Aluminum is a relatively active metal with a standard potential of -1.66V. It can naturally form an oxide film with a thickness of about 0.01-0.1 micrometers in air. This oxide film is amorphous, thin and porous, and has poor corrosion resistance. However, if aluminum and its alloys are placed in an appropriate electrolyte and aluminum products are used as anodes, an oxide film is formed on their surface under the action of an applied current. This method is called anodizing.
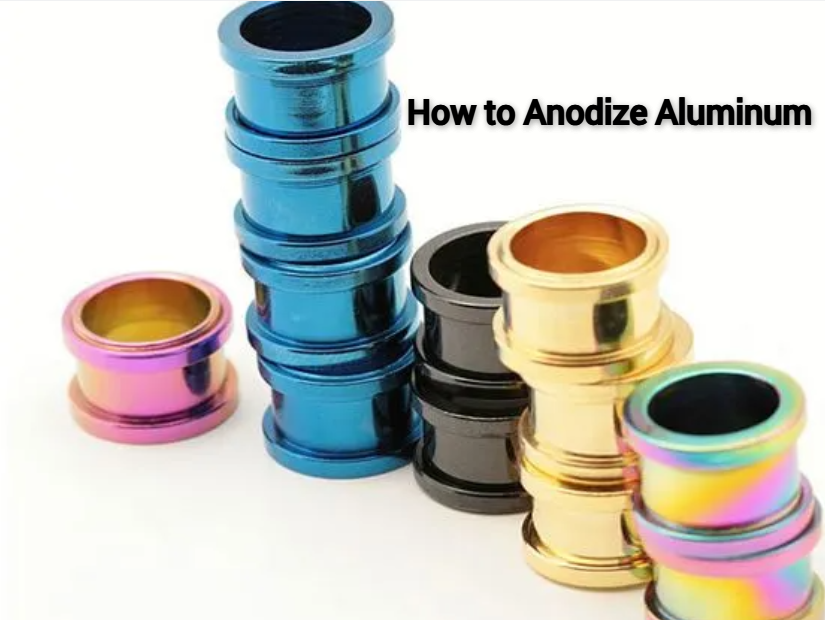
Anodized Aluminum Guide: Process, Prices, Tips & How To Anodize
By selecting different types and concentrations of electrolytes, as well as controlling the process conditions during oxidation, anodic oxide films with different properties and thicknesses ranging from tens to hundreds of micrometers can be obtained. Their corrosion resistance, wear resistance, and decorative properties have been significantly improved and enhanced. The electrolyte used for anodizing of aluminum and aluminum alloys is generally an acidic solution with moderate solubility, with lead or aluminum as the cathode and only playing a conductive role. When anodizing aluminum and its alloys, the following reactions occur at the anode:
2Al –>6e -+2Al3+
The following reactions occur at the cathode:
6H2O+6e –>3H2+6OH-
At the same time, the acid chemically dissolves aluminum and the generated oxide film, and the reaction is:
2Al+6H+–>2Al3++3H2
Al2O3+6H+–>2Al3++3H2O
The growth process of oxide film is the continuous generation and dissolution of oxide film.
How To Anodize Aluminum?
Anodizing is a process that utilizes acid to form a corrosion-resistant and wear-resistant layer on a metal surface. If you want to perform anodizing treatment at home, the following are some steps:
Preparation materials:
Purchasing standard aluminum alloy parts, anodizing works particularly well on aluminum alloys.
Buy a sturdy and durable plastic basin to soak metal parts in.
Go to the nearby grocery store to purchase clothing dyes for dyeing.
Prepare degreaser, lead cathode plate, aluminum wire, purified water, baking soda, rubber gloves, sulfuric acid, and voltage stabilizer.
Clean the surface of aluminum alloy:
Clean the metal surface with soap and water.
Use a degreaser to remove grease from the metal surface.
Mix the alkaline solution with pure water, soak the parts for 3 minutes, and then rinse thoroughly.
Prepare the anodizing tank:
Place the plastic bowl in a well ventilated area and cover it with plywood or thick cloth.
Connect the power supply, connect the positive electrode to the aluminum alloy component, and connect the negative electrode to the lead cathode plate.
Put pure water and battery acid into the basin and mix them in proportion.
Start anodizing:
Turn on the power and stabilize for 45 minutes.
Mix the dye with purified water and heat it to 37-60 degrees Celsius.
Turn off the power, remove the metal parts, and rinse with clean water.
Put the parts into a dyeing bath and then boil them.
What Are the Factors That Affect The Cost Of Anodized Aluminum ?
Anodizing is usually the preferred choice for achieving the best surface finish of aluminum parts. However, this decision depends on the cost of anodizing the required aluminum components. The following factors affect the cost of anodized aluminum oxide parts.
Anodizing Aluminum Tips
There are three types of anodizing techniques that you can use in your project.
Type 1 anodizing, also known as “light” type, involves placing aluminum into a tank containing chromic acid, where aluminum acts as the anode. The current passing through chromic acid causes positively charged aluminum particles to leave the surface, forming small grooves. When oxidized, these grooves form an oxide layer. Compared to unoxidized aluminum, Type 1 anodized aluminum components exhibit higher heat and corrosion resistance.
Type 2 anodizing is similar to Type 1. The main difference lies in the use of sulfuric acid instead of chromic acid. This substitution will result in deeper grooves and thicker oxide layers. Type 2 aluminum parts have enhanced paint retention due to their deeper grooves and ease of filling.
Type 3 anodizing, also known as hard anodizing, involves higher voltage and the use of strong acid sulfuric acid. This type is suitable for manufacturing heavy wear parts.
Any choice of these types will significantly affect the cost of aluminum anodizing. Among the three, Type 1 anodizing is the most economical. This is attributed to the use of inexpensive materials (such as chromic acid) and lower energy consumption.
On the other hand, the cost of aluminum anodizing for Type 3 has increased. The higher cost is due to the use of more expensive materials, such as sulfuric acid, rather than chromic acid. It also has high energy consumption. Generally speaking, the higher the type of anodizing, the higher the cost of anodized aluminum oxide.
Component size and quantity
The size of the selected material significantly affects the cost of anodizing the aluminum portion. The larger the size, the larger the surface area. This surface area requires more materials and facilities to be successfully completed. In addition, the increase in the number of components leads to higher labor and time requirements. Therefore, it directly affects the cost of anodized aluminum oxide.
The possibility of shelves
Shelves are a critical process for managing workflows and ensuring safe electrical connections at all stages. The types of shelves include clamp type, welded type, and bolt type shelves. This process ensures quality and significantly affects the cost of aluminum anodizing services.
In the absence of specified methods, manufacturers will choose economically efficient methods to maximize production while minimizing costs. Specific shelf requirements may limit the number of parts processed at once. This may lead to an increase in the cost of each component.
Coating thickness
This refers to the thickness of the oxide layer on the surface of aluminum parts. It is a key factor in determining the cost of aluminum anodizing. Choosing the basic thickness is the most cost-effective choice. The impact of coating thickness on the cost of anodized aluminum oxide finishing may not be consistent with usual expectations.
Thin or narrower coatings are usually more expensive than thicker coatings. For example, a thickness of+/-001 “is more cost-effective than+/-0001” because it is easier to control thicker oxide layers. Realizing this level of control requires experience and professionalism, which directly leads to higher costs for anodizing.
Required anodized aluminum oxide color
The specific requirements for color can play a role in determining the overall cost of the anodizing process. Different colors of anodized aluminum may involve different materials and processes, which may affect overall costs. Generally speaking, standard colors may be more cost-effective as they typically require fewer specialized materials and are part of regular production operations. On the other hand, customized or unique colors require additional steps, materials, or adjustments to achieve the desired color tone. This may increase the cost of anodized aluminum oxide.
Additional post-processing services
Customers seeking additional processes to improve efficiency or enhance product aesthetics should be aware that these improvements require additional costs. Blocking or masking holes and other services require additional labor and time. Although these additional services add value, they also increase the overall cost of anodized alumina.
Tips For Creating High-Quality Anodized Aluminum Parts
The anodizing process may seem a bit complicated, but in reality, it is not. Here are some tips to help you fully utilize this process.
Purchase appropriate materials
Understanding specific alloys is crucial. The selected aluminum alloy significantly affects the results of anodizing. Different alloys have different compositions and have different effects on the anodic oxidation process. For example, 6061 aluminum is widely popular due to its quality, surface integrity, environmental resistance, and processability.
Once the correct alloy is selected, it is important to consistently use similar parts. There may be multiple types in the supplier’s inventory. The quality and production methods of primary and secondary inventory greatly affect the final product after anodizing.
Don’t ignore chemistry
Ensuring high-quality and reliable results during the anodizing process requires precise control of the scientific aspects of each step. The anodizing method includes multiple stages: cleaning, etching (pretreatment), anodizing, sealing, and rinsing between steps.
The key control measures for each stage include monitoring concentration, pH, time, and temperature. Although chemical suppliers specify parameter ranges for each substance, anodizers must study and test different conditions to determine the optimal range. This can be facilitated through consultation with experts in the field, such as Xin Tielong
Control anodizing tank
Factors such as anodizing temperature, time, stirring, and the quality of the cathode in the tank are crucial. These factors significantly affect the results of part coating during the anodizing process.
Effective anodizing technology requires careful control of the tank and a clear goal of obtaining stable and high-quality coatings. In addition to the chemicals specified in the tank, regular adjustment of the rectifier (power supply) is also crucial.
Ensure appropriate surface treatment
Anodizing is different from other precision machining processes. Each part of the aluminum surface must be fully prepared for anodizing. In order to ensure predictable results during the anodizing process, appropriate treatment and maintenance of aluminum components must be carried out.
Failure to remove oil stains, debris, and fingerprints may lead to surface treatment issues. Checking the materials and ensuring the removal of these pollutants is crucial for increasing the likelihood of success.