In recent years, with the increasing demand for environmentally friendly and lightweight materials in society, the aluminum alloy die-casting industry is gradually becoming a highly anticipated field in the manufacturing industry. Aluminum alloy die-casting, as an advanced metal forming technology, has many advantages. So, what are the technical difficulties of ultra large aluminum die casting parts?
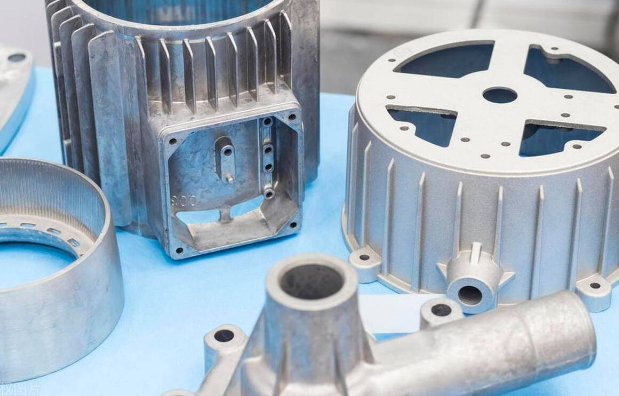
Aluminum Die Casting Part Challenges & Solutions
Compared with traditional casting methods, aluminum alloy die-casting can produce aluminum alloy parts with more precision, higher strength, and more stable size, while also greatly shortening the production cycle. This has led to the widespread application of aluminum alloy die-casting in fields such as automobiles, aerospace, and electronics. With the continuous progress and innovation of industry technology, the market prospects of aluminum alloy die-casting will further expand.
The trend of environmental protection and energy conservation has driven the rapid development of the aluminum alloy die-casting industry. Aluminum alloy has good recyclability and reusability, and compared to traditional forming materials, aluminum alloy die-casting is more in line with the requirements of sustainable development. With the continuous improvement of environmental awareness, aluminum alloy die-casting will become an important choice to replace traditional materials, with huge market potential.
What are the technical difficulties of ultra large aluminum alloy die-casting parts?
The biggest technical challenge in the process of manufacturing ultra large aluminum die castings is how to ensure the integrity and accuracy of the castings. Firstly, during the cooling process of aluminum alloy melt, thermal cracks are prone to occur, especially in areas with large casting thickness, which can cause the casting to burst or even fail to form.
Secondly, oversized aluminum alloy die castings require a relatively large volume to be formed in a short period of time. Excessive heat in the castings makes it difficult to effectively control the temperature and pouring speed of the melt, which can also affect the quality and molding of the castings.
At the same time, due to the long-term processing and treatment required for ultra large aluminum alloy die-casting parts, it is also necessary to consider their transportation and installation issues. Among them, special equipment is required for transportation, while dedicated personnel are required for installation, as even small errors can greatly affect the accuracy and integrity of the finished product.
Faced with these technical difficulties, die-casting manufacturing enterprises should strengthen their technological research and innovation awareness, constantly introduce new ideas, and explore more efficient, safe, and stable production processes.
On this basis, we also need to combine existing technology and market demand to provide consumers with higher quality ultra large aluminum alloy die-casting products.
The manufacturing of ultra large aluminum alloy die-casting parts is a highly technically challenging task.
How to Solve the Difficulties of Aluminum Alloy Die Casting?
Manufacturing ultra large aluminum alloy die castings does face many technical difficulties, but these problems can be solved by adopting advanced processes and technologies, as well as strict quality control. Here are some ways to address these challenges:
Prevention of thermal cracking:
Choosing the appropriate aluminum alloy material: Different aluminum alloys have different thermal crack resistance properties, so it is very important to choose alloy materials suitable for ultra large aluminum alloy die castings.
Temperature control: By accurately controlling the temperature of the melt, especially at the beginning and end of pouring, the occurrence of hot cracks can be reduced.
Mold design: Optimize the design of the mold, taking into account the cooling rate and thermal stress distribution of the material, to reduce the risk of thermal cracking.
Control pouring speed and pressure:
Use advanced pouring system: adopt modern pouring system with precise control of pouring speed and pressure to ensure that the material is fully filled in the mold without overheating.
Mold temperature control: By accurately controlling the mold temperature through the cooling system, the cooling rate of aluminum alloy can be slowed down, which helps to avoid problems caused by rapid cooling.
Quality control:
Non destructive testing: Use non-destructive testing methods such as X-ray, ultrasonic, or magnetic particle testing to inspect the quality of castings and identify potential defects.
Strict process control: Ensure that every step of the production process is strictly controlled and monitored, including pouring, cooling, mold removal, post treatment, and other links.
Transportation and installation:
Customized transportation plan: Collaborate with professional transportation companies to develop customized transportation plans for ultra large aluminum alloy die castings, including the use of special transportation equipment and safety measures.
Professional installation team: Hire an experienced installation team to ensure that aluminum alloy die castings can be accurately installed in designated locations, ensuring integrity and accuracy.