Aluminum alloy 6063 is widely used across industries for its strength, corrosion resistance, and fabricability. Within the 6063 composition, different tempers produce aluminum with distinct mechanical properties better suited to varied application needs. Two prime examples are 6063-T5 and high-strength 6063-T6. However, both have limitations that can impact manufacturability or performance under stress.
Enter 6063-T52 – an alloy with properties balancing the strengths of 6063-T5 and 6063-T6 while mitigating some of their shortcomings. But with three similar-yet-different 6xxx options available, how does one determine which alloy is best for a given use? This article provides a direct comparison between aluminum 6063-T5, 6063-T6, and 6063-T52.
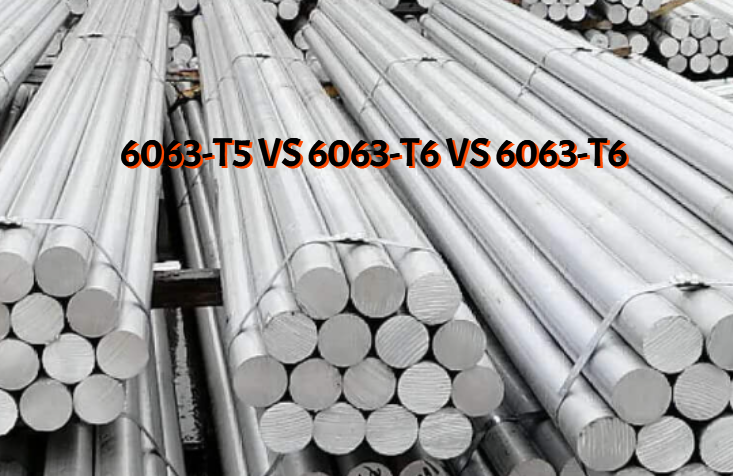
What Is Aluminum 6063-T5?
6063-T5 is an aluminum alloy that is similar to 6061 but contains more magnesium and silicon. The T5 temper designation indicates that 6063-T5 undergoes a solution heat treatment and artificial aging process. This results in higher strength compared to the non-heat-treated alloy through precipitation hardening. 6063-T5 has greater strength but reduced corrosion resistance and machinability relative to 6063 in a non-heat-treated state. Its strength properties make it suitable for various structural applications where 6061 is commonly used, such as transportation, infrastructure, and general fabrication. The T5 temper provides 6063 with enhanced mechanical characteristics for demanding load-bearing use while maintaining many of the attributes of standard 6063 such as weldability and light weight.
What Are The Properties Of Aluminum 6063-T5?
Strength – Higher tensile and yield strength than non-heat treated 6063 due to artificial aging. Has comparable strength to 6061-T6.
Machinability – Machinability is reduced compared to non-heat treated alloys, but still easier to machine than high-strength alloys.
Formability – Good bending and forming properties although strength limits severe deformation. Easier to form than 6061-T6.
Weldability – Can be welded with proper techniques and precautions against heat distortion or cracking.
Corrosion Resistance – Provides good corrosion protection but less than non-heat treated alloys due to temper.
Fatigue Resistance – Artificial aging increases resistance to cyclic stresses compared to basic 6063.
Weight – At around 2.70 g/cm3 density, offers strength/weight ratio advantages over steel.
Durability – Suitable for structural uses such as transportation and infrastructure in many environments.
Availability – Widely used alloy that is stocked by most aluminum distributors and suppliers.
What Are The Applications Of Aluminum 6063-T5?
Transportation – Used in truck trailers, cargo vans, train cars where strength and durability are important.
Marine structures – Decks, bulkheads, superstructures on ships and boats utilize 6063-T5.
Infrastructure – Bridges, signs, guardrails, towers employ its resistance to fatigue and corrosion.
Construction – Formwork, scaffolding, elevators, staircase components benefit from strength.
Industrial equipment – Machine frames, guards, enclosures for manufacturing facilities.
Commercial vehicles – Vans, trucks, taxi bodies, buses implement 6063-T5.
Pressure vessels – Cylinders, tanks for compressed air/gases use the alloy.
Consumer goods – Bicycles, ladders, playground structures, furniture.
Piping/ductwork – Low-pressure HVAC systems employ 6063-T5 tubing.
General fabrication – Prototyping, custom parts for its weld/machine properties.
What Is Aluminum 6063-T6?
6063-T6 is a heat-treated aluminum alloy that provides high-strength properties through a solution heat treatment and artificial aging process. After casting, 6063-T6 undergoes homogenization heating and then cooling, followed by a heat treatment to put the alloy into a thermally stable hardened condition. This technique of heat treating and controlled cooling confers increased strength over non-heat-treated alloys or lower tempers through precipitation strengthening. While more difficult to machine due to its hardness, 6063-T6 provides the highest attainable strength for this alloy, making it well-suited for structural and mechanical applications where maximum load-bearing performance is required, such as aircraft components, vehicles, industrial equipment, and construction.
What Are The Properties Of Aluminum 6063-T6?
Strength – Higher tensile and yield strengths than 6000 series alloys due to heat treatment hardening process.
Tensile Strength – Approximately 42,000 psi after solution heat treatment and artificial aging.
Machinability – More difficult to machine than softer tempers due to increased hardness, but still machinable.
Formability – Forming requires more force than untreated alloys but remains workable for bending.
Weldability – Can be welded but procedures need to prevent heat distortion and cracking.
Corrosion Resistance – Provides very good corrosion protection, comparable to untreated alloys.
Fatigue Resistance – Artificial aging greatly increases resistance to cyclic stresses.
Thermal Properties – Good thermal conductivity transfers heat quickly, resisting stresses.
Weight – At 2.7 g/cm3 density, offers high strength-to-weight ratio versus steel.
Durability – Well-suited for structural uses requiring maximum strength, like vehicles/infrastructure.
What Are The Applications Of Aluminum 6063-T5?
Aerospace structures – Used in airframes, engine components, cargo containers for its high strength.
Automotive components – Drive shafts, suspension parts, wheels, pedals, where maximum strength is needed.
Marine vessels – Bulkheads, hulls, rigging, propulsion systems utilize 6063-T6’s corrosion resistance.
Infrastructure – Bridges, overpasses, towers, poles, foundations leverage high fatigue resistance.
Industrial equipment – Machine frames, manufacturing tools, assemblies rely on the strength.
Pressure vessels – Tanks, pipes, valves for compressed air/gases use high-strength 6063-T6.
Consumer goods – Bicycles, exercise machines, durable tools, appliances employ the alloy.
Construction – Scaffolding, Formwork, window frames, fixtures benefit from durability.
Oil/gas lines – Flowlines, tubing, piping for offshore/underground need 6063-T6’s properties.
General fabrication – Prototypes, custom components, when strongest possible aluminum is required.
What Is Aluminum 6063-T52?
Aluminum 6063-T52 is a heat-treated aluminum alloy that is similar in composition to other 6xxx series alloys like 6063-T6, but with a T52 temper designation indicating a specific heat treatment process. The T52 temper involves solution heat treatment, cold working by stretching, and natural aging. This confers higher strength than the non-heat treated alloy through work hardening, while avoiding the brittleness that can result from artificial aging. 6063-T52 therefore offers elevated strength compared to other tempers, but with potentially better resistance to stress corrosion cracking. Its T52 properties make it suitable for applications requiring good strength with an emphasis on fracture toughness, such as marine structures, pressure vessels, and piping systems that experience dynamic stresses.
What Are The Properties Of Aluminum 6063-T52?
Strength – Higher strength than non-heat treated 6063 due to solution heat treatment and cold working. Stronger than T5 but not as strong as T6.
Tensile Strength – Around 35,000 psi due to work hardening through stretching.
Machinability – Machining is more difficult than annealed temper but easier than T6 due to lower hardness.
Formability – Good bending and forming properties although may crack under severe deformation.
Stress Corrosion Cracking Resistance – Better than T6 due to avoidance of brittle precipitates from artificial aging.
Weldability – Can be welded but procedures needed to prevent stress cracking or distortion on heating.
Corrosion Resistance – Provides good corrosion protection comparable to other 6xxx tempers.
Fatigue Resistance – Increased resistance to cyclic loads from work hardening treatment.
Fracture Toughness – Absorbs more energy when cracked compared to artificial aged T6 temper.
What Are The Applications Of Aluminum 6063-T52?
Pressure vessels – Tanks, pipes and valves that see pressure changes benefit from its fracture toughness.
Marine structures – Decks, hulls, masts, where impacts or stress cracking could occur offshore.
Transportation – Truck/trailer bodies, cargo vans, railcars employ the alloy’s durability.
Piping systems – Water pipes, plumbing, hydraulic lines prefer 6063-T52’s resistance to bursting.
Industrial equipment – Pressure equipment, valves, pumps use its strength and toughness.
Construction – Scaffolding, formwork, handrails need high fatigue performance.
Oil/gas infrastructure – Flowlines, manifolds, flanges in corrosive subsea environments.
Consumer items – Bicycles, ladders, playgrounds, where impacts must be withstood.
Aerospace components – Interior fixtures, ducting, where fatigue is a concern.
General fabrication – Custom mechanical/structural parts benefit from balanced properties.
6063-T5 vs 6063-T6 vs 6063-T52 Aluminum, What Are The Differences?
The additional cost column shows that 6063-T6 has the highest production costs due to the artificial aging process required. 6063-T5 has the lowest cost. 6063-T52 has a medium cost level due to the work hardening treatment involved. This cost differentiation is an important consideration when choosing between these similar yet distinct aluminum alloys. Below are the differences between T52 vs T6 vs T5 aluminum.
Comparison | 6063-T5 | 6063-T6 | 6063-T52 |
Temper Process | Solution heat treated and artificially aged | Solution heat treated and artificially aged | Solution heat treated, cold worked, and naturally aged |
Tensile Strength (psi) | 30,000-35,000 | 42,000 | 35,000 |
Hardness | Medium | High | Medium-high |
Machinability | Good | More difficult | Easier than T6 |
Formability | Good | More difficult | Good |
Stress Corrosion Resistance | Good | Potentially lower than T52 | Best of three tempers |
Weldability | Good with precautions | More difficult | Potentially easiest of three |
Cost | Lower | Highest | Medium |
Applications | General structural, industrial equipment | High strength applications like aerospace, automotive | Pressure vessels, marine, piping where toughness is critical |
6063 T5 Aluminum vs 6063 T6, Which is Better?
Both 6063-T6 and 6063-T5 are variations of the 6063 aluminum alloy, widely used in construction, architectural applications, and extrusion projects. The key difference lies in their heat treatment process, which affects strength, hardness, and workability.
6063-T5 Aluminum
✔ Cooling Process: Air-cooled after extrusion, then artificially aged.
✔ Strength: Moderate strength, lower than T6.
✔ Workability: Easier to bend and shape, making it ideal for applications that require forming.
✔ Common Uses: Window frames, doors, railings, and decorative trim.
6063-T6 Aluminum
✔ Cooling Process: Water-quenched and then artificially aged for higher strength.
✔ Strength: Much higher tensile strength and hardness than T5.
✔ Workability: Less flexible, harder to bend but more durable.
✔ Common Uses: Structural components, aerospace, heavy-duty applications, and parts requiring high strength.
6063 T5 Aluminum vs 6063 T52, Which is Better?
Both 6063-T5 and 6063-T52 are variations of the 6063 aluminum alloy, commonly used in architectural, structural, and extrusion applications. The primary difference lies in their heat treatment and flexibility.
6063-T5 Aluminum
✔ Cooling Process: Air-cooled after extrusion, then artificially aged.
✔ Strength: Moderate strength, slightly lower than T52.
✔ Workability: Good machinability, but not as flexible as T52.
✔ Common Uses: Window frames, doors, railing systems, and general-purpose extrusions.
6063-T52 Aluminum
✔ Cooling Process: Similar to T5 but stress-relieved through stretching, reducing internal stresses.
✔ Strength: Slightly stronger than T5 due to stress relief.
✔ Workability: More flexible than T5, making it easier to bend without cracking.
✔ Common Uses: Applications requiring post-extrusion bending, such as handrails, piping, and curved architectural components.
6063 T6 Aluminum vs 6063 T52, Which is Better?
Both 6063-T6 and 6063-T52 are variations of the 6063 aluminum alloy, commonly used in construction, architecture, and extrusion applications. The main difference lies in their heat treatment, strength, and flexibility.
6063-T6 Aluminum
✔ Cooling Process: Water-quenched and artificially aged to maximize strength.
✔ Strength: Highest tensile strength among 6063 tempers (approx. 30,000 psi).
✔ Workability: Less flexible, making it harder to bend or shape.
✔ Common Uses: Structural applications, load-bearing components, aerospace, and areas requiring high strength.
6063-T52 Aluminum
✔ Cooling Process: Similar to T5 but stress-relieved through stretching to reduce internal stresses.
✔ Strength: Lower strength than T6 but slightly stronger than T5.
✔ Workability: More flexible, allowing for easier bending without cracking.
✔ Common Uses: Handrails, piping, decorative trim, and applications requiring post-extrusion bending.
T5 vs T6 vs T52 Aluminum, Which is Better?
Choose T5 for general extrusion applications with good strength and ease of machining.
Choose T6 for maximum strength and durability, ideal for structural and heavy-duty applications.
Choose T52 if bending and shaping are required, as it resists cracking better than T6.