A hot runner system is an assembly of heated components used in plastic injection molds that inject molten plastic into the cavities of the mold. The hot runner system keeps the plastic in a molten state and allows it to flow into the cavity, ultimately forming the desired part.
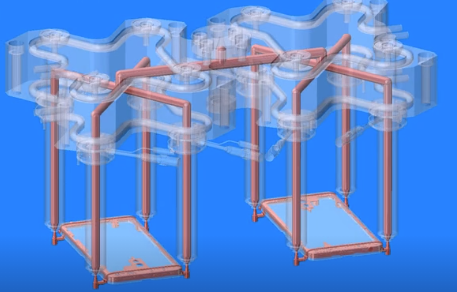
Pros of hot runner system application
- 1. Automation and Efficiency: Since hot runner systems eliminate the need for runners, the plastic molding process becomes fully automated. This saves labor and time required for manual trimming and recycling of runners, thereby increasing overall operational efficiency.
- 2. Reduced Pressure Loss: Hot runner systems maintain a consistent and high temperature, preventing the premature cooling of the plastic material in the runner and thus reducing pressure loss during the injection phase. This results in a smoother flow of the molten plastic, which is particularly beneficial for thick-walled parts that require high injection pressure.
- 3. Material Savings: The absence of cold runners means there’s no scrap produced during the molding process. This eliminates the need to recycle scrap material, which can degrade the physical properties of the plastic, and reduces overall material waste, leading to cost savings.
- 4. Improved Quality: Hot runner systems provide a more balanced flow of plastic into each cavity and maintain a more consistent temperature, resulting in parts with uniform stress, density, and quality. This is particularly beneficial for molding parts with complex geometries, thin wall sections, or strict quality requirements.
- 5. Standardization and Interchangeability: Many hot runner systems are designed with standardized components, increasing the system’s flexibility and interchangeability. This streamlines the maintenance process and reduces downtime during changes in production.
Cons of hot runner system application
- 1. Initial Cost: Hot runner systems are generally more expensive to purchase and install compared to cold runner systems. This initial cost can be significant, particularly for smaller manufacturing operations.
- 2. Maintenance and Complexity: Hot runner systems are more complex than cold runner systems. If a problem arises, it can be more difficult to diagnose and repair. This complexity also means that maintenance and cleaning can be more time-consuming and need to be performed more frequently to ensure the system continues to operate effectively.
- 3. Power Consumption: Although hot runner systems can reduce material waste, they also require continuous heating to keep the plastic in the runners molten. This can lead to increased energy usage compared to cold runner systems.
- 4. Mold Design Limitations: Hot runner systems can restrict the design of the mold due to the need to incorporate the hot runner manifold and nozzles. This might limit the complexity or flexibility of the parts that can be produced.
- 5. Potential for Material Degradation: If the plastic material in the hot runner system is kept at high temperatures for extended periods, it can degrade, which may affect the quality of the final product. This is particularly an issue with heat-sensitive materials.
- 6. System Start-up Time: Hot runner systems may require more time to reach the correct operating temperature, potentially leading to longer start-up times for the mold-making process.
Material PBT+40%GF Case
The original design uses an 8-point nozzle to feed glue, the nozzle weighs 13.25g, the unit weight of the product is 1.3g, and the total weight of 8 products is 10.4g. Switch to the 8-point hot nozzle and use the full hot runner to enter the glue. Every time each set of molds produces 1 million molds, the material cost is saved by approximately US$2,410, and the production time is shortened by 69 days. The labor cost is reduced to 30 days, and the labor cost savings is approximately US$1,600. The total cost savings for a single set of hot runner is approximately US$2,620. Assuming that 50 sets of your company’s molds need to be modified to hot runners, the cost savings can be at least approximately US$131,280.
1. Using a hot runner can bring you higher returns
- -The use of hot runner saves more costs. The higher the material price, the more waste materials at the nozzle, and the greater the product output, the more cost savings will be achieved by using hot runner.
- -The nozzle material requires storage, crushing, and power consumption, which will reduce product quality and increase 1-2 manpower. The hot runner has no nozzle, which saves labor and has better product quality.
- -The three-plate mold is easily damaged due to the movement of the nozzle plate. After switching to a hot runner, the mold life will be longer and the quality will be more stable.
2. Hot runner can be produced in larger quantities
- -Because the hot runner system has no water inlet, the injection and cooling times can be greatly shortened. Using the hot runner system can shorten the molding cycle by 20%-25%.
- -The use of a hot runner system can realize the injection molding of more cavity products, which can increase the production capacity by at least 25%.
- -The internal pressure loss of the hot runner system is small, the internal stress of the product is small, and the product’s surface quality and mechanical properties are better.