In the process of die casting, the mold is heated by high temperature liquid metal, and its temperature is rising. Too high mold temperature will cause some defects on die casting parts, such as bubbles, crack, hot crack, etc. at the same time, the mold material strength will decline in high temperature environment for a long time, which will cause the surface crack of the mold and reduce the mold life. In order to alleviate and solve the above problems, spraying or coating release agent is often used in die casting production. In this article, we give an overview of die casting release agents from all aspects, we analyze the features of release agent for metal die casting, aluminum die casting and zinc die casting.
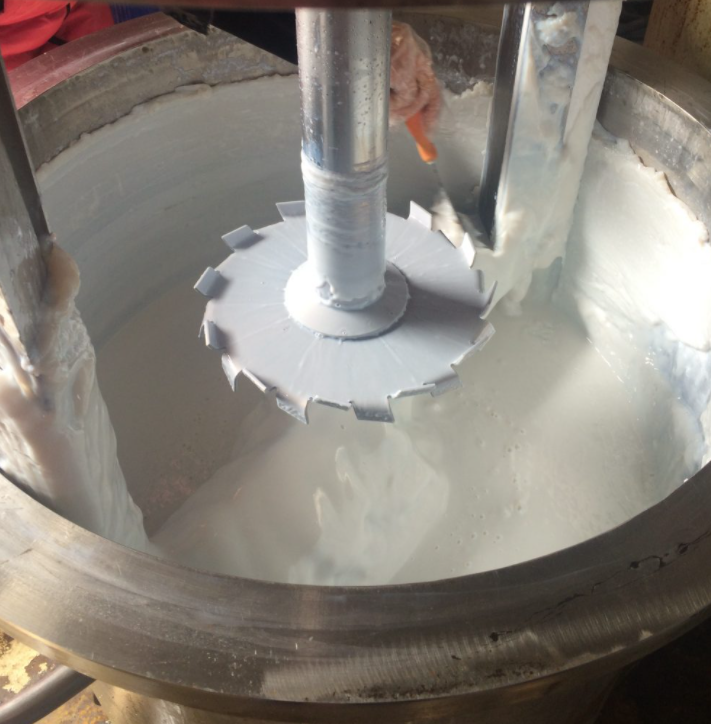
What Is Release Agent – Overview Of Release Agent
A release agent is a chemical used to prevent other materials from bonding to surfaces. It can provide a solution in processes involving mold release, die-cast release, plastic release, adhesive release, and tire and web release. It is also an auxiliary agent for the production of metal die casting products. Its main function is to help the metal die cast product to be taken out of the mold, and to keep the product integrity and post-processing. The second function is to consider the quality and style of the surface of the molded object, the fouling on the mold, the feasibility of cleaning, and the feasibility of painting.
Composition Of Die Casting Release Agent
The basic components of the release agent include different types of waxes, resins, oils, and silicone oils. And the die casting release agent is generally composed of the following components:
Main lubricant
Aluminum, zinc and other metals and their alloys have the characteristics of high pressure, high temperature, even high speed, continuous deformation of metal matrix, continuous renewal of contact surface and unsteady flow of contact surface. In order to adapt to all kinds of working conditions, lubricant formulations should not only have a variety of types, but also have different properties, so as to play a role in lubrication under various harsh friction conditions.
Base oil
Base oil plays an important role in lubrication and penetration. At the same time, it is required not to produce carbon deposit at high temperature, and it should be used as the carrier of various additives, so the selection of base oil is very important. The base oil with higher flash point and viscosity should be selected for lubricating oil used at high temperature. Compared with mineral oil, silicone oil has better stability, higher flash point and viscosity.
High temperature extreme pressure agent
Extreme pressure agent is a kind of lubricant additive which can produce chemical reaction film with metal surface through friction under high temperature and high pressure boundary lubrication state, so as to reduce friction, prevent metal contact surface scratch and fusion welding, and is an effective lubricant additive for metal surface protection. Its essence is a kind of chemical corrosion, but because the amount of corrosion is relatively small, and the film produced by this corrosion is conducive to reducing the friction between metal materials, the chemical corrosion effect of this extreme pressure agent on metal materials can be called a “limited corrosion” or “favorable corrosion” phenomenon. Extreme pressure agents containing sulfur, phosphorus, chlorine and other active atoms can form reaction films on the metal surface through tribochemical reactions.
Surface active agent
For O/W emulsion based water release agents, the raw solution should be kept at high / low temperature for a long time without any stratification, no precipitation, good dispersion and smaller emulsion size. Therefore, the selection and combination of surfactants is particularly important. The acidic medium required by cationic surfactant will corrode metal, so it is not suitable to be used in the formulation; therefore, the surfactant of the mixed system of anionic and non-ionic surfactants is generally used.
Regulator
Adjusting the pH of the release agent emulsion to neutral or weakly alkaline can make the release agent avoid bacterial invasion and deterioration and corrosion of metals. Since inorganic salts and metal oxides, which are the products of the reaction and decomposition of inorganic bases at high temperatures, are easy to deposit in the corners of the mold and are difficult to remove by the spray gun, they will grow into hard crystal grains for a long time and scratch the die castings or make the die castings uniform on the surface. There are depressions and small holes, so inorganic alkali is not suitable for the formulation of the release agent.
Release Agent For Metal Die Casting
Aluminum die casting release agent
The release agent for aluminum alloy die casting forms a protective film on the mold surface, reduces the thermal and mechanical impact of the aluminum alloy liquid on the mold material, reduces the friction and wear of the castings on the mold surface, and slows the physical and chemical effects of the aluminum alloy liquid on the mold material. The performance of the film has an extremely important impact on the life of the mold.
Release agent for zinc die casting
Today’s high surface quality requirements for zinc die-cast parts represent a great challenge for the industry. The products are used all over the world for applications as diverse as the manufacture of vehicle trims or bathroom fittings. High quality release agents provide for good demolding of cores and good lubrication of moving mold components by, at the same time, ensuring combustion with less residues.
Features Of Release Agent For Metal Die Casting
– Good lubrication and demoulding performance.
– Good cooling and thermal insulation.
– Good stability.
– High stability and effectiveness at high mold temperatures.
– Anticorrosion and antibacterial properties. Protect the diluted product from bacterial growth in sumps and spray heads.
– Compatibles with recirculating and recycling systems. Easy treatment of residues.
– Suitable for any kind of water quality and any kind of lubrication system used.
– Prevention of pipes and nozzles clogging.
– Avoiding of intermediate treatment steps between the casting and further finishing operation.