Junying Metal Polishing Services – Polishing Surface Treatment for Die Casting Products
Based on decades of experience in mold making and metal die casting service, we know that aluminum polishing service is important to aluminum casting because the die casting products are often rough after the manufacturing and require surface treatment to get smoother edges, preciser measurements and better surface quality. Metal polishing services at diecasting-mould.com are our major finishing services to improve the exterior of your aluminum die castings and other alloys die cast parts. Polishing surface treatment can remove parting lines and overflows from the die casting process, and heat checking or die washout on old casting surfaces, as well as enhance the safe treatment and increase the aesthetics of die casting components. The accomplished team at Junying die casting plant will follow the safety guideline and industry practices to deliver high-quality polished castings. We can transform your design into a fully finished product all in-house.
Why Choose Our Metal Polishing Services
- Start-to-finish fabrication and finishing company
- Reduced production costs, high efficiency and exceptional consistency
- Strict quality control and inspection throughout each stage
- Prompt communication to discuss all your metal polishing needs
- Visible project timeline and on-time delivery
Details of Our Metal Polishing Services
Material | ADC12, aluminum alloys, metals, etc. |
First Layer Processing | Polishing |
Second Layer Processing | Spray painting |
Third Layer Processing | Adding a protective layer |
Equipment | hand polishing tools, buffing wheels, deburring machine, etc. |
Applications | electronics, lock parts, furniture, communications, medical, etc. |
What is Polishing?
Polishing is a finishing process through which to smooth the surface of an object using an abrasive or a work wheel, generally used for enhancing the appearance, prevent contamination, remove oxidization, and increase the reflectivity. Technically, polishing is different from buffing as polishing uses the abrasive glued to the work wheel while buffing uses the loose abrasive applied to the work wheel. Usually, the polishing process utilizes a pad containing the fine-micron or sub-micron abrasive particle in combination with a liquid to generate a reflective surface. The goal of polishing is not to remove large amounts of materials, instead, just very little materials will be removed to create a smoother surface. The condition of the metal before polishing determines what kind of abrasive is required to achieve the desired surface. Polished aluminum die casting parts and metal casting supplies can add a protective layer like wax, oil, or lacquer to prevent further oxidization and extend the service life.
Advantages of Polishing Surface Treatment
- Get rid of the surface scratches, nicks, lines, marks, etc.
- Achieve a high level of shininess and cleanliness
- Acts a protective sealant to the metal surface to increase its durability
- Prevent or reduce wear and corrosion of the metal castings
- Easy to clean and less maintenance
- Provides better uniformity of surfaces
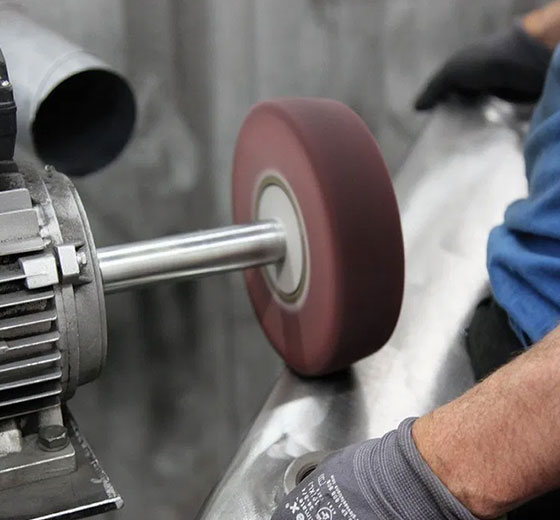