When it comes to selecting aluminum alloys for demanding applications, understanding the distinctions between different temper designations is crucial. Among the most commonly discussed are T6 and T7 aluminum, each with unique properties derived from their distinct heat treatment processes. T6 aluminum, known for its high strength and durability, is a popular choice in industries like aerospace and automotive, where structural integrity is paramount. In contrast, T7 aluminum offers enhanced dimensional stability and ductility, making it ideal for applications that require reliable performance over time. Read our T6 vs T7 aluminium guide, we’ll tell the difference between them, and find out which is better.
What’s T6 Aluminum?
T6 aluminum refers to an aluminum alloy that has undergone the T6 tempering process, which includes solution heat treatment and artificial aging to enhance its mechanical properties. This process strengthens the material, making it highly durable, lightweight, and resistant to corrosion. Commonly used in industries such as aerospace, automotive, and construction, T6 aluminum is prized for its excellent strength-to-weight ratio, machinability, and ability to maintain stability under stress. A popular example is the 6061-T6 aluminum alloy, which is widely used for structural applications due to its versatility and performance.
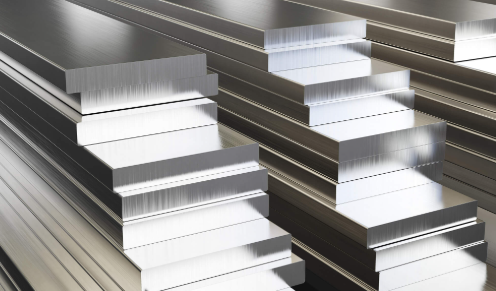
The Advantages of T6 Aluminum
High Strength-to-Weight Ratio: T6 aluminum is exceptionally strong yet lightweight, making it ideal for applications where weight savings are critical, such as aerospace, automotive, and marine industries.
Corrosion Resistance: Its ability to resist rust and corrosion ensures durability and longevity, even in harsh environments like coastal or industrial settings.
Excellent Machinability: T6 aluminum is easy to cut, shape, and machine, allowing for precision in manufacturing processes. It is also compatible with various welding techniques, making it versatile for different applications.
Thermal and Electrical Conductivity: The alloy offers good thermal and electrical conductivity, making it suitable for heat exchangers, electronic components, and wiring.
Versatility in Applications: From aerospace components and automotive parts to construction materials and consumer products, T6 aluminum’s combination of strength, lightweight properties, and corrosion resistance makes it a go-to material for diverse uses.
Cost-Effectiveness: Compared to other high-strength materials, T6 aluminum is relatively affordable, providing an economical option for manufacturers without compromising performance.
The Applications of T6 Aluminum
Aerospace Industry
T6 aluminum alloys, such as 6061-T6, are commonly used in aircraft structures, wings, and fuselages due to their high strength-to-weight ratio and resistance to stress and fatigue.
Automotive Industry
In the automotive sector, T6 aluminum is utilized for lightweight vehicle components, such as wheels, engine parts, frames, and suspension systems, to improve fuel efficiency and performance.
Construction and Architecture
Its durability and corrosion resistance make T6 aluminum suitable for structural components, roofing, bridges, and architectural facades. It is also used in window frames and curtain walls.
Marine Applications
T6 aluminum is a popular choice for boat hulls, masts, and other marine equipment due to its resistance to rust and corrosion in saltwater environments.
Sports Equipment
Sports gear like bicycle frames, baseball bats, and climbing equipment often use T6 aluminum for its lightweight and sturdy characteristics.
Electronics and Electrical Applications
The alloy’s excellent thermal and electrical conductivity makes it a material of choice for heat sinks, electrical wiring, and electronic enclosures.
The Aluminum T6 Heat Treatment
Aluminum T6 heat treatment process is a two-step process that enhances the strength and hardness of aluminum alloys, commonly used in engineering and aerospace applications. The process begins with solution heat treatment, where the aluminum is heated to a high temperature to dissolve alloying elements into a solid solution. This is followed by rapid cooling or quenching to lock in the high-temperature structure. The second step, aging, involves reheating the material to a lower temperature to allow the alloying elements to precipitate, which hardens the material and improves its mechanical properties. The result is an aluminum alloy with significantly increased strength, making it highly resistant to deformation and wear, while still maintaining a relatively low weight. T6-treated aluminum is widely used in the production of high-performance parts, such as aircraft components, automotive frames, and structural elements.
What’s T7 Aluminum?
T7 aluminum is a specific temper designation for aluminum alloys, indicating that the material has undergone a particular heat treatment process to achieve enhanced mechanical properties. This temper is typically associated with high-strength aluminum alloys, such as 7075, which are widely used in aerospace, automotive, and other high-performance applications. The T7 temper is achieved through a combination of solution heat treatment, quenching, and artificial aging, resulting in improved strength and toughness. This makes T7 aluminum suitable for applications requiring high load-bearing capacity and resistance to deformation, such as aircraft structural components and high-performance automotive parts.
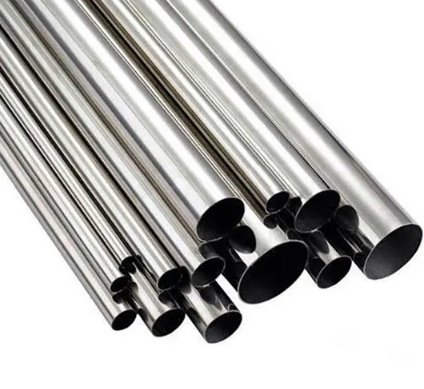
The Advantages of T7 Aluminum
High Strength: T7 aluminum achieves excellent mechanical properties through its heat treatment process, resulting in high tensile strength and yield strength. This makes it ideal for applications requiring robust structural support.
Good Corrosion Resistance: Despite its high strength, T7 aluminum maintains good corrosion resistance, especially when compared to other high-strength materials. This is crucial for applications in harsh environments, such as aerospace and marine industries.
Excellent Toughness: The tempering process enhances the toughness of T7 aluminum, making it less prone to cracking under stress. This is particularly important in applications where the material may be subjected to dynamic loads or impacts.
Lightweight: Like all aluminum alloys, T7 aluminum offers a favorable strength-to-weight ratio. This makes it an excellent choice for applications where weight reduction is critical, such as in aircraft and high-performance vehicles.
Formability: T7 aluminum can be formed into complex shapes without significant loss of mechanical properties. This versatility allows for the creation of intricate and lightweight components.
Weldability: T7 aluminum can be welded using various techniques, although care must be taken to maintain its mechanical properties post-welding. This makes it suitable for applications requiring complex assemblies.
Availability and Cost: T7 aluminum, particularly in the form of 7075 alloy, is widely available and relatively cost-effective compared to other high-performance materials, making it accessible for a variety of industries.
The Applications of T7 Aluminum
Aircraft Structures
T7 aluminum is widely used in the construction of aircraft frames, wings, and fuselages. Its high strength-to-weight ratio makes it ideal for reducing the overall weight of the aircraft, thereby improving fuel efficiency and performance.
Aerospace Components
Components such as landing gear, engine mounts, and other critical parts benefit from the high strength and toughness of T7 aluminum, ensuring reliability and safety in demanding aerospace environments.
High-Performance Vehicles
T7 aluminum is used in the manufacturing of high-performance cars, motorcycles, and racing vehicles. Its lightweight nature helps improve fuel efficiency and handling, while its high strength ensures durability and safety.
Engine Components
Parts such as pistons, connecting rods, and engine blocks can be made from T7 aluminum, contributing to the overall performance and efficiency of the engine.
Military Equipment
T7 aluminum is used in the production of military vehicles, aircraft, and other defense-related equipment. Its high strength and corrosion resistance make it suitable for harsh and demanding conditions.
Armor Plating
Due to its high strength and lightweight properties, T7 aluminum can be used in the development of lightweight armor solutions for both personnel and vehicles.
Shipbuilding
T7 aluminum is used in the construction of naval vessels and high-performance boats. Its corrosion resistance and lightweight nature make it ideal for marine applications where reducing weight and improving fuel efficiency are critical.
Marine Components
Various marine components, such as propellers, shafts, and hull structures, can benefit from the use of T7 aluminum, enhancing durability and performance in saltwater environments.
The Aluminum T7 Heat Treatment
Aluminum T7 heat treatment process is designed to enhance the strength and hardness of aluminum alloys, typically following the initial solution heat treatment (T6). It involves artificially aging the material at a controlled temperature to further improve its mechanical properties. This process is used for high-strength aluminum alloys, such as 7xxx series, which are often used in aerospace and structural applications. T7 treatment increases resistance to stress and improves overall durability, making the alloy more suitable for demanding environments. The result is an aluminum material that offers superior performance in terms of both strength and fatigue resistance, especially when subjected to intense loads or harsh conditions.
T6 Aluminum vs T7 Aluminum, What’s the Difference?
T6 and T7 are designations for aluminum alloys that indicate different heat treatment processes and resulting properties. Here’s a breakdown of the differences between T6 and T7 aluminum alloy:
Property | T6 Aluminum | T7 Aluminum |
Heat Treatment | Solution heat-treated and artificially aged | Solution heat-treated and overaged |
Strength | High strength; commonly used in structural applications | Lower strength compared to T6, but improved stability |
Applications | Aerospace, automotive, and structural components | Applications needing dimensional stability over time |
Corrosion Resistance | Good, but may vary based on alloy composition | Generally better due to overaging |
Ductility | Moderate ductility; may be less ductile than T7 | Higher ductility, making it more workable |
Machinability | Good machinability, but can be prone to cracking | Generally better machinability and less prone to cracking |
Typical Alloys | 6061-T6, 7075-T6 | 7075-T7 |
Strength: T6 aluminum is stronger but less stable over time compared to T7 aluminum.
Applications: T6 is often used where high strength is required, while T7 is chosen for applications where dimensional stability is crucial.
Corrosion Resistance: T7 usually has better corrosion resistance due to its overaging process.
Ductility and Machinability: T7 aluminum is more ductile and easier to work with compared to T6.
T6 vs T7 Aluminum, Which is Better?
When comparing T6 aluminum to T7 aluminum, the choice of which is “better” largely depends on the specific application and requirements. T6 aluminum, known for its high strength after being solution heat-treated and artificially aged, is often preferred in situations where structural integrity and load-bearing capacity are critical, such as in aerospace and automotive industries. However, it may exhibit reduced ductility and can be more prone to cracking during machining.
On the other hand, T7 aluminum, which undergoes overaging, offers improved dimensional stability and greater ductility, making it suitable for applications where parts are subjected to varying temperatures or where long-term stability is essential. While T7 aluminum generally has lower strength compared to T6, its enhanced corrosion resistance and machinability make it advantageous for specific uses, especially in components that require intricate shapes or are exposed to harsh environments. Ultimately, the decision between T6 and T7 aluminum should be based on the specific needs of the project, including strength requirements, environmental factors, and fabrication processes.
Which is Easier to Weld, T6 or T7 Aluminum?
When it comes to welding, T6 aluminum is generally more challenging to work with compared to T7 aluminum. The heat treatment process that T6 undergoes can lead to decreased ductility and increased susceptibility to cracking during welding. This makes it more difficult to achieve strong, reliable welds without specialized techniques and considerations.
On the other hand, T7 aluminum, which is overaged, typically exhibits better ductility and is less prone to cracking. This characteristic makes T7 aluminum easier to weld, allowing for more straightforward processes and better results in terms of weld quality.