Sheet metal is a type of metal that has been rolled or pressed into thin, flat pieces. It is a versatile and widely used material in various industries due to its many advantages. As a discerning customer or a seasoned professional, understanding the unique properties and applications of different sheet metal types can be the key to unlocking the full potential of your project. In this guide, we’ll talk about the distinct characteristics of aluminum, galvanized, and perforated sheet metals.
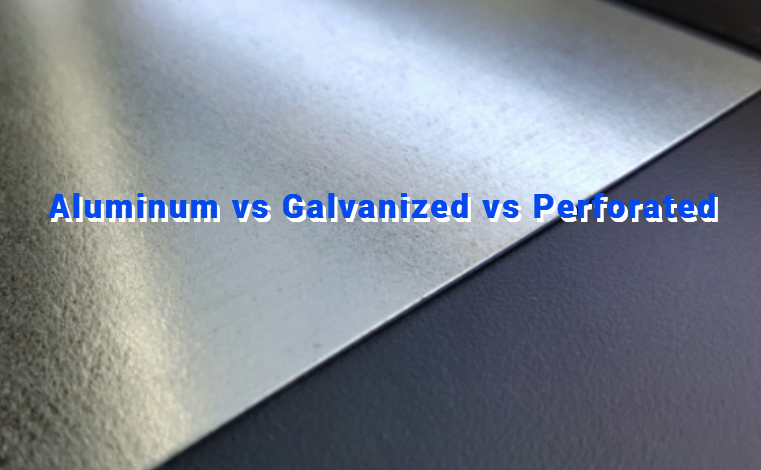
About Sheet Metal
Sheet metal refers to metal that has been reduced to a thin, flat form, typically through a rolling or pressing process. The thickness of sheet metal can range from a few millimeters down to a fraction of a millimeter. Sheet metal fabrication involves various processes, such as cutting, bending, welding, and stamping, to transform the flat sheets into desired shapes and components. The versatility and properties of sheet metal make it an essential material in many modern manufacturing and construction applications.
Common Materials:
The most common materials used for sheet metal are:
- Steel (including stainless steel)
- Aluminum
- Copper
- Brass
What is Aluminum Sheet Metal?
Aluminum sheet metal is a flat, thin piece of aluminum that is formed through a process of rolling aluminum into sheets of varying thicknesses. Known for its lightweight, durability, and resistance to corrosion, aluminum sheet metal is widely used in various industries, including construction, automotive, aerospace, and manufacturing. It is valued for its high strength-to-weight ratio, ease of fabrication, and versatility, making it ideal for applications such as roofing, siding, vehicle panels, aircraft skins, and household appliances. Additionally, aluminum sheet metal can be easily cut, welded, and shaped, offering significant flexibility for both functional and decorative purposes.
What is Galvanized Sheet Metal?
Galvanized sheet metal is steel that has been coated with a layer of zinc to protect it from corrosion and rust. This process, known as galvanization, involves dipping the steel sheet into molten zinc, creating a durable, long-lasting protective barrier. The resulting galvanized sheet metal is highly resistant to environmental factors, such as moisture and humidity, which can cause rust and deterioration. It is commonly used in construction, automotive, and manufacturing industries for products like roofing, fencing, ductwork, and structural support. Its combination of strength, durability, and corrosion resistance makes galvanized sheet metal a popular choice for both indoor and outdoor applications.
What is Perforated Sheet Metal?
Perforated sheet metal is a type of metal sheet that has been mechanically punched or stamped to create a pattern of holes, slots, or decorative shapes. These perforations can vary in size, shape, and spacing, offering both functional and aesthetic benefits. Perforated sheet metal is widely used in various industries, including architecture, manufacturing, and design, for applications such as ventilation, filtration, soundproofing, and decorative facades. Its ability to allow light, air, and sound to pass through while maintaining structural integrity makes it a versatile material for a wide range of projects. Additionally, it can be made from various metals, including aluminum, steel, and stainless steel, further enhancing its adaptability and utility.
Aluminum vs Galvanized vs Perforated Sheet Metal
When it comes to sheet metal fabrication, there are several material options to choose from, each with its own unique properties and applications. Three commonly used types are aluminum sheet metal, galvanized sheet metal, and perforated sheet metal. Let’s explore the key differences between these materials:
Aluminum Sheet Metal:
Composition: Aluminum is a lightweight, non-ferrous metal known for its corrosion resistance and high strength-to-weight ratio.
Properties: Aluminum sheet metal is highly malleable, making it easy to fabricate into various shapes and forms. It is also non-magnetic and has excellent thermal and electrical conductivity.
Applications: Aluminum sheet metal is widely used in the automotive, aerospace, construction, and consumer goods industries. It is popular for its aesthetic appeal, durability, and versatility.
Galvanized Sheet Metal:
Composition: Galvanized sheet metal is steel coated with a layer of zinc, which provides superior corrosion resistance.
Properties: Galvanized steel is known for its high strength, impact resistance, and weather-resistant properties. The zinc coating also helps to prevent rusting and deterioration.
Applications: Galvanized sheet metal is commonly used in roofing, siding, HVAC ductwork, and various industrial applications where corrosion resistance is crucial.
Perforated Sheet Metal:
Composition: Perforated sheet metal can be made from a variety of materials, including aluminum, steel, and stainless steel, with a pattern of uniform holes or openings throughout the material.
Properties: Perforated sheet metal offers unique properties, such as increased airflow, reduced weight, and enhanced visual appeal. The perforations can be customized in size, shape, and pattern to suit specific requirements.
Applications: Perforated sheet metal finds use in a wide range of industries, including architecture, industrial equipment, filtration systems, and decorative applications, taking advantage of its functional and aesthetic qualities.
When selecting between these sheet metal options, consider the specific requirements of your project, such as strength, corrosion resistance, weight, and visual appeal. Additionally, factors like cost, availability, and ease of fabrication should be taken into account.
It’s important to work closely with a reputable sheet metal fabricator who can provide expert guidance and help you choose the most suitable material for your needs.