Aluminum alloys ADC10 and ADC12 are two of the most commonly used die-casting alloys for producing structural components and housings. Both alloys belong to the AA380 aluminum alloy series but have small variations in composition that result in meaningful differences in properties and applications. As these alloys are frequently employed across industries, it is important to understand how they differ and when to select one over the other. This article provides an overview of the key difference between ADC10 and ADC12 (A380) aluminum.
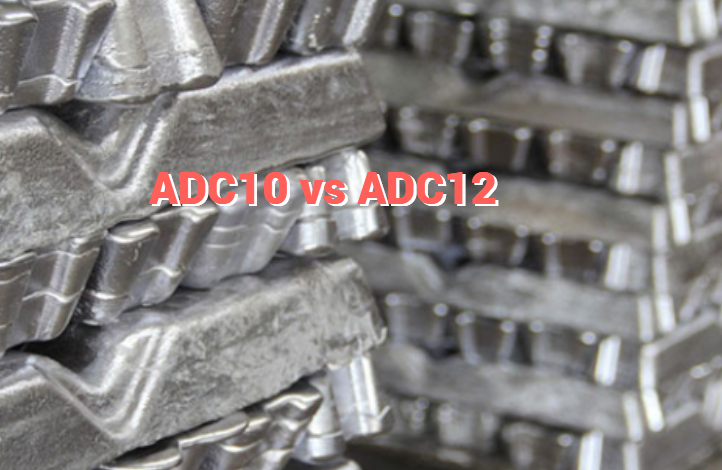
What’s ADC10 Aluminum?
ADC10 aluminum is an aluminum alloy commonly used for die casting applications.ADC10 is equivalent to aluminum alloy A380, with typical composition of 86-91% aluminum, 7-12% zinc, 1-3% copper and 0.5-1.5% silicon.It has excellent castability due to good fluidity and low melting point. This allows it to smoothly fill thin-walled or complex dies. ADC10 aluminum alloy has high strength and stiffness even after solidification, making it suitable for load-bearing die cast components.
The Advantages Of ADC10 Aluminum Alloy
-Good corrosion resistance: ADC10 has excellent corrosion resistance even in marine environments. This is due to the protective aluminum oxide layer that forms on its surface.
-Lightweight: Aluminum ADC10 is much lighter than steel or cast iron. This helps reduce weight and improves energy efficiency in applications.
-High strength-to-weight ratio: It provides good mechanical strength while being lighter than other alloys. This makes it suitable for structural parts.
-Easy to machine and form: ADC10 aluminum alloy can be readily cast, rolled, pressed or machined into complex shapes. It offers good formability.
-Good thermal conductivity: It dissipates heat efficiently thus making it suitable for applications involving heat transfer.
-Recyclable: ADC10 aluminum can be easily recycled, lowering material costs over the long run compared to other alloys.
-Durability: It has high tolerance to wear, impact and cyclic stresses. Parts made from ADC10 last longer.
-Wider service temperature range: ADC10 maintains properties over a wider temperature range from -50°C to 150°C.
Cost effectiveness: Low raw material and production costs due to lighter weight, good castability and formability.
-Low maintenance: Minimal corrosion means less coating or painting is needed for protection.
-Sustainable: Being light and recyclable, ADC10 allows more sustainable construction and transport applications.
The Applications Of Aluminum ADC10
Automotive is one of the largest application areas for ADC10 aluminum due to its strength, formability and corrosion resistance properties. It is used extensively to manufacture powertrain components like gearboxes, engine blocks and cylinder heads. ADC10 is also commonly used for suspension parts, brake components and wheels as it helps reduce the overall vehicle weight.
In the transportation industry, ADC10 aluminum finds widespread use in rail, marine and truck applications. It is regularly employed to fabricate train and subway carriage bodies. Its high strength to weight ratio and corrosion resistant properties make it suitable for trailer frames and truck bodies. In the marine sector, ADC10 aluminum is utilized for outboard motor components, propellers and boat hardware that require durability in harsh marine environments.
Industrial machinery relies heavily on ADC10 aluminum for various structural and functional parts. Its heat dissipation ability and machinability allow precise manufacturing of industrial equipment housing, pumps, conveyor parts, compressors and industrial cooling fan casings. It is an ideal material for plant equipment like pipes, valves, tanks and molds due to weldability, rigidity and minimal maintenance needs.
Building and construction sector exploits the formability and workability of ADC10 aluminum for architectural cladding, window and door profiles, poles and panels. Its corrosion resistance facilitates usage near coastal regions and substitutes for galvanized steel. ADC10 aluminum structural components help reduce the total weight of buildings and bridges.
The electrical and electronics industries also employ ADC10 aluminum extensively for electronic enclosures, computer hardware, telephone components and circuit boards. It offers electromagnetic shielding with customizable aesthetics and rigidity for protecting delicate circuitry. Additional applications of ADC10 aluminum include household appliances, infrastructure, aerospace, medical devices and renewable energy equipment where its physical properties provide technical and economic advantages.
What’s ADC12 Aluminum?
ADC12 aluminum is another commonly used die-casting aluminum alloy. The “ADC12” designation refers to the aluminum alloy composition AA380.2. It contains 8.5-11% zinc, 1-3% copper, 0.5-1.5% silicon, and the remainder aluminum. ADC12 has slightly higher zinc content than ADC10 alloy, which increases its strength. However, the composition is still very similar to ADC10 alloy overall. Both alloys belong to the hypoeutectic AA3xx.x series. ADC12 alloy offers better castability and fluidity compared to ADC10 due to the higher zinc content. It has a lower melting point.
The Advantages Of ADC12 Aluminum Alloy
-Higher strength – With increased zinc content, ADC12 provides greater ultimate tensile strength, hardness and fatigue resistance compared to ADC10.
-Good castability – Contains a higher percentage of zinc which lowers the melting point, improving fluidity during casting filling of complex parts.
-Higher corrosion resistance – The thin aluminum oxide layer protects better in harsh environments due to increased alloying from zinc.
-Machinability – Similar to ADC10, ADC12 can be easily machined, milled, drilled and polished to tight tolerances.
-Heat resistance – Retains mechanical properties at higher operating temperatures ranging from -60°C to 150°C.
-Durability – Resists cracking and failure under cyclic loads or vibrations better than lower strength alloys.
-Lightweight – Though stronger, density remains almost the same as ADC10 at around 2.8 g/cm3, much less than steel.
-Recyclability – Like other aluminum alloys, ADC12 is fully recyclable without loss of properties.
-Cost effectiveness – Combining strength with production via die casting outweighs cost of other high-strength materials.
-Sustainability – Less energy intensive processing and recycling improves environmental profile over alternatives.
-Versatility – Can replace steel and cast iron in applications where weight savings and corrosion resistance are critical.
The Applications Of ADC12 Aluminum Alloy
One of the major use of ADC12 aluminum alloy is in the automotive industry for demanding powertrain and structural components. The higher strength of ADC12 makes it suitable for manufacturing cylinder heads, transmission casings and differentials that must withstand intensive mechanical loads. It is also used for brake caliper housings, suspension control arms and other chassis members.
In industrial machinery manufacturing, ADC12 aluminum finds application in the fabrication of heavy machinery. Its corrosion resistance and strength allows production of large water pump housings, conveyor frames for ports and material handling equipment. Offshore drilling rig components like derrick legs and platform modules also utilize ADC12 where weight is critical.
The marine sector exploits ADC12 in the development of outboard and inboard marine engines given its capability to perform in saline environments. Propellers, marine gearboxes and drive shafts forming the propulsion system are often made from ADC12. It also finds increasing use in commercial ship building for hull parts and superstructures.
ADC12 aluminum alloy is gaining traction in aerospace applications for selected non-safety critical airframe structures. Being significantly lighter, it serves as an alternative to steel in some landing gear components and external paneling. Its weldability allows joining of large airframe assemblies.
Other major segments employing ADC12 include construction machinery, wind and tidal energy turbines, infrastructure, electronic hardware manufacturing and white goods industry. The alloy offers an appealing substitute to cast iron and steel alloys in applications requiring high strength, durable performance and weight optimization.
Aluminum ADC12 vs A380 What’s The Difference?
Composition:
ADC12 has a higher zinc content of 8.5-11% compared to 7-12% in ADC10. It also has 1-3% copper.
Mechanical Properties:
ADC12 has higher ultimate tensile strength, hardness and fatigue strength due to increased zinc levels. However, ADC10 has marginally better ductility.
Casting Properties:
ADC12 has better castability and fluidity due to lower melting point from higher zinc content. Fills thin sections and complicated dies more easily.
Corrosion Resistance:
Being a higher alloy content, ADC12 provides a tad improved corrosion protection. But both alloys have excellent corrosion resistance from aluminum oxide layer.
Applications:
ADC12 is used where additional strength is required over ADC10, like marine, pumps etc. ADC10 is sufficient for general structural and housing applications.
Costs:
ADC12 is slightly costlier than ADC10 due to usage of premium alloying elements.
Melting Points:
ADC10 aluminum alloy has a melting point range of 580-620°C (1076-1148°F). ADC12 aluminum alloy, due to its higher zinc content, has a lower melting point range of 550-590°C (1022-1094°F).
Other Properties:
Machinability, density, heat resistance, recyclability are essentially equivalent.
Property | ADC10 | ADC12 |
Composition | 86-91% Al 7-12% Zn 1-3% Cu 0.5-1.5% Si | 8.5-11% Zn 1-3% Cu 0.5-1.5% Si Remainder Al |
Tensile Strength | 260-310 MPa | 310-340 MPa |
Hardness | 80-100 HV | 90-110 HV |
Fatigue Strength | 150-170 MPa | 170-190 MPa |
Ductility | 5-10% | 3-7% |
Melting Point | 580-620°C | 550-590°C |
Fluidity | Good | Better |
Corrosion Resistance | Excellent | Slightly Better |
Applications | General structural, housings | Pumps, marine, off-shore |
Advantages | Lower cost, castability | Higher strength, castability |
Disadvantages | Lower strength | Higher cost |