Tool steels are essential in the manufacturing of cutting tools, dies, and molds that must withstand significant mechanical stress and wear. Among these, A2 tool steel is one of the most widely used and well-balanced options. It provides a reliable blend of hardness, toughness, dimensional stability, and wear resistance, making it suitable for both industrial and custom applications. With this blog, we are going to present a thorough overview of A2 tool steel – examining its composition, physical and mechanical properties, tempering behavior, equivalents, applications, cost, and how it compares to other well-known tool steels like D2 and O1.
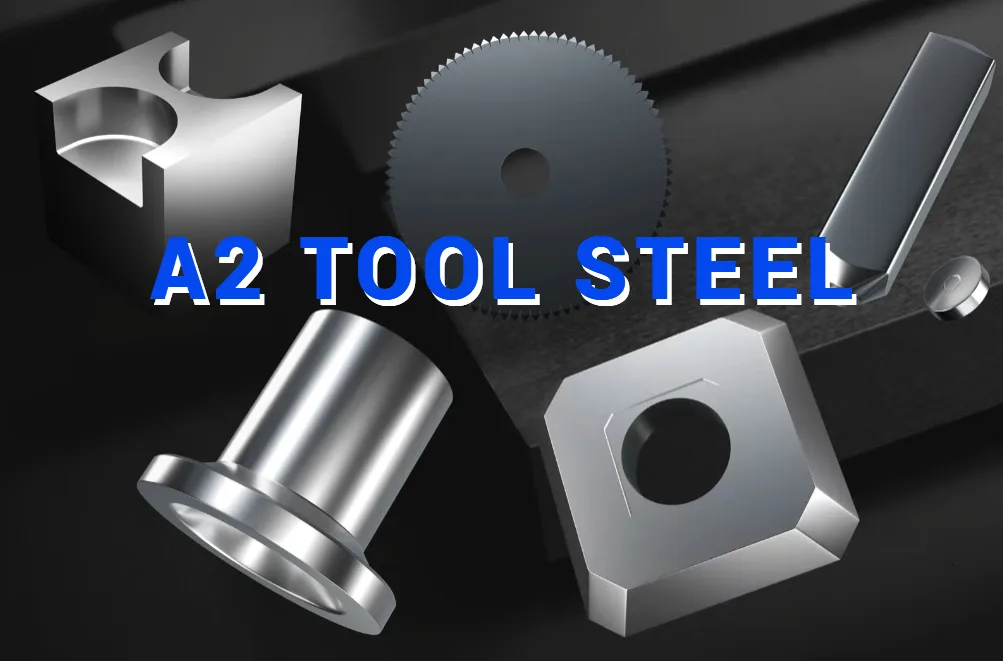
What is A2 Tool Steel?
AISI A2 tool steel is part of the A-series of air-hardening cold work tool steels, developed in the early 20th century. It was designed to provide a middle ground between O1’s ease of machining and D2’s wear resistance, offering both good toughness and dimensional control. As an air-hardening steel, A2 can be hardened in still air, which reduces distortion compared to oil-quenched steels and makes it more forgiving in heat treatment.
Its development was part of a broader evolution in tool steel technology, which progressed from basic carbon steels to more complex alloyed steels with added chromium, molybdenum, and vanadium to improve hardenability and performance. A2 became widely used by the 1940s and has remained popular due to its versatility and performance in cold work environments.
To better understand A2’s capabilities, let’s begin with its elemental makeup.
A2 Tool Steel Composition
The composition of A2 tool steel plays a significant role in determining its mechanical behavior. The typical chemical makeup includes:
- Carbon (0.95–1.05%) – Increases hardness and wear resistance
- Chromium (4.75–5.50%) – Improves hardenability, wear resistance, and provides minimal corrosion resistance
- Molybdenum (0.90–1.40%) – Enhances toughness and deep hardening
- Vanadium (0.15–0.50%) – Refines grain structure and improves wear resistance
- Manganese (0.50–1.00%) and Silicon (0.30–0.50%) – Support hardenability and strength
This balanced alloy ensures that A2 tool steel performs well under mechanical stress and maintains structural integrity during heating and cooling cycles.
With the composition in mind, we now turn to how these elements affect the physical and mechanical properties of A2 steel.
A2 Tool Steel Properties
A2 tool steel is known for its well-rounded performance characteristics. It offers a useful combination of hardness, toughness, wear resistance, and dimensional stability, which are essential for tooling and cutting applications.
A2 Steel Mechanical Properties
- Hardness: 57–62 HRC after proper heat treatment
- Yield Strength: 185–230 ksi
- Tensile Strength: Around 250 ksi
- Impact Resistance: Relatively high for a tool steel
- Edge Retention: Maintains a sharp edge under use
A2 Steel Physical Properties
- Density: ~7.85 g/cm³
- Thermal Conductivity: ~24 W/m·K
- Thermal Expansion: Moderate, aiding dimensional stability
- Corrosion Resistance: Limited; not stainless
- Machinability: Fair when annealed, more difficult when hardened
A2 Steel Machining Processing Features
- Air Hardening: Minimizes distortion during quenching
- Deep Hardening: Uniform hardness throughout the cross-section
- Grindability: Moderate; easier than D2 but harder than O1
These properties make A2 steel a solid choice for applications where balance is key – offering better toughness than D2 and better wear resistance than O1. To fully realize these properties, proper heat treatment is essential.
A2 Tool Steel Heat Treatment & Hardening Process
The performance of A2 tool steel is closely tied to how it is heat treated. The process involves several steps:
- Preheating: Gradually heated to 1200–1300°F (649–704°C) to reduce thermal shock
- Austenitizing: Heated to 1725–1800°F (941–982°C) to dissolve carbides and form austenite
- Quenching: Air-cooled to room temperature, which hardens the steel without the cracking risks of water or oil
- Tempering: Reheated to 300–1100°F (149–593°C) to reduce brittleness
This heat treatment process results in high hardness with minimal distortion, making A2 reliable for precision tooling. To tune the balance between hardness and toughness, manufacturers use specific tempering temperatures, which we cover next.
A2 Tool Steel Tempering Chart
Tempering is essential to reduce the brittleness caused by hardening and to fine-tune mechanical performance.
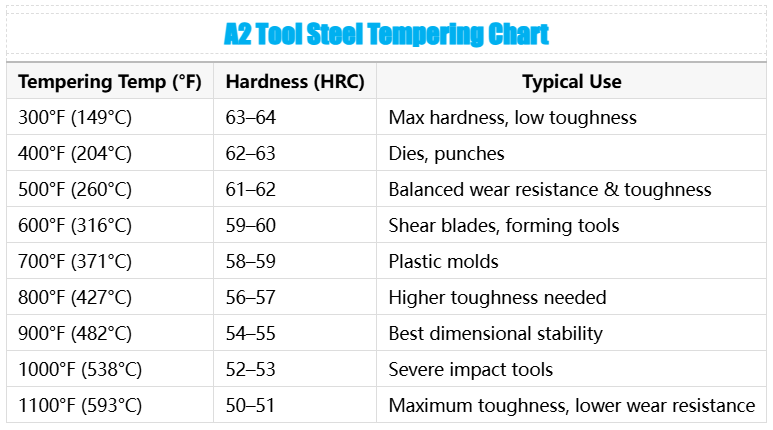
✅ Typical Hardness Range After Tempering: 50–64 HRC
✅ Tempering is often done twice to relieve internal stresses
✅ Recommended tempering range: 300°F to 1100°F (149°C to 593°C)
Multiple tempering cycles (usually two) are recommended to relieve internal stresses and stabilize the structure. Now that we understand how to treat A2 steel, let’s look at how it is categorized and compared internationally.
A2 Tool Steel Equivalent Material Grades
A2 tool steel is standardized under different grade names and equivalent materials across various countries:
- USA (AISI): A2 Steel
- Germany (DIN): 1.2363 / X100CrMoV5 Steel
- UK (BS): BA2 Steel
- Japan (JIS): SKD12 Steel
- China (GB): Cr6WV Steel
- France (AFNOR): Z100CDV5 Steel
- Sweden (ASSAB): XW-10 Steel
Understanding equivalents helps manufacturers and buyers source the correct material globally.
With these grades in mind, let’s explore the real-world applications of A2 steel.
A2 Tool Steel Uses
A2 is a general-purpose tool steel suitable for a wide range of applications:
- Tool & Die Making: Stamping dies, trimming dies, coining dies
- Knives and Cutting Tools: Bushcraft knives, woodworking tools, shear blades
- Cold Forming Tools: Punches, rollers, thread rolling dies
- Plastic Molds: Excellent for wear resistance and dimensional control
- Planer Blades and Chisels: Long-lasting edges with good impact resistance
Its combination of edge retention and toughness makes A2 suitable for both heavy-duty industrial tools and fine custom knives.
A2 Tool Steel Price
The cost of A2 tool steel varies by supplier, form, and treatment:
- Raw Bar/Plate (Annealed): $3.00–$6.00 per pound
- Heat-Treated Tooling: Higher due to processing
- Finished Knives: A2 knives are more affordable than those made from D2 or premium CPM steels
A2 offers good value in terms of performance per dollar, especially for applications requiring dimensional accuracy and durability.
A2 vs D2 vs O1 Tool Steel: What are the Differences
Among the most widely used cold work tool steels, A2, D2, and O1 offer distinct balances of hardness, toughness, wear resistance, and machinability. Each of these steels is engineered to meet specific demands for different applications. Here we will detail the differences between A2, S2, and O1 tool steel:
1. A2 vs D2 vs O1 Properties
Property | A2 Tool Steel | D2 Tool Steel | O1 Tool Steel |
---|---|---|---|
Hardening Method | Air hardened | Air hardened | Oil hardened |
Wear Resistance | Moderate | Very high | Moderate |
Toughness | High | Moderate | High |
Hardness (HRC) | 57–64 | 58–62 | 57–62 |
Dimensional Stability | Excellent | Very good | Fair |
Machinability | Good | Poor | Good |
Grindability | Good | Poor | Excellent |
Edge Retention | Good | Excellent | Fair |
Corrosion Resistance | Low | Moderate (semi-stainless) | Low |
Heat Treat Complexity | Easy | Complex | Moderate |
Cryo Treatment Benefit | Optional | Recommended | Not typical |
Cost | Moderate | High | Low |
2. A2 vs D2 vs O1 Chemical Composition
Element | A2 (%) | D2 (%) | O1 (%) |
---|---|---|---|
Carbon (C) | 0.95–1.05 | 1.40–1.60 | 0.85–1.00 |
Chromium (Cr) | 4.75–5.50 | 11.0–13.0 | 0.40–0.60 |
Molybdenum (Mo) | 0.90–1.40 | 0.70–1.20 | 0.40–0.60 |
Vanadium (V) | 0.15–0.50 | 0.80–1.20 | 0.20 |
Manganese (Mn) | 0.50–1.00 | 0.20–0.60 | 1.00–1.40 |
Silicon (Si) | 0.30–0.50 | 0.10–0.60 | 0.50 |
Iron (Fe) | Balance | Balance | Balance |
3. Hardening Method
A2 and D2 are air-hardening tool steels, meaning they harden when cooled in still air after heat treatment. This reduces the risk of distortion and cracking. O1, on the other hand, is an oil-hardening steel, which requires quenching in oil, leading to a higher chance of dimensional changes or warping during treatment.
4. Wear Resistance
D2 tool steel offers the highest wear resistance among the three, thanks to its high carbon and chromium content. A2 provides moderate wear resistance, making it suitable for general-purpose tools. O1 has lower wear resistance and is more suited for light-duty or short-run applications where extreme wear properties are not critical.
5. Toughness
In terms of toughness, O1 and A2 are better choices. A2 has higher toughness than D2 and maintains good impact resistance. O1 also offers good toughness, especially for an oil-hardening steel. D2, while hard and wear-resistant, is less tough and more brittle, making it more prone to chipping under impact or shock loads.
6. Dimensional Stability
A2 tool steel is known for its excellent dimensional stability during heat treatment, making it ideal for precision tools and dies. D2 also maintains good dimensional control, though not as precisely as A2. O1, by contrast, is more prone to dimensional changes due to its oil quenching process, which can cause distortion if not carefully managed.
7. Machinability
O1 tool steel is the easiest to machine, which makes it popular for small shops and prototype work. A2 is also relatively easy to machine, especially compared to D2. D2 is difficult to machine due to its high hardness and carbide content, and it often requires specialized tooling and slower cutting speeds.
8. Heat Treatment Complexity
A2 is the easiest to heat treat, thanks to its air-hardening nature and low risk of distortion. O1 is moderately easy but requires attention during oil quenching to avoid warping. D2 is the most complex to heat treat correctly, requiring precise temperature control and potentially cryogenic treatment to maximize performance.
9. Price
In terms of cost, O1 is generally the most affordable, followed by A2, which is moderately priced. D2 is typically the most expensive due to its superior wear resistance and alloy content.
10. Corrosion Resistance
While none of these steels are stainless, D2 offers slightly better corrosion resistance because of its high chromium content (around 12%), which gives it some semi-stainless properties. A2 and O1 have lower corrosion resistance and require oiling or coating to prevent rusting.
11. Edge Retention
D2 has excellent edge retention due to its high hardness and wear resistance. This makes it ideal for cutting tools that need to stay sharp for long periods. A2 has good edge retention, though not as long-lasting as D2. O1 has decent edge retention, but it wears faster under heavy or abrasive use.
12. Grindability
O1 is the easiest to grind and finish, making it a favorite for knifemakers and machine shops. A2 is a bit tougher but still grinds well. D2, however, is more difficult to grind due to its high wear resistance and carbide formation, which can rapidly wear down grinding wheels.
13. Working Temperature Range
A2 and D2 can both withstand higher working temperatures than O1 due to their alloy content and air-hardening nature. O1 is more sensitive to heat and is better suited to lower-temperature applications.
14. Carbide Structure
D2 has a high volume of chromium carbides, which gives it outstanding wear resistance but also contributes to brittleness and chipping. A2 has a moderate carbide structure, resulting in a good balance of toughness and wear resistance. O1 has fewer carbides, which helps with toughness and machinability but reduces wear resistance.
15. Finish Quality
O1 and A2 can achieve a very fine surface finish when ground properly. D2, due to its high carbide content, tends to have a grainier finish and is more challenging to polish to a mirror-like surface without special techniques.
16. Availability & Use in Knives
All three steels are used in knife making, but for different reasons:
- D2 is preferred for high-end, long-lasting cutting performance, particularly for tactical and industrial knives.
- A2 is popular among hard-use bushcraft and survival knives due to its toughness.
- O1 is widely used in custom knives, woodworking tools, and beginner knife projects because of its ease of shaping and heat treating.
17. Suitability for Cryogenic Treatment
D2 benefits the most from cryogenic treatment (deep freezing after quenching), which helps convert retained austenite to martensite and improves wear resistance. A2 can also benefit from cryo-treatment to a lesser extent. O1 typically does not require or significantly benefit from it.
18. Response to Surface Treatments
A2 and D2 respond well to coatings and surface treatments, like nitriding or PVD (Physical Vapor Deposition), which can enhance wear and corrosion resistance. O1 can be coated but doesn’t benefit as much due to its lower alloy content.
19. Typical Tool Life
D2 offers the longest tool life in high-wear environments, especially in stamping, blanking, and high-volume production. A2 provides very good tool life with added toughness for impact. O1 has shorter tool life in abrasive applications but is sufficient for low-volume or light-duty tools.
FAQs: A2 Tool Steel
Q: Is A2 tool steel stainless?
No, A2 is not stainless. It has about 5% chromium, which aids hardness and wear resistance but does not prevent rust.
Q: What hardness can A2 reach?
After heat treatment, A2 can reach between 57–62 HRC.
Q: Can A2 be used for knives?
Yes, it’s popular for fixed blades due to its edge retention and toughness.
Q: How does A2 compare to O1?
A2 is tougher and more wear-resistant, while O1 is easier to sharpen and machine.
Q: Is A2 easy to heat treat?
Yes, its air-hardening nature makes it easier to heat treat with less risk of cracking or warping.
Q: Why use A2 for chisels or planes?
Its edge retention and impact resistance make it ideal for tools that undergo repeated stress.