If you’re new to the industry, you might think that casting is a set process, with few variables. In fact, there are many types of due casting available, each with distinct advantages and disadvantages. Take, for example, high pressure casting and low pressure casting – they have lots of similarities, but their properties and features are quite different and used for very different applications. How to tell the difference between low pressure and high pressure die castings, here we are going to show the comparison between low pressure and high pressure die casting, make a proper choice when low pressure die casting vs high pressure die casting.
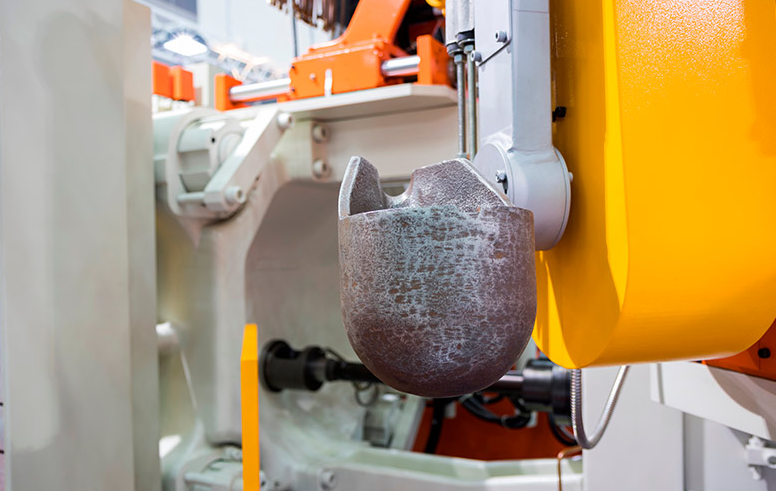
What Is Low Pressure Die Casting?
Using a low pressure die casting machine, the molten metal is packed in an insulated, pressurized and sealed crucible or furnace. The pipe passes through the furnace vertically, its bottom end is immersed in the molten metal, and the top flange is sealed with a furnace cover. The die is installed on the die casting machine above the furnace, and the open end of the pipe is sealed. When the furnace is pressurized with air, the bottom end of the pipe is immersed in the molten metal, The furnace discharges the molten metal and moves the molten metal up the pipe and into the mold cavity. Once the casting begins to cool, the unwanted metal is returned to the furnace by relaxing the air pressure. Open the mold, take out the casting and start the next cycle.
Due to the smooth filling of low-pressure die casting, the direction of liquid flow and air flow is consistent, so the casting produced by low-pressure die casting has less defects such as blowhole and slag inclusion, dense structure, high mechanical properties, and strong filling ability, which is conducive to the formation of castings with clear outline and smooth surface, so the important aluminum alloy die castings will adopt low-pressure casting.
Features and advantages of low pressure die casting:
– Very good strength values
– Complex geometries possible as sand cores can be used
– Higher material utilisation, no need for feeders
– High dimensional accuracy
– Whole process well-suited to automation
– Less complicated machine and die technology
Disadvantages of low pressure die casting:
– Slower casting cycles
– Minimum wall thickness approx. 3 mm (in die)
– Low productivity
What Is High Pressure Die Casting?
High pressure die casting refers to that the molten metal is pressed into the steel mold at high speed in the die casting process, so as to ensure that the molten metal is completely injected into the cavity space between the two half dies. Forced injection cooling shrinkage. When the molten metal enters the mold, the heat flows away from the metal and enters the mold, and the metal is cooled. When the molten metal is completely cooled, the mold is opened and the cooled casting is taken out. There are two types of mechanisms for injecting molten metal into the mold. The “Cold Chamber” mechanism is that the metal melts at high temperature. And molten metals such as aluminum, brass, and magnesium have affinity with iron. In the cold chamber process, there are two kinds of ejecting systems, horizontal and vertical. Zinc and lead metals are commonly used in the “hot chamber” mechanism. The metals melt at low temperature and reduce the affinity with iron.
High pressure die casting is the process of forcing molten metal into a safe locked cavity under pressure. After the metal cools down, the mold is opened, the casting is ejected and taken out. After the casting is removed, the mold is lubricated, closed and locked to prepare for the next cycle.
Features and advantages of high pressure die casting:
– Short casting cycles
– Suitable for thin-walled components
– Smooth surfaces
– Well suited to automation
Disadvantages of high pressure die casting:
– Complicated, expensive dies
– High investment and operating costs
– Only for die-cast parts without under-cuts, as sand cores cannot be used
– Lower strength values
– Die-cast weight limited by the locking force of the machine
Difference Between Low Pressure and High Pressure Die Casting
High pressure die casting is mainly used to manufacture castings such as shells. At the same time, high-pressure die casting can be inlaid with metal, but high-pressure die casting can not carry out heat treatment. Low pressure casting can be heat treated. In addition, in terms of equipment structure and pressurization system, the two are also different.
Although the low pressure die casting has compact structure and good mechanical properties, its productivity is low. The surface quality of high pressure die casting is better, but there are some air holes in it, so it is more suitable for thin-walled castings. When selecting castings with high air tightness requirements, choose low-pressure die casting, and choose high-pressure die casting for non-ferrous metal castings with large batch production and no densification requirement.