The aerospace industry has always been at the forefront of innovation and technology. The quest for efficiency, performance, and safety drives continuous improvements in materials and engineering. One of the materials that has played a pivotal role in this progress is A356 aluminum. A356 aluminum alloys have found their way into an array of aerospace components, contributing to safer and more efficient aircraft. Today, we talk about the applications of A356 aluminum in the aerospace sector.
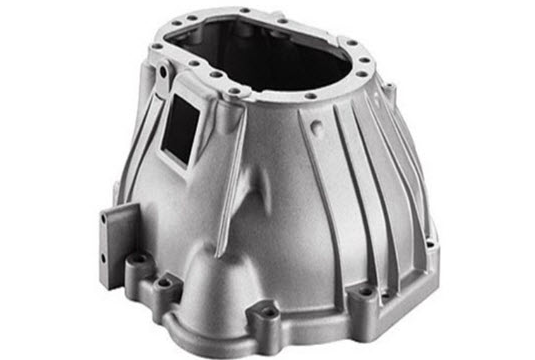
The Advantages of A356 Aluminum
A356 aluminum alloy is an aluminum-silicon-copper-based alloy known for its exceptional combination of properties that make it a prime candidate for aerospace applications. These properties include:
- Lightweight: A356 aluminum is renowned for its low density, making it an excellent choice for applications where weight reduction is paramount. In aerospace, lighter components lead to increased fuel efficiency and payload capacity.
- High Strength: This aluminum alloy boasts impressive strength, especially when subjected to heat treatment. High strength is crucial for structural components that must endure heavy loads and forces during flight.
- Corrosion Resistance: Aerospace components are exposed to a variety of environmental conditions, including moisture and high-altitude atmospheric conditions. A356’s corrosion resistance ensures the longevity of these components.
- Thermal Stability: The ability of A356 aluminum to maintain its integrity at extreme temperatures makes it ideal for aerospace use, where components may experience both high-temperature and low-temperature extremes.
Aerospace Applications of A356 Aluminum
A356 aluminum is an incredibly versatile material, finding its way into numerous aerospace components. Here are some key applications:
- Aircraft Structures: The lightweight yet high-strength nature of A356 aluminum makes it a suitable choice for aircraft structural components. Wing and fuselage components, landing gear, and engine parts are just a few examples where A356 aluminum is employed to enhance structural integrity.
- Aircraft Wheels: Aircraft wheels and brakes require materials that can withstand tremendous forces and temperature variations. A356 aluminum alloys provide the necessary strength and thermal stability for these critical components.
- Aircraft Interiors: Beyond structural components, A356 aluminum also finds applications in the interior of aircraft, such as in seating frames, cabin walls, and other non-structural elements, thanks to its lightweight and corrosion-resistant properties.
- Spacecraft Components: A356 aluminum’s ability to withstand the rigors of space environments has made it a valuable material in the construction of spacecraft and satellite components.
A356 Aluminum: Meeting Rigorous Standards
A356 aluminum alloys are highly regarded in the aerospace industry not only for their exceptional properties but also for their ability to meet and exceed stringent standards and regulations. Aerospace components must adhere to rigorous quality and safety standards to ensure the reliability and durability of aircraft. A356 aluminum alloys are prized for their consistent performance and reliability, making them a dependable choice for aerospace engineers and manufacturers.
Innovations in Manufacturing and Processing
The aerospace industry’s continuous drive for innovation has led to advancements in the manufacturing and processing of A356 aluminum. For instance, cutting-edge casting technologies, including precision investment casting and advanced sand casting methods, are employed to produce intricate and complex components with a high degree of accuracy. These innovations have allowed aerospace engineers to explore new designs that maximize the material’s properties while maintaining strict weight and performance requirements.
Challenges and Solutions
Despite its many advantages, A356 aluminum does come with certain challenges. One of the primary challenges is the need for careful heat treatment to optimize its mechanical properties. The heat treatment process, particularly the T6 treatment, is critical to achieving the desired combination of strength and ductility. Manufacturers must exercise precision and control during heat treatment to ensure consistent results.
Moreover, while A356 aluminum offers excellent corrosion resistance, components that operate in aggressive environments or are exposed to extreme conditions require additional surface treatments or coatings. The aerospace industry addresses this challenge by implementing advanced surface engineering techniques to enhance the durability of A356 aluminum components.
Environmental Considerations
In recent years, the aerospace industry has been placing greater emphasis on environmental sustainability. Fuel efficiency and reduced emissions are at the forefront of the aerospace industry’s concerns. A356 aluminum’s lightweight properties play a pivotal role in this regard, contributing to the development of fuel-efficient aircraft that produce fewer emissions. As the aerospace sector strives to achieve more sustainable practices, A356 aluminum remains a valuable asset.