In this article, we detail all the causes to veining defects in die casting, quality control of raw and auxiliary materials, and everything you should know about die casting & die casting service.
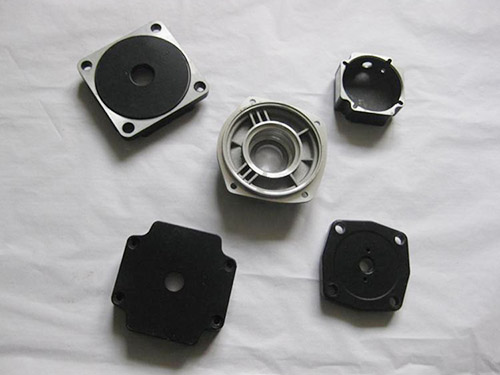
Causes To Veining Defects In Die Casting
In the production of automobile cylinder block and cylinder head, thin burr, namely vein defect, often appears in intake and exhaust port, water jacket inner cavity and inner corner of hot spot. Because the burr position is in the inner cavity, it is difficult to clean. The vein defect in the water jacket cavity will hinder the normal flow of cooling water, and even cause the engine to burn out. The veins in the intake and exhaust channels will affect the vortex characteristics of the air passage, and the aluminum die casting parts will seriously affect the engine performance Therefore, it is very important to solve the vein defect for the cylinder block, cylinder head and other automotive die castings.
The basic conditions of die casting veining defects are as follows: the thermal stress generated by phase transformation expansion is greater than the surface strength of sand core. Liquid iron is liquid and has enough fluidity. Veining defect is a kind of expansion casting defect. It is generally believed that:
● The higher the content of SiO2, the more serious the vein defect.
● The higher the particle size concentration of raw sand is, the more serious the vein defect is.
● The higher the pouring temperature, the more serious the veining defect. However, the pouring temperature is determined according to the casting structure and wall thickness and cannot be changed at will.
Die Casting Process
What is annealing of castings? The process of die casting is called annealing when it is heated to 300 ℃ and cooled to room temperature with furnace after holding for a period of time. During annealing, the solid solution will decompose and the phase particles will gather, which can remove the internal stress of the casting, keep the casting size stable, avoid deformation and enhance the plasticity of the casting.
What is solution heat treatment of castings? The casting is heated to nearly the melting point of eutectic, and then kept at this temperature for a long time. Then cool it rapidly to make the strengthening components dissolve well and keep the high temperature state until room temperature. This process is called solution treatment. Solution treatment can enhance the strength and plasticity of the casting and improve the corrosion resistance of the alloy. The effect of solution treatment is usually related to temperature, holding time and cooling rate.
What is aging treatment? Heat the die castings (after solution treatment) to the set temperature, lasting for a period of time, and cooling it slowly in the air is called aging. If aging strengthening is completed at room temperature, it is called natural aging. If aging strengthening is completed in a higher environment than room temperature and holding for a period of time, it is called artificial aging. Aging treatment is a spontaneous process of supersaturated solid solution decomposition, which can restore the lattice of alloy matrix to a relatively stable state.
What are the main problems die casting parts workshop will encounter in the selection of cutting fluid?
1. It is easy to break the cutter and tap when the aluminum die casting with high finish is required.
2. The service life and cycle of cutting fluid are short, easy to stink, and affect the working environment.
3. It is difficult to find a cutting fluid suitable for various aluminum alloy die castings.
4. The problems of corrosion and mould are easy to occur in processing ADC12 equal pressure casting.
Precautions For Use Of Die Castings
1. Poor corrosion resistance
When the impurity elements Pb, CD and Sn in alloy composition exceed the standard, the castings will be aged and deformed, showing volume swell, mechanical properties, especially plasticity, decrease significantly, and even rupture after a long time. The die castings are aged due to intergranular corrosion.
2. Time effect
The microstructure of zinc alloy is mainly composed of Zn rich solid solution containing Al and Cu and Al rich solid solution containing Zn. Their solubility decreases with the decrease of temperature. However, due to the rapid solidification rate of die casting, the solubility of solid solution is saturated at room temperature. After a certain period of time, the supersaturation phenomenon will be gradually relieved, and the shape and size of the casting will slightly change.
3. Not suitable for high and low temperature
Die casting parts should not be used in high and low temperature working environment. Zinc alloy has good mechanical properties at room temperature. However, the tensile strength at high temperature and the impact property at low temperature decrease significantly. The factors that can reduce the thermal stress, improve the high temperature strength and toughness of sand core, and accelerate the solidification of molten iron, will reduce the occurrence of veining.
Quality Control Of Raw Materials For Die Casting
The quality of die casting raw materials and auxiliary materials is the primary guarantee for the quality of die castings. Only by controlling the incoming inspection of raw and auxiliary materials can the quality of raw and auxiliary materials be controlled.
According to the quality requirements of automotive castings and relevant national standards, the “Technical Specifications for Raw and Auxiliary Materials for Casting” was formulated, including raw materials such as pig iron, ferrosilicon, ferromanganese, keyed iron, ferrosulfur, ferrochrome, copper and nickel, and auxiliary materials such as silica sand, pulverized coal and starch. Each batch of raw and auxiliary materials purchased shall be sampled and tested in time according to the requirements of “Technical Specifications for Raw and Auxiliary Materials for Casting”. Only those meeting the quality requirements can they be used.
Infiltration, Shaping And Repairing Of Die Castings
1. Infiltration of die casting
The infiltration treatment is to infiltrate the die casting into the infiltration liquid which has the function of penetration and filling, so that the infiltration liquid can penetrate into the loose part of the die casting, so as to improve the air tightness of the high pressure casting.
2. Shaping of die castings
Generally, the die castings produced according to conventional procedures will not deform. The castings with complex shape and thin wall may be deformed due to uneven force during ejection, improper holding time, collision during handling, or residual stress due to structural limitation of castings (such as warpage of castings with large plane after die casting). In general, manual or mechanical correction is allowed after deformation.
3. Repair of die casting
Casting or processed castings, found to have defects that do not meet the technical requirements, are generally scrapped, only under the following circumstances, and repair is possible.
– Castings with complex shapes, difficult to die casting or long processing cycles.
– With cast inserts, inserts are made of very precious materials, or are difficult to manufacture and cannot be reused after recycling.