Residual stress is an inevitable product of rapid heating and rapid cooling, which is inherent to the laser powder bed fusion process. We summarized ways to reduce residual stress in metal 3D printing.
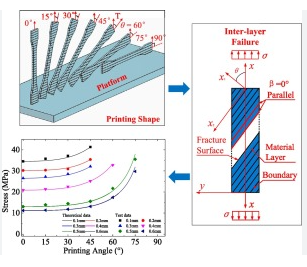
Each machined layer of metal 3D printing is formed by melting metal powder and bonding it to the previous layer. This layer-by-layer stacking process enables metal 3D printing to create complex metal die-casting parts.
- 1. Preparation work: First, the metal powder needs to be prepared, which is usually made of metal materials. Then, spread the metal powder evenly on the printing platform.
- 2. Scanning trajectory: Based on the required part shape and size, the computer generates a series of slice models. Each slice model represents a processing layer. A laser or electron beam scans the profile of the slice model.
- 3. Melted powder: The high energy of a laser beam or electron beam melts metal powder. This high-energy heat source instantly heats the powder above its melting point, causing it to melt into liquid metal.
- 4. Bonding layer: After the molten metal powders cool, they resolve and bond with the previously processed layers. The formation of this bonding layer allows the new processed layer to be tightly connected to the previous layer.
- 5. Repeat the process: After completing one layer, the printing platform will drop a fixed distance to allow the next layer to be printed. Then, repeat the above steps until the entire part is printed.
The accumulation of stress can cause part deformation, especially in parts with larger cross-sections. This can cause the edges of the part to curl up or pull away from the supports. In extreme cases, stresses may exceed the strength of the part, causing it to undergo destructive cracking. This situation usually occurs in parts with larger cross-sections, because the shear force acts over a longer distance due to the large interface, thereby increasing the stress on the part.
How to minimize residual stress
One way to solve this problem is to change the scanning strategy and choose the method that best suits the part geometry being machined. When we fill the center of the part with a laser trace, we typically move the laser back and forth, a process called “scanning.” The mode we choose affects the length of the scan vector and therefore the level of stress that may build up on the part. The shorter the scan vector, the smaller the residual stress.
1. Detour Scan Mode
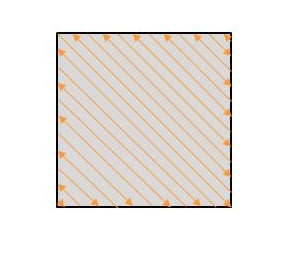
- -Rotate 67° after each layer is scanned
- -Higher processing efficiency
- -Residual stress gradually increases
- – Suitable for smaller and thinner features
2. Stripe Scanning Mode
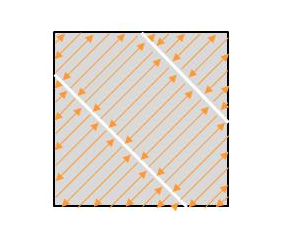
- -Residual stress is evenly distributed
- -Suitable for large parts
- -Processing efficiency is higher than checkerboard scanning mode
3. Checkerboard Scanning Mode
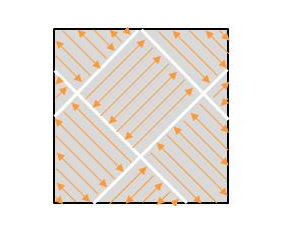
- -Each layer is divided into several 5 x 5 mm island areas
- -After each layer is scanned, the overall pattern and each island area are rotated 67°
- -Residual stress is evenly distributed
- -Suitable for large parts
We can also rotate the direction of the scan vector as we move from one machining layer to the next so that the stresses are not all concentrated in the same plane.
Residual Stress Design Tips
Design recommendations for managing residual stress in additive manufacturing include the following:
- 1. Optimize process parameters, such as laser power, scanning speed, and layer height.
- 2. Use preheating and post-heating
- 3. Pay attention to changes in cross-section
- 4. Avoid large areas uninterrupted melting
- 5. Hybrid processing to integrate thicker base plates into additively manufactured parts
- 6. Use thicker processing pallets where stress may be higher