The quality control process in a die casting workshop involves meticulous oversight of every aspect of the die casting process, spanning from melting to production tuning and inspection control. This includes focusing on critical production points and maintaining equipment and molds. Any oversight in these stages could potentially lead to quality incidents.
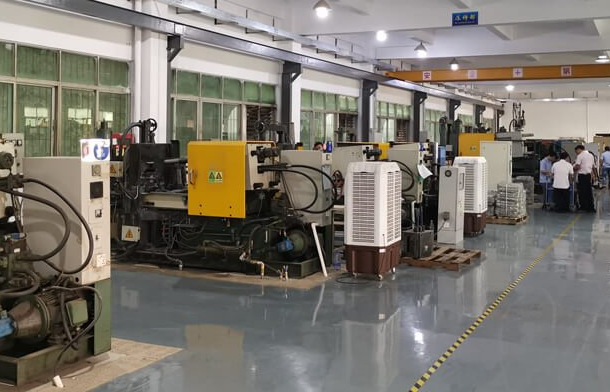
Quality Control in Die Casting Workshop – Ensuring Precision in Every Stage of Die Casting Process
Section One: Alloy Melting
- The furnace temperature should be maintained between 630°C to 680°C.
- Observe the molten aluminum after melting; ideal aluminum should appear bright white. Red color indicates excessive furnace temperature, while ice cream-like consistency suggests low temperature.
- Impurities must not be introduced during aluminum melting. Operators are strictly prohibited from placing defective products back into the furnace for recycling. If recycling is necessary, approval from the team leader is mandatory.
- Maintain a stable liquid aluminum surface, free from floating slag or bubbles. Before casting, remove the oxide layer and impurities from the surface.
- During production, add powder refining agents and slag removers to the furnace twice per shift, approximately every 4 hours. These additions must be made under the guidance of a team leader. Cleanse the impurities produced by refining before proceeding with casting.
- Clean the furnace bottom from aluminum slag at least twice per shift, averaging once every 4 hours.
- Ensure all tools in contact with molten aluminum are thoroughly dried, clean, and free from impurities.
- If excessive impurities are found in aluminum ingots or recycled materials during melting, halt the inclusion of similar ingots or materials. Report immediately to the shift leader and workshop supervisor.
Section Two: Mold Assembly
- Confirm the mold model’s accuracy and ensure mold integrity.
- Mold assembly should be done collaboratively by operators, maintenance personnel, and team leaders.
- Ensure the stability of all secure components during mold assembly to guarantee safety during production.
Section Three: Mold Debugging
- After mold assembly, conduct a test run (manual operation) and one automatic low-pressure cycle to verify mold flexibility.
- Check for loose screws, equipment oil leaks, or other abnormalities.
- Lubricate the active parts of the die-casting machine and mold.
- Preheat the mold surface to 180°C to 220°C.
- Ensure proper cooling water circulation.
- Set die-casting parameters with guidance from the team leader.
- Verify compatibility of the aluminum for casting.
- Monitor equipment and mold operation during casting.
- Confirm proper spraying pressure and quantity of release agent.
- Inspect cast products for dimension, appearance, and defects as per drawings and inspection cards.
- Perform a trial casting of over 50 pieces (low-speed injection of 20 molds followed by high-speed injection) before producing qualified castings.
- Retain the final approved castings as first inspection samples and complete the “First Inspection Sheet.”
Section Four: Die-Casting Production
- After confirming the quality of the die-cast product, the preset parameters must not be altered by operators.
- Immediately halt production if abnormal noises or instances of castings being stuck in molds are detected. Notify maintenance personnel promptly; unauthorized repairs are strictly prohibited.
- Ensure mold reliability during production:
- Uneven or worn parting surfaces could lead to excessive flash due to insufficient mold clamping force.
- Worn punches could cause splashing of molten aluminum during injection.
- Damage to mold cavities or slides due to operator errors.
- Long-term use may lead to mold fatigue and defects, affecting product quality.
- Perform self-inspection during production. Every 20 cast products require a self-inspection. Halt production immediately upon discovering any abnormalities and investigate the cause.
Section Five: Release Agent
- Apply release agent to molds before die-casting.
- Check if the release agent spraying pressure is suitable for production.
- Ensure proper release agent flow for production.
- Verify the effectiveness of the release agent.
- If issues arise, inform the team leader and workshop supervisor promptly. Adjust spraying pressure, flow, and agent mixture as needed.
Section Six: Production Inspection
- Mold Confirmation and Assembly:
- Team leaders must verify mold model accuracy and conformity with production orders.
- Mold integrity must be ensured to prevent damaged molds from being used in production.
- Verify that assembled molds are secure and well-lubricated for flexible operation.
- Mold trial castings must meet quality requirements.
This comprehensive quality control process in the die casting workshop ensures the integrity of each step in the production process, promoting product quality, efficiency, and safety.