When it comes to aluminum alloys, Aluminum 356 and Aluminum 319 are two of the most widely used options in casting applications. Both alloys are favored for their unique properties, making them staples in industries such as automotive, aerospace, and industrial manufacturing. However, the choice between Aluminum 356 and Aluminum 319 often depends on the specific requirements of your project, such as strength, corrosion resistance, machinability, or casting performance. In this 319 aluminum vs 356 aluminum, we’ll break down the differences between them.
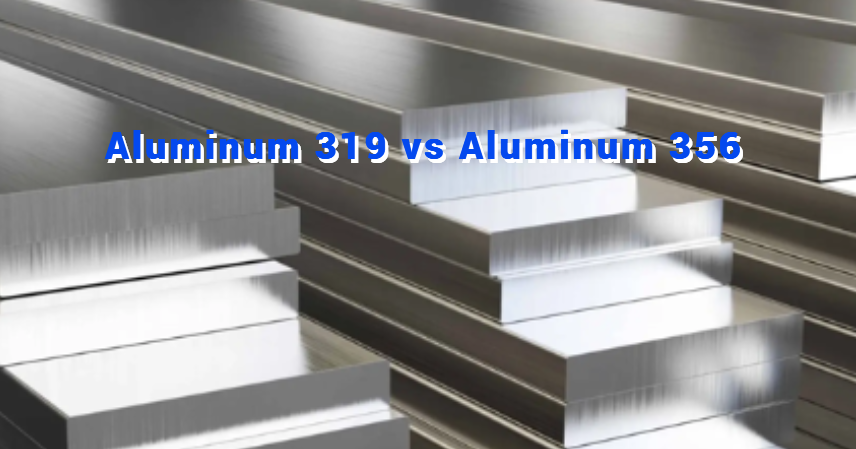
What Is 319 Aluminum Alloy?
319 aluminum is a type of aluminum alloy that is known for its excellent casting properties and good mechanical strength. This alloy is commonly used in the automotive industry for the production of various components, such as engine blocks, cylinder heads, and transmission cases, where its combination of strength, lightweight, and castability make it a popular choice. The 319 aluminum alloy is typically composed of around 6-7% silicon, 3-4% copper, and trace amounts of other elements like magnesium and manganese, which contribute to its unique properties and performance characteristics. This alloy is particularly well-suited for high-pressure die casting applications, allowing for the creation of complex, intricate parts with tight tolerances and a smooth surface finish.
What Are The Properties Of Aluminum 319?
Improved Mechanical Strength: The addition of copper, silicon, and other alloying elements in 319 aluminum enhances its mechanical properties, providing increased strength and rigidity compared to pure aluminum.
Lightweight: Aluminum, including the 319 alloy, is known for its low density, making it a popular choice in industries where weight reduction is critical, such as the automotive and aerospace sectors.
Corrosion Resistance: 319 aluminum exhibits good resistance to corrosion, which helps maintain the integrity and longevity of the components made from this alloy.
Thermal Conductivity: The 319 alloy has relatively high thermal conductivity, which can be beneficial in applications where efficient heat transfer is required, such as in engine blocks and cylinder heads.
Machinability: 319 aluminum can be easily machined, allowing for efficient manufacturing and the creation of precise, complex components.
Cost-Effective: Compared to other high-performance alloys, 319 aluminum is generally more cost-effective, making it a viable choice for various applications where cost is a significant factor.
What Is 356 Aluminum Alloy?
356 aluminum alloy is a type of aluminum alloy that is known for its excellent castability and good mechanical properties. It is a widely used alloy in the automotive, aerospace, and other industries due to its desirable characteristics. The 356 aluminum alloy is typically composed of around 7% silicon, 0.3% magnesium, and trace amounts of other elements such as copper, manganese, and iron.
What Are The Properties Of Aluminum 356?
Excellent Castability: The high silicon content in 356 aluminum provides excellent fluidity and castability, making it well-suited for various casting processes, including sand casting, die casting, and permanent mold casting.
Improved Mechanical Strength: The addition of magnesium in the alloy enhances its tensile strength, yield strength, and hardness, making it suitable for applications that require robust mechanical performance.
Corrosion Resistance: 356 aluminum exhibits good resistance to corrosion, which helps to maintain the integrity and longevity of the components made from this alloy.
Lightweight: As with other aluminum alloys, 356 aluminum is lightweight, making it an attractive choice for industries where weight reduction is a priority, such as in the automotive and aerospace sectors.
Thermal Conductivity: The 356 alloy has relatively good thermal conductivity, which can be beneficial in applications where efficient heat transfer is required, such as in engine components.
Aluminum 319 vs Aluminum 356, What’s The Difference
Composition:
- Aluminum 319 typically contains around 6-7% silicon, 3-4% copper, and trace amounts of other elements like magnesium and manganese.
- Aluminum 356 is composed of around 7% silicon, 0.3% magnesium, and smaller amounts of other elements such as copper, manganese, and iron.
Castability:
- Aluminum 319 has excellent fluidity and castability, making it ideal for high-pressure die casting applications.
- Aluminum 356 also has superb castability, with the high silicon content contributing to its favorable flow and fill characteristics, suitable for various casting processes like sand casting, die casting, and permanent mold casting.
Mechanical Properties:
- Aluminum 319 has improved mechanical strength compared to pure aluminum, due to the addition of copper and other alloying elements.
- Aluminum 356 has enhanced mechanical properties, particularly in terms of tensile strength, yield strength, and hardness, thanks to the presence of magnesium in the alloy.
Applications:
- Aluminum 319 is commonly used in the automotive industry for engine blocks, cylinder heads, and transmission cases, where its combination of strength, lightweight, and castability are crucial.
- Aluminum 356 finds applications in a wide range of industries, including automotive (engine components, wheels), aerospace, and various industrial and consumer products that require good casting characteristics and mechanical performance.
Corrosion Resistance:
- Both aluminum 319 and 356 exhibit good corrosion resistance, helping to maintain the integrity and longevity of the components made from these alloys.
What Are the Heat Treatment Options For Each Alloy?
Aluminum 319 Alloy:
- Solution Heat Treatment:
- Typically performed at temperatures around 495-525°C (920-975°F)
- Allows for the dissolution of copper-rich and other intermetallic phases
- Followed by a rapid quench to room temperature to retain the dissolved elements in a supersaturated solid solution
- Artificial Aging (T6 Temper):
- Involves heating the solution-treated 319 alloy to temperatures around 155-190°C (310-375°F)
- Promotes the precipitation of fine, dispersed hardening phases (such as CuAl2) within the aluminum matrix
- Significantly increases the alloy’s strength and hardness
- Natural Aging (T4 Temper):
- No artificial aging is performed, and the alloy is allowed to age at room temperature
- Results in a lower strength compared to the T6 temper, but higher ductility
Aluminum 356 Alloy:
- Solution Heat Treatment:
- Typically performed at temperatures around 525-550°C (975-1020°F)
- Dissolves the silicon and magnesium-containing phases
- Followed by a rapid quench to room temperature
- Artificial Aging (T6 Temper):
- Aging the solution-treated 356 alloy at temperatures around 155-180°C (310-355°F)
- Promotes the precipitation of Mg2Si hardening phases
- Significantly enhances the alloy’s strength and hardness
- Natural Aging (T4 Temper):
- No artificial aging is performed, and the alloy is allowed to age at room temperature
- Provides a lower strength compared to the T6 temper, but higher ductility
Machinability Comparison: Aluminum 319 vs Aluminum 356
Aluminum 319 and 356 alloys both exhibit good machinability characteristics, but the 356 alloy stands out as the more easily machinable of the two. The key difference lies in their respective chemical compositions.
The presence of copper in the 319 aluminum alloy helps improve its machinability by increasing the overall hardness and strength of the material. Additionally, the silicon content in 319 aluminum acts as a natural lubricant during the machining process, further enhancing its workability. However, the relatively higher copper content in 319 aluminum can make it slightly more challenging to machine compared to the 356 alloy, potentially requiring more specialized tooling and techniques to achieve optimal results.
On the other hand, the 356 aluminum alloy is considered one of the most machinable aluminum alloys due to its favorable chemical composition. The lower copper content and higher silicon content in 356 aluminum contribute to improved chip formation and reduced tool wear during machining operations. Furthermore, the presence of magnesium in the 356 alloy helps to minimize the formation of built-up edges on the cutting tools, further improving the quality of the machined surface. These characteristics make the 356 aluminum alloy a preferred choice for parts that require extensive machining, as it can be easily worked with a wide variety of cutting tools and techniques, resulting in a high-quality finish.