When selecting the right aluminum alloy for your project, choosing between 6082 and 6061 can be a challenging decision. Both are popular heat-treated alloys from the 6000 series, known for their excellent strength, corrosion resistance, and versatility. However, each alloy has distinct characteristics that make it better suited for specific applications. In this aluminium 6061 vs 6082 guide, we’ll break down the key differences between them.
What is Aluminum 6082?
Aluminum 6082 is a medium-strength alloy that belongs to the wrought aluminum-magnesium-silicon family, specifically the 6000 series. It is known for its excellent corrosion resistance and is often used in structural applications due to its high strength compared to other alloys in the same series.
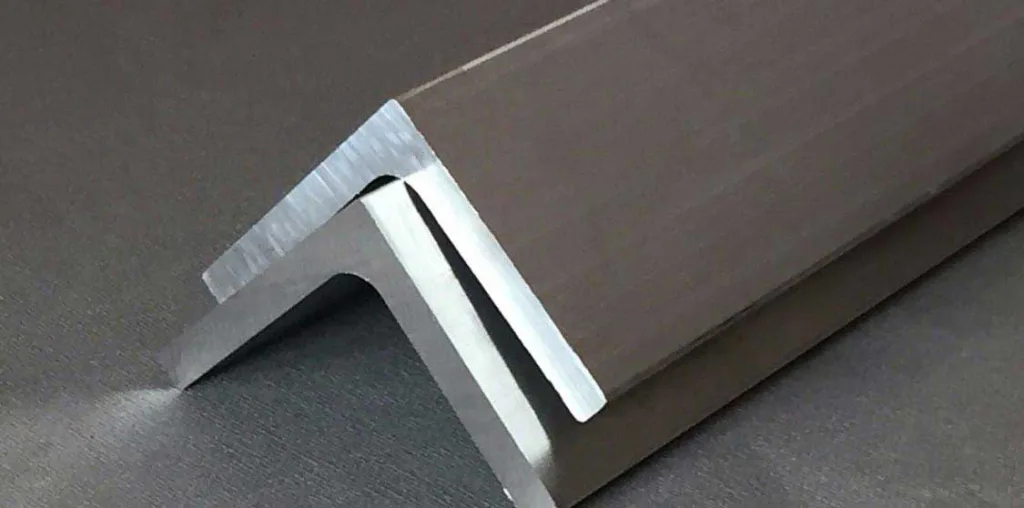
Aluminum 6082 Material Properties
Aluminum 6082 is a medium-strength alloy known for its excellent corrosion resistance and high strength within the 6000 series, making it a popular choice for structural applications. It features a chemical composition that includes silicon (0.7-1.3%), manganese (0.4-1.0%), and magnesium (0.6-1.2%), which contribute to its mechanical properties. In the T6 temper, Aluminum 6082 exhibits a proof stress of 250-260 MPa and a tensile strength of 290-310 MPa, along with good machinability and weldability, although strength may be reduced in the weld zone. This alloy is commonly used in applications such as trusses, cranes, and transport structures due to its favorable balance of strength and workability.
Aluminum 6082 Characteristics
Strength: Aluminum 6082 has the highest strength of the 6000 series alloys, making it suitable for highly stressed applications such as trusses, bridges, and cranes.
Corrosion Resistance: This alloy exhibits excellent resistance to corrosion, which is a critical property for materials used in outdoor and marine environments.
Machinability: It is known for good machinability, especially in the T6 and T651 tempers, which are commonly used in manufacturing processes.
What is Aluminum 6061?
Aluminum 6061 is a widely used aluminum alloy known for its excellent mechanical properties, good weldability, and versatility in various applications. It is classified as a precipitation-hardened alloy, primarily composed of magnesium and silicon, which contribute to its strength and corrosion resistance. Originally developed in 1935, it has become one of the most common aluminum alloys for general-purpose use.
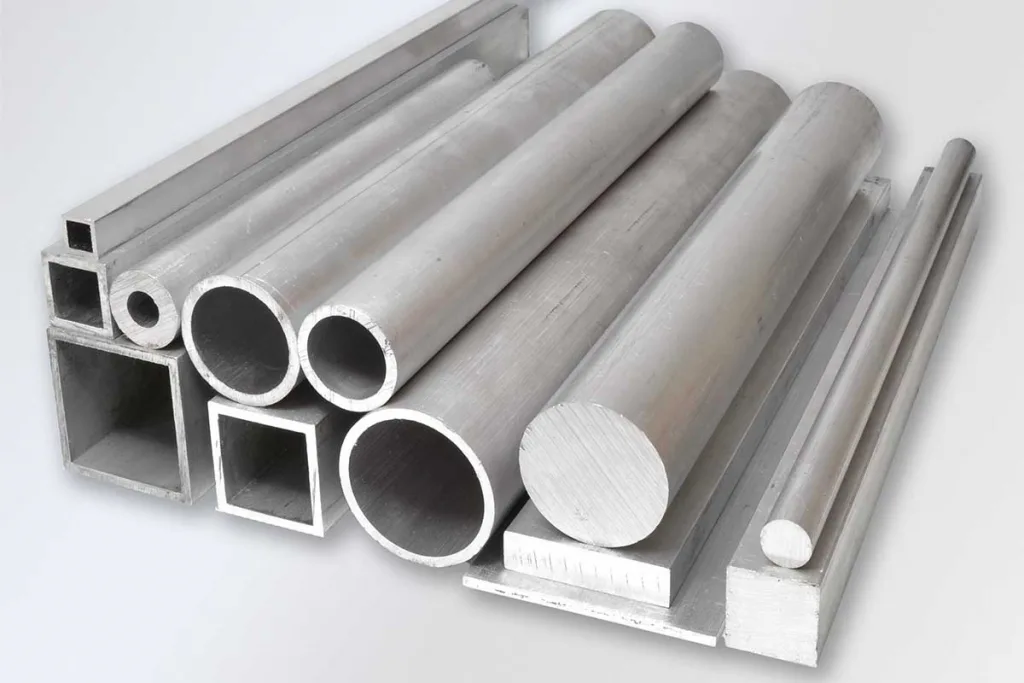
Aluminum 6061 Material Properties
Aluminum 6061 is a versatile alloy known for its excellent mechanical properties, good corrosion resistance, and high weldability, making it suitable for a wide range of applications. It has a chemical composition primarily consisting of aluminum (97.9%), magnesium (1.0%), silicon (0.6%), copper (0.28%), and chromium (0.20%). The alloy exhibits a tensile strength of approximately 310 MPa (45,000 psi) in the T6 temper, with a yield strength of around 276 MPa (40,000 psi) and good elongation properties of 12-17%. Its density is about 2.7 g/cm³, and it has a melting point of 588°C (1,090°F). Aluminum 6061 is commonly used in structural applications, including automotive and aerospace components, due to its favorable balance of strength and workability.
Aluminum 6082 Characteristics
Mechanical Properties: The alloy exhibits a tensile strength ranging from 124 to 290 MPa (18.0 to 42.1 ksi) depending on the temper, with the T6 temper providing the highest strength, reaching up to 310 MPa (45 ksi).
Weldability: Aluminum 6061 is highly weldable using techniques such as TIG and MIG welding, although the strength near the weld may decrease unless properly heat-treated afterward.
Thermal Properties: It has a melting temperature of approximately 585 °C (1,085 °F) and good thermal conductivity, making it suitable for applications requiring heat dissipation.
Forms and Temperatures: The alloy is available in various forms, including extrusions, sheets, and plates, and is commonly found in tempers such as 6061-O (annealed), 6061-T4, and 6061-T6.
Aluminum 6082 vs 6061, What’s the Difference?
Chemical Composition
Aluminum 6082 contains slightly more manganese (Mn) than 6061, which enhances its strength and corrosion resistance. On the other hand, 6061 has a higher content of magnesium (Mg) and silicon (Si), which contribute to its good machinability and balanced strength. These differences in composition are what drive the variations in their mechanical and physical properties.
Density
6082: The density of aluminum 6082 is 2.70 g/cm³.
6061: The density of aluminum 6061 is also 2.70 g/cm³.
Both alloys have the same density, as they are part of the 6000 series and share a similar base aluminum composition.
Melting Temperature
6082: The melting temperature of aluminum 6082 ranges from 555°C to 650°C (1,031°F to 1,202°F).
6061: The melting temperature of aluminum 6061 is slightly higher, ranging from 580°C to 650°C (1,076°F to 1,202°F).
The slight difference in melting temperatures is due to variations in their magnesium and silicon content.
Price
6082: Aluminum 6082 is generally 5–15% more expensive than 6061. This is due to its higher strength and better corrosion resistance, making it slightly less commonly used and more costly.
6061: Aluminum 6061 is more cost-effective and widely available, as it is one of the most commonly used aluminum alloys for general-purpose applications.
Pricing can vary based on supplier, market conditions, and product form (e.g., sheets, plates, bars).
Mechanical Properties
When it comes to strength, 6082 generally outperforms 6061, making it a better choice for applications requiring high structural integrity. However, 6061 compensates for its slightly lower strength by offering better elongation and toughness, making it more resistant to cracking under stress. Similarly, 6082 is harder due to its higher manganese content, while 6061 is less hard but more ductile, allowing it to bend and deform without breaking.
Machinability
6061 is widely regarded for its excellent machinability. It is easier to machine into complex shapes and intricate geometries, which is why it is often favored for CNC machining applications. In contrast, 6082 is slightly less machinable due to its higher strength and hardness. While it can still be machined effectively, it may require more effort and specialized tools.
Weldability
Both alloys are highly weldable, but there are key differences in how they respond to welding. Aluminum 6082 may lose some of its strength in the heat-affected zones after welding because of its higher manganese content. On the other hand, 6061 retains more of its strength after welding, making it a better choice for projects that involve extensive welding. This makes 6061 especially popular in industries like aerospace and automotive, where welding is frequently required.
Corrosion Resistance
Both 6082 and 6061 offer excellent resistance to corrosion, especially in environments prone to oxidation. However, 6082 performs slightly better in this regard thanks to its higher manganese content. This makes it particularly suitable for marine environments or applications where prolonged exposure to moisture or saltwater is a concern. While 6061 is still highly resistant to corrosion, it falls slightly behind 6082 in this category.
Applications
Aluminum 6082 is often used in structural applications such as bridges, trusses, and cranes, where its superior strength and corrosion resistance are vital. It is also a popular choice in marine applications due to its ability to withstand harsh, corrosive environments. In contrast, 6061 is widely used in aerospace, automotive, electronics, and recreational equipment. Its excellent machinability and toughness make it ideal for projects requiring complex machining or welding. It is also a preferred material for lightweight yet durable components.
Heat Treatment
Both alloys are heat-treatable and their mechanical properties can be enhanced through tempering processes. The T6 temper (solution heat-treated and artificially aged) is the most commonly used for both 6082 and 6061. This temper provides the highest strength for these alloys, making them suitable for demanding applications. While both alloys respond well to heat treatment, the choice of alloy will depend on whether you prioritize machinability or structural strength.
Property | 6082 | 6061 |
Density | 2.70 g/cm³ | 2.70 g/cm³ |
Melting Temperature | 555–650°C (1,031–1,202°F) | 580–650°C (1,076–1,202°F) |
Tensile Strength | 310–340 MPa | 290–310 MPa |
Yield Strength | ~260 MPa | ~240 MPa |
Hardness | Higher | Lower |
Machinability | Slightly harder to machine | Excellent |
Weldability | Loses strength in HAZ | Retains strength better |
Corrosion Resistance | Slightly better | Excellent, but slightly less |
Price | ~5–15% higher | More cost-effective |
Applications | Structural, marine | Aerospace, automotive, machining |
Which is Better, 6061 vs 6082 Aluminium?
Choose 6082 if: You need higher strength and better corrosion resistance or you are working on structural or marine applications.
Choose 6061 if: You need better machinability and toughness or you are working on aerospace, automotive, or intricate machining projects.
Aluminum 6082 T6 vs 6061 T6, What’s the Difference
Chemical Composition
Both alloys are primarily composed of aluminum with magnesium and silicon as their main alloying elements. However, 6082-T6 has a slightly higher manganese content, which improves its strength and corrosion resistance. In contrast, 6061-T6 contains slightly more magnesium and silicon, which enhance its machinability and overall toughness.
Strength and Hardness
In terms of strength, 6082-T6 generally has higher tensile strength and yield strength compared to 6061-T6. This makes 6082-T6 better suited for structural applications where load-bearing capacity is critical. Additionally, 6082-T6 is harder due to its composition, while 6061-T6 is slightly softer, offering better flexibility and resistance to cracking under stress.
Machinability
6061-T6 is well-known for its excellent machinability, making it a preferred choice for CNC machining and projects that require intricate shapes or precise geometries. On the other hand, 6082-T6 is slightly more difficult to machine because of its higher strength and hardness. It can still be machined effectively but may require specialized tools or slower cutting speeds.
Weldability
Both 6082-T6 and 6061-T6 are highly weldable, but how they respond to welding differs. 6082-T6 tends to lose more strength in the heat-affected zones (HAZ) after welding, making it less suitable for applications where welding is a critical factor. In contrast, 6061-T6 retains more of its strength after welding, making it a better choice for applications that involve extensive welding processes.
Corrosion Resistance
Both alloys offer excellent corrosion resistance, especially in environments exposed to moisture or oxidizing conditions. However, 6082-T6 slightly outperforms 6061-T6 in terms of corrosion resistance, particularly in marine environments or areas prone to saltwater exposure. The higher manganese content in 6082-T6 contributes to this improved resistance.
Heat Treatment and Aging
Both alloys are heat-treated to the T6 temper, which involves solution heat treatment followed by artificial aging. This process maximizes their strength and hardness. However, the exact mechanical properties after treatment will vary slightly, with 6082-T6 offering higher strength and 6061-T6 offering better machinability and ductility.
Which is Better, 6061 T6 vs 6082 T6 Aluminium?
Choose 6082-T6 if: You need higher strength, better corrosion resistance, and are working on structural, marine, or heavy-duty applications. It is ideal for load-bearing constructions or projects exposed to harsh environments.
Choose 6061-T6 if: You prioritize machinability, weldability, and a more cost-effective solution. It is a great choice for aerospace, automotive, and precision-machined components.