In CNC (Computer Numerical Control) machining, the technical drawing is a key tool that provides a communication bridge between the designer and the manufacturer. This article will introduce the components of CNC machining technical drawings, the role, and usage of machining symbols in technical drawings, how to prepare technical drawings, etc., to ensure high-quality machining results.
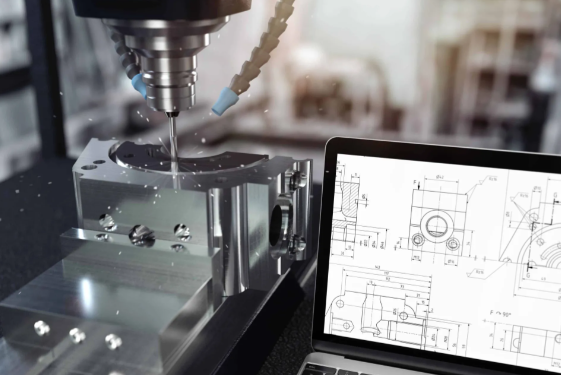
What Does a Technical Drawing for CNC Machining usually Contain
A technical drawing for CNC (Computer Numerical Control) machining typically contains the following elements, each of which provides a detailed description of the part and manufacturing requirements:
- 1. Views: Technical drawings usually contain multiple views, such as front view, top view, section view, etc. These views provide a detailed description of the appearance and shape of the part, viewing the part from different angles.
- 2. Dimensions and Tolerances: Dimensions and tolerances define the size and allowable range of each feature of the part. They guide machining and measurements during manufacturing and ensure parts meet design requirements. Dimensions are usually expressed by numbers and symbols, and tolerances are specified by symbols and limits.
- 3. Annotations: Annotations are used to provide additional information, such as surface roughness requirements, processing methods, special assembly requirements, etc. They provide pertinent instructions and details related to dimensions and tolerances.
- 4. Section Views: Section views display detailed information on part sections. They are used to show the internal structure, the location and characteristics of holes, etc., to better understand the geometry of the part.
- 5. Machining Symbols: Machining symbols are used to describe the specific processing requirements of parts, such as cutting, drilling, threading, etc. They provide instructions on machining operations to ensure correct machining methods and workmanship.
- 6. Material Specifications: Material specifications define the material type, grade, and properties required to manufacture the part. These specifications include information on the chemical composition, strength, hardness, etc. of the material to ensure that the correct material is selected and used.
- 7. Assembly Information: If the part belongs to an assembly system, the technical drawing may contain assembly information, such as matching methods, positioning holes, assembly sequence, etc. This information ensures that the part mates correctly with other components during assembly.
- 8. Title Block: The title block of a technical drawing is usually located at the bottom or upper right corner of the drawing and contains basic information about the drawing, such as drawing number, date, author, unit, etc.
Function and Usage of Processing Symbols in Technical Drawings
In technical drawings, machining symbols are used to illustrate specific machining requirements and operations for a part. They provide guidance to manufacturers and operators to ensure proper machining methods and workmanship. The following are the main functions and usages of processing symbols:
- – Machining process indication: The machining symbol tells the operator which specific machining process should be used to make the part. For example, the symbol “G” indicates that the part needs to be planed, “M” indicates that milling is used, “D” indicates drilling, etc. These symbols ensure correct machining operations and application of the craft.
- – Machining direction indication: Machining symbols can be used to indicate the direction of machining operations. For example, an arrow symbol indicates the direction of movement of a cutting tool or workpiece. This is very important to determine parameters such as cutting direction, feed direction, cutting speed, etc. to ensure correct machining results.
- -Description of machining features: Machining symbols can be used to describe specific machining features on a part. For example, the thread symbol indicates that threads need to be processed on the part, the symbol “R” indicates that chamfering is required, and the symbol “∅” indicates that hole processing is required, etc. These symbols provide information about specific machining features to ensure correctness and consistency.
- – Other processing requirements: The processing symbol can also be used to indicate other specific processing requirements. For example, the symbol “Ra” indicates that specific roughness requirements need to be met, the symbol “T” indicates that heat treatment is required, the symbol “P” indicates that polishing is required, etc. These symbols provide an indication of special processing requirements to ensure parts meet design and function requirements.
The Importance of Technical Drawings for CNC Machining
Technical drawings are very important and useful for CNC machining. They provide a detailed description of part geometry, machining requirements, tolerance ranges, and assembly requirements, providing guidance and a basis for manufacturers to ensure that parts are accurately and consistently CNC machined as designed. Technical drawings are useful for CNC (Computer Numerical Control) machining for the following reasons:
- 1. Provide an accurate geometric description: Technical drawings provide an accurate description of the part geometry. It contains information such as views, dimensions, tolerances, etc., enabling manufacturers to clearly understand the appearance, size, and shape requirements of parts. This is very critical for CNC machining because CNC machine tools can perform automatic machining according to the geometric description on the drawing.
- 2. Guiding processing operations: The processing symbols and processing requirements in the technical drawings provide detailed guidance on the processing process. They tell the operator which specific machining method, cutting tool, feed rate, cutting speed, etc. to use. These guidelines ensure the application of correct machining operations and processes to ensure the accuracy and quality of the parts.
- 3. Determine tolerances and quality requirements: Dimensions and tolerances in technical drawings define the size and allowable range of individual features of the part. These tolerance requirements are critical to CNC machining because they guide cutting, positioning, and measurement during machining. Through the tolerance requirements in the technical drawing, the manufacturer can ensure that the part will be within the tolerance specified by the design.
- 4. Understand the assembly requirements: technical drawings also provide relevant information about the parts during assembly, such as matching methods, positioning holes, assembly sequence, etc. This is very important for manufacturers as they need to ensure that CNC-machined parts fit and assemble properly with other components.
- 5. Traceability and quality control: As the basis of specifications and standards, technical drawings provide the basis for traceability and quality control for CNC machining. The manufacturer can process according to the requirements in the technical drawings, and record and track the process to ensure that the product meets the design requirements and specifications.
Common Methods for Determining the Tolerance Range
There are some common statistical methods that can be used to determine the tolerance range. These methods can help you choose an appropriate tolerance range taking into account manufacturing variation and acceptable variation. The following are several common statistical methods:
- -Six Sigma: The Six Sigma method is a quality management method based on statistical analysis to minimize variation in the manufacturing process. By analyzing the process capability index (Cp) and process capability index (Cpk), the tolerance range can be determined to ensure consistency and stability throughout the production process.
- -Histogram and Normal Distribution Curve: By collecting a sample set of data and plotting a histogram, it is possible to understand the distribution of part sizes. If the sample data tends to be close to a normal distribution, the normal distribution curve can be used to analyze the data to determine an appropriate tolerance range.
- -Cp and Cpk: The process capability index is an index to measure whether the manufacturing process can meet the specification requirements. By calculating the process capability index, the tolerance range can be determined to ensure that the manufacturing process can produce acceptable parts within the allowable range.
- – Pre-determined tolerance (Pre-determined Tolerance): This method is based on past experience and historical data, by determining the acceptable range of manufacturing deviation to select the tolerance. This approach is especially useful for parts with similar features or common manufacturing processes. -Statistical Process Control, SPC: The SPC method can help monitor and control variation in the manufacturing process and provide recommendations for tolerance selection based on statistical analysis. Through real-time monitoring and analysis of process data, tolerance ranges can be established to ensure parts meet specifications.