A356 aluminum is a typical Al Si Mg ternary alloy, which is a cast aluminum alloy with excellent comprehensive properties. It not only has good casting performance (good fluidity, reduced linear shrinkage, and no tendency to hot cracking), but can also cast thin-walled and complex shaped castings. Through heat treatment, it can achieve an ideal combination of high strength, good plasticity, and high impact toughness, making it the preferred material for automotive aluminum wheel hubs. Today, we’re breaking down the characteristics of A356 aluminum alloy for automotive wheel hubs as well as how to choose them.
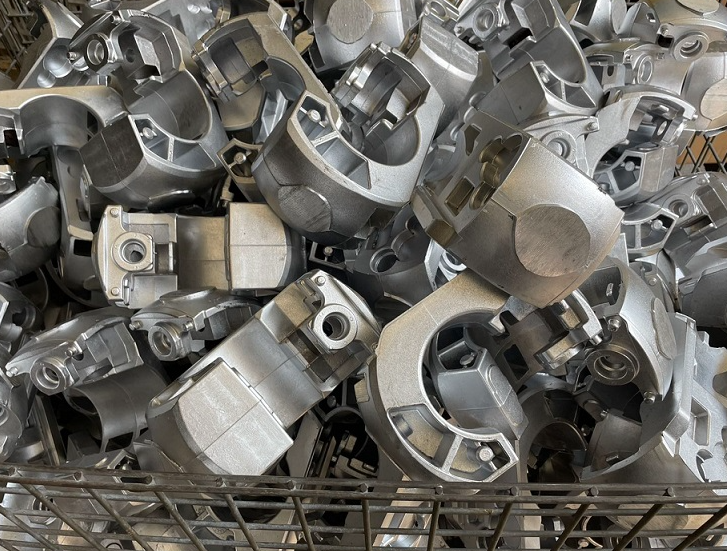
How To Choose A356 Aluminum?
A356 aluminum is a grade series in the American Aluminum Industry Association standard, which consists of three alloys: A356.0, A356.1, and A356.2, and is part of the 356 series
1.356 series is an American standard brand, while ZL101 series is a Chinese standard brand.
2. S-sand mold casting, P-metal mold casting.
3. Chinese standards also have separate provisions for the content of Pb and Sn impurities (which are classified as other impurities in the US standard): Pb<0.05, Sn<0.01 (corresponding to ZL101), Pb<0.03, Sn<0.01 (corresponding to ZL101A); The maximum Fe content of
4.356.2 alloy can reach 0.25%.
It can be seen that the composition design of the A1-7S1-Mg series of post metallization characters has the following characteristics: whether it is an American standard or a Chinese standard, their common feature is that they have the same composition range of si elements: (si-6.) 5/7.5; For magnesium elements, the required mg for casting materials is between 0.25 and 0.45; In the American standard, the requirement for magnesium in ingots has been increased by 0.05%, which is 0. 30 ^ 045, mainly considering the burning loss of magnesium element during smelting. The main difference in the chemical composition of this series lies in the regulations on impurity content. For American standards, the first letter of the grade indicates the level of its performance, so that users can determine the grade based on different application requirements. The first letter B has the highest performance, so the requirements for impurities are also the strictest. Alloys without the first letter have poor performance and are mainly used in general requirements
The A 356 series is a material between. The last digits of the brand (0, 1, 2) limit various impurities according to different situations. A 356. 0 is the material composition specified for the casting material produced; And A 356.1 and A 356. The two grades refer to the two components formulated for the production of raw materials for castings, namely ingots, according to different usage requirements. It can be noted that the current requirements for alloy ingots in automotive wheel hub aluminum are often specified using the requirements of American standard A 356.2. For Chinese standards, it can be noted that the current requirements for alloy ingots in automotive wheel hub aluminum are often specified using the requirements of American standard A 356.2. For Chinese standards, it can be noted that, At present, the requirements for alloy ingots in automotive wheel hub aluminum are often specified according to the requirements of American standard A 356.2. For Chinese standards, in the current automotive industry, aluminum for aluminum wheel hubs usually uses American standards to specify its composition and corresponding requirements
Structure & Solidification Characteristics Of A356 Aluminum
A356 alloy is an A1 Si binary alloy in which magnesium is added to form a strengthening phase Mg2Si. Through heat treatment, the aging strengthening ability of the alloy is significantly improved and the mechanical properties of the alloy are improved In the Al Si Mg ternary system, Mg2si is a stable compound that can form a pseudo binary system with aluminum, dividing the A1 Si Mg system into a+ Two ternary eutectic systems, Mg2Si+Si and a+Mg2Si+Mg5A18, have ternary eutectic temperatures of 558 C and 448 CA 356, respectively. The alloy is in a+ In the Mg2Si+Si ternary eutectic system, the equilibrium structure is primary 0+(a+Si) eutectic+Mg2Si. During cooling, aluminum precipitates first from the liquid phase, and as the aluminum precipitates, the liquid phase composition changes to a binary eutectic line, resulting in a eutectic reaction of L → 0 aluminum+Si Due to the silicon content of A 356 being only 7%, when the liquid phase composition does not reach the ternary eutectic point, the liquid phase disappears and solidification is completed. The solidified structure is primary 0+(a+si) eutectic. After solidification, the aluminum solid solution containing Si and Mg elements precipitates Si and Mg2Si during further cooling.
The microstructure at room temperature is primary 0 aluminum+(a+Si) eutectic+Mg2 SiO. During the casting process with a fast cooling rate, the secondary phases Si and Mg2Si are dispersed and difficult to distinguish, but exhibit a+(a+si) eutectic as shown in Figure 3. Under actual casting conditions, i.e. under non equilibrium solidification conditions, in addition to the basic phase, a small amount of impurity phases composed of a+Mg2Si+Si ternary eutectic and impurity iron, as well as some complex multicomponent eutectic phases, can also appear. The impurity phases mainly include Q (Fe3SiAl12) β (Fe2Si2A19) and A18ElMg3Si6. These needle like impurity phases can disrupt the continuity of the matrix and seriously affect the properties of the alloy, especially the plasticity and impact toughness of the material. This form has a bad impact on the mechanical properties of the material, and if not taken seriously, it will affect the properties of the alloy, especially the plasticity and impact toughness of the material. This form has a bad impact on the mechanical properties of the material, and if no corresponding measures are taken, the distribution of the silicon phase morphology will be changed, Materials are difficult to have practical value.
Melt Tissue Treatment Of A356 Aluminum
Melt microstructure treatment is a general term for the modification treatment and grain refinement treatment carried out during the melting process of aluminum alloys. In order to achieve good performance synthesis, A356 aluminum must undergo modification and grain refinement treatment during melting.
1. Modification treatment of A356 aluminum
A356 aluminum contains about 7% silicon phase, which mainly exists in the form of eutectic silicon in the matrix. In untreated alloys, silicon phase is distributed in a strip like form on the aluminum matrix. The brittle silicon phase in the strip like form can disrupt the continuity of the aluminum matrix, seriously affecting the mechanical properties of the alloy, especially its plasticity and impact toughness. The modification treatment of A356 aluminum is to improve the shape, size, and distribution of silicon phase in the alloy by adding some trace elements, thereby effectively minimizing the adverse effects of strip like silicon on its relative properties.
The modification phenomenon of Al si alloy was observed in France in 1920 Pacz discovered it. Adding a small amount of sodium to the A1 si alloy melt can cause significant changes in the morphology and size of the eutectic silicon phase, resulting in the spheroidization and fibrosis of the original flake silicon, effectively improving the mechanical properties of the alloy. This alloy, which was originally not applicable in industry, has been transformed into a widely applicable casting alloy with good comprehensive properties. However, in the long-term industrial application process, it has been found that sodium deterioration has the problem of premature decay and failure. The deterioration effect of sodium can only last for several decades, making its application very inconvenient and the stability of deterioration very poor. This has led to the development and research of long-lasting detergents.
The modification of A356 aluminum is currently mainly carried out using strontium (Sr). Strontium modification has a good long-term effect, which can maintain the modification effect for up to 5 “8 hours. Due to this characteristic, this modification method is widely used in current aluminum wheel casting production. However, research has shown that the addition of strontium increases the gas absorption of aluminum melt. Therefore, corresponding measures must be taken in the melting process to prevent alloy gas absorption.
2. Refining Grain Treatment of A356 aluminum
Production practice has proven that refining the microstructure can effectively improve the properties of alloys. The basic principle of grain refinement treatment for alloys is to add a small amount of substances that can form heterogeneous nucleation to the alloy melt, generating a large number of crystalline cores in the melt, allowing the alloy to obtain fine grains during solidification. For A356 aluminum, microstructure refinement mainly refers to the grain refinement of the alloy’s matrix – a aluminum solid solution. Usually, a small amount of Ti and B are added during the melting of A356 aluminum. The A13T formed by titanium and aluminum can serve as the crystalline core of aluminum solid solution, playing a heterogeneous core role and refining the microstructure of aluminum alloy.
Heat Treatment Strengthening Of A356 Aluminum
The solid solubility of magnesium and silicon in aluminum varies greatly with temperature. This characteristic gives A356 aluminum a good possibility of heat treatment strengthening. In industry, heat treatment strengthening can be achieved through quenching and aging heat treatment (usually using T5 specifications).
The melting point of a+Mg2Si+si eutectic is 550C, so the quenching temperature of A356 aluminum should be 535C below this temperature. At this temperature, after 30 minutes, the Mg2si phase has completely dissolved into the solid solution. According to the actual production situation, due to the uneven structure of castings, it is usually required that the insulation time be no less than 2 hours. Quenching can be carried out in cold water or in hot water (70C 100C) depending on the wall thickness and complexity of the parts. The most commonly used aging specification is heating to 150C ‘160C after quenching and holding for 3 “5 hours. Increasing the temperature or extending the holding time can significantly reduce the plasticity of A356 aluminum.
Research has shown that during the aging process, Mg and Si precipitate from aluminum in the following manner:
1. Initially, atoms migrated in the direction of magnesium and silicon atoms approaching each other, and recombined to form a transition phase β ‘, The recombination of atoms in a solid solution often leads to distortion of the crystal lattice.
2. Subsequently β’ Transition phase nucleation, forming a hexagonal lattice β’ Phase. Due to the lack of coherent relationship between the phase and the matrix, the distortion of the crystal lattice leads to the accumulation of a large number of dislocations, which is the reason why quenching and aging strengthen A356 aluminum.
3. Furthermore, a stable hexagonal lattice is formed β- M g 2S i phase. When aged at a lower aging temperature, the solid solution precipitates stably β- The progress of m g2Ss i phase is very slow, but at high temperatures (at 300C), it only takes 30 mi n to completely precipitate.
The particles of Mg2Si phase precipitated during aging are very small, and even at high temperature aging at 300C, the particle size of Mg2Si phase is only a few hundred nanometers. Therefore, for A356 aluminum, its strengthening phase is difficult to observe under a microscope.
Advantages Of A356 Aluminum Melting For Wheel Hubs
Automotive wheel hubs are key components related to automotive safety, and there are strict requirements for the mechanical properties of automotive wheel hub materials. Not only should it have sufficient strength, but also good plasticity and impact toughness. At the same time, there are also high requirements for the internal metal quality of aluminum wheel hub castings. Thus, the material requirements for making aluminum wheels have been greatly improved. Therefore, high requirements are put forward for the melting of A356 aluminum used in wheel hubs. In summary, there are the following
Several Requirements
For A356 aluminum used in automobile wheels, there are strict requirements for its chemical composition, especially for the control of its impurity content. A356 aluminum ingots provided for wheel hubs must comply with A356 2 standards are required. For iron content, it should be controlled at 0 Below 12%, other impurities such as Cu, Zn, Pb, Ca, etc. have a very low control range. This puts forward very high requirements for the composition control of smelting. Due to the high requirements for the internal metal quality of aluminum wheel hub castings (with a needle hole requirement of level 1 and no defects such as oxidation inclusions, shrinkage porosity, cracks, etc.), strict requirements are put forward for the metallurgical quality of aluminum melt used in casting. Strict control is required for the hydrogen content and purification level of the molten liquid.
In order to achieve good comprehensive performance of wheel hub aluminum, special requirements have been put forward for the melt structure treatment of A356 aluminum aluminum melt. Both the modification treatment of silicon phase and the grain refinement treatment of aluminum solid solution must meet high standards. It is precisely because of such strict requirements that the characteristics of A356 aluminum melting are highlighted. The selection of raw materials for preparing A356 aluminum is the first step in melting qualified A356 aluminum. Both the chemical composition of the raw material (including the content of its main alloying elements and various impurity elements) and the metallurgical quality of the raw material (whether it is gas content or impurity content) must be strictly controlled according to requirements. Especially if we want to use waste aluminum to refine A356 aluminum for car wheels, control in this regard is even more important. It is imperative to establish a quality control system for waste aluminum sorting, which is the first step to ensure the production of qualified A356 aluminum.
It is necessary to strictly control secondary pollution during the melting process, which is the second characteristic of producing aluminum A356 aluminum for automotive wheel hubs. Practice has shown that the quality of aluminum liquid is to a large extent_ It will depend on whether there is secondary pollution during the melting process of the alloy, especially for the highly demanding aluminum liquid used in automotive wheels. Effectively preventing the reaction of aluminum liquid with furnace lining and gas during the smelting process, controlling the increase in iron, inclusions, and element burning loss during the smelting process, and solving the problems of aluminum liquid suction and oxidation during the smelting process will be the core points of the smelting technology for producing this high-quality A356 aluminum for automotive wheels.
The most effective melt treatment process for preparing A356 aluminum is another characteristic during the melting process. This may increase some processing costs, but it is necessary. The treatment of melt has two parts: purification treatment of melt and control treatment of melt structure. Purification treatment is to control the hydrogen content and oxidation inclusions in the molten liquid to a minimum; Melt structure control is the use of effective modification treatment and grain refinement treatment to optimize the alloy structure and improve the alloy structure and properties.
In the melting of A356 aluminum, in order to ensure its metallurgical quality requirements, the most effective melt treatment process is usually used to complete its melting process. Developing efficient, high-quality, and pollution-free aluminum alloy melt purification and modification treatment technology will achieve high-quality recycling of waste aluminum for the production of automotive wheel hub aluminum.
Technical difficulties to be overcome in engineering. With the development of human society, transportation vehicles represented by automobiles have increasingly become an essential component of people’s lives. The automotive industry will inevitably witness rapid development. Due to the requirements of lightweight and energy-saving in automobiles, the application proportion of aluminum wheels in automobiles is increasing. The demand for wheel hub aluminum is bound to increase.