When it comes to selecting the right aluminum alloy for specific applications, understanding the differences between C355, A356, and 6061 aluminum is crucial. Each of these alloys has unique properties that make them suitable for various industrial uses, particularly in sectors such as automotive, aerospace, and construction. Today, we’re going to find out the differences between C355, A356 and 6061 aluminum alloy.
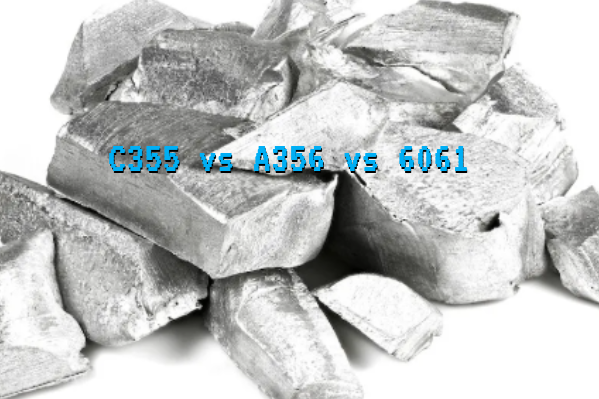
What Is C355 Aluminum?
C355 aluminum is a heat-treatable alloy that is widely used in sand casting applications due to its excellent mechanical properties and performance characteristics. One of the defining features of C355 aluminum is its composition, which includes a significant amount of copper. This copper content greatly enhances the alloy’s strength compared to more common aluminum casting alloys like A356. As a result, C355 aluminum is particularly well-suited for applications that require high strength and durability, making it a preferred choice in various industries.
The Composition of C355 Aluminum
C355 aluminum is a versatile alloy known for its strength and heat treatability. The composition of C355 aluminum is as follows:
Aluminum (Al): 92.90%
Copper (Cu): 1.20%
Magnesium (Mg): 0.50%
Silicon (Si): 5.00%
Iron (Fe): 0.20%
Manganese (Mn): 0.10% (maximum)
Zinc (Zn): 0.10% (maximum)
This specific composition allows C355 aluminum to achieve high strength and good corrosion resistance, making it suitable for various applications, particularly in the automotive and aerospace industries. The alloy is commonly heat treated to enhance its mechanical properties further, which is a significant advantage over other aluminum alloys like A356.
The Property of C355 Aluminum Alloy
C355 aluminum alloy is a heat-treatable aluminum alloy that is highly regarded for its excellent mechanical properties and versatility in various applications. One of the primary characteristics of C355 is its composition, which typically includes about 92.90% aluminum, 1.20% copper, 0.50% magnesium, 5.00% silicon, and small amounts of iron, manganese, and zinc. This specific composition contributes to the alloy’s high strength and good corrosion resistance, making it suitable for demanding environments.
One of the standout features of C355 aluminum is its ability to maintain strength at elevated temperatures. This property is particularly beneficial in applications where components are subjected to heat, such as in automotive and aerospace industries. The alloy is commonly heat treated, which significantly enhances its mechanical properties. For instance, heat treatment can increase the ultimate tensile strength and yield strength, making C355 one of the strongest sand-cast aluminum alloys available. This strength is crucial for applications requiring durability and reliability under stress.
C355 aluminum is also known for its excellent castability, which allows it to be easily shaped into complex geometries. This makes it a popular choice for manufacturing components such as structural parts, machine housings, impellers, and pump components. Additionally, the alloy’s good pressure tightness makes it ideal for applications where leak-proof designs are essential. However, it is important to manage impurity levels carefully, as high iron content can decrease ductility, while excessive nickel can reduce corrosion resistance.
The Application of Aluminum C355
Structural Components: C355 is often used in the manufacturing of structural parts due to its strength and durability. This includes components for buildings, bridges, and other infrastructure.
Machine Parts: The alloy is ideal for producing machine components that require high strength and resistance to wear. This includes gears, housings, and other critical parts in machinery.
Impellers: C355 is commonly used to manufacture impellers for pumps and turbines. Its ability to maintain strength at elevated temperatures makes it suitable for these applications.
Housings: The alloy is frequently used for housings in various equipment, including automotive and aerospace applications, where pressure tightness and strength are essential.
Pump and Valve Components: C355 aluminum is utilized in the production of pump and valve components, benefiting from its corrosion resistance and ability to withstand high pressures.
Tools and Frames: The alloy is also used in the manufacturing of tools and frames, where lightweight yet strong materials are required.
Differences Between C355, A356 & 6061 Aluminum Alloy
Composition
-C355 Aluminum: This alloy typically contains about 92.90% aluminum, 1.20% copper, 0.50% magnesium, and 5.00% silicon. It is known for its high copper content, which enhances strength compared to A356.
-A356 Aluminum: A356 generally consists of 91.1% to 93.3% aluminum, 0.15% to 1.0% copper, 0.25% to 0.6% magnesium, and 6.5% to 7.5% silicon. It is a widely used casting alloy known for good fluidity and moderate strength.
-6061 Aluminum: This alloy contains 95.9% to 98.6% aluminum, with significant amounts of magnesium (0.8% to 1.2%) and silicon (0.4% to 0.8%). It is known for its excellent corrosion resistance and weldability.
Mechanical Properties
-C355 Aluminum: C355 exhibits high strength, particularly after heat treatment, with a tensile strength of around 310 MPa and yield strength of about 270 MPa. It also maintains strength at elevated temperatures, making it suitable for high-performance applications.
-A356 Aluminum: A356 has a lower tensile strength, typically ranging from 160 to 270 MPa, and a yield strength of 83 to 200 MPa. It is known for good ductility and is often used in applications where moderate strength is acceptable.
-6061 Aluminum: This alloy has a tensile strength of approximately 310 MPa and a yield strength of about 270 MPa, similar to -C355. However, 6061 is particularly noted for its excellent corrosion resistance and good weldability, making it versatile for various applications.
Applications
-C355 Aluminum: Commonly used in high-strength applications such as structural components, machine parts, and pressure-tight housings. Its ability to maintain strength at elevated temperatures makes it ideal for aerospace and automotive applications.
-A356 Aluminum: Frequently used for castings in automotive components, housings, and valves. It is favored for applications requiring good castability and moderate strength.
-6061 Aluminum: Widely used in structural applications, including frames, automotive parts, and marine components, due to its excellent corrosion resistance and weldability