In recent years, with the improvement of people’s living standards, the demand for automobiles has also increased, and the competition among various automobile factories has become increasingly fierce, and new models with cost competitiveness have been continuously invested to seize the market. However, natural resources such as iron ore and coke required by the project are becoming increasingly scarce. Improving the utilization rate of materials can not only reduce the manufacturing cost of precision stamping parts of automobiles, improve the competitiveness of automobile brands, but also conform to the environmental protection concept of energy saving and consumption reduction. The following are ways to improve the material utilization rate of die stamping parts in the automotive industry.
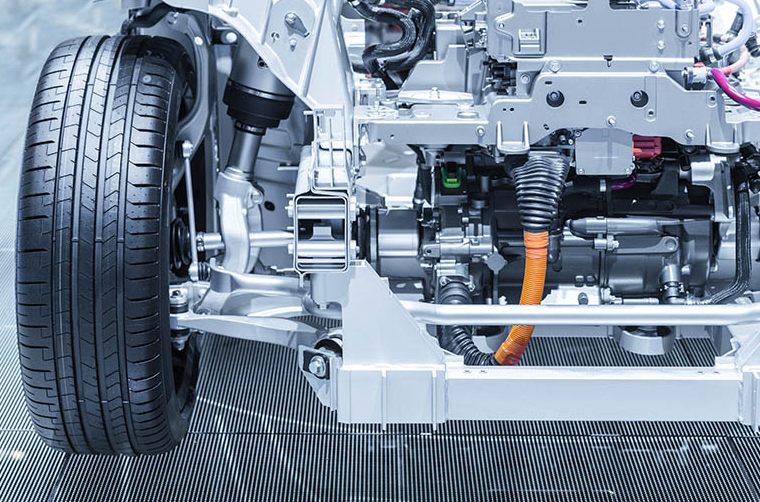
1. Optimize blanking and layout to reduce waste
– For some special-shaped precision stamping parts, the arrangement of blank sheets in the uncoiling blanking die can be optimized to reduce waste, uncoil as many blank sheets as possible, and improve material utilization.
The layout optimization of the rough blanks in the left and right inner longitudinal beam blanking dies of the T6 model optimizes the original one-step production of one blank to one-step production of two blanks, reducing the weight of waste and making the left and right inner The material utilization rate of the longitudinal beams increased from 78.2% to 87.6%.
2. Consolidation of material specifications to reduce waste
-In order to improve market competitiveness and enrich sales product lines, automobile factories will invest in new models every year, and new specifications of materials will be produced for investment in precision stamping parts of new models. When the mass production of models ends, the corresponding special steel will occupy the inventory due to slow consumption. Therefore, each addition of a new specification of steel will increase the inventory and management costs. Automobile factories must ensure the versatility of steel as much as possible to reduce The number of varieties of steel.
The layout optimization process of the hood outer panel of the T6 model, the roll width of the hood outer panel of the T6 model is 1330mm, and the uncoiling step is 1820mm, and a blanking die is required; while the roll width of the hood outer panel of the X7 model is 1830mm, Use the curved pendulum shears to cut blanks without waste. Since the uncoiling step of the T6 hood is similar to the material width of the X7 hood roll material, through field verification, the coil material of the X7 hood can be used to produce the plate of the T6 hood by arc pendulum shearing according to the parameter of the step distance of 1170mm material. Through process optimization, the utilization rate of materials has increased by 3.7%, and at the same time, the special steel specifications for the original T6 hood outer panels have been reduced, the versatility of materials has been increased, and inventory and management costs have been reduced.
3. Mold design optimization, one mold with multiple pieces
– When multiple precision stamping parts are produced on a set of molds at the same time, one or more small precision stamping parts are produced by using the waste at the hole of the large precision stamping part, so as to achieve the effect of improving the utilization rate of materials.
The molds for the inner panel of the hood of the B5 model and the inner panel of the door of the T7 use the waste materials in the holes of the precision stamping parts of the inner panel of the hood and the inner panel of the door to punch out the precision stamping parts of the hood reinforcement plate and the reinforcement plate of the door lock, avoiding Use materials alone to produce hood reinforcements and door lock reinforcements.
4. Die design optimization, slab combination
-During mold design, the left and right symmetrical precision stamping parts are designed to be stamped together. Through process optimization, two precision stamping parts are stamped out of two sheets instead of two precision stamping parts are punched out of one sheet. parts, reduce the process supplementary area, and improve material utilization.
The mold design for the precision stamping parts of the left and right rear door outer panels of the MX3 model is compared with the mold design of the left and right rear door outer panels of the M44 model. The left and right rear door outer panels of the MX3 model stamp one precision stamping part from a sheet, and the four directions of the precision stamping part require process supplementary surfaces; while the left and right rear door outer panels of the M44 model are stamped out of two precision stamping parts from a sheet. parts, which is equivalent to reducing one process supplementary surface. By comparison, the material utilization rate of the rear door outer panel of the M44 model is 4.16% higher than that of the MX3 rear door outer panel.
5. Material size optimization to reduce blank size
-By adjusting the positioning of the blank sheet in the drawing die, the process supplement of excess material other than the drawbead is reduced, thereby reducing the size of the blank sheet required for precision stamping parts and improving the utilization rate of materials.
It is a precision stamping part of the lower beam of the windshield of the T/B model. The observation of the drawn transition piece found that a large part of the blank sheet in the process supplement area of the drawn part has not been effectively utilized. Through measurement, the precision The uncoiling step of the stamping parts was reduced from the original 590mm to 560mm, and the drawing die was grinded together, and the sheet positioning device was adjusted. After visual inspection and three-coordinate measurement of geometric dimensions, it was confirmed that: In the case of 30mm smaller, the precision stamping part is formed normally and the quality meets the standard. After the precision stamping parts of the lower beam of the windshield of the T/B model are optimized by blank size, the material utilization rate increases by 2.4%.
6. Control the tolerance of coil materials and increase the number of blanks
– When steel mills produce steel coils and steel plates, they have a certain control range for the thickness tolerance of the products. Table 1 shows the coil size control standards. If the thickness of the steel coil is delivered to the automobile factory according to the positive tolerance, the thickness of the uncoiled blank sheet will be thicker within the acceptable range, which will cause the actual weight of the blank sheet and stamped precision stamping parts to be higher than the process rated weight. On the other hand, it will cause the actual number of sheets produced by the uncoiling of steel coils to be less than the theoretical number, resulting in a reduction in the finished product rate.
For example, the R33 top cover precision stamping parts, the blank sheet size is 0.8mm×1150mm×1680mm, the material grade is DX54D+Z, there are three suppliers for the material, and the tolerance dimensions of the materials of the three suppliers are all within the acceptable range, but passed According to the follow-up, the actual number of sheets after each uncoiling of one of the materials is less than the theoretical number, while the actual number of sheets after uncoiling of the other two steel coil materials is slightly higher than the theoretical number.
The process consumption quota of R33 top cover precision stamping parts is 11.993kg. A steel coil with a weight of 10t can theoretically be uncoiled to produce 10000kg/11.993kg=834 R33 top cover sheets. According to the standard in Table 1, the yield strength of the DX54D+Z material used for R33 top cover precision stamping parts is less than 280MPa, and the coil width is 1150mm, less than 1200mm, so the thickness difference between the thinnest and thickest sheet metal is 0.06mm, then one The maximum and minimum number of sheets that can be uncoiled for a 10t steel coil are 996 sheets and 771 sheets respectively, with a difference of 125 sheets. In the case of negative tolerance delivery, the material is increased by 15% compared with positive tolerance delivery. utilization rate. Therefore, steel mills are required to deliver steel coils with a negative tolerance, which can significantly increase the number of blanks and improve material utilization.
7. Waste collection and reuse
– When some precision stamping parts are uncoiled and blanked, unused waste with a large area will be generated. Using these waste materials for the production of other small precision stamping parts on the car body can avoid the loss of materials used in small precision stamping parts. Purchasing separately saves costs and improves the material utilization rate of the vehicle.
It is the inner panel of the R33 rear fender, and its coil size is 0.7mm × 1275mm, and there is a waste when uncoiling. The sheet material size of the precision stamping part of the front wall upper cover is 0.7mm×445mm×1070mm, and the consumption quota is 2.594kg. The material grades of these two precision stamping parts are the same. Waste materials are used to produce precision stamping parts of the cowl upper cover, and the material utilization rate increases by 13%. The waste of the R33 side wall outer panel is collected by a similar method, the size of the coil is 0.85mm×1450mm, and the material grade is DX56D+Z. The precision stamping part of the front part of the R33 left and right rear wheel covers, size is 0.8mm×930mm×254mm, and the material grade is DX56D+Z. By collecting the waste generated during the uncoiling of the R33 side wall, and manually trimming the waste, the obtained rectangular sheet can be used to produce R33 left and right rear wheel cover precision stamping parts, and the material utilization rate is increased by 8%.
8. Very high coil weight, reducing head and tail waste
-The stamping process is that the material supplier supplies the packaged coil material. After the coil material is unpacked, it is cut into various shapes required for stamping by the uncoiling equipment, and then various precision stamping parts are stamped out. When uncoiling, it is necessary to cut the outer ring and inner ring of the coil material, and at the same time, the head and tail of the coil material need to pass through the uncoiling equipment, and the head and tail of each coil material is about 15 meters, which is the normal production loss. Therefore, the larger the uncoiling batch, the heavier the average weight of the coil material, the higher the uncoiling efficiency, and the less the average loss of the coil material. The overall side wall outer panel material consumption of a car model is about 60kg, and the stamping and uncoiling line has a large batch. Tracking the weight of the side wall material coil, the coil weight distribution ranges from 7t to 15t, and the average weight is about 10t. After calculation and analysis, if the coil material When the weight is increased to 18 tons, the uncoiling line will produce one less coil per batch, that is, one less coil head and tail processing, the utilization rate of side wall materials can be increased by about 1%, and the uncoiling efficiency can be increased by about 5%. Combined with equipment capacity and transportation conditions, the weight requirements of the coils were proposed to the steel mill. At present, the average coil weight of this side wall material is 18.5t, and the utilization rate of coils into sheets has increased from the original 98.2% to 99.2% (sheet conversion rate = net weight of coil/consumption quota × 100%).