Aluminum is one of the most widely used engineering metals due to its desirable properties such as light weight, corrosion resistance and machinability. While cast aluminum provides flexibility in producing complex shapes, machined aluminum offers enhanced precision and surface quality. This cast vs machined aluminium guide discusses the key distinctions between cast and machined aluminum, two major processing routes for aluminum.
What’s Cast Aluminum?
Cast aluminum refers to aluminum that has been cast into a final shape or near-net shape using a casting process. Common casting methods for aluminum include die casting, sand casting, and permanent mold casting. Die casting uses reusable metal dies to produce parts with greater precision and more detailed features. It’s popular for industrial and automotive parts.
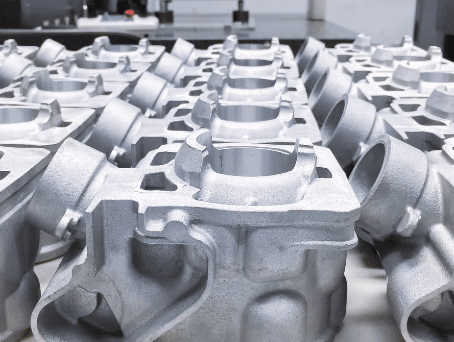
The Properties Of Cast Aluminum
Lightweight – With a density of around 2.7 g/cm3, cast aluminum is about one-third the weight of steel. This reduces material costs and part weight.
corrosion resistance – Aluminum readily forms a tough, transparent oxide layer providing excellent resistance to corrosion from weather, seawater, chemicals.
High strength to weight ratio – Alloying elements like zinc, copper and magnesium provide higher strength than pure aluminum.
Machinability – Cast aluminum can be readily machined, drilled, milled and polished to close tolerances for finish work.
Thermal conductivity – Conducts heat efficiently, suitable for applications involving heat transfer, heat exchangers, engine blocks etc.
Shock and vibration resistance – Dampens vibrations well without deteriorating in performance over time.
Fire resistance – Has a high melting point and does not emit toxic fumes on burning, used for building panels.
Recyclability – Cast aluminum scrap can be remelted and reused multiple times without quality loss.
Formability – Can be cast or formed into intricate shapes with hollow sections, pockets using die casting.
Durability – Parts made of cast aluminum alloys have longevity and remain dimensionally stable.
Low maintenance – Self-protective oxide layer reduces need for coatings to prevent corrosion.
The Disadvantages Of Cast Aluminum
One potential disadvantage of using cast aluminum is that parts produced via casting processes can sometimes exhibit issues that affect the mechanical properties and machinability of the component. Casting involves pouring molten aluminum into molds, and during the solidification process small defects such as gas pores or shrinkage cavities can form if the metal cools and contracts too quickly. These defects weaken the material and make it harder to machine with tight tolerances. Additionally, as-cast surfaces usually require cleaning or surface treatments before further processing like coating or welding since they do not have the consistency of wrought aluminum microstructures.
The Usages Of Cast Aluminum
Cast aluminum finds wide usage across many industries due to its advantageous properties. In the automotive industry, cast aluminum is used extensively for engine blocks, cylinder heads, transmissions casings, and wheels to reduce overall vehicle weight. The construction sector employs cast aluminum in architectural facades, doors, windows, and roofing for its corrosion resistance and strength. Industrial machinery leverages cast aluminum alloys for housings, pumps, conveyors, and heavy equipment frames that require durability.
In the transportation domain, cast aluminum allows lightweight design of aircraft components, train carriages, ships, and trucks. Appliances and consumer goods rely on cast aluminum for durable parts like air conditioner casings, refrigerators, washing machines, outdoor fixtures utilizing its heat transfer ability. The massive die casting capabilities of cast aluminum have also proliferated its use in electronics for enclosures, frames and structural aspects of various devices and equipment. Overall, cast aluminum meets an array of industry needs through economical production of components with tailored mechanical and physical properties.
What’s Machined Aluminum?
Machined aluminum refers to aluminum that has undergone extensive mechanical processing or machining to achieve its final shape and precise dimensions.Machining involves removing material by cutting with tools like drills, lathes, milling machines etc. It’s done on cast or wrought aluminum products like plates, bars, forgings to improve surface finish and tighten tolerances. Common machining processes are turning, milling, drilling, reaming, tapping, broaching and sawing.
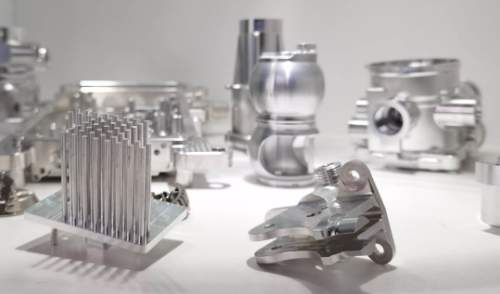
The Properties Of Machined Aluminum
Lightweight – At around 2.7 g/cm3, aluminum is roughly one-third the density of steel, reducing part weight.
High strength-to-weight ratio – Alloys like 6061-T6 offer strength close to mild steel while being much lighter.
Corrosion resistance – Aluminum’s protective oxide layer resist corrosion from weather, seawater, various chemicals.
Durability – Machined parts made of high strength alloys like 7075-T6 are very durable and long-lasting.
Machinability – Aluminum alloys can be easily machined to very close tolerances and smooth surfaces.
Conductivity – It conducts heat efficiently, suitable for heat exchange and heat sink applications.
Recyclability – Machined aluminum scrap can be recycled efficiently without loss of material properties.
Versatility – Can be machined into complex geometries like hollow shapes using multiple processes.
Dimensional stability – Machined parts made of aluminum alloys maintain tight tolerances over lifetime.
Low maintenance – No painting or coating required generally as oxidation layer protects metal.
The Disadvantages Of Machined Aluminum
One potential disadvantage of machined aluminum is the increased production costs compared to unmachined aluminum. While machining allows for extremely tight tolerances and precise dimensions that are required for many applications, the extensive mechanical processes involved make machined aluminum more expensive to manufacture in low to medium volumes. Multiple lathe, milling, drilling and finishing steps are required that not only tie up expensive CNC machinery for longer, but also result in increased wear of cutting tools due to aluminum’s work-hardening properties.
The Usages Of Machined Aluminum
Machined aluminum finds application in a wide variety of industries due to its unique combination of properties. In the aerospace industry, machined aluminum is crucial for components such as airframe structures, jet engine parts, and spacecraft elements where high strength, corrosion resistance and weight savings are critical. Automotive also utilizes machined aluminum extensively for suspension, powertrain and body components to reduce vehicle weight.
Industrial machinery leverages precisely machined aluminum alloys for manufacturing equipment, factory components and heavy machinery that requires tight tolerances and durability. Electronics and technology benefit from machined aluminum casings, housings and heat sinks for devices, equipment and infrastructure equipment given its machinability, conductivity and dimensional stability.
Cast Aluminum vs Machined Aluminum, What’s the Difference?
Production Method:
Cast aluminum involves melting aluminum alloy and pouring it into molds to solidify into near-net shapes.
Machined aluminum starts from cast/forged aluminum stock that is further processed using cutting tools like lathes and mills.
Properties:
Cast aluminum has lower strength than machined due to inherent defects from casting process.
However, machined aluminum has more stresses induced from cutting operations.
Costs:
Cast aluminum has lower upfront costs than machined aluminum due to simpler production.
But machined aluminum parts require additional expensive machining steps.
Dimensional Accuracy:
Cast parts have lower tolerances of ±0.002-0.005″ due to solidification shrinkage.
Machined parts can achieve very high tolerances of ±0.0001-0.001″.
Surface Finish:
As-cast surfaces need cleaning/treatment for further processing.
Machined aluminum has a smooth mirror-like finish from cutting operations.
Recommended Uses:
Cast aluminum is used for complex/intricate parts in mid-high volumes.
Machined aluminum is preferred for applications demanding precision/tolerances.