The manufacturing of aluminum wheel involves various casting processes, and cast aluminum becomes a popular material due to its advantages. Here we’ll also discuss the casting process of aluminum wheels.
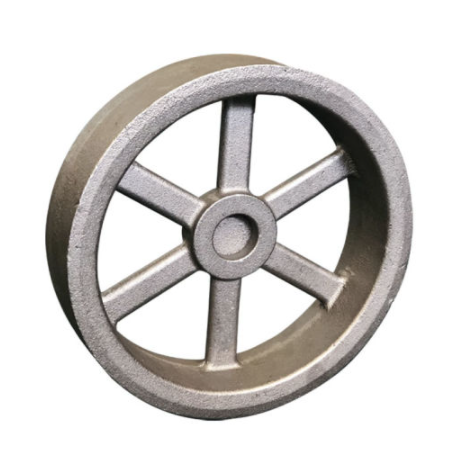
Different Manufacturing Methods for Aluminum Wheels
Aluminum wheels are commonly used in the automotive industry due to their lightweight, durability, and stylish appearance. There are several manufacturing methods for producing aluminum wheels, including:
1) Gravity casting is a common method for producing aluminum wheels, which involves pouring molten aluminum into a permanent steel mold under the force of gravity. This method can produce high-quality, precise aluminum wheels with excellent strength and durability.
2) Low pressure casting involves filling a permanent steel mold with molten aluminum under low pressure (typically around 1 bar) to create the desired shape. This method is known for producing high-strength wheels with excellent corrosion resistance.
3) High pressure casting involves injecting molten aluminum into a steel mold at high pressure (typically 7-10 bar) to create the desired shape. This method can produce high-quality aluminum wheels with excellent surface finish and dimensional accuracy.
4) Forging involves shaping a piece of aluminum billet into the desired wheel shape using a forging press. This method can produce high-strength aluminum wheels with excellent durability and weight savings.
5) Spinning involves forming a flat disc of aluminum into the shape of a wheel using a spinning machine. This method is often used for producing small or custom wheels with a unique shape or design.
Each of these manufacturing methods has its advantages and disadvantages, and the specific method used to produce aluminum wheels may depend on the size, shape, and performance requirements of the wheel.
Is Cast Aluminum Good for Wheels
Yes, cast aluminum is a popular material for wheels in the automotive industry due to its excellent strength, durability, and lightweight properties. Cast aluminum wheels are typically produced using a casting process that involves pouring molten aluminum into a mold and allowing it to cool and solidify into the desired shape. Here are some advantages of using cast aluminum for wheels:
– Lightweight: Cast aluminum is much lighter than other materials such as steel, which can help improve the overall performance of the vehicle by reducing weight and improving fuel efficiency.
– Strength: Cast aluminum has excellent strength properties, which makes it ideal for producing high-performance wheels that can withstand high loads and harsh driving conditions.
– Durability: Cast aluminum wheels are resistant to corrosion and rust, which helps improve their longevity and makes them more durable over time.
– Appearance: Cast aluminum wheels can be designed in various styles and finishes, which makes them a popular choice for drivers who want to customize the appearance of their vehicle.
But not all cast aluminum wheels are created equal, and the quality of the casting process can affect the performance and durability of the wheels. It’s important to purchase high-quality cast aluminum wheels from reputable manufacturers and to ensure that they are properly installed and maintained to help maximize their lifespan and performance.
How are Cast Aluminum Wheels Made?
Cast aluminum wheels are typically produced using a gravity casting process, which involves the following steps:
– Pattern making: The first step in casting aluminum wheels is to create a pattern of the wheel design. The pattern is typically made of wood, plastic, or metal and represents the final shape and size of the wheel.
– Mold making: Once the pattern is made, a mold is created by packing sand or a ceramic material around the pattern to create the negative space of the wheel. The mold is then removed, leaving a cavity in the shape of the wheel.
– Preparing the mold: The mold cavity is then coated with a release agent to prevent the molten aluminum from sticking to the mold. The mold is then heated to a specific temperature to further prepare it for casting.
– Pouring the aluminum: Molten aluminum is poured into the mold cavity using a ladle or automated pouring machine. The molten aluminum fills the mold cavity and takes on the shape of the wheel.
– Cooling and demolding: Once the molten aluminum has solidified, the mold is cooled to room temperature, and the casting is removed from the mold. Any excess material is trimmed away, and the casting is cleaned up.
– Finishing: The casting is then heat-treated to improve its strength and durability, and any additional finishing processes such as machining, polishing, or painting are completed.