Aluminum alloys play a crucial role in various manufacturing industries due to their excellent strength to weight ratio and corrosion resistance properties. When choosing the right alloy for an application, it is important to understand the composition and resulting mechanical characteristics of common options. In this article, we will explore three widely used cast aluminum alloys, and compare their key differences between A356.0, A357.0, and 319.0 Aluminum.
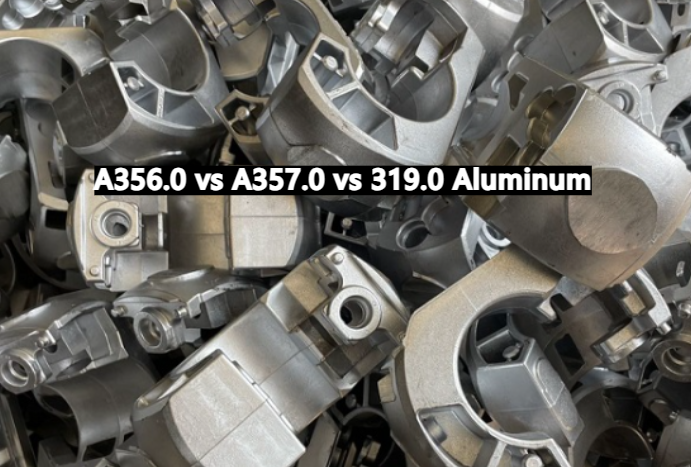
What Is A356.0 Aluminum?
A356.0 aluminum is a designation for a particular aluminum alloy. A356.0 aluminum alloy contains 7-9% silicon, 0.15-1.0% copper, 0.25-0.6% magnesium, and the remainder is aluminum. This composition gives it useful mechanical properties.
Properties: It has good corrosion resistance, machinability, casting ability and moderate strength. Strength levels are lower than other alloys like 6061 or 7075 aluminum.
Applications: Common uses include poured parts for hardware, automotive/truck components, equipment housings, gear housing, pumps, valves etc. It works well for parts that require casting but don’t need extreme durability or strength.
Machinability: It machines well and has good surface finish when machined. Chips break easily during turning or milling operations.
Corrosion Resistance: Has improved resistance to corrosion compared to lower alloyed grades, especially in maritime environments. Not as corrosion resistant as 5xxx or 6xxx series alloys.
Welding: Not generally recommended for welding since welding can reduce mechanical properties. If needed, gas tungsten arc welding works best.
What Is A357.0 Aluminum?
A357.0 aluminum is a wrought aluminum alloy that has a similar composition to A356 aluminum, but is produced in a wrought form rather than as a casting. It has a composition of 7-9% silicon, 0.15-1% copper, 0.25-0.6% magnesium, and the balance aluminum. This is nearly identical to A356 aluminum alloy.
Properties: It has slightly higher strength than A356 due to being a wrought product. Strength ranges between 30-40 ksi (210-280 MPa). It has good machinability, corrosion resistance, and workability.
Applications: Common uses include brake lines, hydraulic tubing, bicycle frames, automotive drive shafts, hand tools, etc. Any application where A356 is used but a wrought product is required.
Processing: A357.0 can be cold worked (bent or formed) due to its wrought production. It can be cold drawn, spun, or formed. It is not as formable as softer grades like 1050 or 3003 aluminum.
Corrosion Resistance: Has improved corrosion resistance compared to lower alloyed aluminum alloys. However, not as corrosion resistant as 5xxx or 6xxx series alloys.
Welding/Brazing: Can be welded or brazed, but will lose mechanical properties in the heat affected zone. Mig or Tig welding works best.
What Is 319.0 Aluminum?
319.0 aluminum is a casting alloy that is part of the 3xx.x series aluminum alloys. It contains 6-9% silicon, 3-5% copper, 0.5-1.5% magnesium, and the remainder aluminum. The copper provides strength while silicon and magnesium enhance corrosion resistance.
Properties: It has higher strength than A356 alloy but lower than 319 aluminum brazing sheet. Tensile strength is around 35 ksi (240 MPa). Good corrosion resistance, machinability and castability.
Applications: Common uses include components for trucks, marine applications, materials handling equipment, irrigation components etc. Used when higher strength than A356 is required.
Machining: Machines easily with continuous chips. Can be drilled, milled, turned without issues. Good surface finish after machining.
Welding: Can be welded but properties reduce in heat affected zone. Filler rods are available for mig welding. Brazing is also possible.
Corrosion Resistance: Has excellent corrosion resistance, similar to 5xxx alloys due to magnesium/silicon content. Used for marine applications or where corrosion is a concern.
Aluminum A356.0 vs A357.0 vs 319.0, What’s the Difference?
A356.0
Form: Casting
Composition: 7-9% Si, 0.15-1% Cu, 0.25-0.6% Mg, Al
Properties: Moderate strength, excellent castability and machinability
Applications: Hardware, pumps, valves – where casting is required
A357.0
Form: Wrought product
Composition: Same as A356.0
Properties: Slightly higher strength than A356.0 due to working
Applications: Automotive shafts, bicycle frames – where wrought form is needed
319.0
Form: Casting
Composition: 6-9% Si, 3-5% Cu, 0.5-1.5% Mg, Al
Properties: Higher strength than A356.0, good corrosion resistance
Applications: Truck components, irrigation, marine – where higher strength is required
Key differences:
A356.0 is for castings, A357.0 is the wrought form for similar applications
319.0 has a different composition – more Cu provides higher strength
319.0 is heat treatable, A356.0 and A357.0 are not
319.0 has excellent corrosion resistance, on par with 5xxx alloys
A356.0 is most commonly used, 319.0 for higher strength applications