Low-pressure die casting is a casting method between pressure casting and gravity casting. It is a molding process in which liquid metal fills the cavity from bottom to top under the action of pressure to form a casting. Today, we are focusing on the working principle, technology, pros, and cons of low-pressure die casting.
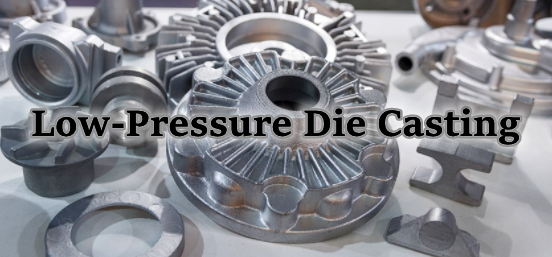
Working principle of low-pressure casting
Low-pressure casting is a casting method that enables the liquid metal to complete the filling of the mold cavity and solidification process under pressure to obtain castings. Because the pressure used is low (20 ~ 60kpa), it is called low-pressure casting. The process is as follows: dry compressed air is introduced into the sealed crucible (or sealed tank), the metal liquid rises along the riser into the spree under the action of gas pressure, enters the mold cavity smoothly through the inner spruce, and maintains the gas pressure on the liquid level in the crucible until the casting is completely solidified. Then release the gas pressure on the liquid level to make the non solidified liquid metal in the riser flow back to the crucible, open the mold, and take out the casting.
The technology of low-pressure casting
1. Mold filling and pressurization
The lifting pressure refers to the pressure required when the liquid metal rises to the gate. The rising speed of liquid metal in the riser shall be as slow as possible to facilitate the discharge of cavity gas and prevent the liquid metal from splashing when entering the gate.
2. Filling pressure
PA refers to the pressure required for a liquid metal filling to rise to the top of the mold. In the mold filling stage, the pressure rise speed on the metal surface is the mold filling speed.
3. Boost and boost speed
After the molten metal fills the mold cavity, continue to pressurize to make the crystallization and solidification of the casting proceed under a certain pressure. The pressure at this time is called crystallization pressure. The higher the crystallization pressure is, the better the feeding effect is, and the denser the casting structure is. However, increasing pressure through crystallization to improve casting quality can not be used in any case.
4. Pressure holding time
After the cavity pressure is increased to the crystallization pressure and maintained under the crystallization pressure for a period of time, the time required to know the complete solidification of the casting is called the holding time. If the pressure holding time is not enough and the casting is not fully solidified, the pressure will be relieved, and all or part of the liquid metal in the mold cavity will flow back, resulting in the “emptying” and scrapping of the casting. If the pressure holding time is too long, the gate residue is too long, which will not only reduce the process yield, but also cause freezing and make it difficult for the casting to produce the mold. Therefore, an appropriate pressure holding time must be selected in the generation.
5. Mold temperature and pouring temperature
Various molds can be used for low-pressure casting. The working temperature of the non-metallic mold is generally room temperature, and special requirements first, while there are certain requirements for the working temperature of the metal mold. For example, when low-pressure casting aluminum alloy, the working temperature of metallicity can generally be controlled at 200 ~ 250 ℃, and when pouring thin-walled complex parts, it can reach 300 ~ 350 ℃. The practice has proved that in ensuring the molding of castings On the premise, the lower, the better. The pouring temperature is generally 10 ~ 20 ℃ lower than that of gravity casting.
6. Coating
In order to improve the service life and casting quality of metal mold low-pressure casting, the coating must be painted evenly, and the coating thickness should be determined according to the surface finish and casting structure of the casting.
Pros of low pressure casting
1. Gas and sundries are less involved, the pressurization speed can be changed, and the molten soup is filled by laminar flow.
2. The bottom injection mold filling is adopted, the liquid metal mold filling is stable and free of a splash, which can avoid the involvement of gas and the scouring of mold wall and core, and improve the qualified rate of castings.
3. The casting crystallizes under pressure, with a compact structure, clear outline, smooth surface, and high mechanical properties, which is particularly beneficial to the casting of large and thin-walled parts.
4. The pressurization speed can be changed, and the molten soup is filled by laminar flow.
5. Materials are widely used
Cons of low-pressure casting
1. Low production efficiency, compared with gravity die casting. Die casting > gravity > low pressure
2. In order to maintain directional solidification and melt fluidity, the mold temperature is high and the solidification speed is slow.
3. The structure near the gate is coarse, and the mechanical performance of the lower profile is not high, so comprehensive and strict management (temperature, pressure, etc.) is required.