In the realm of synthetic materials, Thermoplastic Elastomer (TPE) and Silicone stand out for their versatile uses across various industries. Both materials offer distinct properties that cater to specific needs. However, to make an informed decision between the two, it’s essential to delve into the data that highlight their differences. Here we will explore the quantifiable aspects that set TPE and Silicone apart.
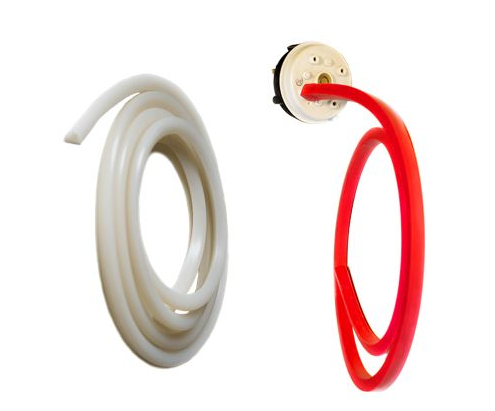
TPE vs. Silicone: Definition, Properties
TPE is a blend of polymers, typically plastic and rubber, that exhibit both thermoplastic and elastomeric properties. TPE can be stretched to elongate at least twice its original length at room temperature and return to its approximate initial length when stress is released.
Silicone is a synthetic polymer composed primarily of silicon together with carbon, hydrogen, and oxygen. Silicones are known for maintaining their properties across a wide temperature range and are used in applications requiring high durability and stability.
Properties | TPE | Silicone |
Hardness | Ranges from very soft (10 Shore A) to semi-rigid (80 Shore D) | Generally from 10 to 80 Shore A |
Specific Gravity | Varies from 0.89 to 1.25 depending on formulation | Ranges from 1.10 to 1.50 |
Tensile Strength | Between 500 to 3,500 psi | Approximately 200 to 1,500 psi |
Elongation at Break | Anywhere from 200% to 800% | From 100% to 700% |
Service Temperature Range | Typically -50°C to 90°C but can go as high as 150°C for special formulations | Extremely wide, from -55°C to over 300°C |
Recyclability | TPE can often be 100% recycled at the end of its life cycle | N/A |
Resistance to UV and Ozone | N/A | Excellent, rarely affected by outdoor exposure |
Key Differences Between TPE Materials and Silicone
Both TPE and Silicone have their own unique benefits and characteristics, which make them suitable for different applications. The choice between using TPE or Silicone will largely depend on the specific requirements of the product being manufactured, including performance, cost, and environmental considerations. Understanding the differences between these two materials is essential for making an informed decision on which to use for any given application.
- 1. Performance and Durability
When comparing the two, silicone has superior temperature resistance. Silicone can operate effectively in temperatures as high as 300°C, whereas TPE’s maximum operating temperature is usually around 150°C. Silicone also tends to have better resistance to UV and ozone exposure, making it more suitable for outdoor applications.
- 2. Cost and Production
From a cost perspective, the price per kilogram of TPE ranges between $1 to $5, while silicone ranges from $5 to $20, depending on the quality and grade. This makes TPE a more economically viable option for cost-sensitive projects.
- 3. Environmental Impact
TPE’s recyclability is a substantial benefit, as it can be melted down and reformed. However, the actual rate of TPE recycling varies, and the presence of multiple types of TPE can complicate the process. Silicone’s durability means it has a longer lifespan, but it is not typically recycled due to the difficulty of breaking down its stable polymers.
- 4. Applications
TPE is often utilized in the automotive industry for parts like gaskets and seals, where it offers substantial cost savings. For example, the automotive industry reports using approximately 60,000 tons of TPE annually. Silicone, with its biocompatibility and temperature resistance, is heavily used in the healthcare sector, which utilizes an estimated 12,000 tons each year for medical devices alone.
- 5. Customization
TPE’s ability to be customized allows for a wide range of applications. The market for TPE is expected to grow at a compound annual growth rate (CAGR) of 6.7% from 2020 to 2027, indicating its rising demand across various industries.
- 6. Process of TPE and Silicone Injection Molding
TPE Injection Molding Process
TPE is a thermoplastic, meaning it becomes pliable or moldable at a certain elevated temperature and solidifies upon cooling. The process to mold TPE is similar to that of traditional plastic injection molding and typically follows these steps:
- Step 1 – Material Preparation: TPE pellets are dried if necessary, to reduce moisture content.
- Step 2 – Melting: The TPE pellets are fed into the injection molding machine where they are heated and melted.
- Step 3 – Injection: The molten TPE is injected into a closed, clamped mold at high pressure.
- Step 4 – Cooling: The TPE cools and solidifies into the shape of the mold. Cooling time can be precisely controlled to help maintain the desired properties of the material.
- Step 5 – Ejection: Once the part has cooled and solidified, the mold opens, and the part is ejected.
- Step 6 – Post-Processing: Any necessary secondary processes such as trimming excess material or finishing the part occur at this stage.
Silicone Injection Molding Process
Unlike TPE, silicone does not have a true melting point but it can be set or vulcanized into a solid state. Silicone injection molding, often referred to as Liquid Silicone Rubber (LSR) molding, requires a different process:
- Step 1 – Material Preparation: Silicone comes in a two-part system where the base and the catalyst must be mixed just before the molding process.
- Step 2 – Mixing: The two parts of the silicone are mixed and often degassed before injection to reduce the potential for air entrapment and imperfections in the finished product.
- Step 3 – Injection: The mixture is then injected into a heated mold. Unlike thermoplastics, the mold for silicone is heated rather than cooled, which helps catalyze the cross-linking process that gives the silicone its final properties.
- Step 4 – Curing: The heat from the mold causes the silicone to cure, a chemical process that creates a solid elastic material.
- Step 5 – Ejection: Once the part is fully cured, the mold opens, and the part is removed. Step 6 – Post-Processing: As with TPE, any additional finishing required is done after the part is ejected from the mold.