H62 brass is a versatile alloy widely used across various industries due to its excellent mechanical properties, corrosion resistance, and cost-effectiveness. With this overview of H62 Brass, we’ll talk about its chemical composition, properties, equivalents, applications, and how it compares to 360 brass.
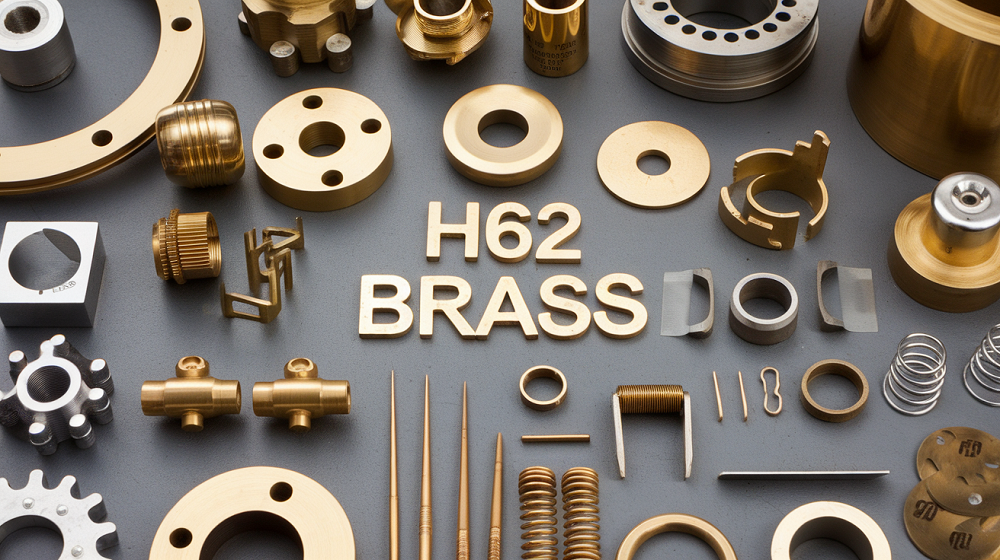
What is H62 Brass?
H62 brass is a copper-zinc alloy, with copper as the primary component (60.5%–63.5%) and zinc comprising the remainder. It is classified as an alpha-beta brass, meaning it contains both the alpha and beta phases of the Cu-Zn solid solution. This dual-phase microstructure provides a balance of strength, ductility, and corrosion resistance, making H62 brass ideal for a wide range of applications.
The “H” in H62 refers to the pinyin initial for “Huang” (meaning yellow in Chinese), while “62” denotes the average copper content. H62 is categorized as a common brass, but it can also be alloyed with trace elements to enhance specific properties.
H62 Brass Chemical Composition
The chemical composition of H62 brass is as follows:
Element | Content (%) |
---|---|
Copper (Cu) | 60.5–63.5 |
Zinc (Zn) | Remainder |
Lead (Pb) | ≤ 0.08 |
Iron (Fe) | ≤ 0.15 |
Phosphorus (P) | ≤ 0.01 |
Antimony (Sb) | ≤ 0.005 |
Bismuth (Bi) | ≤ 0.002 |
Impurities | ≤ 0.5 |
This well-controlled composition ensures stable mechanical properties, good corrosion resistance, and excellent formability.
H62 Brass Material Properties
1. Physical Properties
H62 brass exhibits the following physical characteristics:
- Density: ~8.5 g/cm³
- Thermal Conductivity: ~120 W/m·K
- Electrical Conductivity: ~27% IACS (International Annealed Copper Standard)
2. Mechanical Properties
H62 brass offers a combination of strength, ductility, and machinability. Its mechanical properties include:
- Tensile Strength: 372–540 MPa
- Yield Strength: 250–360 MPa
- Elongation: ≥30% (depending on processing state)
- Hardness: 85–120 Vickers (strip)
3. Processing Properties
- Hot Working Temperature: 650–850°C
- Annealing Temperature: 520–650°C
- Cold Working: Excellent plasticity, suitable for bending, drawing, and stamping.
- Machinability: Moderate (not as high as free-cutting brasses like 360 brass).
- Weldability: Good brazing and welding performance.
4. Corrosion Resistance
H62 brass performs well in atmospheric and freshwater environments but is prone to corrosion in harsh media like hydrochloric acid or ammonia.
H62 Brass Equivalent Grades
H62 brass has equivalents in various international standards:
Standard | Grade |
---|---|
China (GB) | H62 |
Japan (JIS) | C2801 |
Germany (DIN) | CuZn37 |
USA (ASTM) | C27400 |
Europe (EN) | CW508L |
Despite minor compositional differences, these equivalents share similar properties and applications.
H62 Brass Applications
H62 brass is used across numerous industries due to its strength, corrosion resistance, and machinability. Key applications include:
1. Electronics and Electrical
- Wires, cables, plugs, and sockets
- Switch contacts and terminal blocks
- Heat dissipation components
2. Hardware Products
- Locks, handles, hinges, and valves
- Faucets and decorative fittings
3. Automotive and Aerospace
- Radiators, brake system components, and connectors
- Air-conditioning compressor valve plates
4. Building and Construction
- Door/window hardware, curtain wall structures
- Decorative elements
5. Precision Machinery
- Springs, gears, and bushings
- Instrument housings and watch components
6. Marine and Shipbuilding
- Components exposed to seawater, such as hull fittings
7. Crafts and Jewelry
- Artistic sculptures and decorative objects
H62 Brass vs. 360 Brass, What are the Differences?
H62 brass and 360 brass are two distinct alloys, each with unique properties suited to different applications. Below is a detailed comparison:
1. Composition
The primary difference between H62 brass and 360 brass lies in their chemical makeup:
- H62 Brass:
- Copper (Cu): 60–63%
- Zinc (Zn): 37–40%
- Other elements (e.g., lead, iron): Minimal or trace amounts
- H62 is classified as a type of alpha-beta brass, meaning it has both alpha and beta phases, which gives it a balance of strength and ductility.
- 360 Brass (Free-Cutting Brass):
- Copper (Cu): 60–63%
- Zinc (Zn): ~35.5%
- Lead (Pb): ~2.5–3%
- Other elements: Trace amounts
- 360 brass is specifically a free-machining brass, designed for high machinability due to its lead content.
2. Mechanical Properties
Property | H62 Brass | 360 Brass |
---|---|---|
Tensile Strength | 372–540 MPa | 380–620 MPa |
Hardness (Brinell) | ~90–120 | ~100–150 |
Elongation (%) | ~20–45 (depending on temp) | ~10–30 (lower ductility) |
Machinability | Moderate | Excellent (100% rated) |
- H62 Brass: Offers good strength, ductility, and corrosion resistance, making it suitable for forming and bending operations.
- 360 Brass: Known for its exceptional machinability due to the added lead, but it is slightly less ductile compared to H62.
3. Applications
- H62 Brass: Ideal for applications requiring forming, bending, or drawing. Common uses: Radiator fins, heat exchangers, pipes, and decorative objects due to its good corrosion resistance and workability. Less suited for machining compared to 360 brass.
- 360 Brass: Perfect for high-precision machining and complex geometries. Common uses: Screws, nuts, gears, valve stems, and fittings. Its lead content makes it unsuitable for potable water or food-related applications in some regions due to environmental and safety regulations.
4. Corrosion Resistance
- H62 Brass: Good corrosion resistance in neutral or mildly corrosive environments. More resistant to dezincification compared to 360 brass (due to lower lead content).
- 360 Brass: Decent corrosion resistance but more prone to dezincification (selective leaching of zinc in corrosive environments). Not ideal for applications exposed to water or high humidity for extended periods.
5. Workability
- H62 Brass: Excellent for cold working processes like bending, rolling, or deep drawing. Can also be hot worked, but its machinability is moderate.
- 360 Brass: Best suited for machining operations (turning, milling, drilling, etc.). Poorer formability compared to H62 brass due to its lead content and lower ductility.
6. Cost
- H62 Brass: Slightly cheaper than 360 brass because it lacks lead and is less specialized.
- 360 Brass: Slightly more expensive due to the added lead and its optimized machinability properties.
7. Environmental Impact
- H62 Brass: Contains minimal lead, making it safer and more environmentally friendly. Often used in applications where lead-free materials are required.
- 360 Brass: Contains lead (~2.5–3%), which can pose environmental and health concerns. Many regions restrict its use in potable water systems or food-related industries.
H62 Brass vs 360 Brass, Which Should You Choose?
- Choose H62 Brass if: You need a material for forming, bending, or drawing. Corrosion resistance and environmental safety are priorities. Cost is a concern.
- Choose 360 Brass if: Machinability is the primary requirement. You are producing precision components like screws or fittings. Dezincification is not a concern in your application.
H62 brass is a highly versatile alloy with a wide range of applications, from automotive components to decorative hardware. Its balanced composition, excellent mechanical properties, and corrosion resistance make it an indispensable material in industries worldwide. While 360 brass excels in machinability, H62 brass offers greater versatility and environmental benefits, making it a better choice for many applications.