Die casting is basically a method of casting where we use permanent molds instead of using these traditional sand molds. The molds are made of metals metallic molds are used for better properties which we will see in the subsequent slice. If we have to talk something about the types of mold casting, there are different varieties of permanent mold casting that can be grouped under two heads. In this guide, we are going to take a look at the Advantages of die casting over traditional sand castings.
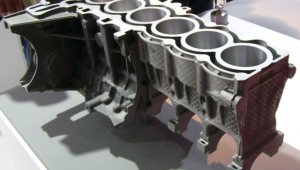
Everything You Should Know About The Die Casting Process
The first one is gravity die casting and the second one is pressure die casting. Under pressure die casting you will have two types of pressure die casting. There is the cold chamber pressure die casting and the hot jumper pressure dies casting. What separates the gravity die casting from the pressure die casting is the fact that in gravity die casting the molten metal enters the mold cavity by gravitational force with no pressure or no other external forces are applied. Whereas in pressure die casting the molded metal is forced to the help of a plunger. A ram or plunger will be there and it will try to squeeze the molten metal into the mold cavities.
What Are The Different Components Of The Gravity Die Casting Machine?
There is a fixed eye and on the left-hand side, there is a movable die. The movable like can be moved to and fro in either direction, either in left and right depending on our use. Just behind the movable die, there is a component called a plunger. The plunger is nothing, but it will try to push the movable die towards the fixed die just before we start pouring the molten metal. Just before pouring the molded metal, the movable die will be forced with the help of a plunger. So these two dies come closer to each other.
Once the plunger starts pushing it, these two dies have come closer to each other. There is a small clearance that we will pour our molten metal with the help of a ladle. In the way, we will try to pour the molten metal into the cavity. Once we are done with pouring, we will allow it to solidify. Once it gets solidified, this is the final casting. If you need a spherical object, so your mold cavity will be aspheric. If you need a rectangular casting, your final casting is to be of rectangular shape. Similarly, you have to create your die in the same manner. So these were all about gravity die casting.
The second case is the pressure die casting. We will try to squeeze the molten metal with the help of different arrangements. Pressure die casting is again can be divided into two heads the cold chamber pressure dies casting and hot-chamber pressure die casting. What differentiates these two are that in cold chamber pressure die casting, the furnace is not part of the machine. The fund is it will be located somewhere away from the die casting machine. In hot chamber pressure die casting, the furnace is actually an integral part of the machine. The furnace will be fixed to the machine. the is the only difference between these two setups.
The plunger in cold chamber pressure die casting will be used to force the molten metal into the die cavity. Once poured start pouring the molten metal in the direction, the molten metal will start coming here and then the plunger will force the molten metal into the die cavity. Then there is a movable part of the die and a fixed part of the die. the movable die will be clamped to the fixed die with the help of the two ejector pins. After done with the casting, bring out the final casting. Remove ejector pins and movable die will be removed to the left side.
In the second case in hot chamber pressure die casting everything is similar, just the setup is different. The main component is the furnace. The furnace is an integral part of the setup that we will meet our metal solid metal. Once the solid metal is melted with the help of the plunger, a force will be applied to the plunger. As a result of the force, the molten metal will flow along the direction and fill the mold cavity. The important part is the gooseneck pipe because it resembles the neck of a ghost goes. Once the molten metal comes and fills the entire cavity, wait for some time to solidify it and then remove the ejector pins, then get the final casting. These were all about the hot chamber and cold chamber die casting.
The Advantages of Die Castings Over Sand Castings
1. The first point is a better surface finish. Since you are using metallic molds, so the surface finish will be far better as compared to the sand molds.
2. The low gas porosity because porosity means small air pockets that remain in the molten metal. Chances of porosity are very less because you are trying to squeeze the molten metal inside. Chances of porosity become negligible.
3. Homogeneous grain structure means uniform grain structure will be attained in case of die casting, which is not always possible in sand casting. Because in die casting since you are applying uniform pressure, so the green structure becomes uniform.
4. Better mechanical properties will be obtained only when the rate of cooling is optimum. Since we are using metallic molds, metals are good conductors of heat. They will try to take the heat at a faster date from the molten metal, and they will release the heat to the environment. Due to the faster cooling rates, we will get better mechanical properties.
5. Last but not least, higher rate of production. Since you are doing everything with the help of a machine, your rate of production will be more in sand casting. You might have seen that after doing one single operation, we have to break the sense and mold. Again, we have to create a new mold, so the process takes a lot of time. If you are running a company where bulk production is your aim. In this case, you should go with the die castings. The initial investment will be high, then it will be compensated since you are creating more parts in a short amount of time.