From plumbing repairs to building backyard fences, the type of iron you choose can make a big difference in how long your project lasts and how much maintenance it needs. Black iron and galvanized iron are two of the most common materials used in everything from gas lines and sprinkler systems to outdoor railings and roofing panels. While they might look alike, they handle moisture, wear, and time in very different ways. In this article, we break down how each one is made, what it’s best used for, how they stand up to rust, and what you can expect to pay – so you can pick the right material for the job and avoid costly mistakes later on.
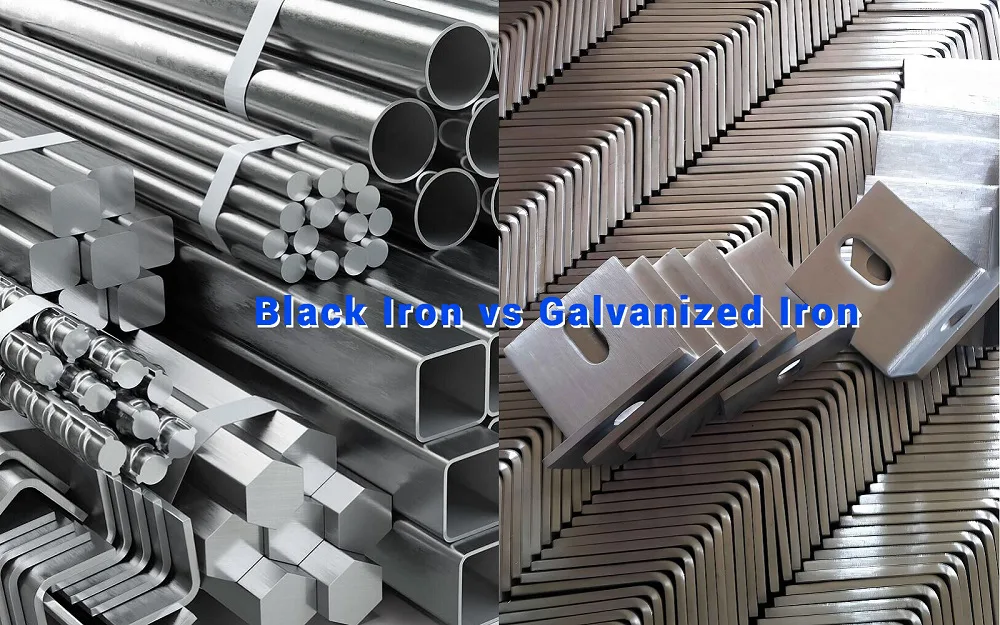
1. What is Galvanized Iron?
Galvanized iron is an iron product coated with a layer of zinc through a process known as galvanization, which protects the iron from rust and corrosion while enhancing its durability. This coating forms a protective barrier that resists moisture and environmental damage, making galvanized iron particularly useful for outdoor applications. If the zinc layer is damaged, the zinc-iron galvanic cell mechanism ensures that the iron remains protected through the sacrificial anode principle. Galvanized iron pipes are a specific application of this technique, commonly used in plumbing, construction, and industrial settings. These pipes benefit from the same rust resistance and long-lasting performance, making them suitable for carrying water and other fluids while withstanding exposure to moisture and varying environmental conditions. The combination of durability, cost-efficiency, and rust prevention has made galvanized iron and its applications, such as pipes, integral to modern infrastructure and daily life.
How is Galvanized Iron Manufactured?
The manufacturing of galvanized iron primarily involves two main processes: hot-dip galvanizing (HDG) and electrogalvanizing (EG). These methods differ in their procedures, coating characteristics, and areas of application.
1. Hot-Dip Galvanizing (HDG)
This method is ideal for large structural components and outdoor applications requiring long-term corrosion resistance, such as pipes, fences, and steel beams. The process begins with surface preparation, including degreasing to remove oil, pickling in hydrochloric acid to eliminate rust and scale, and fluxing in a zinc-ammonium chloride solution to prevent oxidation. The cleaned steel is then immersed in molten zinc at 445–465°C, where it forms a durable zinc-iron alloy layer topped with pure zinc. Afterward, the material is cooled using air or water and often passivated with chromate or environmentally friendly coatings to enhance corrosion resistance. HDG typically produces a coating thickness of 50–150 μm, offering robust protection in harsh environments.
2. Electrogalvanizing (EG)
Used for precision components like automotive parts, electronics, and appliances, electrogalvanizing involves a more controlled and refined coating process. It starts with chemical degreasing and acid activation to clean the steel, followed by electrolytic deposition in a zinc sulfate solution. Zinc ions are deposited onto the steel surface via electrolysis at 20–50°C, forming a uniform layer between 5–30 μm thick. The product may then undergo passivation with trivalent chromium or silicates and sealing with oils or organic coatings for added protection. While EG results in a smoother and more visually appealing finish, it provides a thinner layer of corrosion resistance compared to HDG.
Both methods serve different industrial needs, with HDG offering superior durability for structural use and EG delivering a fine finish for detailed, indoor applications.
Galvanized Iron Chemical Composition
The chemical composition of galvanized iron mainly consists of two parts: the iron substrate (steel) and the zinc coating. Different manufacturing processes (such as hot-dip galvanizing and electro-galvanizing) and intended applications can influence the specific composition. Below is a typical analysis:
1. Chemical Composition of the Iron Substrate (Steel)
The base material of galvanized iron is usually low-carbon steel, with common components as follows:
Element | Content Range (wt%) | Function |
---|---|---|
Fe | 98.0–99.5% | Main material, provides mechanical strength |
C | ≤0.25% | Low carbon content ensures good ductility |
Mn | 0.30–0.60% | Strengthens the steel, improves workability |
Si | ≤0.05% | Small amount reduces impurities during smelting |
S, P | ≤0.05% | Impurities that must be strictly controlled |
Common steel grades
- International: A36 (ASTM), SPHC (JIS)
2. Chemical Composition of the Zinc Coating
The zinc coating may contain small amounts of other elements to enhance performance, depending on the process:
(1) Hot-Dip Galvanized Coating
Element | Content Range (wt%) | Function |
---|---|---|
Zn | ≥99.0% | Primary anti-corrosion component |
Al | 0.1–0.3% | Suppresses excessive growth of zinc-iron alloy layer |
Pb | ≤0.07% | Improves zinc fluidity (being phased out) |
Fe | ≤0.02% | Residual impurity from the process |
Special coatings:
- Zinc-Aluminum Alloy (e.g., Galvalume): Contains 5% Al + trace rare earth elements; improves corrosion resistance by 2–6 times.
- Zinc-Magnesium Alloy: Contains 1–3% Mg; suitable for harsh environments (e.g., marine climate).
(2) Electro-Galvanized Coating
Element | Content Range (wt%) | Characteristics |
---|---|---|
Zn | ≥99.9% | High purity, uniform coating |
Ni | 0.01–0.1% | Enhances adhesion of the coating (optional) |
Fe | ≤0.02% | Residue from the electrolyte |
This composition ensures galvanized iron delivers the required strength, corrosion resistance, and durability across various applications.
Galvanized Iron Properties
Below is a detailed summary of the performance parameters and data for galvanized iron (Galvanized Iron/Steel), covering key aspects such as mechanical properties, corrosion resistance, and workability. The data is based on commonly used industrial standards (e.g., ASTM, GB/T) and practical applications.
1. Basic Physical Properties
Property | Typical Value / Range | Description |
---|---|---|
Density | 7.85 g/cm³ (steel base) | Same as standard low-carbon steel |
Melting Point | Pure zinc layer: 419.5°C | Hot-dip galvanization temperature (450–460°C) is higher than zinc’s melting point |
Thermal Conductivity | 60–70 W/(m·K) (zinc layer) | Higher than regular steel (~50 W/(m·K)) |
Thermal Expansion Coefficient | 11.5×10⁻⁶ /°C (zinc layer) | Close to steel (12×10⁻⁶ /°C), reducing thermal stress cracking |
2. Mechanical Properties
(1) Base Steel Properties (Example: Q235)
Parameter | Value Range | Standard |
---|---|---|
Tensile Strength | 370–500 MPa | |
Yield Strength | ≥235 MPa | |
Elongation (δ₅) | ≥26% | |
Hardness (HV) | 120–150 HV | Suitable for stamping and bending |
(2) Effect of Zinc Coating on Mechanical Performance
- Coating Hardness: Pure zinc layer ≈ 70 HV; Zinc-iron alloy layer (hot-dip) can reach up to 200 HV
- Fatigue Resistance: Fatigue strength increases by 10–15% after galvanizing (zinc layer inhibits crack propagation)
- Ductility Loss: Hot-dip galvanizing may reduce base steel elongation by 3–8% due to high-temperature annealing effects
3. Corrosion Resistance
Corrosion Type | Test Method / Data | Performance |
---|---|---|
Salt Spray Test | ASTM B117 | – Hot-dip: 1000–2000 hours to red rust<br>- Electro-galvanized: 200–500 hours |
Atmospheric Corrosion Rate | Rural (ISO 9223) | 0.5–2 μm/year (hot-dip layer lifespan: 20–50 years) |
Marine Environment | Within 100 meters from coastline | Corrosion rate increases 3–5×; use thicker or zinc-alloy coating (e.g., Zn-Mg alloy) |
Acid-Alkali Resistance | Safe pH range: 5.5–12 | – pH < 5: fast dissolution (>0.1 mm/year)<br>- pH > 12: passivation loses effectiveness |
4. Workability
Process | Adaptability / Data | Notes |
---|---|---|
Stamping/Forming | Limiting Drawing Ratio (LDR): 1.8–2.2 | Risk of coating peel-off: Electro-galvanized < Hot-dip galvanized |
Welding | Resistance welding efficiency: 85–95% | Zinc vapor requires ventilation; coating repair needed post-weld |
Bending | Min. bending radius = 1.5 × sheet thickness | Coating cracking likely if hot-dip zinc layer >80 μm – preheating recommended |
Paint Adhesion | Cross-cut test: Grade 0 (ISO 2409) | Phosphating or passivation pre-treatment required |
5. Coating Performance Parameters
(1) Hot-Dip Galvanizing (HDG)
Parameter | Value Range | Standard |
---|---|---|
Coating Thickness | 50–150 μm (typically 70–90 μm) | GB/T 13912-2020 |
Coating Weight | 180–600 g/m² (double-sided) | |
Spangle Size | 0.5–3 mm (shiny/spangle-free options available) | Customizable for aesthetics |
(2) Electro-Galvanizing (EG)
Parameter | Value Range | Standard |
---|---|---|
Coating Thickness | 5–30 μm (typically 10–20 μm) | ISO 2081 |
Coating Weight | 7–40 g/m² (double-sided) | |
Surface Roughness | Ra 0.4–1.6 μm | Ideal for direct painting |
6. Environmental and Sustainability Factors
Indicator | Data / Certification | Comparative Advantage |
---|---|---|
Recycling Rate | Zinc: >95%, Steel: 100% | Reduces recycling cost by 30–50% |
Carbon Emissions | Hot-dip galvanizing: 0.8–1.2 t CO₂/ton steel | Lower than stainless steel (6–8 t CO₂/ton) |
Hazardous Substances | RoHS compliant (Lead ≤ 0.1%, Cadmium ≤ 0.01%) | No hexavalent chromium or mercury |
These properties make galvanized iron a highly durable, cost-effective, and environmentally friendly material suitable for a wide range of industrial, construction, and consumer applications.
Galvanized Iron Applications
Galvanized iron is widely used across various industries due to its durability, corrosion resistance, and cost efficiency. Its applications span construction, transportation, household products, and industrial machinery, making it an essential material in modern life.
- Construction: Used in steel frames, roofs, fences, and utility poles for its rust resistance in outdoor applications. Common in scaffolding, guardrails, and temporary fences at construction sites.
- Transportation: Found in vehicle parts like brake discs, fuel tanks, and chassis for rust prevention. Used in railway tracks, guardrails, and station structures for durability.
- Household Products: Used in items like door hinges, handles, gardening tools, and shelving supports to prevent rust. Found in appliances like washing machines and refrigerators for moisture protection.
- Industrial Use: Used in factory parts like gears, bolts, and panels to resist heat, moisture, and wear. Galvanized pipes are common in plumbing and gas systems for long-term corrosion resistance.
- Agriculture and Marine: Employed in grain silos, irrigation systems, and livestock enclosures to withstand moisture. Used in docks, piers, and boat fittings to resist saltwater corrosion.
- Electrical Applications: Used in battery casings, terminal connections, and appliance housings for rust prevention and conductivity.
- Decorative Use: Applied in fences, gates, balconies, and sculptures for both durability and aesthetic appeal.
- Renewable Energy: Used in solar panel mounts, wind turbines, and infrastructure exposed to harsh weather conditions.
Ganvanized Iron Price & Cost
The price of galvanized iron is significantly affected by the base steel, zinc price fluctuations and process type. The cost of hot-dip galvanized steel sheet is usually 15%-30% higher than that of ordinary steel. The current market price is about US$890-1000 per ton (taking 1.0mm thick plate as an example), while the price of electro-galvanized steel sheet is lower due to its thinner coating, about US$800-890 per ton. The processing cost of hot-dip galvanizing process is relatively high (about US$90-150 per ton), mainly due to zinc consumption (30-50 kg of zinc per ton, calculated based on the current zinc price of about US$2700-3500/ton) and environmental treatment costs (additional US$20-45 per ton). In contrast, the initial cost of stainless steel (such as 304) is as high as US$1800-2700 per ton, while galvanized iron, with its maintenance-free characteristics, has a comprehensive cost of only 1/5-1/3 of that of stainless steel over a 30-year life cycle, making it a cost-effective choice. Optimization strategies such as the use of zinc-aluminum-magnesium alloy coatings can reduce zinc usage by 30%, further reducing long-term costs.
Average Market Price for Galvanized Iron
Form | Price Range (Approx.) |
---|---|
Galvanized Iron Sheets | $1.00–$3.50 per pound |
Galvanized Pipes | $2.00–$6.00 per foot (depending on diameter) |
Galvanized Iron Bars | $1.50–$3.00 per pound |
Galvanized Wire | $0.80–$2.00 per pound |
Galvanized Roofing | $5.00–$10.00 per square foot |
2. What is Black Iron?
Black iron typically refers to a type of steel pipe known for its dark, matte finish caused by an iron oxide coating formed during manufacturing. Unlike galvanized pipe, black iron pipe is not coated with zinc, making it unsuitable for water transport due to rust concerns but ideal for gas lines, fire sprinkler systems, and certain HVAC applications. The term can also broadly describe untreated or heat-blackened iron or mild steel used in structural, industrial, or decorative contexts. Its strength, durability, and cost-effectiveness make it a popular choice in construction and mechanical systems.
How is Black Iron Manufactured?
Black iron is manufactured by producing mild steel through the standard steelmaking process, which typically involves melting iron ore or recycled steel in a blast furnace or electric arc furnace. The molten steel is then cast into shapes such as billets, which are further processed into pipes or sheets through rolling and forming. During the final stages, the steel is not galvanized or coated with zinc; instead, it develops a dark iron oxide layer on its surface as a result of high-temperature exposure during manufacturing. This oxide layer gives black iron its characteristic dark appearance and provides limited corrosion resistance, making it suitable for specific applications like gas piping and fire sprinkler systems.
Black iron Chemical Composition
The chemical composition of black iron, also known as pig iron, varies depending on its intended application, but it primarily consists of iron with a significant amount of carbon and small quantities of other elements. These elements influence the material’s properties, such as hardness, strength, brittleness, and corrosion resistance.
Element | Content Range (%) | Function |
---|---|---|
Iron (Fe) | 90–96 | Base element providing structure, strength, and magnetic properties. |
Carbon (C) | 2–4 | Defines hardness and brittleness; higher content increases hardness but reduces ductility. |
Silicon (Si) | 0.5–3 | Improves fluidity during casting, promotes graphitic carbon, and enhances machinability. |
Sulfur (S) | 0.04–0.1 | Typically an impurity that causes brittleness; minimized during refining. |
Phosphorus (P) | 0.1–0.5 | Enhances fluidity for casting but can reduce toughness if present in high amounts. |
Manganese (Mn) | 0.5–1 | Acts as a deoxidizer, neutralizes sulfur effects, and improves strength and hardness. |
Nickel (Ni), Chromium (Cr), Copper (Cu) | ≤0.1 each | Trace elements that slightly improve corrosion resistance and mechanical properties. |
Oxygen (O), Nitrogen (N), Hydrogen (H) | Trace amounts | Impurities introduced during production that can affect quality if not controlled. |
Black Iron Properties
Black iron possesses a range of mechanical, physical, and chemical properties that make it suitable for specific industrial and structural applications. Below is a comprehensive overview of its properties:
1. Mechanical Properties
Property | Value/Description |
---|---|
Tensile Strength | 330–550 MPa (varies with steel grade); withstands moderate pressure and stress. |
Yield Strength | 200–250 MPa; suitable for structural and piping applications without excessive deformation. |
Hardness | Brinell 120–180 HB; moderate hardness depending on carbon content. |
Ductility | Good ductility; can bend and deform without breaking, ideal for forming processes. |
Impact Resistance | Reasonable under normal conditions, but may become brittle in extremely cold environments. |
2. Physical Properties
Property | Value/Description |
---|---|
Density | Approximately 7.85 g/cm³, typical for carbon steel. |
Melting Point | 1425–1540°C, depending on carbon and alloy content. |
Thermal Conductivity | About 50 W/m·K; suitable for industrial applications, though lower than copper. |
Electrical Conductivity | Lower than non-ferrous metals like copper; not typically used in electrical applications. |
Magnetic Properties | Ferromagnetic; attracted to magnets and can be magnetized. |
3. Chemical Properties
Property | Value/Description |
---|---|
Composition | Iron (Fe) with 0.1%–0.3% carbon, manganese, and trace elements depending on grade. |
Corrosion Resistance | Low; prone to rust when exposed to moisture or oxygen, as it lacks protective coatings. |
Oxide Layer | Thin iron oxide (Fe₃O₄) layer gives it a black appearance but provides minimal corrosion protection. |
4. Workability
Property | Value/Description |
---|---|
Weldability | Excellent; can be welded using standard arc, MIG, or TIG methods. |
Machinability | Good machinability; can be cut, drilled, and threaded with standard tools. |
Formability | Easily formed into various shapes; suitable for bending and rolling. |
5. Thermal and Environmental Performance
Property | Value/Description |
---|---|
Temperature Tolerance | Performs well under high temperatures; ideal for gas lines and heating systems. |
Water Suitability | Not recommended for potable water or outdoor plumbing due to high corrosion risk. |
Black Iron Applications
Black iron also has a wide range of application across various industries with the following main uses:
- Industrial: Steel production, machinery, vehicles, shipbuilding.
- Construction: Structural components, black iron pipes for gas, heating, and fire systems.
- Tools and Equipment: Tools, agricultural machinery, heavy-duty equipment.
- Cast Iron Products: Pipes, manhole covers, kitchenware, decorative castings.
- Plumbing and Piping: Gas, oil, steam, and air transportation systems.
- Heating and Fire Systems: Boilers, radiators, fire sprinkler systems.
- Historical and Decorative: Wrought iron furniture, fences, sculptures, and historical machinery.
Black Iron Price & Cos
The price of black iron typically ranges from $0.50 to $2.50 per pound or $1.50 to $5.00 per foot for pipes, depending on the form, size, and grade. It is generally more affordable than galvanized or stainless steel due to its lack of protective coatings, making it a cost-effective choice for applications where corrosion resistance is not critical. Factors such as processing, market demand, and raw material costs can influence pricing, while additional expenses may arise for maintenance, such as painting or coating to prevent rust. Black iron is widely used in construction, plumbing, and industrial applications due to its strength and affordability, but its susceptibility to corrosion can lead to higher long-term maintenance costs in certain environments. For precise pricing, contacting local suppliers is recommended, as costs vary by region and market conditions.
Average Market Price for Black Iron
Form | Price Range (Approx.) |
---|---|
Black Iron Sheets | $0.50–$2.00 per pound |
Black Iron Pipes | $1.50–$5.00 per foot (depending on diameter) |
Black Iron Bars | $0.60–$2.50 per pound |
Raw Pig Iron | $300–$500 per metric ton |
3. Black Iron vs Galvanized Iron: What are the Differences?
From the above introduction of the two types of iron, we can see black iron and galvanized iron are two common materials used in construction, plumbing, and industrial applications, but they differ significantly in properties, applications, and cost. Here we sort out the differences between black iron and galvanized iron:
1. Corrosion Resistance
- Black Iron: Lacks a protective coating, making it highly susceptible to rust when exposed to moisture or oxygen. Requires additional coatings (e.g., paint or oil) for corrosion protection in outdoor or wet environments.
- Galvanized Iron: Coated with a layer of zinc (via hot-dip galvanizing or electroplating), which provides excellent corrosion resistance. Suitable for outdoor and moisture-prone applications, such as roofing, fencing, and plumbing.
2. Durability
- Black Iron: Strong and durable for indoor use, but its lack of corrosion resistance limits its lifespan in harsh environments.
- Galvanized Iron: More durable in environments exposed to moisture, chemicals, or weather due to the zinc coating, which prevents rust and extends its lifespan.
3. Applications
- Black Iron Commonly used for: Gas lines, heating systems, and indoor structural components. Industrial applications where corrosion resistance is not critical. Temporary structures like scaffolding and fencing.
- Galvanized Iron Widely used for: Outdoor construction, including roofing, fences, and utility poles. Plumbing systems, especially for transporting water. Household items, agricultural equipment, and marine structures.
4. Appearance
- Black Iron: Has a dark, matte finish due to a thin layer of iron oxide (Fe₃O₄) formed during manufacturing.
- Galvanized Iron: Typically has a shiny or matte silver finish, depending on the zinc coating process.
5. Cost
- Black Iron: Cheaper than galvanized iron because it does not have a zinc coating or additional processing for corrosion resistance. Example: Black iron pipes cost around $1.50–$5.00 per foot.
- Galvanized Iron: More expensive due to the galvanizing process. Example: Galvanized pipes cost around $2.00–$6.00 per foot.
6. Workability
- Black Iron: Easier to weld, cut, and machine because of its simpler composition and lower surface treatment.
- Galvanized Iron: Slightly harder to weld due to the zinc coating, which can release toxic fumes during welding and requires proper ventilation.
7. Environmental Exposure
- Black Iron: Not suitable for outdoor or water systems without additional protection, as it rusts quickly in moist conditions.
- Galvanized Iron: Ideal for outdoor, marine, and wet environments, as the zinc coating effectively prevents rust and degradation.
8. Maintenance
- Black Iron: Requires regular maintenance, such as repainting or re-coating, to prevent rust in exposed environments.
- Galvanized Iron: Low-maintenance due to its inherent corrosion resistance provided by the zinc coating.
Black Iron vs Galvanized Iron FAQs
With that being said, let’s sort out the main FAQs about Black Iron vs Galvanized Iron:
Black Iron Pipe or Galvanized Iron Pipe, Which is Stronger?
Black iron pipe and galvanized pipe have similar mechanical strength since both are typically made from carbon steel. However, black iron pipe is better for high-temperature applications like gas lines, as it lacks a zinc coating that can degrade under heat. Galvanized pipe, with its zinc coating, is more durable in wet or corrosive environments, making it ideal for plumbing or outdoor use. While their structural strength is nearly identical, galvanized pipe lasts longer in moisture-prone conditions, while black iron pipe is better suited for indoor or high-heat applications.
Black Iron vs Galvanized Iron, which is Better for Gas?
When it comes to gas piping, black iron is generally the better choice over galvanized pipe. Here’s why:
- Black iron pipe is commonly used and approved for natural gas and propane distribution. It is durable, easy to thread and install, and does not have a coating that could potentially flake off and clog gas regulators or burners.
- Galvanized pipe, on the other hand, is not typically recommended for gas lines. The zinc coating inside galvanized pipe can react with natural gas, causing the coating to flake off over time. These flakes can accumulate and lead to blockages or damage to gas appliances.
Black Iron vs Galvanized Iron, Which is Better for Water?
When it comes to water piping, galvanized pipe is better than black iron due to its corrosion resistance.
- Galvanized pipe is coated with a layer of zinc, which protects the steel underneath from rust and corrosion. This makes it more suitable for cold water supply lines, especially in older homes or outdoor applications.
- Black iron pipe, in contrast, lacks any protective coating and is highly susceptible to rust when exposed to water. Using black iron for water lines can lead to corrosion, leaks, and contamination, especially in potable (drinking) water systems.