Do you need copper machined parts made but don’t know which type of material to use? This article introduces three types of the most popular copper alloy in CNC machining – C110, C1100, and C11000, not only breaking down their properties, composition, material properties, machinability, and common applications but also going over the differences between them!
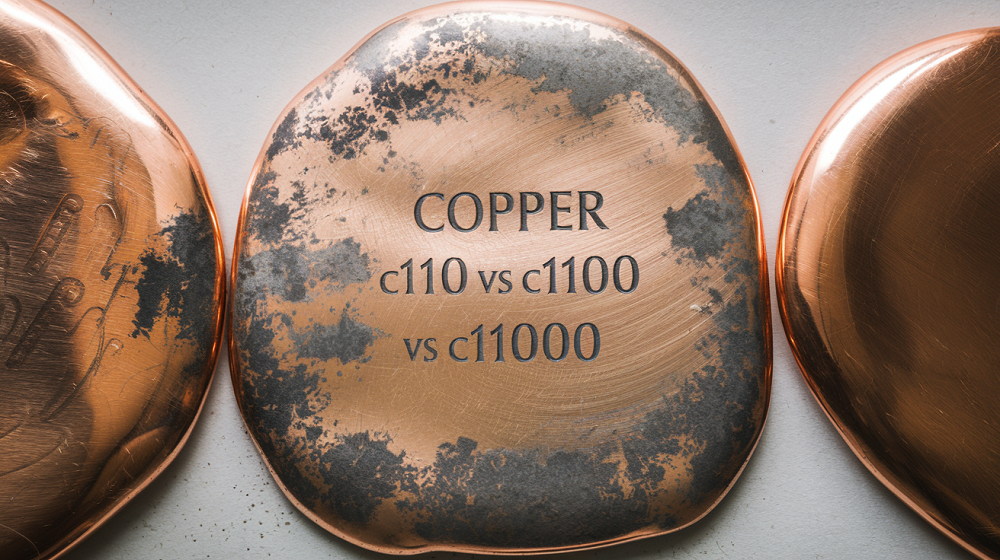
Copper C110 vs C1100 vs C11000: What are the Differences?
When it comes to CNC machining and manufacturing with copper, choosing the right alloy can make all the difference in your project’s success. C110, C1100, and C11000 are three of the most popular copper alloys used in CNC machining. Each of these alloys offers unique properties and advantages, making them suitable for a wide range of applications.
Now let’s take a detailed overview of these copper alloys and then compare them in a table so you can see the differences at a glance!
1. What is Copper 110?
Copper 110, also known as UNS C11000 and CDA 110, is Electrolytic Tough Pitch (ETP) Copper, containing 99.99% copper. Copper Alloy 110 is available in various shapes, including round, square, flat, sheet, and plate. Its excellent mechanical properties make Cu-ETP versatile for use as CNC machined copper parts in various applications, especially electrical equipment and products such as cables, overhead line conductors, generator windings, and coaxial lines due to its high conductivity.
Composition of Copper Alloy 110
Copper (Cu): 99.99%
Oxygen (O): Minimal, as it may contain trace amounts for deoxidization purposes
Material Properties (Features) of Copper Alloy 110
Density: Approximately 8.89 g/cm³
Hardness: Around 40 Rockwell B (HRB)
Yield Strength: Approximately 69 MPa (10,000 psi)
Electrical Conductivity: Excellent, around 100% IACS (International Annealed Copper Standard)
Thermal Conductivity: High, facilitating efficient heat transfer
Corrosion Resistance: Very good, especially in non-oxidizing environments
Ductility: High, allowing it to be easily formed and drawn
Annealing Resistance: Can be easily annealed for increased softness
Formability: Excellent for both hot and cold forming processes
Forgeability: Good, making it suitable for various forging applications
Machinability of Copper 110
Copper 110 has good machinability, making it suitable for CNC machining. It offers excellent ductility and thermal conductivity, allowing for precise and efficient machining processes. However, due to its softness, care must be taken to avoid tool wear and to achieve smooth finishes.
Applications of Copper 110
What is Copper 110 used for? Copper 110 is ideal for electronic applications that require freedom from harmful impurities and oxide damage or contamination. Copper 110 can also be applied in various products and industries, including heat exchanger components, automotive spark plug electrodes, plumbing fittings, electrical components, waveguides, base plates, bus bars, blade and ring terminals, cables, power transmission components, resistance welding electrodes, terminals, parts for vacuum devices, switches, circuit breakers, deposition units, electron tubes, glass-to-metal seals, and superconducting magnet components.
2. What is Copper 1100?
Copper 1100, designated as JIS C1100, is also known as Tough Pitch Copper. It primarily contains 99.90% copper, making it a high purity non-ferrous metal widely utilized in electrical applications. Copper 1100 is available in numerous forms such as wires, sheets, bars, and plates, boasting properties that make it ideal for electrical conductors, architectural uses, and various types of machinery.
Composition of Copper Alloy 1100
Copper (Cu): 99.90% or more
Oxygen (O): Present in trace amounts, influencing the material’s properties and processing characteristics
Material Properties (Features) of Copper Alloy 1100
Density: Ranges from 8.89 to 8.94 g/cm³
Specific Heat: 385 J/kg.K
Coefficient of Thermal Expansion: 17.7 x 10^-6 per °C
Electrical Conductivity: 101% IACS (International Annealed Copper Standard). Very high, making it suitable for electrical applications
Thermal Conductivity: 391 W/(m·K). Excellent, which is beneficial in heat exchangers and cooking utensils
Volume Resistivity: 0.0171 ohm.cm
Young’s Modulus: 118 GPa
Corrosion Resistance: Good, with a natural ability to resist rusting which can be enhanced by forming an oxide layer
Ductility: High, facilitating easy forming and drawing processes
Machinability: Moderate, but care must be taken due to the material’s softness and tendency to produce burrs
Machinability of Copper 1100
Copper 1100 is known for its good machinability though it requires considerations to manage its softness and malleability. It tends to stick to cutting tools and may require specific tools or lubricants to achieve smooth finishes. High-speed machining with sharp, well-maintained tools and appropriate coolant use are recommended to avoid welding to the tool surfaces.
Applications of Copper 1100
Copper 1100 is predominantly used in applications requiring high electrical and thermal conductivity. Its common uses include:
Electrical components: Such as wires, cables, and bus bars due to its excellent conductivity
Architectural applications: For roofing, gutters, and domes due to its corrosion resistance and appearance
Heat exchangers: Where its thermal conductivity plays a critical role
Automotive & Machine parts: Components that benefit from its ductility and machining ease
This copper grade combines excellent conductivity with substantial physical properties, making it a versatile choice for a wide range of industrial applications.
3. What is Copper 1100?
C11000 is a high-purity Electrolytic Tough Pitch Copper, classified under the United States Unified Numbering System (UNS). This copper alloy is widely used across various fields due to its high purity, excellent electrical conductivity, and thermal conductivity. C11000 contains at least 99.90% copper and is one of the most widely used types in the industry, especially in applications requiring high conductivity and good workability.
Composition of Copper Alloy 11000
Copper (Cu): Minimum 99.90%
Oxygen (O): Typically around 0.04%
Material Properties (Features) of Copper Alloy 11000
Electrical Conductivity: Excellent, around 100% IACS (International Annealed Copper Standard).
Thermal Conductivity: High, facilitating efficient heat transfer.
Corrosion Resistance: Good, especially in non-oxidizing environments.
Workability: Excellent ductility and formability, suitable for various fabrication processes.
Strength: Moderate strength, but can be enhanced with cold working.
Weldability: Good, though care must be taken to avoid hydrogen embrittlement.
Machinability of Copper 11000
C11000 copper alloy can be processed by conventional metal processing techniques, including machining, welding and casting.
Applications of Copper 11000
The application of C11000 copper alloy is very wide, including but not limited to:
Electrical industry: used to manufacture wires, cables, electrical connectors, switches and other conductive parts.
Electronic industry: as the substrate of printed circuit boards (PCBs) and the conductive path of electronic devices.
Construction industry: used for roofs, gutters, pipes and architectural decorations.
Heat exchangers and condensers: due to its excellent thermal conductivity, it is used in heat exchanger and condenser components.
Decoration and art: the beautiful luster of high-purity copper makes it an ideal material for making decorations and works of art.
4. Copper C110 vs C1100 vs C11000, What are Differences Between Them?
Copper C110, 1100, 11000 are compared in many aspects such as chemical composition, density, tensile strength, yield strength, and hardness.
Property | Copper C110 | Copper C1100 | Copper C11000 |
Electrical Conductivity | High conductivity, excellent for precision applications. No hydrogen embrittlement. | Very high conductivity, suitable for applications requiring high conductivity. | Good conductivity and thermal conductivity, despite lower oxygen content. |
Thermal Conductivity | Good thermal conductivity. | Same as C110, high thermal conductivity. | Maintains good thermal conductivity. |
Corrosion Resistance | Excellent in atmosphere, seawater, some non-oxidizing acids, alkalis, salts, and various organic acids. | Excellent, used in electrical equipment and heat exchangers. | Slightly decreased due to trace oxygen, but still good. |
Fabrication Properties | Excellent machinability, no hydrogen embrittlement, suitable for both cold and hot working. | Excellent plasticity, good for hot and cold pressing, welding, and brazing. | Moderate strength, good formability, suitable for welding and brazing. |
Density | 8.96 g/cm³ | 8.94 g/cm³ | 8.96 g/cm³ |
Melting Point | 1083°C | 1083°C | 1083°C |
Chemical Composition | Primarily copper, trace amounts of phosphorus to enhance strength and corrosion resistance. | Copper + silver, high purity (>99.9%), minimal impact from impurities. | Low oxygen content, impurities ≤ 0.05%, purity > 99.95% copper. |
Copper C110 vs C1100 vs C11000, Which One Is Better To Use?
With differences show on the above table, here we sum up when to choose the each type of these copper alloy for your project:
Copper C110: Known for its lack of hydrogen embrittlement and excellent machinability, making it particularly suitable for precision machining parts. Its minor phosphorus content enhances mechanical properties and corrosion resistance, ideal for architectural and electrical components where precision is crucial.
Copper C1100: Characterized by its high purity and excellent overall performance, including superior plasticity and conductivity. This makes it widely applicable in the fabrication of electrical parts and heat exchangers where high conductivity is critical.
Copper C11000: While it has a slightly lower corrosion resistance due to trace oxygen, it maintains high purity and good physical and chemical properties. Its suitability for welding and brazing makes it versatile for various industrial applications, particularly where moderate strength and good formability are required.
Each type of copper offers distinct advantages to specific applications, ensuring that engineers and designers can select the most appropriate material based on performance requirements and environmental conditions.