Today, let’s take a look at the differences between ductile iron and cast iron.
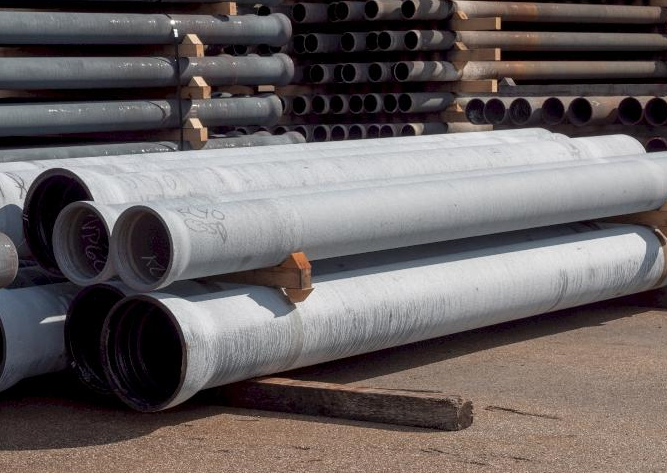
What are Ductile Iron and Cast Iron
Cast iron is a type of iron alloy that is made by melting iron and adding carbon, silicon, and other elements to form a molten mixture. The mixture is then poured into molds to create the desired shape. Cast iron is known for its excellent casting properties, and it is often used in the production of pipes, cookware, and machine parts.
Ductile iron, also known as nodular cast iron or spheroidal graphite iron, is a type of cast iron that has improved ductility and toughness due to the addition of small amounts of magnesium or other rare earth metals. Ductile iron has a microstructure of graphite nodules or spheres, which gives it better mechanical properties than traditional cast iron. Ductile iron is often used in the production of automotive components, gears, and construction materials.
Ductile iron has higher tensile strength, yield strength, and elongation than cast iron, making it more resistant to impact and fatigue. Ductile iron is also more ductile and has better machinability than cast iron. However, cast iron is typically more cost-effective and has better thermal conductivity than ductile iron.
Difference Between Ductile Iron and Cast Iron
Cast Iron vs Ductile Iron Composition
– Cast Iron Chemical Composition: The main compostion of cast iron are iron and carbon, with the carbon content usually ranging between 2% and 4%. In addition, cast iron contains varying amounts of silicon, manganese, phosphorus, sulfur, and other elements. Among these, silicon is one of the most abundant elements in cast iron and can improve its fluidity and corrosion resistance. The manganese content helps control the solidification process of molten iron, while phosphorus affects both the fluidity and solidification of the molten iron. The presence of sulfur reduces the toughness and strength of cast iron. The typical composition ranges for cast iron are approximately:
- Carbon (C): 2.4% to 4.0%
- Silicon (Si): 0.6% to 3.0%
- Manganese (Mn): 0.2% to 1.2%
- Phosphorus (P): 0.04% to 1.2%
- Sulfur (S): 0.04% to 0.20%
Cast iron may also contain other alloying elements. - – Ductile Iron Chemical Composition: Ductile iron is a type of cast iron formed by adding a certain amount of magnesium and rare earth elements to cast iron, followed by a nodularizing treatment. Compared to regular cast iron, ductile iron contains higher amounts of alloying elements. Its specific composition ranges are:
- Carbon (C): 3.6% to 3.8%
- Silicon (Si): 2.0% to 2.5%
- Manganese (Mn): 0.6% to 0.8%
- Phosphorus (P): less than 0.1%
- Sulfur (S): less than 0.03%
Additionally, ductile iron may contain other alloying elements such as copper, nickel, and chromium to improve its properties.
Ductile Iron vs Cast Iron Corrosion
Both ductile iron and cast iron are prone to corrosion, but their corrosion resistance can be improved through various methods.
– Cast iron is relatively resistant to atmospheric corrosion but is susceptible to internal corrosion caused by moisture, chemicals, and oxygen. Corrosion inhibitors, coatings, and cathodic protection can be used to improve the corrosion resistance of cast iron.
– Ductile iron, on the other hand, has better corrosion resistance than cast iron due to its higher nickel and chromium content. Ductile iron is less susceptible to atmospheric and internal corrosion than cast iron, but it can still be affected by aggressive environments. Corrosion inhibitors, coatings, and cathodic protection can also be used to protect ductile iron from corrosion.
Ductile Iron vs Cast Iron Density & Weight
– Cast iron is a dense and heavy material, with a typical density of around 6.9 to 7.8 grams per cubic centimeter (g/cm³). The exact density can vary depending on the specific composition and manufacturing process used. Cast iron is known for its high weight and is often used in applications where weight is not a significant concern, such as in machine parts, pipes, and cookware.
– Ductile iron is also a dense material, with a typical density of around 6.9 to 7.3 g/cm³. While ductile iron is slightly less dense than cast iron, the difference is relatively small and may not be significant in most applications. However, ductile iron is known for its higher strength and toughness compared to cast iron, making it a popular choice in applications where weight and durability are important, such as in automotive components and construction materials.
Ductile Iron vs Cast Iron Cost
– In general, cast iron is often less expensive than ductile iron because it is simpler to produce and requires fewer additives. Cast iron is commonly used in applications where cost is a significant concern, such as in pipes, machine parts, and cookware.
– Ductile iron is typically more expensive than cast iron due to its improved mechanical properties, including higher strength, toughness, and ductility. The addition of magnesium or other rare earth metals to the iron alloy also adds to the cost of production. Ductile iron is commonly used in applications where strength and durability are important, such as in automotive components and construction materials.
Ductile Iron vs Cast Iron Applications
– Cast iron is mainly used in fields where high strength is not required, such as automotive parts and railway vehicles.
– Ductile iron (nodular cast iron), on the other hand, is widely used in areas that require high strength and high toughness, such as components for construction machinery, lubricant pump housings, and automotive shock absorber spring seats.