The choice of aluminum alloy can make a significant difference in product performance, durability, and cost-effectiveness. Three particularly noteworthy alloys – A357, 6061, and F357 – have emerged as crucial players in various industrial applications, each bringing its unique set of characteristics and advantages to the table. In this comprehensive analysis, we’ll explore the differences between A357, 6061, and F357 aluminum alloy, examining their chemical compositions, mechanical properties, heat treatment responses, and typical applications.
A357 Aluminum vs 6061 vs F357, Which Should You Choose?
While these alloys share aluminum as their primary component, their distinct chemical compositions, mechanical properties, and processing requirements create specialized use cases that can significantly impact project outcomes. From aerospace components to automotive parts, and from structural applications to precision instruments, understanding the nuanced differences between these alloys becomes essential for engineers, designers, and manufacturers aiming to optimize their material selection. By understanding these differences, professionals can make more informed decisions about which alloy best suits their specific requirements, ultimately leading to better-performing and more cost-effective products.
What’s A357 Aluminum?
A357 aluminum is a high-strength, heat-treatable casting alloy that belongs to the aluminum-silicon-magnesium (Al-Si-Mg) family. It’s commonly used in aerospace, automotive, and other industries requiring lightweight, durable, and corrosion-resistant components.
Key Characteristics of A357 Aluminum Alloy
Composition: Primarily aluminum, with silicon (6.5-7.5%), magnesium (0.45-0.6%), and trace amounts of other elements like iron, copper, and titanium.
Heat Treatment: Can be heat treated to improve mechanical properties (typically T6 temper).
Strength: High tensile strength and good fatigue resistance.
Corrosion Resistance: Excellent resistance to corrosion, especially after heat treatment.
Castability: Good fluidity and low shrinkage make it suitable for precision casting.
Common Applications of Aluminum A357
Aerospace components (e.g., structural parts, engine components).
Automotive parts (e.g., wheels, engine blocks).
High-performance machinery and equipment.
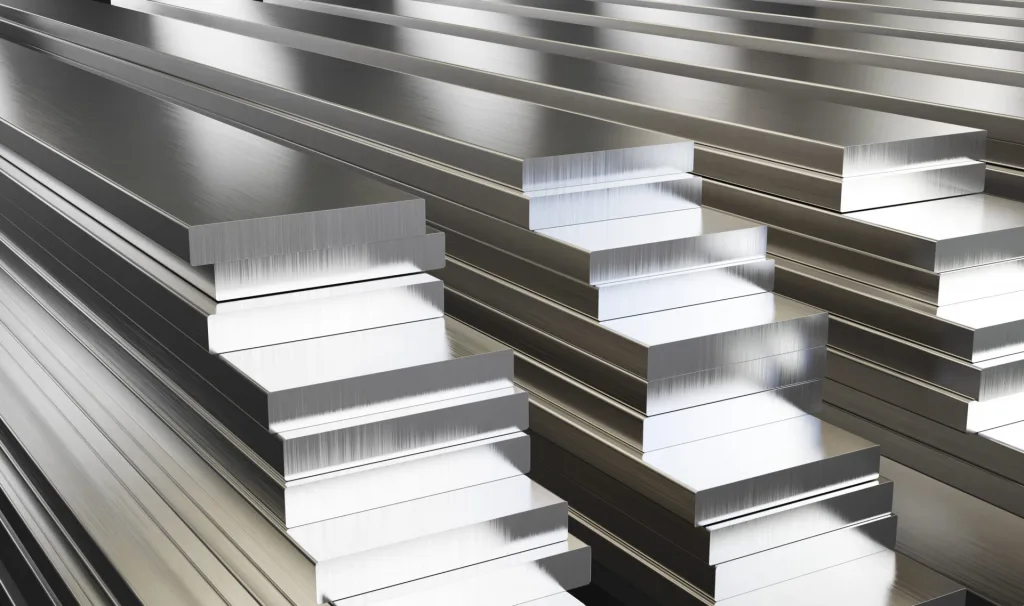
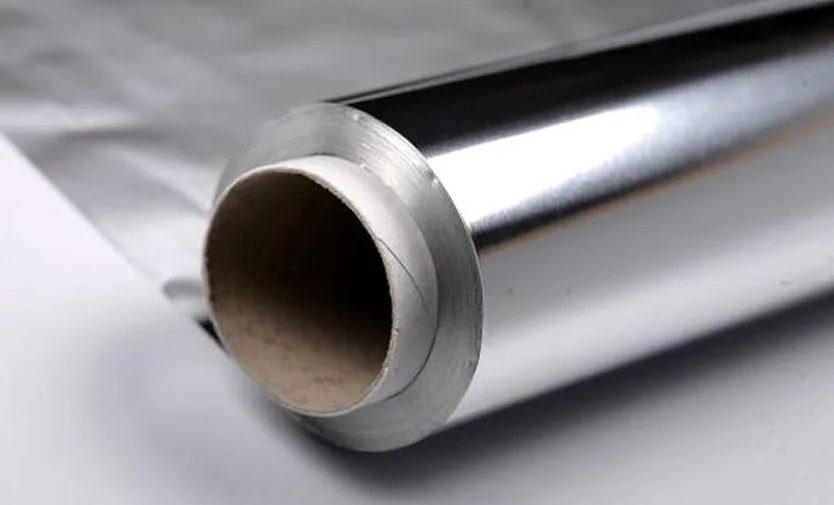
What’s 6061 Aluminum?
6061 aluminum is one of the most commonly used aluminum alloys, known for its versatility, strength, and good corrosion resistance. It belongs to the 6xxx series, which means it primarily contains aluminum, magnesium, and silicon.
Key Characteristics of 6061 Aluminum Alloy
Composition: About 97.9% aluminum, 0.8–1.2% magnesium, 0.4–0.8% silicon, with small amounts of copper, chromium, iron, and other elements.
Heat Treatment: Can be heat treated to improve mechanical properties, commonly found in the T6 temper (solution heat-treated and artificially aged).
Strength: Medium to high strength, lower than 7075 aluminum but higher than 5052.
Machinability: Excellent machinability, making it suitable for milling, drilling, and turning.
Weldability: One of the best aluminum alloys for welding, especially using TIG and MIG methods.
Corrosion Resistance: Good resistance to corrosion, especially when anodized.
Formability: Easily extruded or rolled into sheets, plates, and various shapes.
Common Applications of Aluminum 6061
Aerospace: Aircraft fittings and couplings.
Automotive: Structural components and frames.
Construction: Structural beams and supports.
Marine: Boat hulls and other watercraft components.
Recreational Equipment: Bicycles and other sporting goods.
What’s F357 Aluminum?
F357 aluminum is a high-strength, heat-treatable casting alloy similar to A357 aluminum, but with improved properties for specific applications. It belongs to the aluminum-silicon-magnesium (Al-Si-Mg) family, like A357, and is known for its excellent mechanical properties and corrosion resistance.
Key Characteristics of F357 Aluminum Alloy
Composition: Primarily aluminum, with around 6.5–7.5% silicon, 0.45–0.6% magnesium, and trace amounts of titanium, iron, and other elements.
Heat Treatment: Often heat-treated to the T6 temper to enhance mechanical properties.
Strength: Comparable to A357 but offers slightly better fatigue resistance and tensile strength due to more controlled impurities.
Corrosion Resistance: Very good, especially when heat-treated.
Castability: Excellent fluidity and resistance to hot tearing, making it suitable for complex and thin-walled castings.
Common Applications of Aluminum F357
Aerospace: Structural and engine components.
Automotive: Performance and racing parts.
Defense: High-performance weapon and vehicle components.
Medical Devices: Prosthetics and implants.
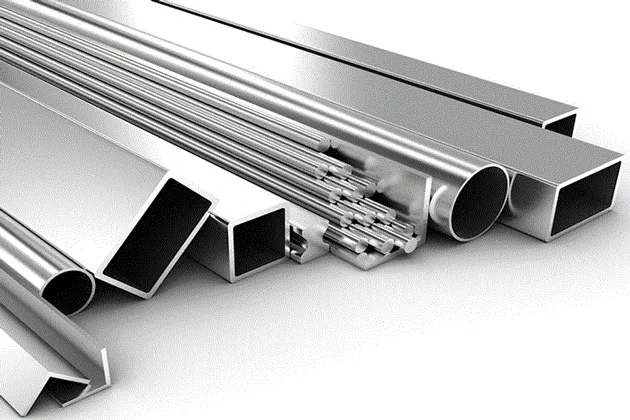
A357 vs 6061 Aluminum: What’s the Difference?
Both A357 and 6061 aluminum alloys are widely used but serve different purposes due to their unique properties and applications. Here’s a quick comparison.
Composition:
A357 aluminum contains around 6.5–7.5% silicon and 0.45–0.6% magnesium, with small amounts of titanium and iron. It’s designed for casting applications.
6061 aluminum is about 97.9% aluminum with 0.8–1.2% magnesium and 0.4–0.8% silicon. It also contains copper and chromium, making it great for extrusions and forgings.
Manufacturing Process:
A357 is primarily used for casting, including sand and investment casting methods. It’s suitable for producing complex shapes.
6061 is commonly used for extruding, rolling, and forging into bars, plates, and pipes, making it versatile for structural applications.
Mechanical Properties:
A357 in the T6 temper has a tensile strength of 330–380 MPa and a yield strength of 200–250 MPa. It’s strong but has limited elongation at break (3–5%).
6061 T6 has a tensile strength of around 310 MPa and a yield strength of 276 MPa. It’s slightly less strong than A357 but offers much better elongation (12–17%).
Corrosion Resistance:
Both alloys offer good corrosion resistance, but 6061 has a slight advantage because of its controlled composition. It is often anodized for extra protection, especially in marine environments.
Machinability and Weldability:
A357 has moderate machinability but may suffer from casting porosity, making precise machining tricky. Weldability is generally good but can vary with casting quality.
6061 excels in machinability and weldability, especially with TIG and MIG welding. It’s easy to work with and commonly used for fabricated parts.
Applications:
A357 is preferred for casting aerospace and automotive parts, like engine components and machinery parts. It’s ideal when high strength and fatigue resistance are needed.
6061 is used in structural applications, bike frames, pipelines, and marine parts. Its excellent machinability and weldability make it versatile for various manufacturing needs.
A357 vs F357 Aluminum: What’s the Difference?
A357 and F357 are both high-strength aluminum casting alloys belonging to the Al-Si-Mg family. They are quite similar but differ mainly in impurity control and performance. Here’s a breakdown of the key differences.
Composition:
Both alloys have a similar composition, with around 6.5–7.5% silicon and 0.45–0.6% magnesium. However, F357 has more stringent controls on impurities, especially iron and other trace elements. This results in better consistency and performance compared to A357.
Purity and Quality Control:
F357 is essentially an improved version of A357, with tighter impurity limits. This higher purity level reduces the risk of casting defects, such as porosity and inclusions, making F357 more reliable in critical applications.
Mechanical Properties:
Both alloys offer similar mechanical properties when heat-treated to T6. However, F357 typically has slightly better fatigue resistance and tensile strength due to its controlled composition. This makes it more suitable for high-stress applications.
Corrosion Resistance:
Both alloys provide good corrosion resistance, but F357’s improved purity can enhance its resistance in certain environments. This makes F357 more suitable for applications exposed to harsh conditions.
Castability and Processing:
Both alloys have excellent castability, but F357’s improved quality control reduces the likelihood of casting defects. This makes it a better choice for precision cast parts, especially in aerospace and defense applications.
Applications:
- A357: Commonly used for automotive and aerospace components where casting complexity and strength are essential.
- F357: Preferred for aerospace, military, and medical applications that demand high performance, consistency, and fatigue resistance.
A357 vs 6061 vs F357 Aluminium: Which Is the Best?
A357, 6061, and F357 aluminum alloys each excel in different applications due to their unique properties. A357 and F357 are primarily casting alloys, with F357 being a purer, higher-quality version of A357, offering improved fatigue resistance and consistency, making it ideal for aerospace and critical applications. In contrast, 6061 is a versatile wrought alloy, known for its excellent machinability, weldability, and corrosion resistance, commonly used in structural and general fabrication. While A357 and F357 are great for complex cast shapes, 6061 is preferred for extrusions, plates, and welded structures. If you need high-strength castings with low impurities, choose F357. For versatile machining and fabrication, go with 6061. A357 is suitable when cost is a concern, and absolute purity is less critical.
Property | A357 (T6) | 6061 (T6) | F357 (T6) |
---|---|---|---|
Tensile Strength | 330–380 MPa | 310 MPa | 340–390 MPa |
Yield Strength | 200–250 MPa | 276 MPa | 240–270 MPa |
Elongation at Break | 3–5% | 12–17% | 4–6% |
Hardness (Brinell) | ~80 | 95 | ~85 |
Density | 2.68 g/cm³ | 2.70 g/cm³ | 2.68 g/cm³ |
Corrosion Resistance | Good | Very Good | Excellent |
Machinability | Moderate | Excellent | Moderate |
Weldability | Good | Excellent | Good |
Best Use | Cast components | Structural | High-quality casting |