Aluminum is widely used across multiple industries due to its lightweight nature, corrosion resistance, and versatility. Among the many available aluminum alloys, 3003, 5052, and 6061 are some of the most commonly used. Each of these alloys has distinct properties that make them suitable for different applications.
3003 vs 5052 vs 6061 Aluminum Alloy
Here we will provide a detailed overview of 3003, 5052, and 6061 aluminum alloys, followed by a comparison to highlight their strengths and limitations.
What is Aluminum 3003?
Aluminum 3003 is a non-heat-treatable alloy that belongs to the 3000 series. It is primarily composed of aluminum and manganese, which enhances its corrosion resistance and strength compared to pure aluminum (such as 1100). It is commonly chosen for applications where durability, formability, and resistance to environmental factors are needed. Due to its excellent corrosion resistance, especially in humid conditions, it is widely used in roofing, cooking utensils, storage tanks, and automotive components.
3003 Aluminum Composition
The composition of aluminum 3003 includes manganese as the main alloying element, along with small amounts of other elements that contribute to its mechanical and chemical properties.
Element | Composition (%) |
---|---|
Aluminum (Al) | 97.0 – 98.0 |
Manganese (Mn) | 1.0 – 1.5 |
Copper (Cu) | 0.05 – 0.20 |
Silicon (Si) | ≤ 0.60 |
Iron (Fe) | ≤ 0.70 |
Zinc (Zn) | ≤ 0.10 |
Other elements | ≤ 0.15 |
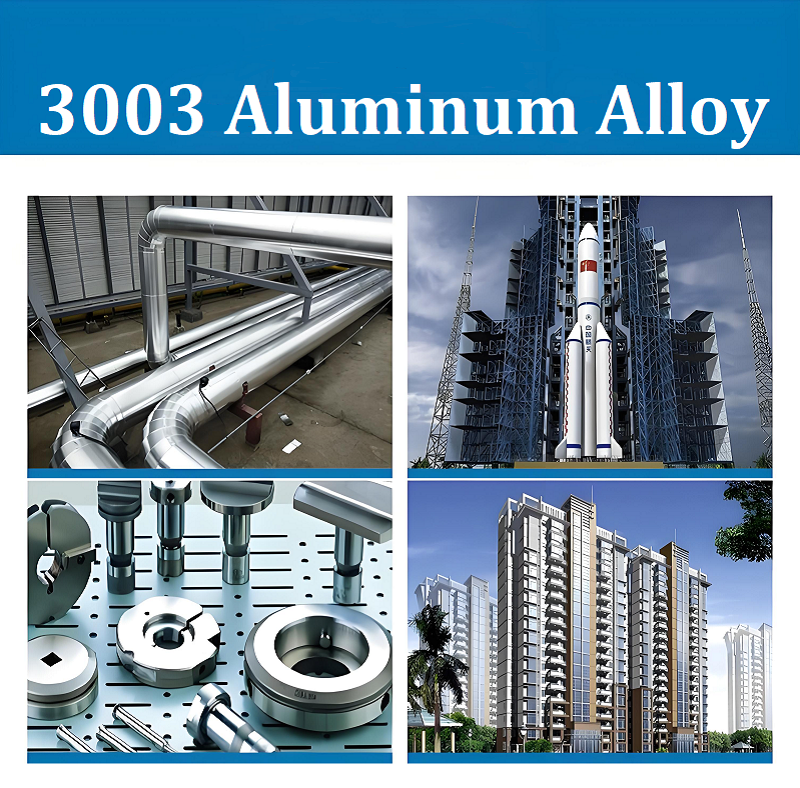
3003 Aluminum Properties
Physical Properties
- Density: 2.73 g/cm³
- Melting Point: ~643–654°C
- Thermal Conductivity: 193 W/m·K
- Electrical Conductivity: 40–50% IACS
- Electrical Resistivity: 0.034 mΩ·m
- Poisson’s Ratio: 0.33
- Elastic Modulus: 68.9 GPa
- Shear Modulus: 25 GPa
Mechanical Properties
The mechanical properties of aluminum 3003 vary depending on the temper.
Temper | Tensile Strength (MPa) | Yield Strength (MPa) | Elongation (%) | Brinell Hardness (HB) |
---|---|---|---|---|
O (Annealed) | 110 | 40 | 30–40 | 28 |
3003-H12 | 135 | 125 | 10–20 | 35 |
3003-H14 | 155 | 150 | 8–16 | 40 |
3003-H16 | 185 | 175 | 5–14 | 47 |
3003-H18 | 205 | 190 | 4–10 | 55 |
Chemical Properties
Aluminum 3003 has strong corrosion resistance due to the natural oxide layer that forms on its surface. It performs well in humid environments and exposure to chemicals, making it suitable for applications that require long-term durability.
Magnetic and Oxidation Properties
- Magnetic Behavior: Aluminum 3003 is a paramagnetic material, meaning it does not attract or repel magnetic fields significantly.
- Oxidation Resistance: This alloy forms a protective aluminum oxide layer when exposed to air, preventing rust and corrosion.
3003 Aluminum Temper Types & Their Properties
Aluminum 3003 is available in different tempers, which affects its hardness, strength, and elongation.
- 3003-O (Annealed): Soft and highly formable
- 3003-H12: Half-hard with increased strength compared to O temper
- 3003-H14: The most commonly used type, balancing strength and formability
- 3003-H16: Higher strength with reduced elongation
- 3003-H18: The hardest among the tempers, used for applications requiring rigidity
3003 Aluminum Equivalent
Aluminum 3003 has equivalent materials under different international standards:
Standard | Equivalent Material |
---|---|
AA | 3003 |
ASTM | B209 |
ISO | AlMn1Cu |
UNS | A93003 |
EN | AW-3003 |
3003 Aluminum Applications
Due to its corrosion resistance, formability, and moderate strength, aluminum 3003 is used in various industries.
- Construction: Roofing sheets, wall panels, and structural components
- Transportation: Automotive panels, truck trailers, and fuel tanks
- Food & Beverage: Aluminum cans, cooking utensils, and food storage tanks
- HVAC Systems: Air conditioning fins and heat exchangers
- Marine Industry: Boat hulls and other water-exposed structures
- Gas Pipelines: Used for gas lines due to its high strength and corrosion resistance
- Ductwork: Lightweight and durable, making it ideal for HVAC ducts
- Heat Exchangers: Used in radiators and evaporators due to its excellent heat conductivity
What is Aluminum 5052?
Aluminum 5052 is a non-heat-treatable aluminum alloy that belongs to the 5000 series. It contains magnesium as the main alloying element, providing excellent corrosion resistance, good strength, and high workability. This alloy is widely used in marine, automotive, construction, and industrial applications due to its durability and ability to perform well in harsh environments.
5052 Aluminum Composition
Aluminum 5052 consists primarily of aluminum with magnesium and other elements that improve its mechanical and chemical properties.
Element | Composition (%) |
---|---|
Aluminum (Al) | Remainder |
Magnesium (Mg) | 2.2 – 2.8 |
Chromium (Cr) | 0.15 – 0.35 |
Silicon (Si) | ≤ 0.25 |
Iron (Fe) | ≤ 0.40 |
Copper (Cu) | ≤ 0.10 |
Manganese (Mn) | ≤ 0.10 |
Zinc (Zn) | ≤ 0.10 |
Other elements | ≤ 0.15 |
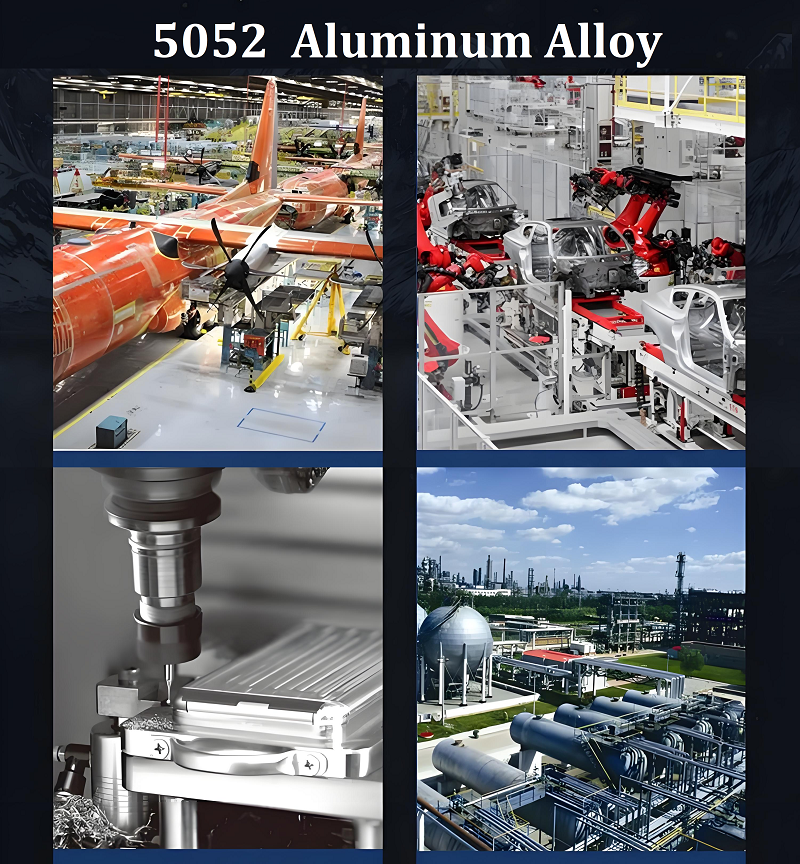
5052 Aluminum Properties
Physical Properties
- Density: 2.68 g/cm³
- Melting Point: 593–649°C
- Thermal Conductivity: 137 W/m·K
- Electrical Conductivity: 35% IACS
- Elastic Modulus: 68 GPa
- Shear Modulus: 26 GPa
- Poisson’s Ratio: 0.33
Mechanical Properties
The mechanical properties of aluminum 5052 vary depending on the temper.
Temper | Tensile Strength (MPa) | Yield Strength (MPa) | Elongation (%) | Brinell Hardness (HB) |
---|---|---|---|---|
O (Annealed) | 195 | 90 | 25–30 | 47 |
H32 | 230 | 195 | 12–18 | 60 |
H34 | 265 | 220 | 10–14 | 68 |
H36 | 280 | 245 | 8–12 | 73 |
H38 | 295 | 260 | 7–10 | 77 |
Chemical Properties
Aluminum 5052 has excellent corrosion resistance, particularly in marine environments. This is due to the natural oxide layer that forms on its surface, protecting it from rust and chemical exposure.
Processing Characteristics
- Weldability: Excellent, suitable for gas tungsten arc welding (GTAW), gas metal arc welding (GMAW), and resistance welding.
- Machinability: Moderate; better than pure aluminum but not as easy to machine as harder alloys like 6061.
- Formability: Good, allowing for bending and shaping without cracking.
- Surface Treatment: Accepts anodizing, painting, and other coatings for improved durability and appearance.
5052 Aluminum Temper Types & Their Properties
Aluminum 5052 is available in different tempers, which affects its hardness, strength, and elongation.
- 5052-O (Annealed): Soft with excellent formability, used for deep drawing applications.
- 5052-H32: Work-hardened and stabilized to provide a balance of strength and flexibility.
- 5052-H34: Higher strength than H32, with reduced elongation.
- 5052-H36 and H38: Stronger tempers with lower elongation, suited for structural applications.
5052 Aluminum Equivalent
Aluminum 5052 has equivalent materials under various international standards.
Standard | Equivalent Material |
---|---|
AA | 5052 |
ASTM | B209 |
ISO | AlMg2.5 |
UNS | A95052 |
EN | EN AW-5052 |
5052 Aluminum Applications
Due to its corrosion resistance, formability, and moderate strength, aluminum 5052 is widely used in various industries.
- Marine Industry: Boat hulls, ship components, and offshore structures due to its resistance to saltwater corrosion.
- Automotive and Transportation: Fuel tanks, truck trailers, and vehicle body panels.
- Construction: Roofing sheets, wall panels, and structural components.
- Food & Beverage: Aluminum cans, food storage tanks, and cooking utensils.
- Industrial Equipment: Pressure vessels, chemical storage tanks, and heat exchangers.
- Aerospace: Aircraft fuel tanks and structural elements requiring corrosion resistance.
What is Aluminum 6061?
Aluminum 6061 is a widely used aluminum alloy that belongs to the 6000 series. It contains magnesium and silicon as its primary alloying elements. This alloy is known for its good strength, corrosion resistance, and excellent machinability. It is a heat-treatable alloy, meaning its mechanical properties can be improved through heat treatment processes such as T6 tempering. Due to its balance of properties, aluminum 6061 is commonly used in aerospace, automotive, construction, and industrial applications.
6061 Aluminum Composition
Aluminum 6061 consists primarily of aluminum, with specific amounts of magnesium and silicon to improve strength and corrosion resistance. Other elements such as copper, chromium, and iron contribute to its mechanical properties.
Element | Composition (%) |
---|---|
Aluminum (Al) | Remainder |
Magnesium (Mg) | 0.8 – 1.2 |
Silicon (Si) | 0.4 – 0.8 |
Copper (Cu) | 0.15 – 0.40 |
Chromium (Cr) | 0.04 – 0.35 |
Iron (Fe) | ≤ 0.7 |
Zinc (Zn) | ≤ 0.25 |
Manganese (Mn) | ≤ 0.15 |
Titanium (Ti) | ≤ 0.15 |
Other elements | ≤ 0.15 |
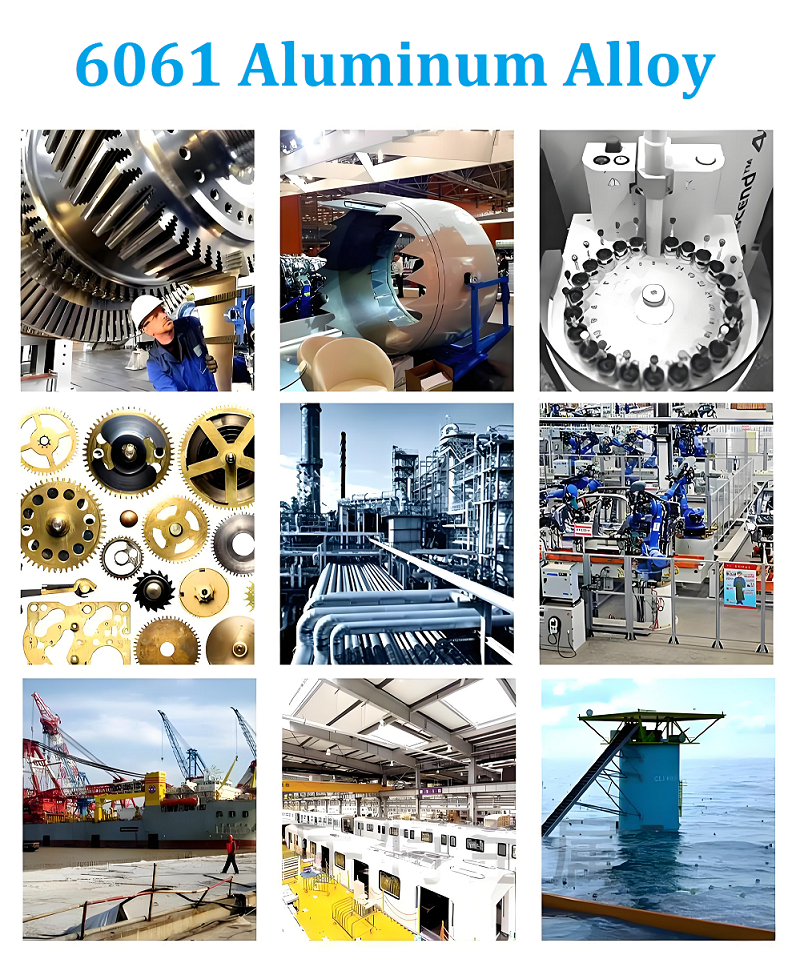
6061 Aluminum Properties
Physical Properties
- Density: 2.70 g/cm³
- Melting Point: 582–652°C
- Thermal Conductivity: 167 W/m·K
- Electrical Conductivity: 40–43% IACS
- Elastic Modulus: 68.9 GPa
- Shear Modulus: 26 GPa
- Poisson’s Ratio: 0.33
Mechanical Properties
The mechanical properties of aluminum 6061 vary depending on its temper.
Temper | Tensile Strength (MPa) | Yield Strength (MPa) | Elongation (%) | Brinell Hardness (HB) |
---|---|---|---|---|
O (Annealed) | 125 | 55 | 25–30 | 30 |
T4 | 245 | 150 | 22–25 | 65 |
T6 | 315 | 280 | 12–17 | 95 |
Chemical Properties
- Corrosion Resistance: High due to its oxide layer, making it suitable for marine and industrial applications.
- Anodizing Capability: Good, allowing for protective surface treatments.
- Weldability: Good, but heat-affected zones may experience strength reduction if not properly treated.
Processing Characteristics
- Machinability: Excellent, making it ideal for CNC machining and precision components.
- Formability: Moderate; easier to shape in the annealed (O) condition.
- Heat Treatment: Can be strengthened through solution heat treatment and artificial aging (T6).
6061 Aluminum Temper Types & Their Properties
Aluminum 6061 is available in different tempers, which affect its hardness, strength, and elongation.
- 6061-O (Annealed): Soft with excellent formability, used for deep drawing applications.
- 6061-T4: Solution heat-treated and naturally aged, offering moderate strength and good formability.
- 6061-T6: Solution heat-treated and artificially aged, providing the highest strength among 6061 tempers.
- 6061-T651: A stress-relieved version of T6, reducing internal stresses and improving dimensional stability.
6061 Aluminum Equivalent
Aluminum 6061 has equivalent materials under various international standards.
Standard | Equivalent Material |
---|---|
AA | 6061 |
ASTM | B209 |
ISO | AlMg1SiCu |
UNS | A96061 |
EN | EN AW-6061 |
6061 Aluminum Applications
Due to its strength, corrosion resistance, and machinability, aluminum 6061 is widely used in various industries.
- Aerospace: Aircraft structures, fuselage components, and wings.
- Automotive & Transportation: Vehicle frames, truck bodies, and rail components.
- Construction: Structural components, bridges, and scaffolding.
- Marine Industry: Boat hulls, docks, and offshore structures.
- Industrial Equipment: Machine parts, pressure vessels, and piping.
- Consumer Goods: Bicycle frames, sports equipment, and electronic enclosures.
Aluminum 3003 vs 5052 vs 6061, What are the Differences?
Although we have introduced these three aluminum alloys in detail above, in order to help you understand the differences between them more clearly, below we compare their composition, properties, applications, and costs to help in selecting the right material for specific needs.
Composition Comparison
Each of these alloys contains aluminum as the primary element but differs in secondary alloying elements, which influence their strength, corrosion resistance, and machinability.
Element | 3003 (%) | 5052 (%) | 6061 (%) |
---|---|---|---|
Aluminum (Al) | Remainder | Remainder | Remainder |
Magnesium (Mg) | 1.0 – 1.5 | 2.2 – 2.8 | 0.8 – 1.2 |
Manganese (Mn) | 1.0 – 1.5 | ≤ 0.10 | ≤ 0.15 |
Silicon (Si) | ≤ 0.60 | ≤ 0.25 | 0.4 – 0.8 |
Copper (Cu) | 0.05 – 0.20 | ≤ 0.10 | 0.15 – 0.40 |
Chromium (Cr) | – | 0.15 – 0.35 | 0.04 – 0.35 |
Iron (Fe) | ≤ 0.70 | ≤ 0.40 | ≤ 0.70 |
Zinc (Zn) | ≤ 0.10 | ≤ 0.10 | ≤ 0.25 |
Titanium (Ti) | – | ≤ 0.03 | ≤ 0.15 |
3003: Contains manganese, which improves corrosion resistance and workability, making it ideal for non-structural applications.
5052: Has more magnesium, providing higher strength and superior corrosion resistance, especially in marine environments.
6061: Includes magnesium and silicon, allowing for heat treatment that significantly increases strength.
Properties Comparison
The differences in composition affect their strength, corrosion resistance, and workability.
Property | 3003 | 5052 | 6061 |
---|---|---|---|
Density (g/cm³) | 2.73 | 2.68 | 2.70 |
Tensile Strength (MPa) | 110 – 205 | 195 – 295 | 125 – 315 |
Yield Strength (MPa) | 40 – 190 | 90 – 260 | 55 – 280 |
Elongation (%) | 4 – 40 | 7 – 25 | 8 – 30 |
Brinell Hardness (HB) | 28 – 55 | 47 – 77 | 30 – 95 |
Melting Point (°C) | 643–654 | 593–649 | 582–652 |
Thermal Conductivity (W/m·K) | 193 | 137 | 167 |
Strength: 6061 has the highest tensile and yield strength, followed by 5052, with 3003 being the weakest.
Workability: 3003 and 5052 are easier to form and weld compared to 6061.
Corrosion Resistance: 5052 offers the best corrosion resistance, making it ideal for marine environments.
Machinability: 6061 is the easiest to machine due to its higher hardness, while 3003 and 5052 are softer and more challenging to machine.
Applications Comparison
Aluminum 3003
- Food and Beverage Containers: Due to its corrosion resistance and non-toxic properties.
- Roofing and Siding: Common in the construction industry for its formability.
- Cooking Utensils: Lightweight and resistant to corrosion.
- Storage Tanks: Used in chemical and water storage.
Aluminum 5052
- Marine Industry: Used in boat hulls and fuel tanks due to its saltwater resistance.
- Automotive Panels: Provides durability and corrosion resistance.
- Pressure Vessels: Suitable for environments requiring high strength and corrosion resistance.
- Aircraft Fuel Tanks: Lightweight and corrosion-resistant for aviation applications.
Aluminum 6061
- Aerospace Components: Used in aircraft frames due to high strength and low weight.
- Structural Applications: Bridges and load-bearing components.
- Bicycle Frames: Provides rigidity and durability.
- Automotive Parts: Found in engine components and chassis.
Cost Comparison
The cost of aluminum alloys varies based on raw material prices, processing requirements, and availability.
Alloy | Cost ($/kg) | Strength | Corrosion Resistance | Workability |
---|---|---|---|---|
3003 | Low | Low | High | Excellent |
5052 | Moderate | Medium | Very High | Good |
6061 | Higher | High | Medium | Moderate |
5052 is more expensive but offers better corrosion resistance and strength.
6061 is the most expensive due to its high strength and machinability.
Aluminum 3003 vs 5052 vs 6061, Which One to Choose?
- For corrosion resistance and moderate strength, 5052 is a great choice, especially for marine and chemical applications.
- For cost-effective solutions with good formability, 3003 is ideal for roofing, food containers, and decorative items.
- For structural strength and machinability, 6061 is the best option, making it suitable for aerospace, automotive, and heavy-duty applications.