The heat treatment of aluminum alloy die casting is to change the alloy structure by quenching solid solution, controlling the heating speed to rise to a corresponding temperature, holding for a certain time, and cooling at a certain speed. Its main purpose is to improve the mechanical properties of the alloy, enhance the corrosion resistance, improve the processing type, and obtain dimensional stability.
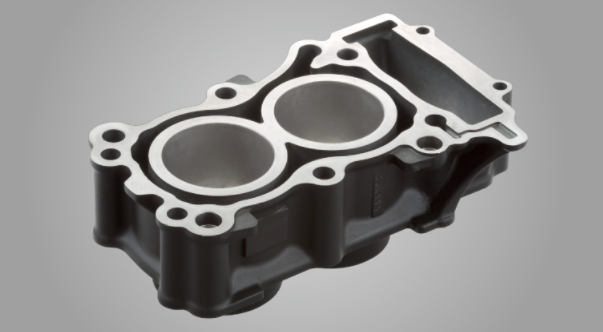
If aluminum alloy castings can be heat treated, the heat treatment process can be divided into the following four categories
1. Annealing treatment: the process of heating aluminum alloy castings to a higher temperature, generally about 300 ℃. After holding for a certain time, it is called annealing. During annealing, the solid solution decomposes and the second phase particles gather, which can eliminate the internal stress of the casting, stabilize the casting size, reduce deformation and increase the plasticity of the casting.
2. Solution treatment: heat the casting to the highest possible temperature, close to the melting point of eutectic, keep it at this temperature for a long time, and then quickly cool it to maximize the dissolution of strengthening components. This high-temperature state is fixed and stored at room temperature. This process is called solution treatment. Solution treatment can improve the strength and plasticity of castings and improve the corrosion resistance of alloys.
3. Aging treatment the process of heating the casting after solution treatment to a certain temperature, holding it for a certain period of time, and slowly cooling it to room temperature in air is called aging. If the aging strengthening is carried out at room temperature, it is called natural aging. If the aging strengthening is carried out after being higher than room temperature and holding for a period of time, it is called artificial aging. Aging treatment is a spontaneous process of supersaturated solid solution decomposition, to restore the lattice of the alloy matrix to a relatively stable state.
4. Cold and heat cycle treatment: for castings subjected to cold and heat cycle treatment, the lattice of solid solution shrinks and expands due to repeated heating and cooling, resulting in a small displacement of the lattice of each phase, making the particles of the second phase in a more stable state, to improve the dimensional stability of castings and be suitable for the manufacture of precision parts.
Aluminum alloy has no tendency of brittle fracture at low temperature. With the decrease of temperature, the mechanical properties change and the strength increases, but the plasticity decreases little. Therefore, sometimes in order to reduce or eliminate the internal stress of the casting, the cast or quenched casting can be cooled to – 50 ℃, – 70 ℃ or lower for 2-3H, Then it is heated to room temperature in air or hot water, or followed by artificial aging. This process is called cold treatment.