When it comes to selecting the right aluminum alloy for an engineering application, a crucial step is understanding how individual alloy compositions will impact key properties. Two alloys frequently considered are LM6 and A383. While both are aluminum-based, they differ in ways that influence machining, strength, corrosion resistance, and more. Read our A383 vs LM6 guide, we’re going to talk about the difference between ADC12 and LM6.
What’s Lm6?
An aluminum alloy designation. Like other aluminum alloys (e.g. A383), LM6 would be a numeric code indicating the specific chemical composition of an aluminum alloy. Alloy compositions are standardized.
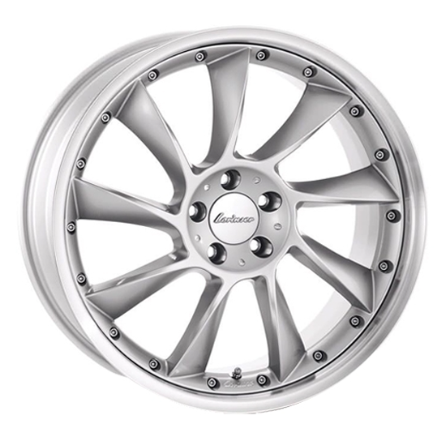
Properties of Lm6?
Lightweight – As an aluminum alloy or cast iron engine component, LM6 would be lighter than comparable steel parts, improving power-to-weight ratio.
Good heat transfer – Aluminum is an excellent heat conductor, allowing LM6 components like cylinder heads or blocks to dissipate heat efficiently.
Durability – Automotive alloys and cast irons are engineered for durability under high loads and temperatures over long periods.
Machinability – Aluminum alloys are easier to machine than steel, reducing component manufacturing costs.
Corrosion resistance – Aluminum forms a protective oxide layer, shielding LM6 from corrosion in many operating environments.
Recyclability – Should LM6 contain aluminum, it can be recycled without loss of material properties, an environmental plus.
Familiar design – If an engine or transmission, LM6 may leverage a pre-existing, proven design for reliability.
Performance potential – Engine variants allow for modification and upgrades to boost horsepower/torque output.
Parts availability – Widespread vehicle use means replacement parts for LM6 components are readily accessible.
Proven technology – Decades of refinement have optimized reliability of aluminum alloy and cast iron compositions.
Applications of Lm6?
M6 alloy opens several application opportunities that take advantage of aluminum’s inherent properties. In the automotive industry, aluminum LM6 could be used to make lightweight engine components like cylinder heads, blocks, and intake manifolds. Reducing weight over cast iron or steel versions improves fuel efficiency and performance. The alloy’s heat conductivity also helps dissipate engine heat. LM6 is also suitable for transmission casings and suspension components seeking lower mass without compromise.
Within transportation more broadly, LM6 provides a durable, formable material for fabricating vehicle chassis, frames, and structural elements. Its strength and formability allows complex shaping while reducing Vehicle mass. Similarly, its strength and recyclability make LM6 well-suited for constructing airframes, internal panels, and engines in the aerospace sector. On the seas, aluminum LM6 resists corrosion better than steel in marine vessel applications like outboard motors.
Beyond mobility, LM6 offers benefits for industrial uses. Its heat management qualities position it for producing machined parts like heat exchangers, sinks, or fins. It can also craft durable yet lightweight housings, enclosures, and load-bearing structures needing resistance to challenging chemical exposures. Infrastructure components like underground piping may utilize LM6’s longevity underground.
What’s A383/ADC12?
Aluminum 383 is an aluminum alloy. Aluminum alloys are typically identified by a numeric designation that indicates their chemical composition. The 383 designation would correspond to a specific aluminum alloy composition.
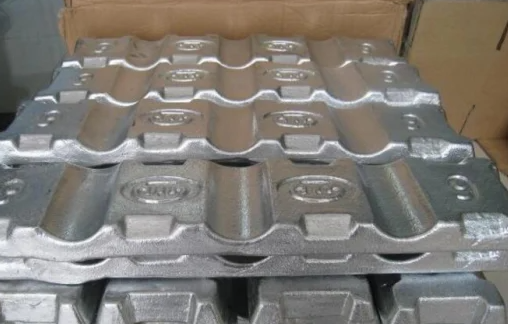
Properties of A383/ADC12?
Lightweight – Aluminum alloys are much lighter than metals like steel, reducing weight.
Corrosion resistance – The aluminum oxide layer that forms on the surface protects underneath metal from corrosion.
Machinability – Aluminum alloys can be readily machined into complex shapes via milling, machining, etc. compared to other metals.
Recyclability – Aluminum alloys are highly recyclable without loss of properties, making them environmentally friendly.
Good strength-to-weight ratio – Provides strength while maintaining lightweight properties.
Applications of A383?
A383 aluminum finds applications in several industries. It is commonly used in automotive components like wheels, drivetrains parts, and engine components where weight savings and corrosion resistance are valued. In aerospace, it is used in aircraft structural elements and engines. Marine applications also employ A383 for hardware and equipment that will be exposed to salty sea environments. General fabrication utilizes it for machined structural pieces, brackets, and housings. A383 is also well-suited for heat exchangers and heat transfer applications due to aluminum’s high thermal conductivity. Its non-corroding attributes make it applicable for piping, tubing, and HVAC ductwork as well.
Differences Between ADC12 & LM6 Aluminum Alloys
ADC12 | LM6 | |
Composition | Aluminum-Copper-Magnesium | Aluminum |
Mechanical Properties | Higher strength | Strength varies based on composition |
Heat Resistance | Higher heat resistance due to copper | Lower heat tolerance |
Machinability | Lower machinability than aluminum-only alloys | Better machinability than copper-containing alloys |
Corrosion Resistance | Lower resistance, more prone to pitting | Better corrosion resistance |
Applications | Heat exchangers, hydraulic applications | Broader applications depending on composition |
Cost | More expensive to produce than simpler alloys | Lower cost aluminum-based alloy |