CAD (Computer Aided Design), CAE (Computer Aided Engineering), and CAM (Computer Aided Manufacturing) are abbreviated as 3C. This is a very important field of contemporary computer applications and an emerging comprehensive computer application technology. It uses computers as the main technical means to process various digital and graphic information, assisting in the completion of various activities such as production scheduling, analysis simulation, evaluation, and manufacturing.
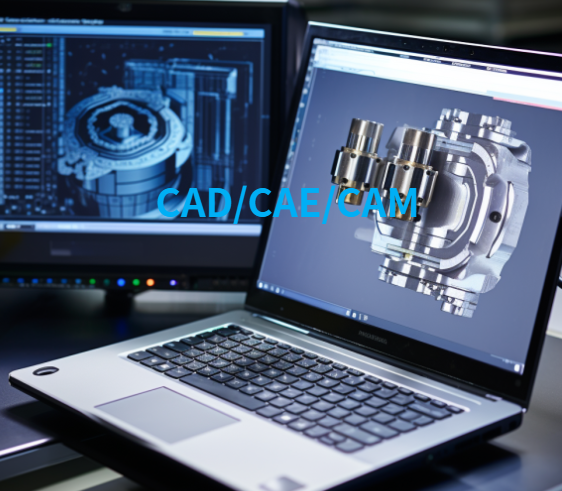
What is CAD, CAE & CAM?
CAD
CAD refers to the activities of technical personnel using computers as tools to analyze, calculate, draw, and write technical documents for products. It can transform creative thinking activities and practical experience into mathematical models and programs that computers can process, comprehensively analyze, make judgments and evaluations in the program, and control the entire design process.
CAE
CAE is an approximate numerical analysis method that utilizes computers to solve mechanical properties such as structural strength, stiffness, buckling stability, dynamic response, heat conduction, three-dimensional multi-body contact, elastoplasticity, and optimization design of structural performance in complex engineering and products. The purpose of stamping die CAE is to verify the forming process and die design results, and to optimize certain process parameters. The simulation calculation results are returned to the designers, allowing them to modify the original design based on the calculation results, reduce the workload of trial molding, and achieve optimized design.
CAM
CAM refers to the use of computers to design, manage, and control manufacturing processes. It includes both process design, CNC programming, and computer monitoring directly related to the machining process, as well as supportive activities indirectly related to the machining process.
Advantages of Mold CAD, CAE & CAM
(1) CAD/CAM can improve the quality of mold design. The computer system stores comprehensive technical knowledge related to various specialties, providing a scientific basis for mold design and process formulation. The interaction between computers and designers is conducive to leveraging the strengths of both humans and machines, making mold design and manufacturing more rational. The optimization design method adopted by the system helps to optimize certain process parameters and mold structures.
(2) CAD/CAM can save time, improve work efficiency, and shorten design cycles. The automation of design calculations and drawing greatly shortens design time. The integration of CAD and CAM can significantly shorten the cycle from design to manufacturing. For example, using a stamping die CAD/CAM system to design and manufacture molds can increase efficiency by more than 5 times compared to traditional methods.
(3) CAD/CAM can significantly reduce production costs. The high-speed operation and automatic drawing of computers greatly save labor, freeing technical personnel from heavy drawing work and freeing them from redundant calculations, verification, drawing, and programming, allowing them to engage in more creative labor. During the design process, designers can directly access graphics from the standard parts library, saving a lot of repetitive labor.
(4) With the improvement of computer simulation technology for plastic forming process, the integrated technology of mold CAD/CAE/CAM can greatly increase the reliability of molds and reduce the time for trial and repair.
The CAD-CEUS system specifically designed and manufactured for plastic molds, launched by UNISYS Co., Ltd. in Japan, is also quite distinctive. This system integrates all the functions required for plastic products from design to mold production, with a focus on the linkage between 3D design and 2D views, reflecting technological progress in humanization and integration. D-M-E Company in the United States has started to conveniently download CAD mold graphics, standard mold bases, and hot runners from the internet, and provides a variety of neutral format files. The IMOLD software developed by the National University of Singapore is based on Solidworks software and is used for designing injection molds. It can automatically generate parting lines, convex and concave molds, and other standard components for injection molds.
At present, some foreign software developers are dividing product series according to the actual production process functions, achieving the integration of CAD/CAE/CAM under network systems, and solving the problem that traditional hybrid CAD/CAM systems cannot meet the needs of actual production process division of labor and cooperation. It can be expected that the mold CAD/CAE/CAM system will gradually develop into an integrated product information management system that supports the entire process from design, analysis, management, and processing in the coming years. At the same time, the new generation of mold CAD/CAE/CAM systems are being transformed using KBE (Knowledge Based Engineering) technology, such as the artificial intelligence module KF (Knowledge Fusion) provided in UG-NX, which can integrate design knowledge into the system and recognize relevant graphics
And reasoning. The combination of numerical computation and artificial intelligence technology will be a very challenging and important task for a considerable period of time in the future.
So the basic characteristics of the modern mold industry are highly integrated, intelligent, standardized, and networked. Its pursuit is to improve product quality and production efficiency, shorten design and manufacturing cycles, reduce production costs, maximize the adaptability of the mold industry, and timely meet user needs.
Different Between CAD, CAE & CAM
CAD vs CAE:
CAD (Computer Aided Design) is used for product design and documentation.
CAE (Computer Aided Engineering) is used for analyzing and simulating designs.
CAE takes the CAD model and applies engineering principles to validate performance before manufacturing.
CAE is better for verifying that a design will meet requirements through simulation of real-world forces.
However, CAD is needed to first create the design model for it to be analyzed in CAE.
CAD vs CAM:
CAD (as above) creates the design and documentation
CAM (Computer Aided Manufacturing) is used for planning the manufacturing process.
CAM takes the CAD model and generates CNC toolpaths and programs for production.
CAM is better suited for automating programming of manufacturing equipment like CNC machines.
But CAD is required to design the product that will then be manufactured using CAM.
CAE vs CAM:
CAE focuses on simulation, verification and optimization of designs
CAM focuses on automation of the manufacturing process
CAE is more design-oriented while CAM is more production-oriented
For analysis of designs, CAE is better. But for programming manufacturing equipment, CAM is better.
In conclusion, all three are important and often used together in an integrated product development process:
CAD to design the product
CAE to validate and optimize the design
CAM to plan and automate the manufacturing of the verified design
Using all three together provides the most comprehensive digital product development solution.