Molding shrinkage is a very important physical phenomenon in the production of plastic injection-molded products. To produce injection-molded products with the desired dimensions and shapes, it is essential to accurately understand this physical phenomenon. So here we will talk about the injection molding shrinkage for plastic and metal. We will cover the causes of shrinkage in plastic and metal injection molding, the shrinkage rate chart for different materials, and how to calculate shrinkage in injection molding to reduce even avoid the defect!
What is Mold Shrinkage in Injection Molding?
Mold shrinkage is the difference between the dimensions of the mold cavity and the final dimensions of the molded part after it has fully cooled. When materials like plastic or metal are molten, they expand. Once the material is injected into a mold, it cools and solidifies. As the material cools, it contracts, leading to a slight reduction in the final size of the molded part compared to the dimensions of the mold cavity. Shrinkage Rate refers to the ratio of the dimensional difference between the size before shrinkage (the mold’s dimensions) and the size after shrinkage (the molded product’s dimensions). The term is commonly used in plastics and metal injection molding industries.
What Causes the Mold Shrinkage & Affects the Rating?
Note that the molding shrinkage rate is affected by the following factors:
Type of molding material: The basic shrinkage rate range is determined by the type of plastic. However, there are subtle differences between material manufacturers and material grades.
Cavity surface temperature: The shrinkage rate is influenced by the cavity surface temperature during the molding process. Generally, higher temperatures tend to result in larger shrinkage rates.
Holding pressure × Holding time: The shrinkage rate is also affected by the product of the holding pressure level and holding time after resin filling. Generally, higher holding pressure and longer holding time tend to result in smaller shrinkage rates.
Thickness of the molded product: The shrinkage rate is also influenced by the thickness of the molded product. Thicker parts tend to have larger shrinkage.
Molding Gate shape: The gate shape and size also affect the shrinkage rate. Generally, gates with larger cross-sectional areas tend to result in smaller shrinkage. Side gates tend to have smaller shrinkage rates compared to pin-point gates or submarine gates.
Presence of additives in the molding material: There is usually a significant difference in shrinkage rates between natural materials and those containing glass fibers. Materials with glass fibers tend to have smaller shrinkage rates.
Plastic Injection Molding Shrinkage
Resins (plastics) expand and contract in volume with changes in temperature and pressure. Factors that affect the shrinkage of plastic molded products also include the molding conditions and the shape of the product being manufactured.
– Molding conditions (resin temperature, mold temperature, cooling time, holding pressure¹⁾, etc.)
– Shape of molded product (dimensions, thickness, etc.)
– Differences in shrinkage rate for each type of plastic (differences in density)
Below we use this table to more concisely and clearly list the main factors affecting mold shrinkage:
Factors Affecting Plastic Molding Shrinkage Rate | ||
Factor | Condition | Shrinkage Rate |
Plastic Density | High | Small |
Low | Large | |
Plastic Temperature | High | Large |
Low | Small | |
Mold Temperature | High | Large |
Low | Small | |
Cooling Time | Long | Small |
Short | Large | |
Holding Pressure | High | Small |
Low | Large |
How To Calculate the Shrinkage in Plastic Injection Molding?
Molding shrinkage refers to the reduction in volume that occurs after the resin injected into the mold is cooled. The volume of the resin decreases as it solidifies from a molten state. The ratio of this decrease in volume is called the “shrinkage rate.” For example, the shrinkage rate of ABS resin ranges from 4/1000 to 9/1000. This means that an object with a total length of 1000mm will shrink by 4mm to 9mm. Therefore, in order to make precise products, we not only need to know the shrinkage rate of the material but also need to calculate the exact size of the product mold. Below we will tell you how to calculate the shrinkage in Plastic Injection Molding:
Plastic Mold Shrinkage Calculation:
The shrinkage rate of a molded product can be calculated from the dimensions before shrinkage (mold dimensions) and the dimensions after shrinkage (molded dimensions).
Plastic Mold Shrinkage Rate Formula: S (%) = (Dm – Dp) / Dm
Where:
S: Plastic Mold Shrinkage Rate
Dm: Dimension of the mold cavity
Dp: Dimensions of the molded product at room temperature (usually 20°C) (mm)
Length After Shrinkage = Dimensions of the molded product at room temperature
Therefore, the mold needs to be made larger than the actual target dimensions.
For example, for a molded product using resin with a shrinkage rate of 4/1000 and aiming for a size of 100mm: 100mm x 1.004 = 100.4, so the mold dimensions need to be 100.4 mm.
Plastic Mold Shrinkage Chart
Based on the above calculation method, we have calculated the general shrinkage rate of plastics in injection molding. These data help us design molds more conveniently and accurately.
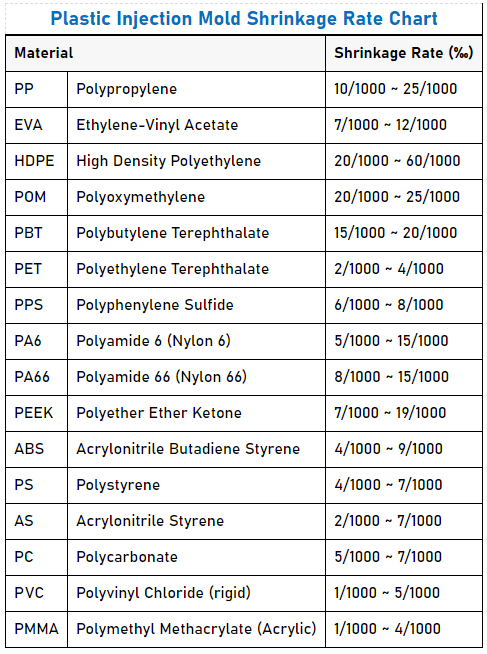
The mold shrinkage chart covers two types of plastics (resins) used in injection molding: crystalline resin & amorphous resin. A state in which atoms and molecules are regularly arranged is called a “crystal,” and plastics have some degree of crystallinity. Crystalline resins have a large shrinkage rate. Resins with a shrinkage rate of over 10/1000 are crystalline resins.
How To Calculate the Mold Dimension with Plastic Molding Shrinkage?
So now, if you know the dimensions of molded product and the type of plastic used, you can calculate the mold dimensions from the shrinkage rate of each resin:
Plastic Mold Dimension Calculate Formula: Dm = (100 x Dp) / (100 – S)
Where:
S: Plastic Mold Shrinkage Rate
Dm: Mold Dimensions (mm)
Dp: Dimensions of the molded product at room temperature (usually 20°C) (mm)
During actual molding, the part may shrink more than expected, or may not shrink at all. In this case, the shrinkage rate can be controlled to some extent by adjusting the molding conditions. However, there is a limit to how much dimensional control can be achieved through molding conditions. Therefore, if the desired dimensions are not achieved, the mold must be modified. Because the mold is made of metal, it is possible to correct it by grinding it down, but it is difficult to correct it by adding more material. It is important to apply a small shrinkage rate to the cavity (female mold) of the injection molding mold and a large value to the core (male mold), and adjust the dimensions while grinding the mold.
How To Calculate the Molded Plastic Product Dimension with Molding Shrinkage?
When we at molding manufacturers design molds, we determine the mold dimensions to achieve the desired product dimensions while taking into account the shrinkage rate of the resin used.
Plastic Molded Product Dimension Formula: Dp = ((100 – S) x Dm) / 100
Where:
S: Plastic Mold Shrinkage Rate
Dm: Mold Dimensions (mm)
Dp: Dimensions of the molded product at room temperature (usually 20°C) (mm)
As introduced, the shrinkage of molded products is affected by a variety of factors, so even if the shrinkage rate is taken into account, the molded product may end up with dimensions different from those expected. Before mass-producing a new product, we explore optimal molding conditions such as the mold temperature and cooling time after molding.
Metal Injection Molding Shrinkage
Metal Injection Molding is a manufacturing process that combines plastic injection molding with powder metallurgy. It is used to create complex metal parts with high precision. So the shrinkage in metal injection molding is more compliacted than in plastic injection molding. Shrinkage in Metal Injection Molding (MIM) refers to the reduction in size of the metal part during the molding, debinding, and sintering processes, and it also must be carefully controlled and accounted for during production to ensure that the final part meets the desired specifications.
Causes of Shrinkage in MIM
Shrinkage in MIM primarily occurs during the sintering phase, where the part undergoes densification. However, some shrinkage can also occur during debinding. The overall shrinkage is a combination of both stages.
Sintering: During sintering, the metal particles fuse together, and the part densifies. This densification causes the part to shrink because the voids between the metal particles are reduced.
Debinding: In the debinding stage, the binder, which makes up a significant portion of the green part, is removed. The removal of the binder can also contribute to some shrinkage, although the major shrinkage happens during sintering.
Factors Affecting Shrinkage in MIM
Several factors influence shrinkage in the MIM process:
Metal Powder Properties: The particle size, shape, and distribution of the metal powder affect the shrinkage behavior. Finer powders tend to shrink more because they create a more compact green part.
Binder Composition: The type and amount of binder used in the feedstock influence how much the part shrinks during debinding and sintering.
Sintering Temperature and Time: Higher sintering temperatures and longer sintering times generally lead to more shrinkage as the part reaches higher densities.
Part Geometry: Complex shapes or varying wall thicknesses can lead to uneven shrinkage. Thicker sections may shrink more than thinner ones due to different cooling rates.
Mold Design: The mold must be designed to accommodate the expected shrinkage. This means the mold cavity needs to be larger than the final part size to account for the shrinkage that will occur during sintering.
Metal Mold (MIM) Shrinkage Chart
Shrinkage in MIM is typically 15% to 20% in linear dimensions, but this can vary depending on the material and processing conditions. The shrinkage is often anisotropic, meaning that it may not be uniform in all directions. This must be carefully considered during mold design.
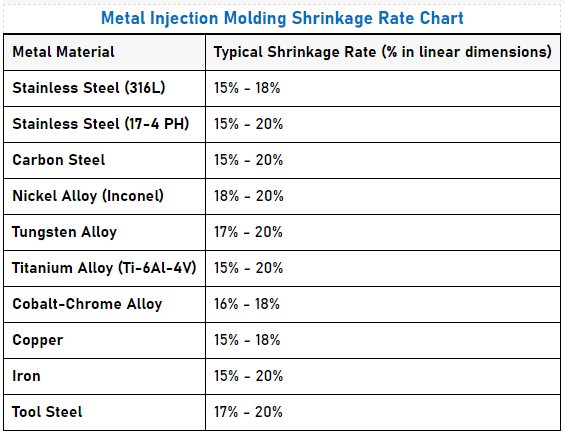
How To Calculate the Shrinkage in Metal Injection Molding?
To calculate the shrinkage in Metal Injection Molding (MIM), you need to determine the difference between the mold cavity dimensions and the final dimensions of the sintered part. This calculation helps in designing molds that account for the shrinkage that occurs during debinding and sintering.
Metal Mold Shrinkage Formula
The shrinkage percentage in MIM is usually calculated using the following formula:
Shrinkage (%)= (Dmold−Dfinal) / Dmold x 100
Where:
Dmold = Dimension of the mold cavity (before shrinkage)
Dfinal = Final dimension of the part after sintering
Rearranged Formula to Calculate Mold Cavity Dimension
If you know the desired final part dimension and the typical shrinkage rate, you can rearrange the formula to calculate the required mold cavity dimensions:
Dmold = Dfinal / (1 – Shrinkage / 100)
For example, if you know the shrinkage rate is 18% and you need the final part to have a length of 10 mm, you can calculate the required mold cavity dimension as:
Dmold = 10 / (1 – 18/100) = 10/0.82≈12.20mm
Step-by-Step Calculation
Determine the Shrinkage Rate: Start by identifying the typical shrinkage rate for the material you’re using. For example, stainless steel 316L has a shrinkage rate of 15% to 18%.
Measure or Define Final Part Dimensions: Decide or measure the required final part dimensions after sintering (e.g., length, width, height).
Calculate the Mold Cavity Dimensions: Using the shrinkage percentage, calculate the required mold cavity size to accommodate the shrinkage.