When selecting aluminum for a project, choosing the right alloy can make all the difference in performance, durability, and cost-effectiveness. Among the many options available, Aluminum 3003 and Aluminum 6061 are two of the most popular choices due to their versatility and unique properties. While both are widely used across industries, they differ significantly in terms of composition, strength, corrosion resistance, and machinability. Understanding these differences is essential to ensure the alloy meets the specific requirements of your application. In this 3003 aluminum and 6061 comparison guide, we’ll find out the differences between them, as well as advantages, and the best use cases to help you make an informed decision.
What is Aluminum 3003?
Aluminum 3003 is a non-heat-treatable aluminum alloy primarily composed of aluminum (around 97%) with small amounts of manganese (1.0%-1.5%) and trace amounts of copper (~0.12%). It belongs to the 3xxx series of aluminum alloys, which are known for their excellent corrosion resistance and moderate strength. Due to its chemical composition, Aluminum 3003 is highly resistant to atmospheric corrosion, making it suitable for outdoor and industrial applications.
This alloy is widely recognized for its outstanding formability and ductility, allowing it to be easily bent, spun, or deep-drawn without cracking. While it is not as strong as some other aluminum alloys, such as 5052, it compensates by being lightweight, easy to work with, and cost-effective.
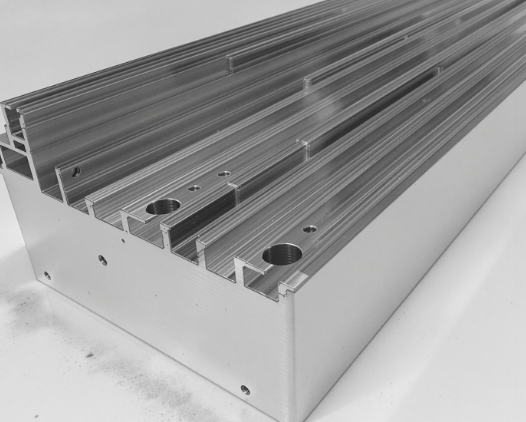
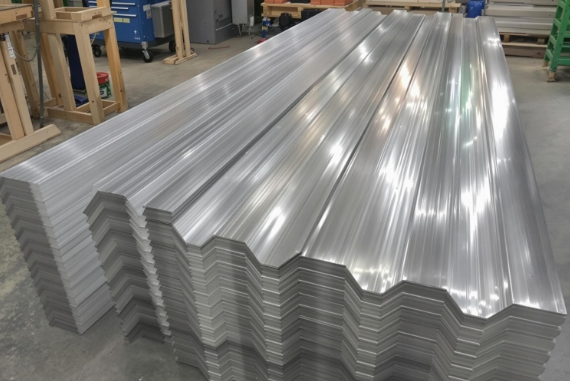
What is Aluminum 6061?
Aluminum 6061 is a heat-treatable aluminum alloy that belongs to the 6xxx series, which is primarily known for its excellent strength, corrosion resistance, and machinability. It is composed mainly of aluminum (around 97.9%), with magnesium (0.8%-1.2%) and silicon (0.4%-0.8%) as its primary alloying elements, along with trace amounts of iron, copper, and chromium. The combination of these elements gives Aluminum 6061 a unique balance of mechanical properties and versatility.
One of the standout features of 6061 is its high strength-to-weight ratio, making it suitable for structural applications. Additionally, it exhibits excellent corrosion resistance, particularly against environmental factors and stress cracking. 6061 is easily welded and can be machined into complex shapes with precision, making it a go-to material in many industries.
Key Properties Aluminum 3003
Aluminum 3003 is highly valued for its excellent corrosion resistance, lightweight nature, and outstanding formability. As a non-heat-treatable alloy, it has moderate strength, making it suitable for applications where high structural integrity is not critical. Its ability to resist atmospheric corrosion and chemical exposure makes it ideal for outdoor and industrial uses. Additionally, Aluminum 3003 is highly ductile, allowing it to be easily bent, spun, or deep-drawn without cracking, making it perfect for applications requiring intricate shapes or designs. Its combination of versatility, durability, and cost-effectiveness makes it a widely used alloy across various industries.
Common Applications of 3003 Aluminum
- Roofing, siding, and gutters
- Cooking utensils and food storage containers
- HVAC ductwork
- Fuel tanks and chemical storage tanks (non-pressurized)
- Signs and decorative panels
Key Properties Aluminum 6061
Aluminum 6061 is known for its excellent strength-to-weight ratio, good corrosion resistance, and versatility. As a heat-treatable alloy, its strength can be significantly enhanced through tempering, making it suitable for both structural and precision applications. It resists corrosion well in most environments, including marine and industrial conditions. Additionally, 6061 offers excellent machinability, allowing it to be shaped and cut with ease, while its good weldability ensures strong, reliable joints for various uses. These combined properties make 6061 a durable, lightweight, and adaptable choice for a wide range of applications.
Common Applications of 6061 Aluminum
- Aerospace components
- Automotive parts
- Construction materials (e.g., frames, bridges, and pipelines)
- Marine equipment
- Bicycle frames
- Electronics enclosures and industrial equipment
6061 vs 3003 Aluminum: What’s the Difference?
Composition and Basic Properties
- 3003 Aluminum Alloy: It is a manganese alloy, containing about 1.2% manganese. It has good ductility, corrosion resistance, and weldability.
- 6061 Aluminum Alloy: It is a magnesium-silicon alloy, containing magnesium and silicon. This alloy can be strengthened by heat treatment and has high strength and good corrosion resistance.
Mechanical Properties
Property | 3003 Aluminum Alloy | 6061 Aluminum Alloy |
---|---|---|
Tensile Strength | Lower | Higher |
Yield Strength | Lower | Higher |
Shear Strength | Lower | Higher |
Machinability | Good | Good |
Corrosion Resistance | Excellent | Good |
Weldability | Excellent | Excellent |
Formability | Excellent | Moderate |
Heat Treatable | No | Yes |
Application Fields
- 3003 Aluminum Alloy: Suitable for applications where high strength is not required, such as food processing equipment, architectural decoration, chemical processing equipment, ventilation ducts, kitchen utensils, storage tanks, and transportation containers.
- 6061 Aluminum Alloy: Widely used in fields where high strength and corrosion resistance are required, such as aerospace, automotive manufacturing, shipbuilding, bicycle frames, building structures, and industrial components.
Which Is Better, 6061 Aluminum or 3003 Aluminum?
The choice between aluminum 6061 vs 3003 depends on your specific needs. If cost, corrosion resistance, and formability are your priorities, 3003 aluminum is the better option. However, if strength, durability, and structural applications are critical, 6061 aluminum is the ideal choice despite its higher cost.
Aluminum 3003 vs 6061 Cost & Price
When comparing 3003 aluminum vs. 6061 aluminum in terms of cost, 3003 aluminum is the more economical option. This is because 3003 contains fewer alloying elements (primarily manganese and a trace of copper), making it less expensive to produce. It is widely used in non-structural applications where high strength is not required, providing an affordable solution for projects like roofing, siding, or food containers.
In contrast, 6061 aluminum is more expensive due to its complex composition, including magnesium and silicon, and the additional processes required for heat treatment to achieve its higher strength. Its premium price reflects its superior mechanical properties, making it better suited for demanding structural and industrial applications such as aerospace, automotive, and marine industries.
3003 Aluminum vs 6061 Tensile Strength
When comparing tensile strength, 6061 aluminum significantly outperforms 3003 aluminum.
- 3003 Aluminum has a tensile strength of approximately 20,000–30,000 psi, depending on the temper. This moderate strength is sufficient for lightweight applications like roofing, siding, or cooking utensils, where heavy loads or high stresses are not involved.
- 6061 Aluminum, on the other hand, has a tensile strength of approximately 35,000–45,000 psi, depending on its temper (e.g., T6 being the strongest). This makes it nearly double the strength of 3003 aluminum, making it an ideal choice for structural, aerospace, and automotive applications where durability and load-bearing capacity are critical.
6061 Aluminum vs 3003 Aluminum Tread Plate, Which Is Better?
1. Strength:
- 6061 Tread Plate: Superior strength and durability, with a tensile strength of 35,000–45,000 psi. It can handle heavy loads and high-stress environments, making it ideal for structural and industrial applications like flooring in trucks, platforms, and warehouses.
- 3003 Tread Plate: Lower tensile strength at 20,000–30,000 psi. It is better suited for lighter-duty applications, such as decorative purposes or flooring in low-traffic areas.
2. Corrosion Resistance:
- Both 6061 and 3003 have good corrosion resistance, but their performance varies by environment.
- 6061 offers excellent resistance to stress corrosion cracking, making it suitable for marine and industrial environments.
- 3003 has outstanding corrosion resistance in chemical or atmospheric conditions, ideal for applications like food storage or outdoor use.
3. Formability:
- 3003 Tread Plate is much easier to bend and form due to its softer nature, making it ideal for applications requiring intricate shapes or designs.
- 6061 Tread Plate is more rigid and less formable, especially in the T6 temper, which may limit its use in projects requiring significant bending.
4. Weldability:
- Both alloys are weldable, but 3003 is easier to weld with conventional techniques and doesn’t require special handling.
- 6061 can also be welded but requires attention to avoid weakening the heat-affected zone, which can affect its structural integrity.
5. Applications:
- 6061 Tread Plate: Best for structural applications like truck beds, heavy-duty walkways, stair treads, and marine decks due to its strength and durability.
- 3003 Tread Plate: Ideal for decorative purposes, lightweight flooring, toolboxes, or storage containers where strength is less critical.