Aluminum alloys are some of the most widely used engineering materials in the world due to their high strength-to-weight ratio, corrosion resistance, and formability. The 6XXX series refers to alloys belonging to the aluminum-magnesium-silicon system, with magnesium and silicon serving as the primary alloying elements.
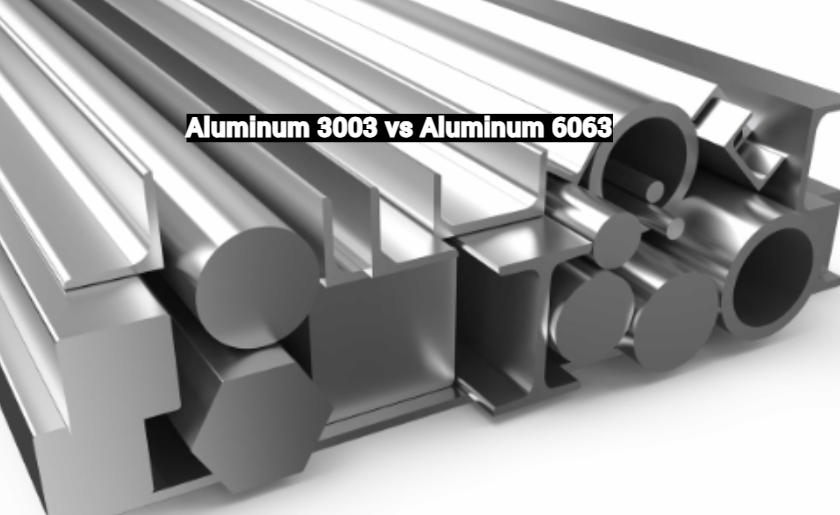
Aluminum 3003 vs Aluminum 6063
Within the 6XXX group, 3003 and 6063 are two of the most prevalent and commonly utilized aluminum alloys. Though similar in key properties such as resistance to chemical weathering, 3003 and 6063 differ substantially in terms of composition, strength characteristics, and suitable industrial applications. A thorough understanding of each alloy’s mechanical properties, performance considerations, and optimal use cases is critical for engineers and manufacturers. This article provides a detailed overview and comparison of 3003 and 6063 aluminum.
What Is 3003 Aluminum ?
Alloy 3003 aluminum alloy is commonly referred to as AL-Mn alloy systems. It is one of the most widely used non-heat treatable aluminum alloys for corrosion resistance applications. This alloy has relatively low strength (slightly higher than industrial pure aluminum) as it cannot be strengthened through heat treatment processes. Its mechanical properties are usually improved through cold working processes such as stretching and bending
What Is 6063 Aluminum?
Alloy 6063 aluminum alloy belongs to the AL-Mg-Si alloy system, which refers to alloys with medium strength that can be heat treatable. Mg and Si are the main alloying elements. 6063 alloy is widely used for aluminum door and window frames, curtain walls, due to its high requirements on wind pressure resistance, assembly performance, corrosion resistance and decorative performance, which are far higher than the comprehensive performance requirements of structural aluminum alloys in national standards GB/T3190. The range of chemical composition specified in the national standard results in different material properties, and when the range of composition is large, the performance fluctuations may vary greatly, making it difficult to control the comprehensive performance of the alloy.
Aluminium 3003 vs Aluminium 6063
Composition: 3003 aluminum alloy contains 96.5-98.5% aluminum, 1.0-1.5% silicon, and up to 1.5% other impurities. 6063 aluminum alloy contains 95.8-98.6% aluminum, 0.7-1.3% silicon, 0.8-1.2% magnesium, and up to 0.15% other impurities.
Mechanical Properties: 3003 alloy has good formability but relatively low strength. It has a yield strength of 130 MPa and an ultimate tensile strength of 280 MPa. This alloy is easily machinable and suitable for bending and stretching. 6063 alloy has higher strength than 3003 alloy. It has a minimum yield strength of 290 MPa and ultimate tensile strength range of 310-340 MPa. Due to the presence of magnesium, this alloy also has good corrosion resistance.
Applications: 3003 alloy is commonly used for architectural applications where good formability is required, such as wall panels, signs, and furnitureexteriors. 6063 alloy is widely used in applications requiring moderate structural strength like aircraft components, truck/trailer/van bodies, and bicycle frames. It is also used to make beverage cans. In summary, 3003 aluminum alloy has excellent formability making it suitable for fabrication processes involving bending and stretching. However, it has relatively low strength. 6063 alloy has higher strength making it preferable for load-bearing structures, but its formability is poorer compared to 3003. The composition and properties of these two alloys make them suitable for different application needs.