Comparison Of Performance Parameters Of Die Casting Machine
Before purchasing or using a die casting machine, we must consider the performance parameters. In this guide, we make a comparison of performance parameters of die casting machine.
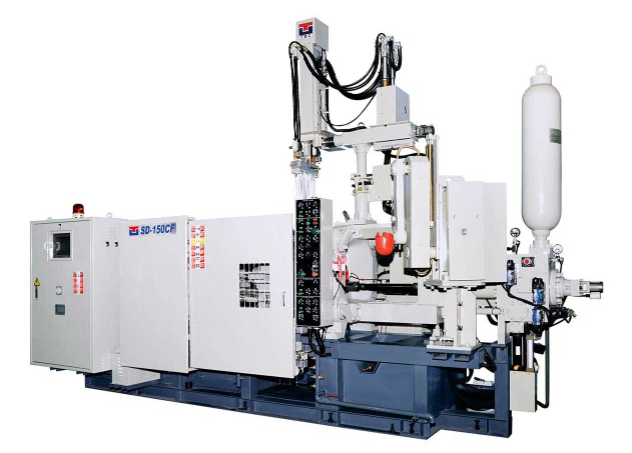
Comparison Of Performance Parameters Of Die Casting Machine
1) Clamping force
The national standard lists the clamping force index of the die-casting machine as the first, because the function of the clamping force is to prevent the parting surface of the die casting mold from separating under the action of the expanding force during injection, resulting in the splashing of liquid metal. This is an index related to the safety of die casting production. According to the national standard, the actual clamping force of the die casting machine is required to be greater than the nominal clamping force. When selecting the die casting machine, the possible release force shall be calculated according to the projected area of the workpiece and the injection specific pressure required for the production of the workpiece. The nominal clamping force of the selected die casting machine shall be greater than the release force.
When checking the clamping force, press the injection specific pressure PS for checking calculation.
P=P0*(D2/d2)
Where: P is the injection specific pressure (PA); P0 is the charging pressure of the accumulator (PA); D is the inner diameter of injection cylinder (CM); D is the diameter of the injection chamber (CM).
(2) Mold space size
One is the clearance between the column and the tie rod. This is the limit size of the width or length of the die casting mold allowed to be accommodated. This dimension shall be larger than the corresponding dimension of the die casting mold, and the actual overall dimension of the die casting mold shall be smaller than the corresponding space between columns in at least one direction, otherwise the die casting mold will not be installed.
The second is the mold holding thickness – the allowable thickness range of the die casting mold. If the actual thickness of the die casting mold is greater than (or less than) the maximum (minimum) mold holding thickness of the die-casting machine, the die casting mold cannot be locked effectively.
In addition, for the workpiece with large longitudinal size, check whether there is enough space to take the workpiece out of the die after subtracting the actual thickness of the die casting mold from the space between the dynamic setting templates in the open state.
When the length and width of the die casting mold used are small, it is suggested to add a larger backing plate to improve the stress condition of the moving and setting formwork. At the same time, because the projection area of the corresponding workpiece will not be large, there is no need for a large clamping force, and the pressure of high-pressure clamping should not be adjusted too high, so as to prolong the service life of the machine and mold.
(3) Injection position
Generally, the die casting mold is made into central injection. However, sometimes, in order to facilitate alignment or exhaust, the die casting mold needs to be designed as eccentric injection. At this time, the die casting machine is required to have the function of die base lifting. The die casting machine with this function will inject the central injection position and eccentric injection position in the sample. When designing the die casting mold, attention should be paid to its cooperation, because at this time, the water inlet of the die casting mold does not coincide with the ejection center, and its deviation is the lifting amount of the die base.
(4) Injection force
The injection force can be calculated according to the cylinder diameter of the injection cylinder of the die casting machine and the maximum injection pressure (hydraulic pressure) that the die casting machine may provide. It is an important index to measure the performance of the die casting machine. The national standard requires that the actual injection force of the die casting machine should be higher than the nominal injection force. Obviously, when the injection cylinders are the same, the higher the hydraulic pressure that the oil pump of the die casting machine can provide, the greater the injection force.
In practice, the required specific injection pressure is often selected according to the average wall thickness of the workpiece. The relationship between the injection specific pressure P and the injection force F is as follows:
P = 4P pressure / π D2
Where: P is the specific pressure of injection (PA), P is the injection force (n), and D is the diameter of injection chamber (CM).
In the design of die casting machine, in order to improve the injection force and injection specific pressure, it is suggested that the first is to select the appropriate injection cylinder diameter and injection chamber diameter. Second, the rated pressure of the hydraulic system should be increased as much as possible. A die casting machine can provide enough injection force and injection specific pressure to obtain sufficient filling speed and die cast high-quality die castings.
Sometimes, some factories use small machines to press large castings. In order to increase the pouring volume, the method of increasing the diameter of the injection chamber is adopted. If it is increased too much, the injection specific pressure of the die casting machine is reduced too much, it is difficult to obtain high-quality die castings.
(5) Maximum metal pouring volume
The maximum metal pouring amount is calculated theoretically to measure the pouring capacity of the die casting machine. Die casting is to inject molten metal into the mold cavity under high pressure and high speed, and solidify it under pressure to obtain castings. By increasing the liquid pressure of injection, sufficient specific pressure of injection can be obtained; By adjusting the flow of hydraulic oil during injection, the required ingate speed can be obtained. In the actual injection cycle, the injection speed increases from zero. In the first stage – slow injection stage, in order to facilitate exhaust, the injection speed should not be too high. However, in the second stage – rapid filling stage, the injection speed is required to be increased rapidly. Accordingly, the die casting machine is required to have the ability to quickly increase the injection speed. However, there is a process to increase the speed. After it reaches the maximum speed, with the release of energy from the accumulator, the injection liquid pressure will gradually decrease, the filling resistance will gradually increase, and the injection speed will decay quickly. In order to obtain qualified die-casting products, sufficient filling speed must be guaranteed. Therefore, the rapid filling stage of die casting should be controlled in the stage where the speed has been increased to a level that has not been reduced too low.
(6) Maximum air injection velocity
The maximum air injection speed refers to the maximum speed that can be achieved by the plunger of the injection cylinder during the no-load test of the die casting machine. This is different from the metal filling speed, but there is a close relationship between them, which is an important index to measure the injection performance of die casting machine.
(7) Parallelism of working surface of moving and setting plate
This is not only an important index to measure the machining and assembly accuracy of die casting machine, but also an important index related to the actual die locking effect. In some die casting machines, the nominal clamping force is not small, but in actual production, it is often unable to lock the die and fly water. The reason is that this index is out of tolerance.
(8) Security
Safety is a factor that must be considered when selecting die casting machine. Because the die casting machine works under high temperature and high pressure, the problem of safety is more important.
According to the national standard, the die casting machine should be equipped with safety protection devices, emergency stop buttons, and reliable measures to prevent out of control movement or abnormal action sequence. The purpose is to ensure the safety of people, equipment, molds and plants in die-casting production. When selecting die casting machine, it is necessary to examine the safety.
Since the die-casting machine uses electricity as the power source, the national standard also stipulates three electrical indicators for the safe use of electricity for the die-casting machine. Namely: ① withstand withstand voltage test of l500v for 1min. ② The insulation resistance shall not be greater than l m Ω. ③ The continuous grounding resistance shall not be greater than 0.1 Ω.
(9) Reliability
According to the national standard, the first overhaul period of the die casting machine under normal service conditions is 15000h. The operation system of die casting machine shall be flexible and reliable, and all actions shall operate well. During the specified test, all systems and devices shall not have faults or abnormal phenomena. Wear resistant measures shall be taken for the moving parts of the die casting machine and shall comply with relevant regulations.
(10) Control mode
At present, there are three control modes of die casting machine: the most original is relay control mode, which is simple, but the volume of electric box is huge and the failure rate is high. Common is PLC control. Or programmable controller control, which is a big step forward than relay control, but the operation is still complex.