After the assembly of the new mold is completed, it is necessary to complete the machine installation and sampling, which means taking some products as samples and going to the quality control department for dimensional measurement to see if they are qualified. After completing this step, the mold will proceed to the mass production stage. During the mass production process of mold-making, various structural and design issues are likely to arise.
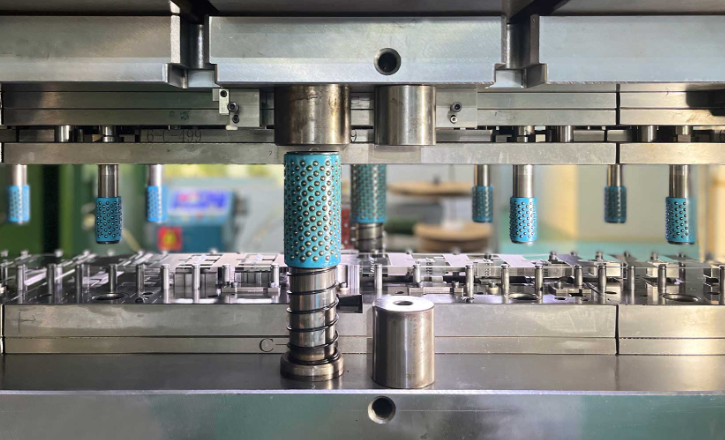
1. Tensile (deep) fracture
Reason:
- -The gap between the convex and concave molds is too small (including the overall gap and the local gap caused by the deviation of the convex and concave molds)
- -The concave mold has no rounded corners, and the roughness is too large
- -The material is too hard and has poor plasticity
- -The drawing height exceeds the limit of material plastic deformation (the number of drawing times is one)
- -The second deep drawing material was not in place
- -Insufficient edge pressing, wrinkling or depression at the edge of the protrusion after deep drawing
Improvement measures:
- -Trim the gap between the convex and concave molds to the normal value
- -Grind to normal value according to product requirements
- -If the material exceeds the specifications too much, replace the material, and increase the R angle and brightness of the concave mold accordingly to avoid it
- -It can be deep drawn several times
- -Adjust the positioning to ensure correct positioning
- -The rubber material plate of the concave convex mold adds elasticity and increases the edge pressing force
2. Bud breakage and deviation
Reason:
- -The pre-punch edge of the sprouting punch is broken
- -The convex and concave molds are offset (one-time sprouting)
- -The gap between the punch and the die is too small (pre-punching)
- – The burrs of the pre-punched hole are too large or the punch is broken and the hole is not punched out.
- -The punch is broken (the working part of the sprouting punch is broken)
Improve strategy:
- -Replace the sprouting punch
- -Adjust the position of the convex and concave molds
- -Adjust the gap between the convex and concave molds to a moderate level
- -Replace the pre-punch head
- -Replace the sprouting punch
3. The sprouting height is not high enough
Reason:
- -The pre-punched hole diameter is too large
- -The working part of the sprouting punch does not enter the die deeply enough
- -The punch diameter is too small and the gap between the punch and the die is too large (or the die diameter is too large)
- -The pre-punched material is misaligned when it arrives at the germination station, causing one side to be higher and the other to be lower after germination.
Improve strategy:
- -Change the pre-punched hole to the appropriate diameter (if the pre-punched hole is too small, it will result in higher height after sprouting)
- -Lengthen the working length of the sprouting punch
- -Modify the sprouting punch to the required diameter and the same for the die
- -Adjust the positioning of the two work stations of sprouting or pre-punching, depending on the position of the sprouting hole
4. Unsmooth material removal
Reason:
- -Template magnetism too high
- -Positioning too tight
- -Failure of the stripper pin spring (the same applies to the stripper plate)
- -No stripper pins on the stripper plate
- -The increase in extrusion width of the material under pressure is caused by poor positioning in the subsequent process
- -Poor flatness of material deformation
- -Insufficient positioning on the mold after product folding or forming
- -The slider is stuck and the movement is not smooth
- -For composite molds, the material and waste are not completely separated
Improvement measures:
- -Demagnetize the template
- -Adjust positioning based on the correctness of product positioning
- -Replace the stripper pin spring (the same applies to the stripper plate)
- -Add a top material pin to the stripper plate
- -It is best to use internal localization or locate in a location without variation
- -Adjusting the flatness of the material
- -Increase the yield on the mold
- -Trim the slider to make it smooth
- -Add top material pins to the upper and lower molds to ensure smooth separation of materials and waste materials
5. Screw breakage: divided into normal damage and abnormal damage
Reasons for normal damage:
- -The stress design of the screw itself is not enough (the specifications are wrong or the quantity is not enough)
- -The material of the screw itself is too poor
- -The normal wear and tear of the screw has been reached and the screw is broken.
Improve strategy:
- -Enlarge the size of the screws, such as increasing the number of M8 or M10 (it will not be enough depending on the actual situation)
- -Replace screws with new material
- -Maintenance mold pair replacement
Abnormal damage:
- -The two boards are misaligned and forcibly tightened
- -The convex-concave gap is too small (especially in forming molds)
- – For molds with air cushions, the ejector pin is too long and the air cushion pressure is too large, causing the lower mold screws to break.
- – Folding, forming die, stamping two pieces or punching twice
Improve strategy:
- -Ream or re-drill holes
- -Adjust the gap between convex and concave molds
- -Standardization of ejector pins and mold air cushion plates
- – Try to avoid punching twice or two pieces of material