Understanding the strengths and limitations of each alloy will help you select the right material for your specific needs. 1100, 5052, and 3003 stand out for their unique properties and applications. If you don’t know the difference between 1100 aluminum, 5052, and 3003, here is the guide for you. We’ll compare Aluminum 1100, 5052, and 3003 to help you determine which alloy best meets your project needs.
Each of these alloys is non-heat-treatable, lightweight, and corrosion-resistant, but they differ significantly in terms of strength, formability, and specific use cases. Whether you’re designing chemical equipment, marine components, or automotive parts, choosing the right alloy can make all the difference in performance and cost.
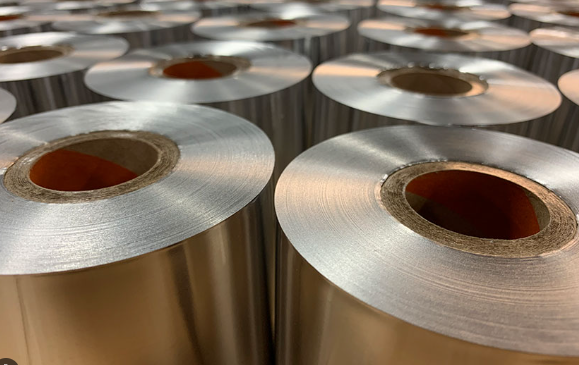
What’s Aluminum 1100?
Aluminum 1100 is a commercially pure aluminum alloy with excellent formability, corrosion resistance, and thermal conductivity. It is widely used in various industries due to its unique properties.
What Are 1100 Aluminum Properties?
Aluminum 1100 is a commercially pure aluminum alloy with excellent corrosion resistance, high thermal and electrical conductivity, and superior formability. It has a minimum aluminum content of 99.0% and exhibits good ductility, with elongation up to 30% in the annealed state. The alloy is not heat-treatable but can be strengthened by cold working. Its mechanical properties vary depending on the temper condition; for example, in the H14 temper, it has a tensile strength of 110-145 MPa and a yield strength of 95 MPa. Due to its unique combination of properties, Aluminum 1100 is widely used in applications such as chemical storage tanks, heat exchangers, food packaging, and architectural panels.
What’s Aluminum 5052?
Aluminum 5052 is a widely used aluminum alloy that belongs to the 5xxx series, known for its high magnesium content. It offers an excellent combination of strength, corrosion resistance, and formability, making it ideal for a variety of applications, especially in harsh environments like marine and chemical industries.
What Are 5052 Aluminum Properties?
5052 aluminum is a high-strength, non-heat-treatable alloy known for its excellent corrosion resistance, particularly in marine and chemical environments. It has good weldability, outstanding formability, and strong fatigue resistance, making it ideal for applications that require durability and flexibility. With a tensile strength range of 31,000-44,000 psi and a yield strength of 28,000 psi, it is stronger than 3003 aluminum but still lightweight and ductile. Its exceptional resistance to saltwater and harsh chemicals, combined with its ability to be easily shaped and welded, makes it a popular choice for marine vessels, fuel tanks, pressure vessels, and industrial equipment.
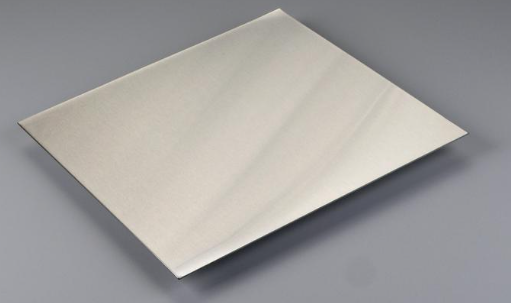
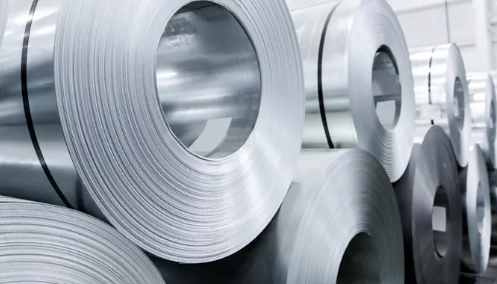
What’s Aluminum 3003?
Aluminum 3003 is a widely used medium-strength aluminum alloy, primarily composed of aluminum with manganese as the main alloying element. It is known for its excellent corrosion resistance, good formability, and workability
What Are 3003 Aluminum Properties?
3003 aluminum is a non-heat-treatable alloy known for its excellent corrosion resistance, especially in environments exposed to moisture and chemicals. It has moderate strength, with a tensile strength of around 21,000 psi and a yield strength of 10,000 psi, making it more durable than pure aluminum (1100) while remaining lightweight and highly formable. This alloy is easy to weld, exhibits good machinability, and offers excellent workability for bending, rolling, and stamping. Its versatility and resistance to corrosion make it ideal for roofing, siding, storage tanks, cooking utensils, and chemical equipment.
Aluminum 1100 vs 5052, What’s the Difference?
Property | 1100 Aluminum | 5052 Aluminum |
Purity | 99% pure aluminum | Magnesium alloy with chromium |
Strength | Lower, softer | Higher, stronger |
Corrosion Resistance | Excellent | Superior, especially in saltwater |
Formability | Outstanding | Good (less than 1100) |
Weldability | Excellent | Excellent (better post-weld strength) |
Applications | Electrical, chemical, and decorative uses | Marine, automotive, and industrial uses |
1. Chemical Composition
1100 aluminum is composed of 99% pure aluminum, making it one of the purest aluminum alloys available. Its high purity gives it excellent corrosion resistance and exceptional thermal and electrical conductivity. It contains small amounts of iron and silicon as impurities. On the other hand, 5052 aluminum is an alloy with magnesium (2.2%-2.8%) as the primary alloying element and trace amounts of chromium (0.15%-0.35%). This composition gives 5052 aluminum its superior corrosion resistance, particularly in saltwater environments, and enhances its strength compared to 1100 aluminum.
2. Strength
1100 aluminum is a soft and low-strength alloy, making it ideal for applications where ductility is more important than strength. Its low tensile strength limits its use in structural applications. In contrast, 5052 aluminum is much stronger, with higher tensile and fatigue strength. This makes it suitable for components that will endure stress or heavy loads, such as marine, automotive, or industrial parts.
3. Corrosion Resistance
Both alloys offer excellent corrosion resistance, but 5052 aluminum outperforms 1100 aluminum in harsh environments. 1100 aluminum resists corrosion effectively in most general environments, making it ideal for chemical and food-related applications. However, 5052 aluminum’s magnesium content enhances its resistance to saltwater and marine environments, making it the better choice for applications exposed to moisture or corrosive conditions.
4. Formability
1100 aluminum is highly ductile and boasts outstanding formability. It is ideal for processes such as deep drawing and spinning, where the metal is shaped into complex geometries without cracking. Although 5052 aluminum also offers good formability, its higher strength makes it slightly less malleable than 1100 aluminum. It can still be formed into various shapes but requires more effort during fabrication.
5. Weldability
Both 1100 and 5052 aluminum are known for their excellent weldability, making them suitable for applications requiring welded joints. However, 5052 aluminum has an edge in post-weld strength. While welding slightly reduces the strength of both alloys, 5052 aluminum retains better structural integrity after welding, making it preferred for critical applications like pressure vessels.
6. Applications
The differences in composition and mechanical properties translate into distinct applications for the two alloys. 1100 aluminum is best suited for applications requiring corrosion resistance, ductility, and lightweight properties, such as chemical equipment, electrical components, and decorative products. Meanwhile, 5052 aluminum is favored for applications that demand higher strength and corrosion resistance, such as marine equipment, automotive components, and industrial storage tanks. Its durability makes it reliable in challenging environments where 1100 aluminum may not perform as well.
1100 Aluminum vs 3003, What’s the Difference?
Property | 1100 Aluminum | 3003 Aluminum |
Purity | 99% pure aluminum | Aluminum with 1.0%-1.5% manganese |
Strength | Low | ~20% stronger than 1100 aluminum |
Corrosion Resistance | Excellent | Slightly better in harsher environments |
Formability | Outstanding | Excellent, but slightly less ductile |
Weldability | Excellent | Excellent, with better post-weld strength |
Applications | Chemical, electrical, and decorative uses | Roofing, automotive, and HVAC systems |
1. Chemical Composition
1100 aluminum is composed of 99% pure aluminum, making it one of the purest aluminum alloys. Its high aluminum content gives it excellent corrosion resistance and thermal/electrical conductivity, but it is relatively soft and low in strength. In contrast, 3003 aluminum is an alloy that includes 1.0%-1.5% manganese as its primary alloying element. The addition of manganese significantly increases its strength compared to 1100 aluminum while maintaining good corrosion resistance.
2. Strength
1100 aluminum is a soft, low-strength material with excellent ductility, making it ideal for applications where formability is more important than strength. Its lower tensile strength limits its usage in structural applications. On the other hand, 3003 aluminum is about 20% stronger than 1100 aluminum thanks to the presence of manganese. This added strength makes 3003 a better choice for applications requiring increased durability and load-bearing capacity.
3. Corrosion Resistance
Both 1100 and 3003 aluminum alloys have excellent corrosion resistance, especially in environments with minimal exposure to corrosive chemicals. However, in slightly harsher environments, such as industrial or marine applications, 3003 aluminum offers slightly better corrosion resistance due to its manganese content. That said, 1100 aluminum’s purity makes it highly resistant to chemical corrosion, making it suitable for chemical processing applications.
4. Formability
1100 aluminum excels in formability due to its high ductility. It is easy to bend, shape, and fabricate into complex designs, making it ideal for processes like deep drawing and spinning. While 3003 aluminum is also highly formable, its higher strength gives it slightly less ductility than 1100 aluminum. Nonetheless, 3003 can still be formed into various shapes with ease, making it versatile for a wide range of applications.
5. Weldability
Both 1100 and 3003 aluminum have excellent weldability and are commonly used in projects requiring welded joints. However, 3003 aluminum retains slightly better strength in the welded areas compared to 1100 aluminum. This makes 3003 more suitable for structural applications involving welding.
6. Applications
The differences in their properties make these two alloys suitable for different applications:
- 1100 Aluminum: Best for applications requiring corrosion resistance, lightweight properties, and excellent formability. Common uses include:
- Chemical equipment (e.g., tanks and piping)
- Electrical components (e.g., bus bars and conductors)
- Food and beverage packaging (e.g., bottle caps and foil)
- Decorative and architectural elements
- 3003 Aluminum: Preferred for applications requiring greater strength while still maintaining good corrosion resistance and workability. Common uses include:
- Roofing and siding materials
- Automotive parts (e.g., fuel tanks and radiators)
- Cooking utensils and food storage equipment
- HVAC systems (e.g., fins and ducts)
3003 Aluminum vs 5052, What’s the Difference?
Property | 3003 Aluminum | 5052 Aluminum |
Purity | Higher purity (~97% aluminum with manganese and copper as alloying elements) | Slightly lower purity (~96% aluminum with magnesium as the primary alloying element) |
Strength | Lower strength (20,000-30,000 psi tensile strength) | Higher strength (33,000-38,000 psi tensile strength) |
Corrosion Resistance | Excellent corrosion resistance, but slightly reduced in saltwater due to copper content | Superior corrosion resistance, especially in marine and industrial environments |
Formability | Highly malleable and easy to form, ideal for deep drawing and bending | Good formability, though slightly less malleable than 3003 due to higher strength |
Weldability | Excellent weldability, suitable for non-structural applications | Excellent weldability with stronger welds, suitable for structural applications |
Applications | Roofing, siding, gutters, HVAC ductwork, cooking utensils, and lightweight storage tanks | Marine applications, fuel tanks, pressure vessels, aircraft parts, and electronics enclosures |
1. Chemical Composition
3003 aluminum is primarily an aluminum-manganese alloy with 1.0%-1.5% manganese and a small amount of copper (~0.12%), which enhances its corrosion resistance but slightly reduces saltwater performance. In contrast, 5052 aluminum is an aluminum-magnesium alloy with 2.2%-2.8% magnesium and no significant copper content, giving it superior corrosion resistance, especially in marine environments.
2. Strength
3003 aluminum has a lower tensile strength (~20,000-30,000 psi), making it suitable for light-duty applications where high strength is unnecessary. On the other hand, 5052 aluminum offers significantly higher strength (~33,000-38,000 psi), making it ideal for structural and high-stress applications.
3. Corrosion Resistance
Both alloys exhibit excellent corrosion resistance, but 5052 is superior due to its magnesium content and lack of copper, making it highly resistant to saltwater and industrial environments. 3003, while still resistant to corrosion, is slightly less effective in harsh conditions because of its copper content.
4. Formability
3003 aluminum is highly malleable and easy to shape, making it ideal for deep drawing, spinning, and bending applications. While 5052 aluminum is also formable, its higher strength makes it slightly harder to shape compared to 3003, though it remains suitable for most forming processes.
5. Weldability
Both alloys have excellent weldability, but 5052 produces stronger welds, making it better for structural and critical applications. 3003, while easy to weld, is more suitable for less demanding projects where weld strength is not a key concern.
6. Applications
3003 aluminum is commonly used in roofing, siding, gutters, cooking utensils, and HVAC ductwork due to its ease of forming and corrosion resistance. Meanwhile, 5052 aluminum is favored for marine applications, fuel tanks, pressure vessels, and industrial equipment, where higher strength and superior corrosion resistance are required.
When comparing aluminum 5052 vs 3003, the choice ultimately depends on the specific needs of your application. 3003 aluminum, with its higher purity and excellent corrosion resistance, is ideal for applications requiring high formability, such as roofing, siding, HVAC ductwork, and lightweight storage tanks. It is best suited for non-structural uses where strength is not a critical factor.
3003 vs 5052 Bending
Ease of Bending:3003 is easier to bend because it is a softer, lower-strength alloy.
Strength After Bending:5052 retains more strength after bending, making it a better choice for applications that need more durability and resistance to wear.
Applications: 3003 is commonly used for applications where flexibility and formability are needed, such as decorative parts or lightweight panels. 5052, on the other hand, is often used in more heavy-duty applications like marine, automotive, and military uses where both strength and corrosion resistance are needed.
Aluminum 1100 vs 5052 vs 3003, Which Should You Choose?
Choose 1100 Aluminum if you need:
- Maximum corrosion resistance for chemical or food-related applications.
- High ductility for deep drawing or spinning processes.
- Lightweight, low-strength components.
Choose 5052 Aluminum if you need:
- Higher strength and durability.
- Superior corrosion resistance, especially in marine or industrial environments.
- Components exposed to stress or harsh conditions.
Choose 3003 Aluminum if you need:
- Greater strength for load-bearing or structural components.
- Slightly better corrosion resistance in industrial or outdoor environments.
- Versatility for roofing, automotive, or HVAC applications.