As die-cast products continue to find widespread use in industries like automotive manufacturing, the demand for enhanced production efficiency, product quality, extended mold lifespan, and cost reduction has grown significantly. This has led to an increasing need for finely tuned mold temperature control, as well as higher levels of automation and intelligence in the process.
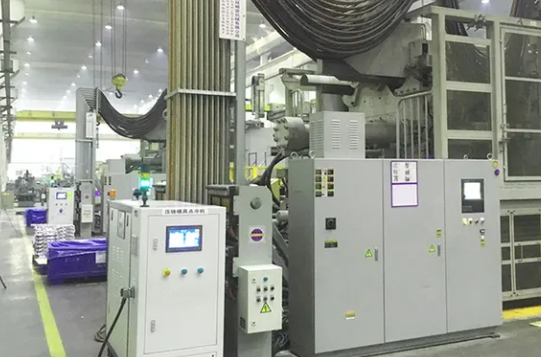
Temperature Control of Die Casting Molds – A Solution for Precision Die Casting Temperature Regulation
In die-casting production, the thermal balance of molds profoundly impacts the quality of castings, the longevity of molds, and the overall production cycle. Conventional methods of manual control and temperature regulation rely on human intervention, demanding a high degree of skill, offering limited repeatability, and often proving inefficient. Manual operations also make it difficult to detect parameter changes or promptly address emerging faults, resulting in frequent batch product scrap and significant losses for companies.
Traditional die-casting mold cooling typically employs cooling water channels and localized cooling points. This involves continuously pumping circulated water at pressures of 0.2-0.3 Mpa into the mold’s core or inserts to dissipate heat. However, manually switching on/off the cooling water, adjusting flow rates, and monitoring conditions based on experience often leads to unstable mold temperatures, affecting both product yield and production efficiency. Excessive mold temperatures can lead to aluminum sticking issues, causing frequent shutdowns for mold polishing and negatively impacting both efficiency and product quality. Conversely, lower mold temperatures can hamper the flow of molten aluminum, resulting in defects like cold shuts.
In addition, continuous cooling water constantly draws away heat from the mold, leading to a post-mold opening temperature drop. This fluctuation in mold temperature, coupled with high mold surface stress, can cause surface cracking. To optimize the die-casting mold cooling process, a novel mold temperature control system, known as the “Temperature Control Island,” has emerged.
Composition of Temperature Controlled Islands
The temperature control island mainly consists of a pure water machine, a chiller, an intermediate water tank, a fine core point cooler, and a high-pressure mold cooler. The entire mold cooling system uses pure water to ensure water quality and the entire circulation system is independently closed. Cooling water can be achieved through both atmospheric and high-pressure methods, both of which have intermittent cooling functions. The opening and closing of the mold cooling water are controlled by signals provided by the die-casting machine.
Pure water machine: Provide pure water for the entire system, with a conductivity of<15us/cm and a desalination rate of>95%, ensuring system water quality and avoiding blockage of cooling water pipes;
Chiller: used for secondary cooling of circulating water to ensure a constant temperature of cooling water in the intermediate water tank;
Cooling water tank: Intelligent control of water supply constant temperature, achieving constant temperature water supply throughout the year, ensuring the stability of the process.
Fine core cooling machine: provides high-pressure intermittent cooling for the fine core cooling pipes in the core pins and small inserts, mainly used to control casting hot spots and eliminate shrinkage cavities;
High pressure mold cooling machine: Provides high-pressure intermittent cooling for large point cooling and linear cold water pipes in mold cores, sliders, and other mold parts, mainly used to control mold heat balance.
During automated die-casting production, the Temperature Control Island receives signals such as “injection start” or “mold locked” from the die-casting machine. The high-pressure mold cooling unit and localized high-pressure cooling units pump cooling water from an intermediate water tank according to preset process requirements. Each group of cooling circuits can be individually controlled for on/off settings, timing, delay, and flow rate via the Temperature Control Island’s user interface. Following the cooling process, compressed air is automatically injected to sweep the entire cooling circuit. The cooling process is executed once per die-casting cycle.
Advantages of the Temperature Control Islands
- Independent Closed Cooling System: The closed and independent cooling system using pure water effectively prevents cooling pipeline blockages due to water quality issues. Real-time flow monitoring ensures that blockages or leaks are promptly detected.
- Tailored Control for Different Zones: The Temperature Control Island allows separate control of each cooling circuit’s switch, cooling duration, and flow rate. This customization optimizes temperature control across different mold regions, addressing hotspots and reducing shrinkage defects.
- Post-Cooling Purge: The automatic compressed air purge following cooling prevents residual cooling water from seeping into mold cavities after part removal, mitigating potential porosity issues.
- Intermittent Cooling: Intermittent cooling post-mold opening reduces temperature drop, minimizing thermal stress and extending mold lifespan.
- Efficient Parameter Storage: The control system of the Temperature Control Island can store a range of process parameters. During mold changes, a one-button process switch ensures rapid, uninterrupted production, minimizing downtime, and enhancing efficiency.
In scenarios involving complex molds, traditional cooling methods often struggle to deliver efficient, partitioned control. Temperature Control Islands, on the other hand, allow precise temperature control based on product and mold structure, enabling the setup of different cooling times and flow rates for various mold positions. This approach improves product quality, boosts production efficiency, and extends mold lifespan.
As die casting continues to evolve, solutions like the Temperature Control Island exemplify the industry’s commitment to advancing automation and intelligence, ensuring high-quality castings, optimized production processes, and enhanced resource utilization.