Aluminum alloys have long been a crucial material in various industries, from automotive and aerospace to manufacturing and construction. Among the many aluminum alloys available, A357 stands out as a highly versatile and sought-after option, prized for its exceptional mechanical properties and broad range of applications. In this comprehensive article, we will delve into the A357 aluminum composition, properties, and uses, as well as explore the key differences between A357, A356 and A357-T6.
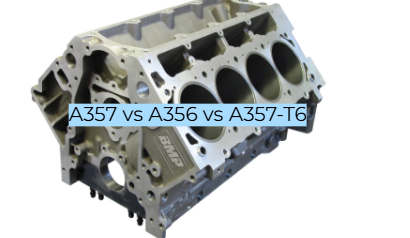
What’s Aluminum A357?
A357 is a cast aluminum alloy that is highly regarded for its exceptional mechanical properties, particularly after undergoing heat treatment. This alloy is composed of several key elements, including 6.5 to 7.5% silicon, 0.04 to 0.07% beryllium, 0.2% iron, 0.2% copper, 0.4 to 0.7% magnesium, 0.04 to 0.2% titanium, 0.1% zinc, and 0.1% manganese. The specific composition of A357 contributes to its strength, corrosion resistance, and pressure tightness, making it suitable for a wide range of applications.
The Properties of A357 Alumimum
One of the standout features of A357 is its strength, especially when heat treated. This process significantly enhances the alloy’s mechanical properties, allowing it to become one of the strongest sand-cast aluminum alloys available. As a result, A357 is often used in situations where high strength is essential, such as in structural components and machinery. Additionally, the alloy’s high corrosion resistance makes it ideal for use in environments where exposure to moisture or chemicals is a concern.
The Applications of A357 Aluminum Alloy
A357 is commonly utilized in the manufacturing of various components, including structural parts, machine components, impellers, housings, pump and valve components, tools, frames, and brackets. These applications benefit from the alloy’s combination of strength, corrosion resistance, and ability to maintain pressure tightness, making it a preferred choice in industries such as automotive, aerospace, and general engineering.
A357 vs A356 Aluminum Alloy, What’s The Difference?
Composition
A356 Aluminum: Typically contains 6.5 to 7.5% silicon, 0.15 to 1.0% copper, 0.25 to 0.6% magnesium, and the remainder is aluminum. It may also contain small amounts of other elements like iron and manganese.
A357 Aluminum: Similar to A356, A357 contains 6.5 to 7.5% silicon, but it has a slightly different composition with 0.04 to 0.07% beryllium, 0.2% iron, 0.2% copper, and 0.4 to 0.7% magnesium. The presence of beryllium is a notable difference that contributes to its properties.
Mechanical Properties
Strength: A357 is generally stronger than A356, especially after heat treatment. A357 is known for being one of the strongest sand-cast aluminum alloys, making it suitable for applications requiring high strength.
Corrosion Resistance: Both alloys exhibit good corrosion resistance, but A357 may have a slight edge due to its specific composition, which enhances its performance in corrosive environments.
Applications
A356 Aluminum: Commonly used for parts that require good castability and moderate strength, such as automotive components, housings, and valves. It is favored for applications where extreme durability is not critical.
A357 Aluminum: Used in applications where high strength and pressure tightness are essential, such as structural components, machine parts, impellers, and housings. Its superior strength makes it ideal for more demanding applications.
Property | A356 Aluminum | A357 Aluminum |
Silicon Content | 6.5 to 7.5% | 6.5 to 7.5% |
Beryllium Content | 0.04 to 0.07% | |
Copper Content | 0.15 to 1.0% | 0.2% |
Iron Content | 0.2% | 0.2% |
Magnesium Content | 0.25 to 0.6% | 0.4 to 0.7% |
Titanium Content | 0.04 to 0.2% | |
Zinc Content | 0.1% | |
Manganese Content | 0.1% | |
Heat Treatment | Not typically heat treated | Typically heat treated |
Strength | Moderate strength | High strength, especially after heat treatment |
Corrosion Resistance | Good | High |
Applications | Automotive components, housings, valves | Structural parts, machine components, impellers, housings |
Casting Method | Sand casting | Sand casting |
What Is The Difference Between A357-T6 & A357.0?
- Heat Treatment
A357-T6: This alloy undergoes a specific heat treatment process known as T6, which involves solution heat treatment followed by aging. This process significantly enhances its mechanical properties, particularly its strength.
A357.0: This designation typically refers to the alloy in its as-cast state without any heat treatment. As a result, A357.0 will have lower strength compared to A357-T6. - Mechanical Properties
Tensile Strength: A357-T6 exhibits higher ultimate tensile strength (UTS) compared to A357.0. For instance, A357-T6 can achieve a UTS of around 350 MPa, while A357.0 has a lower UTS of approximately 270 MPa.
Yield Strength: Similarly, the yield strength of A357-T6 is significantly higher (around 270 MPa) compared to A357.0, which has a yield strength of about 200 MPa.
Elongation: A357.0 generally has better elongation properties (around 6.0%) compared to A357-T6 (around 3.4%), indicating that A357.0 may be more ductile in its as-cast state. - Applications
A357-T6: Due to its enhanced strength and durability after heat treatment, A357-T6 is often used in applications requiring high strength and resistance to deformation, such as in aerospace and automotive components.
A357.0: This alloy is typically used in applications where the mechanical demands are lower, and the benefits of heat treatment are not necessary.