Units |
Yield Strength | 36,000 (250) | psi (MPa) |
Tensile Strength | 58,000 – 80,000 (400 – 550) | psi (MPa) |
Elongation at Break | 20 – 40 | % |
Reduction of Area | 40 – 60 | % |
Hardness | 180 – 230 | Brinell |
Fatigue Strength | 30,000 (200) | psi (MPa) |
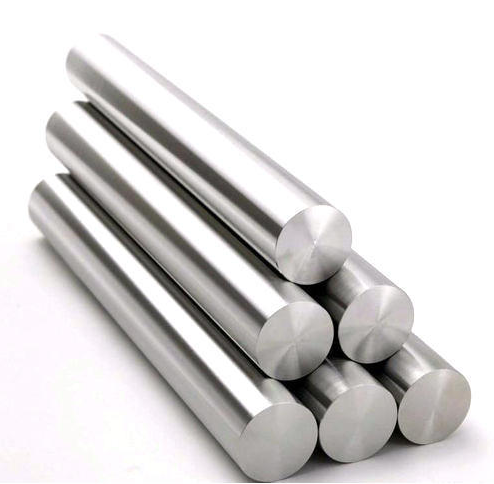
About 4140 Steel
4140 alloy steel is a specific type of alloy steel that contains chromium, molybdenum, and small amounts of other alloying elements. 4140 alloy steel is a versatile chromium-molybdenum alloy steel that is stronger than plain carbon steel while maintaining good toughness through proper heat treatment.
Uses of 4140 Alloy Steel
4140 alloy steel excels in the drivetrain, industrial, off-highway, agricultural, and power generation applications needing a balance of strength, hardness, and toughness.
1. Automotive drive shafts
Many car manufacturers use 4140 alloy steel for drive shafts in vehicles like Ford, GM, Toyota, Honda, etc. due to its strength and durability.
2. Industrial gears
Industrial gear manufacturers like Rexnord, Baldor, and Renold use 4140 steel for high-strength gears that see heavy loads in machinery.
3. Off-highway equipment
Equipment brands like Caterpillar, John Deere, and Komatsu rely on 4140 steel for components like sprockets, links, and idler arms that endure rough use.
4. Motorcycles
Harley Davidson and Ducati use 4140 steel alloy for heavily loaded parts like connecting rods, crankshafts, and gears.
5. Farm equipment
Case IH, New Holland, and John Deere use 4140 in drive line components, linkages, and lifting structures.
6. Construction equipment
Volvo, Hitachi, Komatsu, and others use 4140 alloys in undercarriage and heavy structural parts.
7. Power generation
Siemens, Cummins, and GE employ 4140 steel for parts in gas turbines, generators, and other rotating equipment.
8. Fitness equipment
Precor, Life Fitness, and other brands use 4140 alloy steel for durable weight stacks, bearings, and other load-bearing parts.
Properties of 4140 Alloy Steel
1. Chemical Composition
Element | Percentage |
Carbon (C) | 0.38 – 0.43% |
Manganese (Mn) | 0.75 – 1.00% |
Phosphorus (P) | ≤ 0.040% |
Sulfur (S) | ≤ 0.040% |
Silicon (Si) | 0.15 – 0.30% |
Chromium (Cr) | 0.80 – 1.10% |
Molybdenum (Mo) | 0.15 – 0.25% |
Iron (Fe) | Balance |
2. Physical Properties
Property | Value | Units |
Density | 7.85 | g/cm³ |
Melting Point | Approx. 2700 | °F (1480 °C) |
Electrical Resistivity | 0.000013 | ohm-cm |
Thermal Conductivity | 52 | BTU-in/hr-ft²-°F |
Specific Heat | 0.11 | BTU/lb-°F |
Thermal Expansion | 6.5 × 10⁻⁶ | in/in-°F |
3. Mechanical Properties
Property | Value | Units |
Yield Strength | 125,000 (860) | psi (MPa) |
Tensile Strength | 170,000 (1170) | psi (MPa) |
Elongation at Break | 14 | % |
Reduction of Area | 40 | % |
Hardness | 85 | Rockwell B |
Fatigue Strength | 90,000 (620) | psi (MPa) |
Typical Heat Treatment Processes Used for 4140 Alloy Steel
Proper heat treatment is important for 4140 to develop the required mechanical properties for applications like gears and shafts that demand high strength and wear resistance while maintaining adequate toughness.
- – Annealing: Heating to 1550-1650°F, soaking for 1-2 hours per inch of thickness, then cooling in furnace or air. This relieves internal stresses and softens the steel.
- – Normalizing: Heating to 1500-1600°F, soaking 1 hour per inch of thickness, then air cooling. This refines the grain structure and relieves stresses from machining.
- – Hardening: Heating to 1550-1650°F, soaking 30 minutes per inch thick, then quenching in oil. Rapid cooling hardens and strengthens the steel.
- – Tempering: Reheating hardened steel to low temperatures (300-600°F) then air cooling. This relieves stresses from hardening and improves toughness. Common temperatures are 325°F, 400°F, 450°F depending on desired properties.
- – Quenching and partitioning: Heating to 2050°F, then water quenching and reheating to 375-425°F for oil quenching. Improves strength and toughness. – Martempering: Heating to 1550-1650°F, oil quenching to 450-600°F, then air cooling. Provides strength/toughness intermediate between hardened and tempered states.