When working with aluminum, understanding the differences between various tempers is crucial for selecting the right material for your project. 1100 aluminum, renowned for its high purity, excellent corrosion resistance, and exceptional workability, is available in several tempers, with H14 and H18 being two of the most common. In this article, we’ll explore the key differences between aluminum 1100-H14 and 1100-H18, including their mechanical properties, applications, and when to choose one over the other.
What’s 1100 Aluminum Composition?
Aluminum 1100 is a commercially pure aluminum alloy with a minimum aluminum content of 99.0%. Its chemical composition includes the following elements and their respective limits:
Silicon (Si) + Iron (Fe): Combined maximum of 1.0%
Copper (Cu): 0.05% – 0.20%
Manganese (Mn): 0.0% – 0.50%
Zinc (Zn): 0.0% – 0.10%
Other elements (each): 0.0% – 0.05%
Other elements (total): 0.0% – 0.15%
These elements are present in very small quantities, and the remainder is aluminum. The alloy is known for its excellent corrosion resistance, high ductility, and good formability, making it suitable for a wide range of applications.
What Is 1100 Aluminum Used For?
-Construction and Building
Roofing and Siding: Aluminum 1100 is used for roofing sheets and siding due to its corrosion resistance and lightweight nature. Its ease of fabrication makes it a popular choice for these applications.
Interior Panels: The alloy’s aesthetic appeal and durability make it suitable for interior panels in buildings.
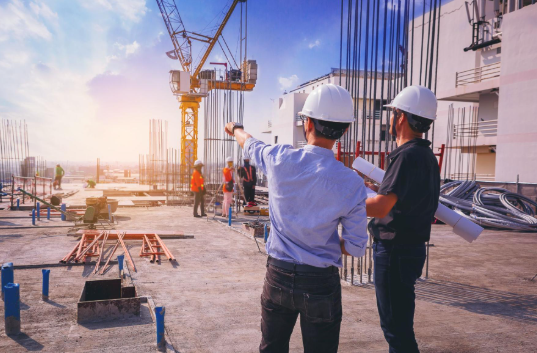
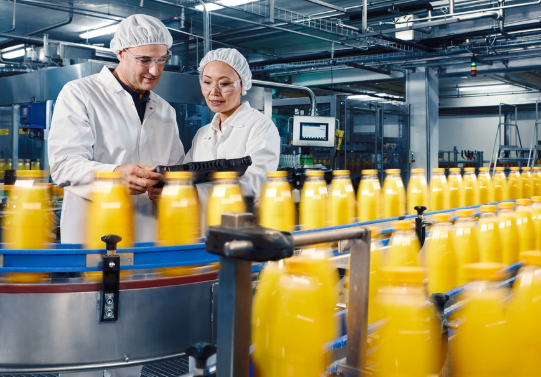
-Food and Beverage Industry
Food Processing Equipment: The non-toxic nature and corrosion resistance of Aluminum 1100 make it ideal for food processing equipment, ensuring food safety and hygiene.
Packaging: It is used in packaging materials, such as bottle caps and aluminum foil, which are essential for preserving food and beverages.
-Chemical Industry
Chemical Processing Equipment: Aluminum 1100 can withstand corrosive chemicals, making it suitable for use in chemical processing equipment and storage tanks.
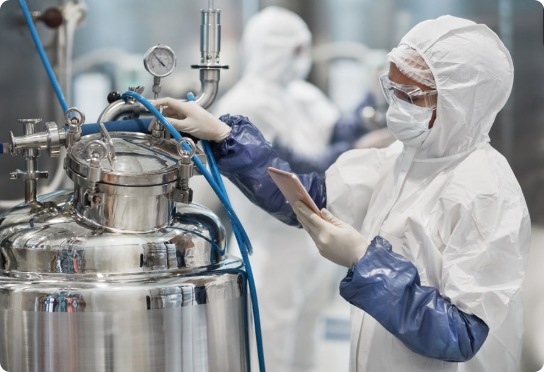
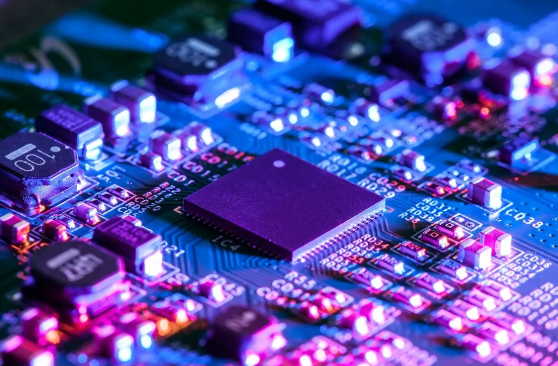
-Electrical and Electronics
Electrical Conductors: Due to its excellent electrical conductivity, Aluminum 1100 is used in the manufacturing of electrical conductors and transmission lines.
Heat Sinks: The alloy’s high thermal conductivity makes it an ideal material for heat sinks in electrical applications, helping to dissipate heat efficiently.
-Transportation
Automotive Components: Aluminum 1100 is used in the manufacture of components for automobiles, trailers, and other transportation vehicles. Its lightweight nature contributes to fuel efficiency and reduced emissions.
Heat Exchangers: In the transportation industry, it is also used for heat exchangers, which are crucial for cooling engines and other systems.
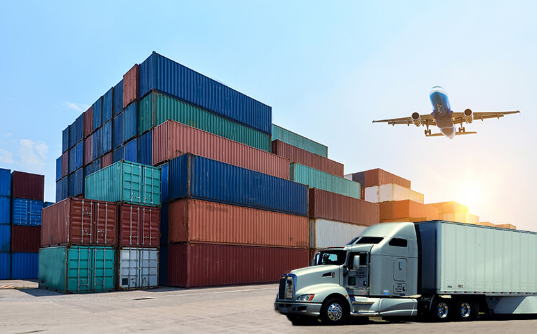
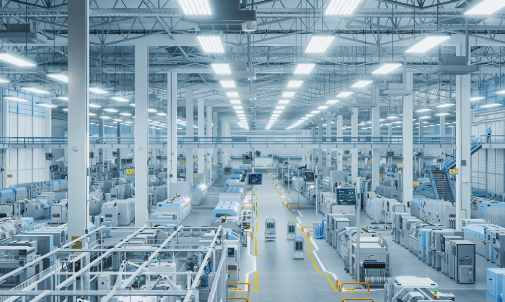
-General Manufacturing
Sheet Metal Products: Aluminum 1100 is used to produce sheet metal products due to its excellent formability and workability.
Welding and Fabrication: The alloy’s superior weldability allows it to be easily joined with other materials, making it suitable for various fabrication processes.
What’s Aluminum 1100-H14 & Its Grade?
Aluminum 1100-H14 is a commercially pure aluminum alloy in the H14 temper condition, known for its excellent corrosion resistance, high ductility, and good workability. It contains a minimum of 99.00% aluminum with trace amounts of other elements such as iron and silicon. In the H14 temper, it offers a tensile strength of 110-145 MPa and a yield strength of 95 MPa, with an elongation of at least 5%. This grade is ideal for applications requiring moderate strength and excellent formability, such as general sheet metal work, heat exchangers, food containers, and architectural components.
What’s Aluminum 1100-H18 & Its Grade?
Aluminum 1100-H18 is a high-purity aluminum alloy (with a minimum of 99.00% aluminum content) in the fully strain-hardened temper, offering the highest strength and hardness among the 1100 series. It has excellent corrosion resistance, thermal conductivity, and electrical conductivity, making it suitable for applications requiring high strength and durability. The H18 temper indicates that the material has been strain-hardened to achieve maximum strength, resulting in reduced ductility. This grade is commonly used in structural components, heavy-duty applications, and environments where high strength is crucial.
1100 H14 Aluminum vs 1100 H18, What’s the Difference?
When comparing 1100-H14 aluminum and 1100-H18 aluminum, the main differences lie in their temper (hardness) and mechanical properties, which result from how they are processed. Both belong to the 1100 aluminum series, which is known for its high purity, excellent corrosion resistance, and outstanding workability.
- Temper Designation
The temper designation refers to the mechanical treatment the material has undergone to achieve specific properties.
H14: This temper indicates the aluminum is strain-hardened to half-hard. It strikes a balance between strength and formability.
H18: This temper indicates the aluminum is strain-hardened to the full-hard condition, making it stronger but less ductile than H14. - Strength and Hardness
The difference in temper directly affects the aluminum’s strength and hardness:
1100-H14: This has moderate strength and hardness, with a tensile strength range of approximately 18,000–22,000 psi. It is softer than H18, making it easier to form into shapes.
1100-H18: This has higher strength and hardness, with a tensile strength range of around 24,000–27,000 psi. It is harder and more durable, which makes it better suited for applications requiring higher strength. - Ductility and Formability
Ductility refers to how easily the aluminum can be stretched or shaped without breaking:
1100-H14: Offers excellent ductility and is easier to bend, roll, or form into complex shapes. It is ideal for aphplications like deep drawing or spinning.
1100-H18: Has reduced ductility due to its full-hard temper, making it less suitable for intricate forming processes. It is better for flat, rigid applications where strength is more important than flexibility. - Applications
The choice between H14 and H18 depends on the specific requirements of the application:
1100-H14: Commonly used in applications where moderate strength and high ductility are required, such as:
Decorative panels
Chemical equipment (e.g., tanks, pipes)
Roofing and siding materials
Food and beverage containers
1100-H18: Typically used in applications requiring higher strength and rigidity, such as:
Nameplates and tags
Rigid panels
Reflectors
Industrial equipment components