TIG welding, also known as gas tungsten arc welding (GTAW), is an arc welding process that uses a non-consumable tungsten electrode to produce the weld. The weld area is protected from oxidation or other atmospheric contamination by an inert shielding gas (usually argon or helium), and a separate welding filler material is often used. A constant-current welding power supply produces an arc between the tip of the non-consumable tungsten electrode and the weld pool. The electrode does not melt during the process, so it must be manually sharpened as needed between welds using a stone.
This article presented TIG welding, explained it, and discussed how to use it and its pros and cons. To learn more about tig welding, contact a Diecasting-Mould representative.
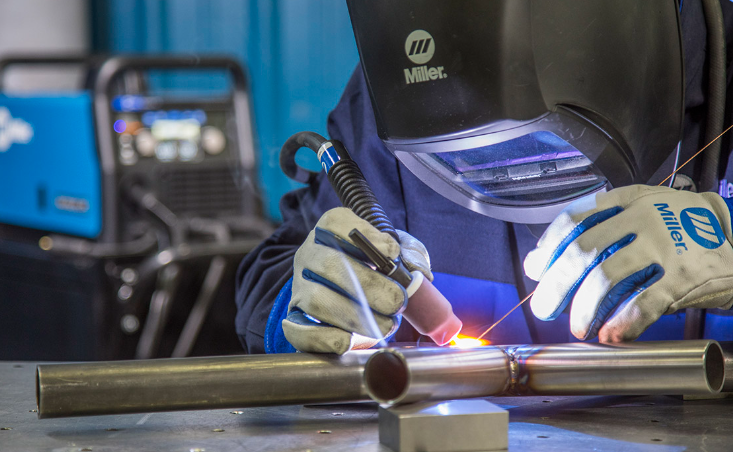
How Does TIG Welding Work
TIG welding uses a non-consumable tungsten electrode to create an electric arc between the tip of the electrode and the metals being welded. A constant current power supply is used to generate the arc. An inert gas, such as argon or helium, flows through a torch and delivers the gas to the weld area through nozzles around the tungsten electrode.
The gas shields the weld area from oxygen and other gases in the air that could react with and contaminate the hot weld metal. It also helps conduct heat and electricity. A filler rod made of the same or similar material as the base metal is often added manually to increase welding deposition rates.
When the electrode is brought close to the base metal, the constant current power supply senses the change in electrical resistance and triggers, generating an arc. Temperatures at the tip of the arc can reach over 6,000°C, melting the base and filler metals to form a weld pool.
The welder carefully controls the weld pool using the electrode like a brush, forming a joint. As the weld pool solidifies behind the arc, it fuses the materials. By precisely controlling variables like arc length, travel speed, and filler addition, high-quality welds can be produced.
Uses of TIG Welding
- – Aerospace: Welding jet engine components, aircraft frames, and skin that require high strength, corrosion resistance, and transparency.
- – Automotive: Joining chassis, suspension, and powertrain parts for cars, trucks, and motorcycles. Often used on luxury and high-performance vehicles.
- – Medical: Surgery tools and implants made of titanium or stainless steel. Also dental implants, crowns, and bridges. Precision and biocompatibility are critical.
- – Art and sculpture: Artists will use TIG for assembling metal sculptures and other works given the aesthetic quality of welds.
- – Jewelry manufacturing: Brazing or welding precious metals like gold, silver, and platinum used in rings, bracelets, and other fine pieces.
- – Bicycles: Frames and components like gears and pedals are commonly TIG welded for lightweight and corrosion resistance.
- – Pipefitting: Connecting pipes, valves, and fixtures made of copper, brass, or stainless for plumbing, heating, and cooling systems.
- – Food processing equipment: Welding parts for machinery used in dairy, beverage, and other food production due to sanitary requirements.
Different Parts of TIG Welding
The torch, electrode, gas, power source, and work cables are core TIG welding system components.
- – Tungsten electrode: The non-consumable electrode that arcs to the workpiece and is manually sharpened as needed. Common types are thoriated, ceriated, lanthanated, or pure tungsten.
- – Torch: Houses the electrode and gas delivery parts. Different-sized torch cups fit various electrode diameters.
- – Shielding gas: Inert gas like argon or helium that flows through the torch to shield the weld. Cylinders or machines provide the gas source.
- – Clamp: Secures the torch while welding to allow electrode manipulation with both hands. Booms help position large workpieces.
- – Filler rod: Added manually as needed for fillet or some groove welds. Made of matching filler metal.
- – Welding power source: Constant current AC or DC power supplies. More advanced units have waveforms and pulsing options.
- – Work cable: Connects the workpiece to the power source to complete the circuit. Heavy duty for welding large metal.
- – Ground clamp: Secures the work cable for proper welding current path.
- – Safety gear: Helmet, gloves, and other PPE to protect the welder from UV rays, sparks, and electric shock.
Types of Materials That Can Be TIG Welded
TIG is very versatile and can fuse an array of metals provided the proper gases and techniques.
- – Aluminum: A very popular material for TIG welding due to the process control and compatibility with aluminum. Alloys like 6061 are commonly welded.
- – Stainless steel: The various grades of austenitic and duplex stainless steel weld well with TIG. 304 and 316 are frequently used.
- – Titanium: An important structural metal that requires an inert shielding gas. Both commercial purity and alpha-beta alloy titanium.
- – Magnesium: When used with pure argon gas, TIG can join this light but flammable metal. Alloys like AZ31B.
- – Copper: Both copper alloys and pure copper are amenable to TIG. Good for piping, tubing, and electronics applications.
- – Nickel alloys: Corrosion-resistant alloys containing nickel perform well with TIG, such as Monel and Hastelloy.
- – Zinc: Galvanized sheet metal and die-cast zinc components can be spot welded or repaired.
- – Platinum: Precious metal TIG welding used for industrial process parts and jewelry.
- – Steel (carbon and low-alloy): Mild steels like A36 can be welded though higher alloy steels are more common.
Advantages and Disadvantages of TIG Welding
TIG enables high-quality precision welds but takes more skill and equipment investment compared to other techniques.
Advantages:
- – Produces high-quality, aesthetic welds suitable for precision applications
- – Provides excellent welding control with a focused arc
- – Versatile process for many metals including aluminum, stainless steel, titanium
- – Minimal filler material needed, permitting tightly controlled welds
- – Does not generate smoke or slag like other welding processes
- – Can be used to weld most any position including overhead
- – Inert gas protects the weld area from contamination
Disadvantages:
- – Requires more skilled operators compared to other welding processes
- – The learning curve can be steep for the TIG technique and setup
- – Welding costs are higher than some other welding processes
- – Process is slower than alternatives like MIG or stick welding
- – Equipment costs are higher for the power source and torch
- – Filler material must be added manually for some joints
- – Greater chance of operator error affecting weld quality
- – Proper shielding gas and flow rate is critical for good results
Difference Between TIG Welding and Laser Welding
The key differences are that the laser uses a focused non-contact beam vs TIG’s electric arc, and the laser typically provides faster, more precise, and higher-powered welding capabilities.
- Electrode: TIG uses a non-consumable tungsten electrode to create an arc, while laser welding uses a focused laser beam.
- Heat Source: The electric arc heat source in TIG welding is concentrated but not as precise as the laser beam, which can be tightly focused.
- Shielding Gas: TIG requires an inert shielding gas like argon to protect the weld area. Lasers typically do not need external shielding gas.
- Filler Material: TIG often uses a separate filler rod added manually, while laser welding can join materials without filler.
- Welding Speed: Laser welding is generally much faster than TIG, which must be moved along the joint manually.
- Joint Preparation: TIG typically requires a beveled joint for proper penetration, while a laser can often fusion weld without edge preparation.
- Material Depth: Laser energy can be absorbed to weld deeper into thick materials, while TIG is better for thinner gauges.
- Precision: The laser beam enables highly precise welds down to a few microns in width and depth. TIG is less precise.
- Cost: Laser systems are more expensive initially but can have higher welding throughput rates than TIG.