Die casting is a manufacturing process that has been used for over a century to create high-quality metal parts. It involves injecting molten metal into a mold cavity at high pressure and then allowing it to solidify into a desired shape. Die casting has come a long way since its inception, with modern technology and techniques improving the efficiency and quality of the process. In this article, we will talk about the evolution of die casting, from traditional methods to modern techniques.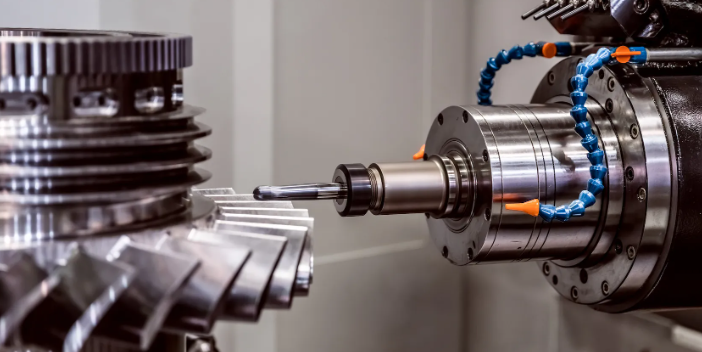
Traditional Die Casting Methods
The first die casting machines were developed in the mid-19th century, and they used low-pressure techniques to produce parts. In these early machines, the metal was manually poured into the die, and the mold was cooled by air or water. This method was slow and produced inconsistent results.
In the early 20th century, hot chamber die casting machines were introduced. These machines used a pool of molten metal that was continuously replenished, allowing for faster production and more consistent results. This method was ideal for producing parts made from low-melting-point metals such as zinc, tin, and lead.
In the 1930s, cold chamber die casting machines were introduced. These machines were capable of producing parts made from high-melting-point metals such as aluminum, magnesium, and copper. In this method, the molten metal was poured into a separate chamber, then injected into the mold cavity under high pressure.
Advances in Die Casting Technology
Since the introduction of hot and cold chamber die casting machines, technology has continued to evolve to improve the efficiency and quality of the process. Here are some of the major advances in die casting technology:
- High-pressure die casting: In the 1950s, high-pressure die casting (HPDC) was introduced. This method uses even higher pressures and speeds than traditional die casting, resulting in even greater precision and quality.
- Vacuum-assisted die casting: Vacuum-assisted die casting (VADC) is a variation of the traditional die casting process that uses a vacuum to remove trapped air and gases from the mold cavity. This method can improve the quality and consistency of the parts and reduce the risk of defects.
- Multi-slide die casting: Multi-slide die casting is a process that uses multiple slides to produce complex parts with intricate shapes and features. This process allows for greater flexibility and customization in part design and production.
- Simulation software: Simulation software is being used in die casting to model and simulate the process parameters, such as temperature, pressure, and mold filling. This software can help to optimize the process and reduce the risk of defects and waste.
-
Modern Die Casting Techniques
Recent advancements in die casting technology have led to the development of new techniques that offer greater flexibility and precision in part design and production. Here are some of the modern die casting techniques:
- Squeeze casting: Squeeze casting is a method that combines the advantages of casting and forging to produce high-strength parts. In this method, the molten metal is injected into the mold cavity under high pressure, then pressure is applied to the mold during solidification.
- Thixomolding: Thixomolding is a process that involves the use of semi-solid metal to produce parts with superior strength and precision. In this method, the metal is heated to a semi-solid state, then injected into the mold cavity.
- Rheocasting: Rheocasting is a process that uses a metal slurry to produce parts with a fine grain structure and superior mechanical properties. In this method, the metal is heated to a semi-solid state, then mixed with a stirring device to create a slurry.
-
Applications of Die Casting
Die casting is a versatile process that is used in various industries to
produce high-quality metal parts with complex shapes and precise dimensions. Here are some of the most common applications of die casting:
- Automotive: Die casting is widely used in the automotive industry to produce various components, such as engine parts, transmission housings, and suspension components. The high strength and lightweight properties of die cast parts make them ideal for improving fuel efficiency and reducing emissions.
- Aerospace: Die casting is increasingly being used in the aerospace industry to produce lightweight and strong components, such as engine parts, structural components, and interior fittings. The high-performance properties of die cast parts make them ideal for improving fuel efficiency and reducing weight.
- Consumer goods: Die casting is used in the production of various consumer goods, such as kitchen appliances, tools, and toys. The precision and durability of die cast parts make them ideal for high-quality and long-lasting products.
- Electronics: Die casting is used in the electronics industry to produce various components, such as computer hardware, mobile phone cases, and audio equipment. The precision and durability of die cast parts make them ideal for high-quality and long-lasting electronic devices.
-
Challenges and Opportunities in Die Casting
While die casting has undergone significant advancements, there are still challenges and opportunities that lie ahead for the industry. Here are some of the key challenges and opportunities in die casting:
- Sustainability: The use of sustainable materials and processes is becoming increasingly important in die casting, with pressure from customers, regulators, and stakeholders to reduce the environmental impact of manufacturing. The industry is exploring new methods for reducing energy consumption, minimizing waste, and increasing the recyclability of materials.
- Cost-competitiveness: The pressure to remain cost-competitive in a global market is a challenge for the die casting industry. Manufacturers are looking for ways to reduce costs without compromising on quality or efficiency. This includes optimizing production processes, reducing material waste, and adopting new technologies that can improve productivity and quality.
- Skills gap: The die casting industry is facing a skills gap as experienced workers retire and new entrants to the workforce lack the necessary training and experience. Manufacturers are working to attract and train new workers, and to implement apprenticeship programs that can provide hands-on experience and training.
- Customization and flexibility: The demand for customized products and shorter lead times is increasing in various industries, such as consumer goods and electronics. The die casting industry is exploring new methods for customization and flexibility, such as the use of additive manufacturing, multi-slide die casting, and other advanced techniques.
- Quality control: The quality of die cast parts is critical for many applications, such as automotive and aerospace. The industry is exploring new methods for quality control, such as advanced inspection technologies, statistical process control, and real-time monitoring of process parameters.
-
- The die casting industry has come a long way since its inception, with advancements in materials, technology, and applications. While challenges remain, the industry is well-positioned to address them through innovation, collaboration, and a commitment to sustainability and quality. The future of die casting looks promising, with potential for even greater efficiency, customization, and flexibility in part design and production.tal