Iron is one of the most important metals in human civilization. Its different forms play unique roles in industrial production and daily life. Pig iron, cast iron, and wrought iron, as three key representatives of iron-based materials, originate from the same source but exhibit significant differences in composition, properties, applications, and recyclability rate. Today, we will provide a scientific analysis of these three iron materials, offering a reference for industrial material selection.
Pig Iron vs Cast Iron vs Wrought Iron
1. What is Pig Iron?
Pig iron is the raw, unrefined form of iron obtained from smelting iron ore. It is the starting material used to produce cast iron, wrought iron, and steel. While pig iron is not suitable for direct use due to its brittleness, it is a critical intermediate product in iron and steel production.
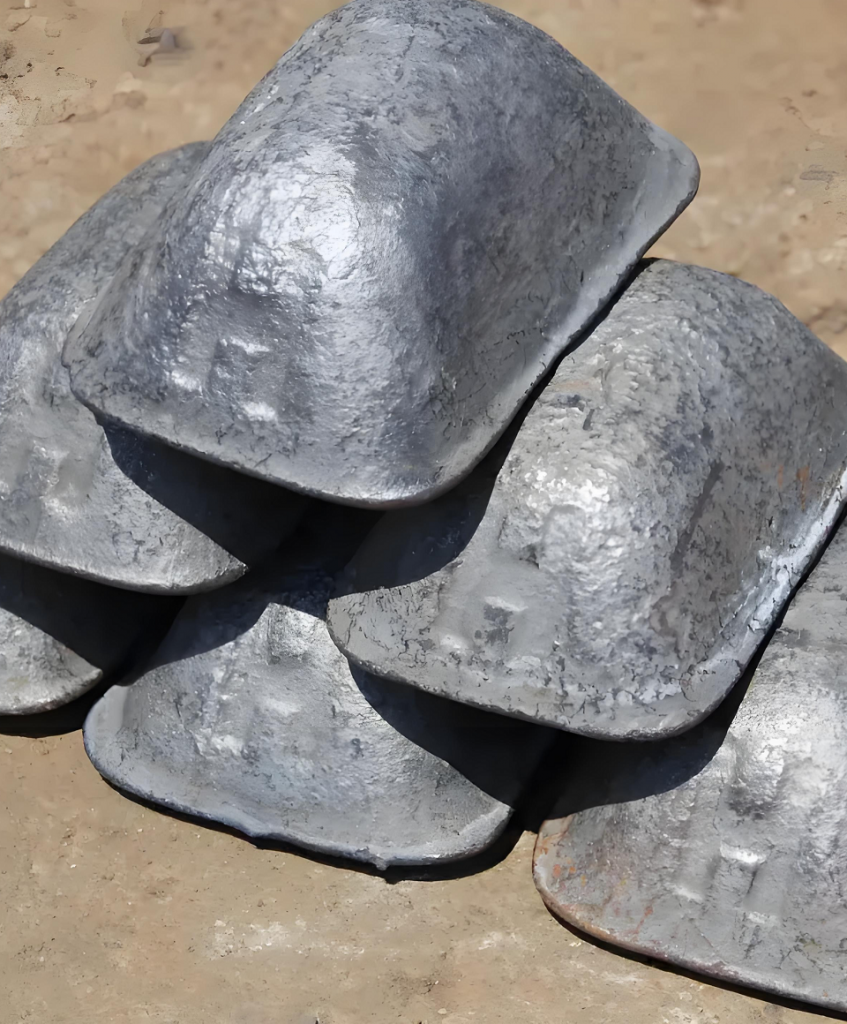
Pig Iron Composition
- Carbon Content: 3.5%-4.5%
- Other Elements: Silicon (0.5%-3%), Manganese (0.5%-6%), Sulfur (0.02%-0.1%), Phosphorus (0.1%-1%)
- Structure: Contains a high amount of impurities, making it brittle and unsuitable for most direct applications.
Pig Iron Production Process
- Raw Materials: Iron ore, coke (carbon source), and limestone (flux) are used.
- Blast Furnace: The raw materials are smelted in a blast furnace. The coke removes oxygen from the iron ore to produce molten iron, while limestone removes impurities as slag.
- Casting: The molten iron is poured into molds called “pigs” (named after the mold arrangement resembling piglets feeding from a sow).
Pig Iron Physical and Chemical Properties
- Physical Properties: High hardness (HB 150-250) but extremely brittle, unable to withstand impact loads. Low melting point (about 1100-1200°C), with good fluidity, making it suitable for casting.
- Chemical Properties: Poor corrosion resistance, prone to oxidation and rust. High sulfur and phosphorus content lead to poor welding performance.
Pig Iron Types and Applications
- White Iron (Steelmaking Pig Iron): Carbon exists as cementite (Fe₃C) and has a silvery fracture. Primarily used as raw material for steelmaking (over 90% of pig iron production).
- Gray Iron (Casting Pig Iron): Carbon exists as flaky graphite, with a gray fracture. Used to make simple castings like farming tools and iron pans.
Pig Iron Market Price
The price of pig iron is generally influenced by the prices of raw materials and market demand. In 2025, pig iron prices are expected to be around $400 to $600 per ton depending on the quality and market conditions.
2. What is Wrought Iron?
Wrought iron is a malleable and ductile form of iron with very low carbon content (<0.08%). It is produced by repeatedly heating and working pig iron, making it a highly forgeable material.
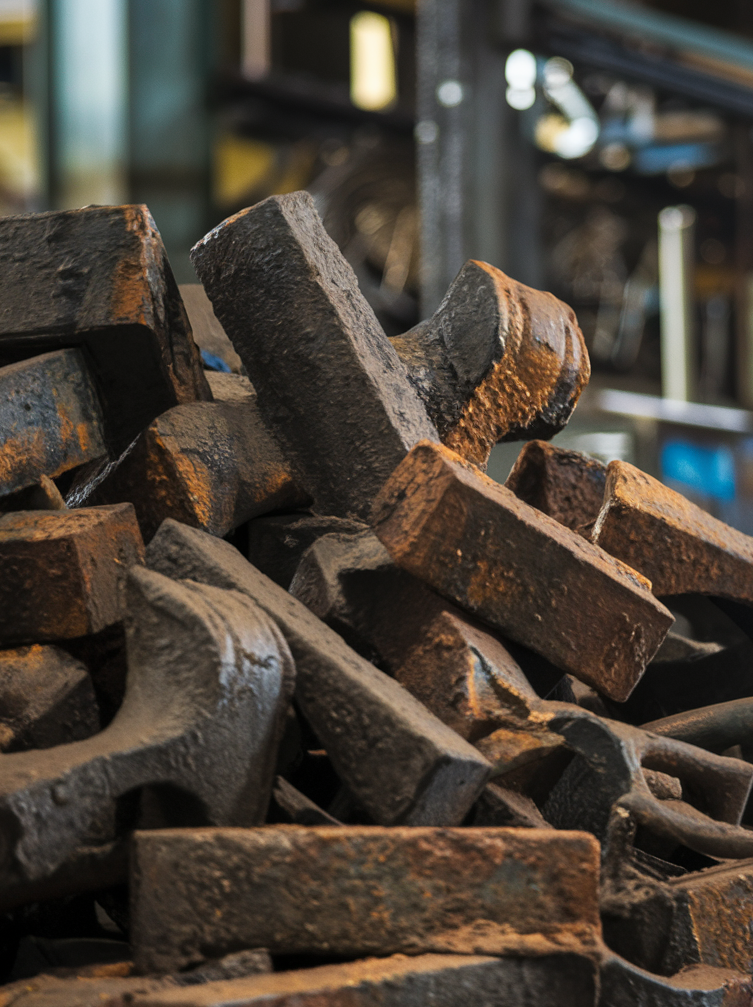
Wrought Iron Composition
- Carbon Content: <0.08%
- Other Elements: Minimal impurities, with slag inclusions (1%-2%).
- Structure: Tough, fibrous texture due to slag remnants.
Wrought Iron Production Process
- Heating: Pig iron is reheated in a forge with charcoal, which serves as both fuel and a reducing agent.
- Hammering: The heated mixture of iron and slag is hammered to expel most of the slag and shape the metal. This process is repeated several times.
Wrought Iron Properties
- Physical Properties: Excellent ductility (elongation >30%), suitable for cold forging; low hardness (HB 50-80) and high magnetic permeability (5,000-10,000 μH/m).
- Chemical Properties: Better corrosion resistance than pig iron but prone to oxidation, requiring surface treatment; reacts with acids to produce hydrogen.
Wrought Iron Types and Applications
- Traditional Wrought Iron: Forged by blacksmiths into gates, railings, and decorative items.
- Industrial Pure Iron: Used in electromagnetic components (e.g., transformer cores).
- Modern Mislabeling: Mild steel or cast iron pieces painted black are often mislabeled as “wrought iron.”
Wrought Iron Market Price (2025)
Wrought iron, being less commonly produced today, has a market price that can range from $1,200 to $2,500 per ton. The price is influenced by its low availability and the specialized processes required for its production.
3. What is Cast Iron?
Definition: Cast iron is an alloy of iron and carbon (2%-4%), along with small amounts of other elements. It is produced by remelting pig iron and is primarily used for casting due to its excellent fluidity and compressive strength.
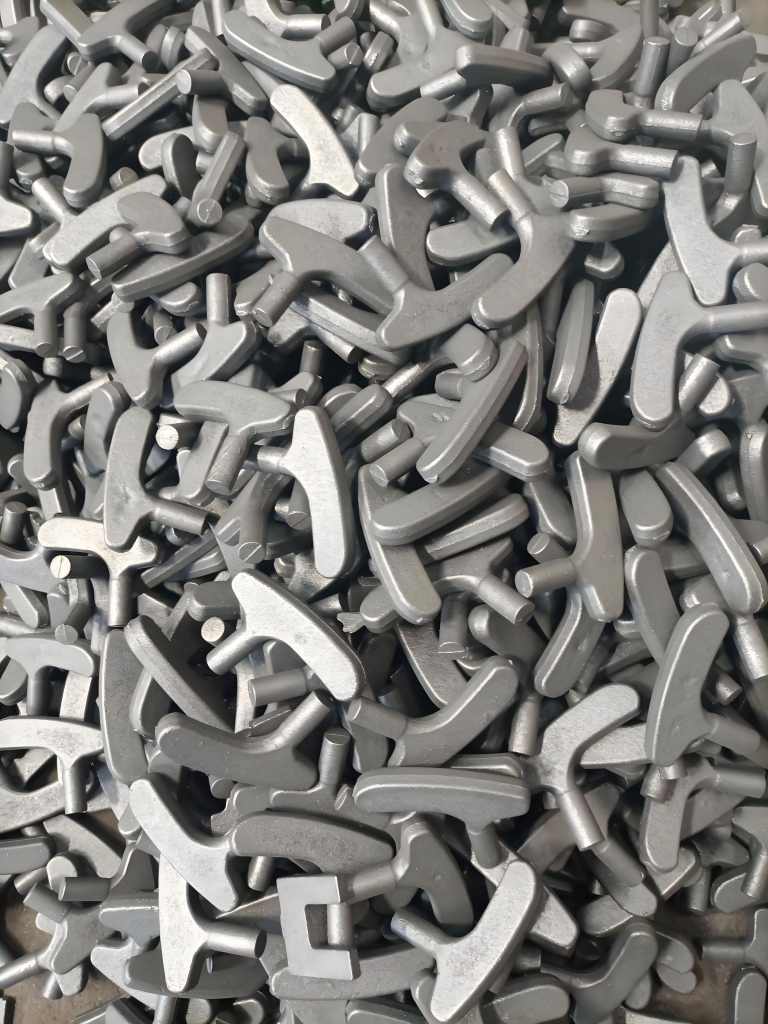
Cast Iron Composition
- Carbon Content: 2%-4%
- Other Elements: Silicon (1%-3%), Manganese, Sulfur, Phosphorus.
- Microstructure: Contains graphite, which influences mechanical properties.
Cast Iron Production Process
- Remelting: Pig iron is remelted in a cupola furnace with coke and limestone. Scrap metals and alloys may also be added.
- Casting: The molten iron is poured into molds, cooled, and solidified.
Cast Iron Physical and Chemical Properties
- Physical Properties: High compressive strength (200-400 MPa) but low tensile strength (100-350 MPa). Excellent vibration damping and wear resistance (friction coefficient 20%-30% lower than steel).
- Chemical Properties: Better oxidation resistance than pig iron; some alloyed cast irons resist acid and alkali corrosion.
Cast Iron Types and Applications
Type | Graphite Form | Properties | Typical Applications |
---|---|---|---|
Gray Cast Iron | Flaky | Easy to machine, low cost | Machine beds, engine blocks |
Ductile Cast Iron | Spherical | Strength close to steel (400-900 MPa) | Pipes, crankshafts, gears |
Compacted Graphite Iron | Vermicular | Excellent thermal fatigue resistance | Exhaust manifolds, brake discs |
Malleable Cast Iron | Nodular | Certain plasticity (elongation 2%-12%) | Pipe fittings, railway fasteners |
Cast Iron Market Price
Cast iron prices vary based on the specific type (e.g., gray cast iron, ductile cast iron). The market price for cast iron is approximately $600 to $1,200 per ton in 2025, reflecting its higher carbon content and the costs associated with its production and processing.
4. Pig Iron vs Cast Iron vs Wrought Iron: What Are the Differences?
Pig iron, cast iron, and wrought iron originate from the same raw material—iron ore—but differ significantly in composition, physical and chemical properties, processing methods, and applications. Below is a detailed comparison of these three iron types.
1. Composition and Microstructure
Aspect | Pig Iron | Cast Iron | Wrought Iron |
---|---|---|---|
Carbon Content | 3.5%-4.5% | 2%-4% | <0.08% |
Graphite Form | None (mostly cementite Fe₃C) | Flaky, spheroidal, or vermicular | None (slag inclusions present) |
Other Elements | Silicon (0.5%-3%), Manganese (0.5%-6%), Sulfur (0.02%-0.1%), Phosphorus (0.1%-1%) | Silicon (1%-3%), small amounts of Mn, S, P | Nearly pure iron with slag fibers |
Structure | Brittle due to high carbon | Hard but brittle matrix with graphite inclusions | Tough and fibrous due to slag |
- Pig Iron has the highest carbon content, making it extremely brittle and unsuitable for mechanical applications.
- Cast Iron has a lower carbon content than pig iron but still retains a brittle nature, though certain variants (e.g., ductile cast iron) have improved mechanical properties.
- Wrought Iron is the purest form, with minimal carbon and a fibrous structure due to slag inclusions, which enhance its toughness.
2. Physical and Mechanical Properties
Property | Pig Iron | Cast Iron | Wrought Iron |
---|---|---|---|
Hardness (HB) | 150-250 | 150-300 | 50-80 |
Tensile Strength (MPa) | Not significant (brittle) | 100-900 (depending on type) | 180-300 |
Compressive Strength (MPa) | Low | 200-400 | Moderate |
Ductility | Very low | Low to moderate | High |
Malleability | Very poor | Poor | Excellent |
Impact Resistance | Very low | Moderate (varies by type) | High |
- Pig Iron is extremely hard but brittle, meaning it cannot be shaped or worked mechanically.
- Cast Iron is also brittle but has excellent compressive strength, making it suitable for applications requiring wear resistance.
- Wrought Iron is the most ductile and malleable, allowing it to be forged, bent, and welded easily.
3. Workability and Processing
Aspect | Pig Iron | Cast Iron | Wrought Iron |
---|---|---|---|
Melting Point (°C) | 1100-1200 | 1150-1250 | 1480-1590 |
Machinability | Poor | Good (especially gray cast iron) | Excellent |
Weldability | Not weldable | Poor (brittle) | Excellent (easily welded) |
Forgeability | Not workable | Cannot be forged | Highly forgeable |
Casting Ability | Poor (used as raw material) | Excellent (designed for casting) | Poor (not suitable for casting) |
- Pig Iron is not directly used in manufacturing due to its brittleness and lack of workability.
- Cast Iron is ideal for casting because of its excellent fluidity when molten. However, it cannot be forged or welded easily.
- Wrought Iron is highly malleable, allowing it to be forged into intricate shapes, but it lacks the fluidity needed for casting.
4. Corrosion Resistance and Durability
Property | Pig Iron | Cast Iron | Wrought Iron |
---|---|---|---|
Oxidation Resistance | Poor | Moderate | High |
Rust Formation | Prone to rust | Rusts but forms a protective layer | Resists rust due to slag inclusions |
Wear Resistance | Low | High (especially white cast iron) | Moderate |
Fatigue Strength | Poor | Moderate | High |
- Pig Iron has poor corrosion resistance and rusts easily.
- Cast Iron resists oxidation better than pig iron, but prolonged exposure to moisture can cause rusting.
- Wrought Iron is the most corrosion-resistant due to its slag inclusions, which act as a natural barrier against rust.
5. Applications and Common Uses
Iron Type | Key Applications |
---|---|
Pig Iron | Used primarily as a raw material for steelmaking, or remelted into cast iron. |
Cast Iron | Used in machinery, engine parts, pipes, cookware, construction, and municipal infrastructure (e.g., manhole covers). |
Wrought Iron | Used in gates, railings, decorative items, chains, and historically in tools and weapons. |
- Pig Iron is not used in finished products—its primary role is as a raw material for steel and cast iron production.
- Cast Iron is used in applications where strength and wear resistance are important, but where brittleness is not a major issue.
- Wrought Iron is used in applications requiring malleability, durability, and corrosion resistance, but its modern use is limited due to the availability of mild steel.
6. Economic and Market Considerations
Aspect | Pig Iron | Cast Iron | Wrought Iron |
---|---|---|---|
Market Price (CNY/ton) | 2,000-3,000 | 3,000-8,000 | 5,000-30,000 |
Production Cost | Low | Moderate | High |
Recyclability | Nearly 100% | 85%-95% | 98% |
- Pig Iron is the least expensive because it is an unrefined raw material.
- Cast Iron is moderately priced, with ductile and alloyed variants being more expensive due to additional processing.
- Wrought Iron is the most expensive due to the labor-intensive production process and limited modern supply.