Cast aluminum and die cast are two common aluminum alloy fabrication processes that result in similar looking final products, but there are important distinctions between the two. Let’s break down the key differences between cast aluminum and die cast.
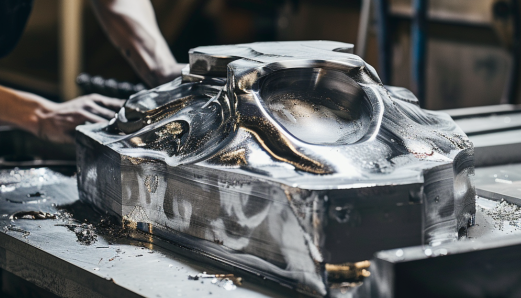
What is Cast Aluminum?
Cast aluminum is a manufacturing process whereby molten aluminum alloy is poured into reusable sand molds and allowed to solidify, forming a metal part that takes on the shape of the mold cavity. The molten aluminum is gravity fed into a single cavity sand mold, allowing it to slowly solidify which leads to a cooling rate that produces a porous, lower strength internal structure compared to die casting processes. Common cast aluminum applications include automotive engine blocks, wheels, and housings where strength and dimensional accuracy demands are not as critical as mass production volumes. It is a lower cost fabrication method well suited for prototype runs and small to medium batch sizes of parts.
What is Die Cast?
Die casting is a metal fabrication process where molten metal is injected under high pressure into reusable steel molds or dies and solidifies into a part that precisely takes the shape of the mold cavity. The molten aluminum alloy is forcefully injected into a multi-cavity steel mold utilizing injection pressures exceeding 90,000 pounds per square inch. The extreme pressure and rapid cooling rate results in a very dense, non-porous internal structure that provides improved material strength and dimensional accuracy over cast aluminum. Common uses for die casting include electronics and appliance housings, automotive transmission cases and other components requiring precision dimensions in high production volumes, as the process is well suited for mass manufacturing applications once the high initial die tooling costs are offset by economies of scale.
Cast Aluminum vs Die Cast, What’s the Difference?
Material Composition
Cast aluminum uses a molten aluminum alloy poured into a mold. Common alloying elements include copper, magnesium, manganese, silicon and zinc.
Die cast uses a molten aluminum alloy injected into a mold under high pressure. Zinc is a common alloying element that lowers the melting point.
Molding Process
In cast aluminum, molten metal is poured into a single cavity mold by gravity. Cooling is slower.
Die cast usesinjection molds with multiple cavities. Molten metal is forced into the mold under extreme pressure (>900 PSI) and cools very quickly.
Material Properties
Cast aluminum has a porous internal structure and lower strength than wrought aluminum.
Die cast has a very dense, non-porous internal structure due to rapid solidification. It exceeds cast aluminum in strength.
Applications
Common cast aluminum applications include engine blocks, wheels, housings.
Common die cast applications include enclosures for electronics/ appliances, automotive parts like transmissions that require precision.
Identification
Cast aluminum is silvery gray and porous inside if cut. Die cast is denser and often zinc alloys give it a lighter, shinier metallic appearance.
Chemical spot tests can identify die cast (turns black) vs cast aluminum (no reaction).
How Do The Manufacturing Costs & Production Volumes Compare Between Cast Aluminum And Die Cast Parts?
- Tooling/setup costs: Die casting dies are more expensive to produce than sand casting molds used for cast aluminum. This makes die casting less economical for low production volumes.
- Production costs: Once the die is made, die casting is more efficient than sand casting and has lower direct production costs per part due to shorter cycle times and less manual labor requirements.
- Minimum order quantities: Sand casting can produce parts in smaller minimum batches due to reusable pattern plates. Die casting usually requires higher minimum order quantities to justify the die cost.
- Tool component costs: Individual sand casting molds are less expensive to produce than hardened steel die casting dies with complex internal cooling lines/ejector systems.
- economics of scale: As production volumes increase, the amortized cost per part of the die Casting tooling decreases significantly. Die casting becomes more cost competitive above ~10,000-50,000 units.
- Prototyping costs: Sand casting is more suitable for initial prototyping as it has a faster turnaround. Die casting tooling takes longer to produce prototypes.